タフピッチ銅の精密なフライス加工 – 試作を成功させるためのステップ
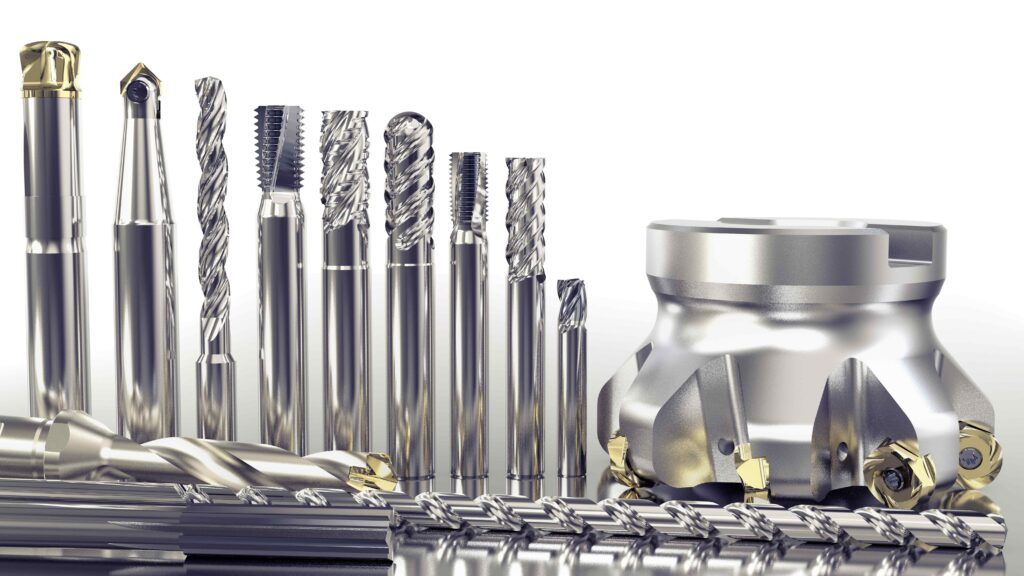
タフピッチ銅の精密なフライス加工とは、製品試作に不可欠なステップの一つです。しかし、その複雑な性質やフライス加工の技術は多くの人にとってとっつきにくいものです。本記事では、タフピッチ銅を使用した精密なフライス加工に焦点を当て、試作を成功させるためのステップについて詳しく解説します。製品試作におけるタフピッチ銅とフライス加工の重要性、試作に向けた準備から実際の加工方法までをイラスト入りで分かりやすく紹介します。
1. タフピッチ銅 フライス加工 試作の概要
タフピッチ銅のフライス加工は、精密な試作を成功に導くため、重要なステップです。この金属の特性は、優れた導電性と加工性を持つ一方で、その柔軟性ゆえに精密加工には注意が必要です。具体例として、製造業ではタフピッチ銅を使って微細な電子部品や接続端子などを作ることが多いですが、これらは高い精度が求められます。試作段階でのフライス加工においては、適切な工具選びや速度設定が重要で、また、加工時の温度管理など細かな条件調整が成功の鍵を握ります。試作を重ねることで得られるノウハウを活かし、最終的な量産につなげることができるため、この段階の効率的な進行はコスト削減にも直結します。以上より、タフピッチ銅のフライス加工は試作において精密かつ慎重なアプローチが必要であると言えます。
2. タフピッチ銅の物性とフライス加工の相性
タフピッチ銅はその優れた電気伝導性や耐食性から、精密なフライス加工においても非常に重宝されています。しかし、その加工には成功のためにいくつかのステップを踏む必要があります。まず、タフピッチ銅の物性を理解し、適切な切削工具や条件を選定することが重要です。例えば、工具の材質や刃の形状、回転速度などが、加工精度に直接影響を与えます。次に、加工前の準備として、フライス盤の精度を確認し、必要に応じてメンテナンスを行うことで、加工時の振動や誤差を最小限に抑えることができます。特に試作段階では、微小な加工のズレも許されないため、工程の細部に至るまで慎重な検討が求められます。最終的に、これらのステップを丁寧に実行することで、タフピッチ銅の精密なフライス加工に成功することができるのです。
3. 試作フェーズでのフライス加工の計画
タフピッチ銅のフライス加工における成功は、試作フェーズの計画にかかっています。タフピッチ銅はその優れた電気伝導性と加工性で、精密部品製造において重宝されていますが、特有の軟らかさと粘り気があるため、フライス加工は慎重に行う必要があります。成功のためのステップとしては、まず適切な切削工具の選定が重要です。例えば、銅の加工には鋭い刃先と高い耐久性を持つ超硬工具が推奨されます。次に、適正な切削速度や送り速度の設定が不可欠で、これによりバリの発生を抑え、仕上がりの精度を向上させることができます。更に、冷却液の使用は切削熱の影響を抑制し、材料の変形や工具の摩耗も防ぎます。これらのステップを踏むことで、高品質な試作品のフライス加工が実現可能です。最終的に、計画的な加工でタフピッチ銅のポテンシャルを最大限に引き出し、精密な試作を成功させることができます。
4. タフピッチ銅 フライス加工のための工具選定
タフピッチ銅の精密なフライス加工を行う際、適切な工具選定は成功への鍵です。タフピッチ銅は優れた電気伝導性と加工性を持った材料であり、精密機器の試作にしばしば用いられます。ただし、その軟らかさと粘り強さから、加工時にバリが発生しやすく、表面が荒れる可能性があります。これを防ぐためには、材料に合った刃の形状やコーティングを施した工具を選び、速度や送りのパラメータを細かく調整することが重要です。例えば、鋭角なエッジをもつエンドミルは、バリの発生を抑えることができます。また、数値制御(NC)技術を駆使して、高精度なフライス加工を実現することも、試作の成功には不可欠です。適切な工具の選定と加工条件の調整によって、タフピッチ銅の試作は高品質に仕上がるでしょう。
5. タフピッチ銅のフライス加工パラメータ設定
タフピッチ銅のフライス加工は精密加工において非常に重要です。その成功の鍵は適切な加工パラメータの設定にあります。タフピッチ銅は高い熱伝導率と良好な電気伝導性を持つため、電子部品の試作にしばしば使用されます。しかし、その軟らかさと粘り気のある性質が加工を難しくしています。適切な工具の選定、正確なスピンドル速度の調整、適切な送り速度と切削深さの設定が、仕上がりの品質を左右します。具体的には、耐摩耗性が高く、銅に適したコーティングが施されたエンドミルを使用することが推奨されます。また、低速で一貫した送り速度を保つことで、過剰な熱の発生を防ぎ、加工精度を高めることができます。これらのステップに注意を払い、調整を行うことで、タフピッチ銅の加工においても高品質な試作品を生み出すことが可能です。
6-1. 加工精度を高めるための技術と工夫
タフピッチ銅の精密なフライス加工には、徹底した工程管理が求められます。この金属は、その高い熱伝導性と加工性により、電子部品や半導体の試作品作りにしばしば用いられます。しかし、その柔らかさが原因で、加工時に形状が変形しやすいという課題があります。そこで、成功へ導くためには、適切な切削条件の選択、専用の刃物使用、そして微細なバリ取り作業が重要です。例えば、フライス加工においては、タフピッチ銅の特性に合わせた低速での切削や、熱影響を抑える冷却技術の使用が効果的です。さらに、高精度を要する試作では、CNCマシンによるプログラム制御が精度のブレを最小限に抑えます。これらのステップを踏むことで、タフピッチ銅の精密なフライス加工が可能となり、信頼の置ける試作品が完成します。最終的には、これらの工夫を通じて、精度が高く、再現性のある加工が保証されるのです。
6-2. タフピッチ銅 試作品の精度評価方法
タフピッチ銅の精密なフライス加工での試作は、成功へのステップが重要です。まず、タフピッチ銅はその優れた電気伝導性と加工性から、精密機器の部品などに幅広く使用されています。しかし、加工時にはその柔軟性が課題となることがあります。成功の鍵は、高い精度を確保しつつも、材料の特性に合わせた加工方法を見つけ出すことにあります。具体例として、工具の選定は非常に重要で、タフピッチ銅に適した切削工具や条件を選び、切削速度や送り速度を精密に制御する必要があります。フライス加工においては、冷却液の利用もまた、材料の熱変形を防ぐために欠かせません。さらに、試作段階では、加工後の寸法測定や表面粗さの評価を通じて、加工精度を徹底的に検証することが大切です。これらのステップを経ることで、タフピッチ銅の精密なフライス加工における試作は成功すると言えるでしょう。
7. 長野県輸出産業とタフピッチ銅 フライス加工技術
タフピッチ銅の精密なフライス加工は、試作を成功させるためには非常に重要です。なぜなら、タフピッチ銅は優れた電気伝導性を持つ一方で、加工が難しい材料としても知られているためです。成功の秘訣は、正確なカットが可能な高品質な工具の選択と、適切な加工方法の適用にあります。例えば、フライス加工においては、切削速度や送り速度、そして切削液の使用が重要になってきます。これらを適切に組み合わせることにより、加工中の振動や熱を抑え、精度の高い加工が可能になります。特に、試作段階では、加工パラメーターの微調整が重要となり、経験豊富な技術者の知識が必要です。タフピッチ銅のフライス加工を成功させるためには、これらのステップを慎重に踏むことが不可欠です。
8. タフピッチ銅を用いた核融合技術への応用
タフピッチ銅の精密なフライス加工は、成功するためにはいくつかの重要なステップを踏む必要があります。まず、タフピッチ銅はその優れた電気伝導性と加工性から試作品製作に適していますが、正確な加工には経験と専門知識が必要です。加工の成功は、適切な工具選定、切削速度、送り速度の最適化から始まります。例えば、精密なフライス加工には、硬度や切れ味が長持ちする超硬質材料の工具が選ばれます。また、タフピッチ銅特有の焼け付きを防ぐために適切な冷却剤の使用も不可欠です。試作段階で複数の加工条件を試し、最適な条件を見出すことが成功への鍵となります。綿密な準備と試行錯誤を重ねることで、精密な試作品を成功させることができるのです。
9. 高精度空気軸受スピンドルのタフピッチ銅フライス加工
タフピッチ銅の精密なフライス加工は、試作における成功へのカギとなります。タフピッチ銅は熱伝導性や電気伝導性に優れているため、電子部品や放熱材料などで広く利用されています。しかし、その硬さと粘り強さが加工を難しくする要因にもなるため、精密な加工技術が求められます。例えば、正確な寸法を実現するためには、適切な切削工具の選択や、切削速度、送り速度の最適化が不可欠です。さらに、加工時の振動を抑えるための工夫も必要です。これらの点に注意を払い、細心の注意をもってフライス加工を行えば、高品質なタフピッチ銅の試作品を創出することが可能です。最終的には、これらのステップを踏むことで、精密なフライス加工が実現され、試作の成功へとつながるのです。
まとめ
タフピッチ銅を使用したフライス加工の試作を成功させるためには、まず適切な設計と計画が必要です。材料の特性や加工条件などを考慮して工程を慎重に進めることが重要です。また、適切な切削工具や加工方法を選択し、精密な加工を行うことがポイントです。試作品の仕上がりを高品質に保つためには、適切な検査と修正を繰り返すことが求められます。