高精度フライス加工を実現するためのステップバイステップガイド
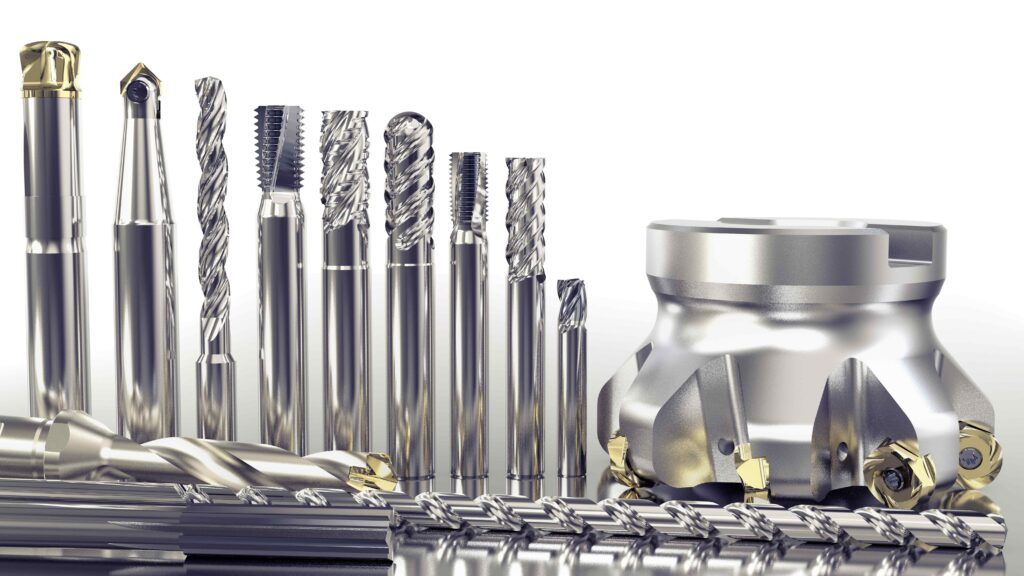
精密な加工が求められる現代の製造業において、高精度フライス加工は不可欠な技術となっています。しかし、「高精度フライス加工を始めたいけれど、どうすればいいのかわからない…」という悩みを抱えている方も多いのではないでしょうか。そこで、私たちは「高精度フライス加工を実現するためのステップバイステップガイド」を作成しました。
このガイドでは、以下の質問にお答えします:
- 高精度フライス加工とは何か?
- どのように高精度な加工を実現するのか?
- 初心者が知っておくべき基本的な知識やステップは何か?
高精度なフライス加工は、製品の品質や生産効率に大きく影響します。また、正確な加工を行うことで、競争力を高めることも可能です。本記事では、初心者でもわかりやすく高精度フライス加工の実現方法を解説し、実際に業務に活かすためのヒントを提供します。さあ、一緒に高精度フライス加工の世界へ踏み出しましょう!
高精度フライス加工を実現する方法
フライス加工の基本と精度向上の重要性
- フライス加工は、切削工具を回転させながらワークピースを移動させる加工方法で、複雑な形状を精密に削ることができます。精度の向上は、部品の寸法や表面品質、形状精度に大きな影響を与え、機械部品の信頼性と性能に直結します。
- 精度向上のためには、加工機の剛性、切削条件、工具の状態を最適化することが重要です。
高精度フライス加工を実現するための機械選定
- 高精度機械選定のポイント:
- 剛性の高いフライス盤: 剛性の高い機械は加工中の変形を抑え、高精度な加工が可能です。
- 精密な送り装置: 高精度な送りシステムを持つ機械は、位置決め精度を向上させ、寸法精度を保ちます。
- 振動抑制技術: 振動を抑える設計が施された機械は、加工精度を大幅に向上させます。
刃物の選定とその影響
- 切削工具の選定:
- 材質: 高精度を求める場合、耐摩耗性が高い工具(例: セラミックやダイヤモンドコーティング工具)を使用することが推奨されます。
- 形状: 刃先の形状が適切でないと、加工中の振動や切削力が不安定になります。精密加工には、精密な刃物の形状が求められます。
- 工具の摩耗管理: 刃物の摩耗を定期的にチェックし、早期に交換することが、精度を維持するために重要です。
加工条件の最適化
- 切削条件: 高精度加工には、最適な切削速度、送り速度、切込み量を設定することが必要です。特に、切削抵抗を最小化するために、適切な冷却と潤滑の選定も大切です。
- 温度管理: 加工中に発生する熱を管理することが、寸法精度を維持するために重要です。冷却装置や工具の熱膨張特性を考慮する必要があります。
旋盤加工とフライス加工の精度比較
旋盤加工とフライス加工の基本的な違い
- 旋盤加工は、ワークピースを回転させて固定した工具で切削する方法で、円形の形状や回転部品に適しています。フライス加工は、回転する切削工具でワークピースを加工する方法で、平面や複雑な形状の部品に使用されます。
- 旋盤加工は比較的高精度で円形の部品を加工するのに適しており、フライス加工は形状自由度が高い分、精度を保つためには細かい調整が必要です。
精度向上のためのアプローチの違い
- 旋盤加工の精度向上:
- 高精度な旋盤を使用し、ワークのバランスを取ることで、切削中の振動を抑え、精度を保ちます。
- 切削油の適切な使用や、適切な回転数の選定が重要です。
- フライス加工の精度向上:
- 加工機の剛性や工具の選定、切削条件の最適化に加え、切削液の管理が重要です。
- 加工中に発生する熱や振動を最小限に抑えるための技術が求められます。
それぞれの加工法の利点と欠点
機械の剛性や工具の摩耗が精度に影響を与えやすい。
旋盤加工の利点:
高精度で円形部品を製造できる。
比較的単純な工程で高精度を達成できる。
旋盤加工の欠点:
円形の部品以外には不向き。
形状の自由度が少ない。
フライス加工の利点:
複雑な形状や角度のある部品を加工できる。
高精度な平面や溝の加工が可能。
フライス加工の欠点:
精度を保つためには細かい調整と高い技術が必要。
機械の剛性や工具の摩耗が精度に影響を与えやすい。
鉄鋼部品のフライス加工で精度を確保するための対策
鉄鋼部品の特性と加工の注意点
- 鉄鋼部品の特性:
- 硬度と靭性: 鉄鋼は一般的に硬度が高く、切削時には工具に対する負荷が大きくなりやすいです。そのため、切削工具の耐摩耗性が求められます。
- 熱膨張: 加工中に熱が発生しやすい鉄鋼は、温度変化により部品が膨張しやすいため、精度に影響を与える可能性があります。
- 切削力の増大: 高硬度の鉄鋼を切削する場合、切削力が大きくなり、機械や治具に不安定な振動を引き起こすことがあります。
- 加工時の注意点:
- 適切な切削条件を選定し、切削液を使用して熱の発生を抑えることが重要です。
- 工具の材質とコーティングも重要で、硬度に対応した工具を選定することが求められます。
- 加工中の振動を抑えるために、適切な機械の剛性と安定した加工条件が必要です。
精度を確保するための治具の重要性
- 治具の役割:
- ワークの固定: 精度の高いフライス加工には、ワークがしっかりと固定されていることが必須です。精度を確保するためには、専用の治具を使用してワークの位置決めを正確に行います。
- 加工中の振動抑制: 治具は、加工中に発生する振動を最小限に抑える役割も果たします。治具の剛性や設計が、最終的な製品精度に大きな影響を与えます。
- 高精度治具の使用: 精度が要求される部品を加工する場合、治具自体の精度が非常に重要です。治具の設計においては、部品の寸法公差に合わせた高精度な加工が必要です。
加工後の検査と品質管理
- 加工後の検査:
- 加工後に、寸法検査や形状検査を実施し、仕様通りの部品が完成していることを確認します。
- 非接触測定機器(例: 三次元測定機、レーザー測定器)を使用して、表面の精度や寸法精度を高精度にチェックします。
- 表面粗さや形状精度の確認も重要です。これにより、製品の機能性を確保します。
- 品質管理:
- 継続的な品質管理が精度を保つために不可欠です。加工時に得られたデータを基に、次回の加工条件の見直しや改善点を反映させることが求められます。
- 製品の仕様に対して公差範囲を設定し、その範囲内での品質を保つために定期的に検査を行い、必要に応じて加工条件を調整します。
高精度加工を実現するために必要な基本的な要素
加工環境の整備
- 清潔で安定した環境:
- 高精度加工を実現するためには、加工機や工具が清潔な環境で使用されることが重要です。加工中の粉塵や油汚れなどが精度に悪影響を与える可能性があります。
- 温度や湿度が安定している環境を維持することで、機械の熱膨張を抑制し、寸法精度を安定させることができます。
- 機械のメンテナンス:
- 高精度な加工を行うためには、定期的な機械メンテナンスが欠かせません。摩耗した部品や経年劣化した部品の交換、潤滑油の管理などが精度維持に役立ちます。
技術者のスキル向上
- 技術者の役割:
- 加工精度を確保するためには、技術者のスキルも重要です。特に、機械設定や加工条件の選定、工具の交換タイミング、精密検査の実施など、経験と知識を活かす必要があります。
- 技術者のトレーニングを定期的に行い、最新の技術や設備に対応できるようにすることが、高精度加工を支える要素となります。
継続的な改善とフィードバックの重要性
加工条件や機械性能、材料の特性などをデータとして蓄積し、それを元に次回の加工に生かすことで、より高精度な加工が可能になります。
改善プロセス:
高精度加工を持続するためには、加工後の結果をフィードバックし、問題点を特定して改善を行うプロセスが不可欠です。継続的な改善により、精度が向上し、品質が安定します。
加工条件や機械性能、材料の特性などをデータとして蓄積し、それを元に次回の加工に生かすことで、より高精度な加工が可能になります。
まとめ
高精度フライス加工を実現するためには、まず適切な工具と材料を選定し、次に機械の設定を正確に行います。加工条件を最適化し、定期的なメンテナンスを行うことで、精度を保ちます。また、試作品を作成し、フィードバックを基に改善を重ねることが重要です。これらのステップを踏むことで、品質の高い製品を生み出すことができます。