高精度が魅力!小型精密NCフライスでできること
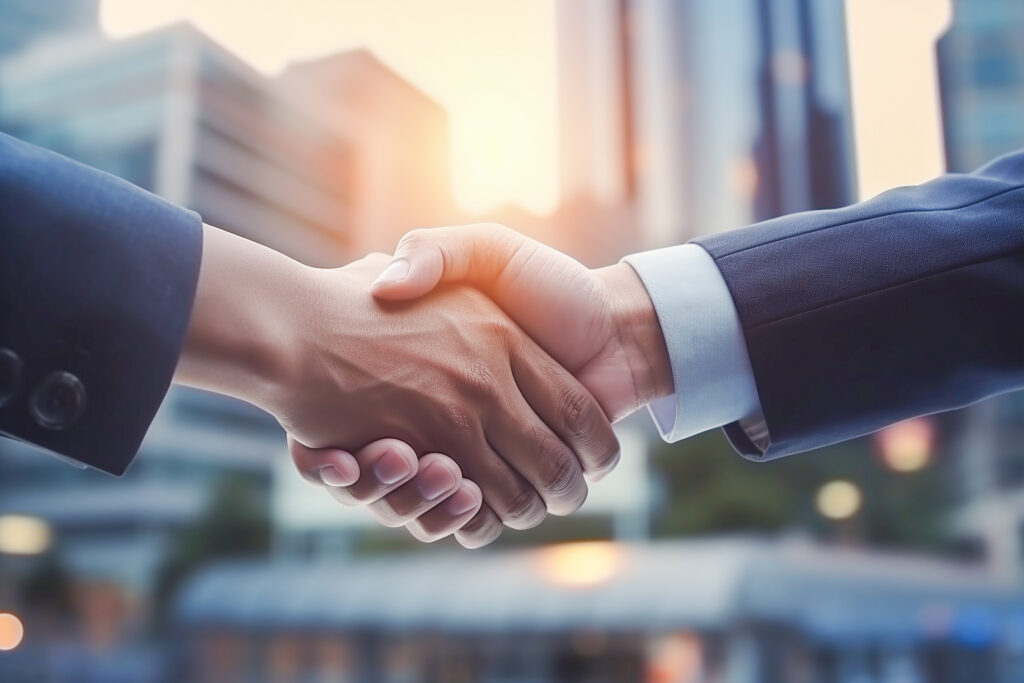
小型精密NCフライスという技術は、その高い精度と効率性によって注目を集めています。その魅力とは一体何でしょうか?本記事では、小型精密NCフライスの可能性に迫ります。
機械加工の世界において、小型精密NCフライスは革新的な存在として位置づけられています。その高い精度によって、細かなディテールや複雑な形状を効率的に加工することが可能となり、さまざまな産業分野で活躍しています。
本記事では、小型精密NCフライスの基本的な仕組みから、実際にどのようなことが可能なのかまで、分かりやすく解説していきます。小型精密NCフライスの世界に踏み込んでみたい方々にとって、必見の内容となっています。どうぞお楽しみに!
小型精密NCフライスの基本
小型精密NCフライスとは
小型精密NCフライスとは、高い精度を持ちながらコンパクトなサイズで機能する工作機械です。この機械は、非常に細かい作業を必要とする産業や製造現場で重宝されています。例えば、精密部品や微細加工が必要な部品を作る際に活躍します。このようなハイテク分野だけでなく、医療機器や航空機部品など、さまざまな産業で活用されています。 小型精密NCフライスは、コンピュータ制御によって高い精度を実現し、複雑な形状の加工も可能とします。そのため、製品の品質向上や生産効率の向上に貢献しています。さらに、省スペースで設置できるため、工場内のレイアウトにおいても優れた選択肢となっています。 小型精密NCフライスは、現代の製造業において重要な役割を果たしており、その需要は今後ますます高まることが期待されています。高精度が魅力!小型精密NCフライスでできること
高精度加工は、製品の精度や品質を向上させるうえで非常に重要です。小型精密NCフライスは、この高度な加工を可能にし、さまざまな産業で活躍しています。例えば、自動車産業ではエンジン部品や歯車などの精密パーツを製造する際に欠かせない技術です。 NCフライスを使用することで、金属やプラスチックなどの素材から、複雑な形状や細かな加工が可能となります。これにより、製品の耐久性や性能が向上し、高付加価値製品の製造に貢献します。 小型精密NCフライスの登場により、精密加工が容易になり、製品の品質向上に貢献しています。これにより、さまざまな産業分野で革新的な製品開発が可能となり、市場競争力を高めることができます。小型NCフライス盤の種類と特徴
1. 小型NCフライス盤の概要
項目 | 詳細情報 |
---|---|
定義 | 小型のコンピュータ数値制御(CNC)フライス盤で、精密な切削加工が可能な機械。 |
用途 | 精密部品や小型部品の加工に使用される。特に、小さなサイズの部品や複雑な形状の加工に適している。 |
特徴 | – コンパクトな設計 – 高精度な加工 – 多機能性で、小さな作業場でも使用可能 |
2. 小型NCフライス盤の種類
種類 | 詳細情報 |
---|---|
立形NCフライス盤 | – 垂直方向に工具が回転し、材料に対して切削を行う。 – 高精度な加工が可能で、小型部品に最適。 |
横形NCフライス盤 | – 水平回転する工具を使用。 – 幅広い加工が可能で、高速な切削が特徴。 |
マルチタスクNCフライス盤 | – フライス加工、ドリル加工、タッピングなどを1台で行える多機能タイプ。 – 複雑な部品の加工に適している。 |
3. 小型NCフライス盤の特徴
特徴 | 詳細情報 |
---|---|
精度の高さ | – 高精度な切削が可能で、微細な部品加工に対応。 |
コンパクト設計 | – 小型で省スペースのため、小さな作業場でも設置可能。 |
高速加工 | – 高速で効率的な加工が可能で、短時間での生産が実現。 |
自動化の柔軟性 | – プログラムによる自動加工が可能で、人手を減らし作業効率が向上。 |
機能性の多様性 | – 様々な機能が搭載されており、複雑な形状や多品種小ロットにも対応可能。 |
4. 小型NCフライス盤の利点と欠点
利点 | 欠点 |
---|---|
– コンパクトで省スペース | – 高速加工を行うときに、発生する熱が問題になる場合がある。 |
– 高精度な加工が可能 | – 小型のため、大型部品の加工には不向き。 |
– 高速で効率的な加工が可能 | – 機械の価格が比較的高価であることがある。 |
詳細情報
- 小型NCフライス盤は、精密で効率的な加工を実現するための機械であり、特に小型部品や複雑な形状の加工に優れています。これらの機械は、コンパクトで省スペースな設計が特徴であり、限られた作業場でも使用することができます。
- 小型NCフライス盤には、立形、横形、マルチタスクタイプがあり、それぞれ異なる加工ニーズに対応します。立形NCフライス盤は精密な加工に優れ、横形NCフライス盤は高速加工に適しています。マルチタスクNCフライス盤は、複数の加工機能を一台でこなせるため、多品種小ロットの生産に最適です。
- 高精度な加工、コンパクトな設計、高速な切削などの特徴があり、効率的な生産を実現しますが、価格が高価であり、大型部品の加工には不向きという点があります。
加工精度向上のための方法
正確な設計とプログラミング
1. 設計段階の重要性
項目 | 詳細情報 |
---|---|
CAD設計 | – コンピュータ支援設計(CAD)を使用して、製品の図面を正確に作成する。 – 3Dモデリングにより、部品同士の干渉や公差を事前に検討できる。 |
公差の設定 | – 設計時に必要な公差を正確に設定し、加工精度に影響を与えないようにする。 – 設計段階で過度な公差を避けることが重要。 |
材料選定 | – 使用する材料の特性(硬さ、加工性、耐摩耗性など)を考慮し、設計を行う。 – 材料の変形や収縮を予測して設計に反映させる。 |
2. プログラミングの精度向上
方法 | 詳細情報 |
---|---|
CAMプログラミング | – コンピュータ支援製造(CAM)を使用して、CADデータを基に正確な加工プログラムを生成する。 – 適切な加工順序やツールの選定を行う。 |
Gコードの最適化 | – Gコード(数値制御)のプログラムは、加工の効率と精度に影響を与えるため、最適化を行う。 – 不必要な動作や加速・減速を避け、加工時間の短縮を図る。 |
シミュレーション | – 加工前にシミュレーションを行い、干渉や誤動作を検出して修正する。 – プログラムが実際の加工と一致することを確認する。 |
3. 高精度加工のためのツール選定
方法 | 詳細情報 |
---|---|
ツールの選定 | – 加工する材料や形状に適した工具を選定する。 – 高精度の工具を選ぶことで、加工精度の向上を図る。 |
ツールライフの管理 | – ツールの摩耗や破損を避けるため、適切に管理し、定期的に交換する。 – ツールの寿命を最大限に活用するための管理が重要。 |
4. 加工条件の最適化
項目 | 詳細情報 |
---|---|
切削条件の調整 | – 切削速度、送り速度、切削深さなどを最適に設定することで、加工精度を確保する。 – 適切な条件で加工することで、熱変形や工具の摩耗を抑える。 |
加工順序の見直し | – 加工の順序を適切に設定することで、工具の動作を最適化し、誤差を減らす。 – 事前に加工する部分を見極め、順序を変更することが精度向上に繋がる。 |
5. 加工後の調整
方法 | 詳細情報 |
---|---|
測定と調整 | – 加工後の部品は、三次元測定機やマイクロメーターなどで精度を確認する。 – 測定結果に基づき、プログラムや機械設定を微調整する。 |
仕上げ加工の最適化 | – 仕上げ工程では、より高精度な加工が求められるため、精密加工ツールの使用や細かな設定を行う。 |
詳細情報
- 正確な設計とプログラミングは、精度高い加工を実現するための基盤です。設計段階でのCADデータ作成や公差設定、材料選定が重要であり、これらの要素が加工精度に直結します。
- プログラミング段階では、CAMシステムを活用して加工プログラムを作成し、Gコードの最適化とシミュレーションにより、加工前に誤動作や干渉を検出して修正します。
- 加工においては、精度向上のためのツール選定や最適な加工条件が必要です。切削条件を調整し、加工順序を見直すことで、より精密な加工が可能になります。
- 加工後には、測定を行い、必要に応じて微調整を行うことで、最終的な加工精度を確認・向上させることができます。
適切な工具と材料の選択
1. 工具の選定
項目 | 詳細情報 |
---|---|
工具の種類 | – 加工する素材や形状に適した工具を選定する。 – 旋盤、フライス盤、ドリルなど、目的に応じた工具を選ぶ。 |
材料特性に適した工具 | – 材料の硬さや加工の難易度に応じて工具の素材を選ぶ。 – 高硬度材料には超硬工具、低硬度材料にはHSS工具など。 |
切削性能 | – 工具の切削性能(切れ味、耐摩耗性、耐熱性)を確認し、最適なものを選ぶ。 – 長寿命な工具を選ぶことで、加工精度の安定化とコスト削減が可能。 |
工具の形状 | – 加工する形状に合わせた工具(エンドミル、ボールエンドミルなど)を選定する。 – 複雑な形状や細部の加工には高精度な工具が必要。 |
2. 材料の選定
項目 | 詳細情報 |
---|---|
材料の種類 | – 加工する部品に適した材料を選定する。 – 金属材料、樹脂材料、複合材料など、目的に応じた素材を選ぶ。 |
材料の機械的特性 | – 材料の硬度、引張強度、耐摩耗性などの特性を考慮して選定する。 – 高強度の部品には高強度鋼、耐摩耗性が求められる部品には特殊鋼やセラミックなど。 |
加工性 | – 材料の加工のしやすさ(切削性、鍛造性)を評価する。 – 加工の難易度に応じて、工具や加工方法を調整する。 |
材料のコスト | – 選定する材料のコストと必要な性能のバランスを取る。 – 過剰な性能が求められない場合は、コスト削減を図る。 |
3. 工具と材料の相性
項目 | 詳細情報 |
---|---|
材料と工具の摩擦 | – 材料と工具の間に発生する摩擦を考慮し、工具の素材を選定する。 – 高摩擦を避けるために、冷却剤や潤滑剤を使用する場合がある。 |
材料の熱伝導性 | – 材料の熱伝導性を考慮し、熱による変形を抑えるために適切な工具を選ぶ。 – 熱伝導性の低い材料では、冷却が重要になることがある。 |
加工条件との調和 | – 材料の特性と加工条件(切削速度、送り速度)に合わせた工具選定が重要。 – 適切な工具と材料の組み合わせにより、加工の安定性と精度が向上する。 |
4. 工具の寿命とメンテナンス
項目 | 詳細情報 |
---|---|
工具寿命の管理 | – 工具の寿命を延ばすために、適切な切削条件で使用する。 – 切削速度や送り速度を適切に調整することが重要。 |
定期的な点検 | – 工具の摩耗や破損を防ぐため、定期的に点検を行う。 – 工具の交換時期を予測し、事前に準備しておくことで生産効率を保つ。 |
冷却と潤滑の管理 | – 工具と材料の相性を考慮し、冷却剤や潤滑剤を適切に使用する。 – 過度の熱が発生すると工具の寿命が短くなるため、冷却を怠らない。 |
詳細情報
- 工具の選定では、加工する部品の形状や材質に合わせて最適な工具を選ぶことが求められます。適切な工具を選ぶことで、加工精度や加工効率が大きく向上します。
- 材料の選定は、部品の機械的特性や使用環境に合った素材を選ぶことが重要です。材料の特性を理解し、求められる性能を満たす材料を選ぶことが、長期的な品質維持に繋がります。
- 工具と材料の相性を考慮することで、摩耗や熱による変形を抑えることができます。冷却剤や潤滑剤の使用も、工具の寿命を延ばし、安定した加工を可能にします。
- 工具の寿命管理においては、適切な切削条件と定期的な点検が必要です。これにより、予期せぬ故障を防ぎ、安定した生産を確保することができます。
切削条件の最適化
1. 切削速度の最適化
項目 | 詳細情報 |
---|---|
切削速度の定義 | – 切削速度は工具の先端が材料を削る速度で、通常はm/min(メートル毎分)で表されます。 |
切削材料に応じた調整 | – 材料の硬さや種類に応じて切削速度を調整する。 – 軟鋼では高速切削が可能だが、硬鋼や高硬度材料では低速での加工が必要。 |
目標 | – 切削速度を最適化することで、工具寿命の延長や加工効率の向上が可能です。 – 最適な切削速度は、加工精度を保ちながら、過度の熱発生を抑え、効率的に加工するために重要です。 |
2. 送り速度の調整
項目 | 詳細情報 |
---|---|
送り速度の定義 | – 送り速度は、材料を削るために工具が1回転する間に進む距離を指し、通常はmm/minで表されます。 |
材料特性に基づく調整 | – 硬度が高い材料では、送り速度を低く設定することで加工がスムーズになります。 – 軟鋼やアルミニウムでは高速の送りが可能です。 |
目標 | – 送り速度の最適化は、加工時間を短縮し、効率的に作業を進めるために重要です。 – 高速な送り速度は、適切な切削条件を確保するために調整する必要があります。 |
3. 切削深さの設定
項目 | 詳細情報 |
---|---|
切削深さの定義 | – 切削深さは、工具が一度の切削で材料を削る厚さで、通常はmmで表されます。 |
材料に対する適応 | – 硬い材料では、浅い切削深さに設定して過度な負荷をかけないようにします。 – 軟鋼やアルミなど、加工しやすい材料では深い切削深さが可能です。 |
目標 | – 切削深さの適切な設定は、加工精度の向上と工具寿命の最適化に寄与します。 – 過度の切削深さは工具の摩耗を早めるため、最適な深さに調整することが必要です。 |
4. 切削液の使用
項目 | 詳細情報 |
---|---|
切削液の役割 | – 切削液は摩擦の低減、冷却、工具の潤滑を助けるために使用されます。 |
種類と選定 | – 水溶性、油性、合成タイプの切削液があり、加工する材料や切削条件に応じて選定します。 – 高速切削では冷却性能が重要となるため、冷却性能が高い切削液を選ぶことが多いです。 |
目標 | – 切削液を最適に使用することで、加工中の温度上昇を抑え、工具の寿命を延ばすことができます。 |
5. 研削力と加工温度の最適化
項目 | 詳細情報 |
---|---|
研削力の調整 | – 高い研削力は切削効率を向上させますが、過度に強い研削力は工具や材料に過負荷をかけるため、適切に調整する必要があります。 |
加工温度の管理 | – 加工温度が高くなると、材料の特性や工具の耐久性に影響を与えるため、冷却方法の最適化が重要です。 |
目標 | – 研削力と温度の最適化を行うことで、加工精度を保ちながら、工具寿命や品質を向上させることができます。 |
詳細情報
- 切削速度の最適化は、材料の種類に応じた適切な速度設定を行うことが必要です。過度の切削速度は工具を早く摩耗させたり、部品に不良を引き起こす原因になるため、適切な調整が求められます。
- 送り速度の調整は、加工時間の効率化に直接関係します。適切な送り速度を選定することで、無駄なエネルギー消費を避け、精度を保ちながら速やかな加工を実現できます。
- 切削深さの設定においては、材料の硬度に合わせて深さを調整することで、加工精度を保ちながら工具への負担を減らすことができます。
- 切削液の使用は、工具寿命を延ばし、加工中の熱の影響を抑えるために欠かせません。冷却・潤滑が効果的に行われることで、長時間の安定した加工が可能になります。
- 研削力と加工温度の最適化では、過度な温度上昇や研削力の増加を抑えることが、加工精度や工具寿命を保つために重要です。特に硬度の高い材料の加工時には、冷却方法に注意を払う必要があります。
メンテナンスと校正
1. 定期的なメンテナンスの重要性
項目 | 詳細情報 |
---|---|
メンテナンスの目的 | – 機械の性能を維持し、故障を予防するために必要な作業です。 |
主な作業内容 | – 日常的な清掃、潤滑、冷却システムの点検 – 工具や部品の摩耗チェック – 機械部品の交換や修理 |
目標 | – 定期的なメンテナンスを行うことで、機械の故障を未然に防ぎ、生産性を維持します。 |
2. 校正と精度の確保
項目 | 詳細情報 |
---|---|
校正の目的 | – 機械の測定精度や加工精度を確認し、正確な製品を作成するために必要です。 |
校正方法 | – 校正ゲージや標準工具を使用して、加工機械の精度を確認 – 定期的に測定器具のキャリブレーションを行う |
目標 | – 校正を定期的に実施することで、加工精度を保ち、品質の向上を図ります。 |
3. 機械の清掃と潤滑
項目 | 詳細情報 |
---|---|
清掃の目的 | – 機械内に積もった切削屑や汚れを取り除き、機械の運転状態を良好に保つためです。 |
清掃方法 | – 高圧エアーでの清掃、油分や切削屑の除去 – 冷却液の交換やフィルター清掃 |
目標 | – 機械内の汚れを定期的に除去することで、摩耗や故障を防ぎます。 |
4. 部品の摩耗チェックと交換
項目 | 詳細情報 |
---|---|
摩耗チェックの目的 | – 工具や機械部品が摩耗していないか定期的にチェックし、必要な部品交換を行います。 |
摩耗チェックの方法 | – 部品に異常な摩耗が見られた場合、早期に交換します。 – 測定機器を使って精度の低下を確認 |
目標 | – 摩耗した部品を交換することで、機械の精度や性能を維持し、長期的に安定した生産を実現します。 |
5. 加工後の点検と調整
項目 | 詳細情報 |
---|---|
点検の目的 | – 加工後に製品や機械の状態を確認し、必要に応じて調整を行います。 |
点検内容 | – 加工精度、仕上がり状態、部品の寸法精度のチェック – 不良があれば、機械の設定を再確認して調整 |
目標 | – 加工後の点検で問題を早期に発見し、修正することで製品の品質を確保します。 |
詳細情報
- 定期的なメンテナンスは、機械の耐用年数を延ばし、生産ラインの停止を防ぐために不可欠です。これにより、生産性が維持され、機械の突発的な故障を未然に防ぐことができます。
- 校正と精度の確保は、製品の品質を保証するために重要です。定期的な校正は、製品の寸法や公差を守るために必要な作業であり、機械の設定ミスを防ぎます。
- 清掃と潤滑は、機械の長寿命を確保し、故障を防ぐために必要です。切削中に発生する熱や摩擦を適切に処理することで、機械の精度を保ち、故障を減らすことができます。
- 部品の摩耗チェックと交換は、部品の劣化を早期に発見し、交換することで、機械のパフォーマンスを維持するための重要な作業です。
- 加工後の点検と調整は、製品の品質を確認するために必須です。製品に不良が見つかった場合、機械の設定や加工条件を調整し、品質を確保します。
小型精密切削機のトラブルシューティング
一般的なトラブルとその原因
トラブル例 | 原因 |
---|---|
切削精度の低下 | – 工具の摩耗や不良 – 加工機械の振動や不安定な設置 – 加工条件の不適切(切削速度、送り速度) |
表面仕上がり不良 | – 不適切な工具選定 – 過度な切削力 – 冷却液の不足または不適切な使用 |
オーバーヒート | – 切削条件が過負荷 – 冷却システムの不調や不足 – 過度な摩擦が発生している |
切削音の異常 | – 工具の摩耗 – 加工物の材質不良 – 機械の摩耗や部品の不具合 |
加工物の歪み | – 加工中の温度変化 – 過剰な切削力や振動 – 加工物の取り付け不良 |
詳細情報
- 切削精度の低下:
- 原因: 工具の摩耗や不良により、加工精度が低下することがあります。また、機械の設置が不安定だと振動が発生し、精度が落ちることもあります。加工条件(切削速度、送り速度)が適切でない場合も精度に影響を与えます。
- 対策: 定期的な工具の交換と点検を行い、機械設置の安定性を確保します。加工条件の見直しも重要です。
- 表面仕上がり不良:
- 原因: 工具選定が不適切な場合や、過度な切削力が加わると、仕上がりが不良になります。また、冷却液の不足や不適切な使用も仕上がりに悪影響を及ぼします。
- 対策: 工具の選定を適切に行い、必要に応じて切削条件を調整します。また、冷却液の管理と使用方法にも注意が必要です。
- オーバーヒート:
- 原因: 切削条件が過負荷になっている場合や、冷却システムが正常に機能していない場合にオーバーヒートが発生します。過度な摩擦も原因となることがあります。
- 対策: 切削条件の見直しや、冷却システムの点検を行い、必要に応じて冷却液の交換を行います。
- 切削音の異常:
- 原因: 工具の摩耗や加工物の材質不良、または機械部品の不具合により異常な音が発生することがあります。
- 対策: 工具の定期的な点検と交換、加工物の材質チェックを行い、機械のメンテナンスを徹底します。
- 加工物の歪み:
- 原因: 加工中の温度変化や過剰な切削力、振動が原因で加工物が歪むことがあります。また、加工物の取り付けが不適切な場合も歪みが発生します。
- 対策: 加工物の取り付けを安定させ、切削力を適切に調整します。加工中の温度管理や振動対策も有効です。
効果的なトラブル解決方法
1. トラブルシューティングの基本ステップ
ステップ | 詳細情報 |
---|---|
1. 問題の特定 | – 発生している問題の症状を詳細に確認します。 – 異常がどの部分で発生しているのかを特定します。 |
2. 原因の分析 | – 問題の根本的な原因を洗い出し、可能性のある原因をリストアップします。 |
3. 仮説の立てる | – 複数の原因に基づいた仮説を立て、それぞれを検証するための手順を決めます。 |
4. 解決策の実施 | – 最も可能性の高い原因に基づいた修正作業を行います。 – 必要に応じて部品交換や調整を行います。 |
5. 効果の確認 | – 解決策を実施した後、問題が解消されたか確認します。 – 再発防止策を検討します。 |
2. 具体的なトラブル解決方法
トラブル例 | 解決方法 |
---|---|
切削精度の低下 | – 工具の定期的な交換と研磨を行う – 加工条件の再確認と最適化 – 機械の設置状態を確認し、安定化させる |
表面仕上がり不良 | – 工具の選定を見直し、適切な工具を使用 – 切削条件を調整し、過度な切削力を避ける – 冷却液の補充と適切な使用方法を徹底する |
オーバーヒート | – 切削条件を適正範囲内に調整する – 冷却システムの点検と必要な補修を行う – 速やかに機械を冷却し、過負荷を避ける |
切削音の異常 | – 工具や部品の摩耗状態を確認し、必要な交換を行う – 加工物の材質チェックを実施し、不良品は取り換える – 機械の部品の不具合を修正する |
加工物の歪み | – 加工物の取り付けを再確認し、安定させる – 切削力を適切に調整し、振動を減少させる – 温度変化を管理するための対策を講じる |
3. 予防と再発防止策
トラブル例 | 再発防止策 |
---|---|
切削精度の低下 | – 定期的なメンテナンスと工具管理 – 加工条件の定期的な見直し |
表面仕上がり不良 | – 工具の品質管理と適切な使用 – 定期的な冷却液の交換 |
オーバーヒート | – 加工前に冷却システムの状態を確認 – 切削条件の適正化 |
切削音の異常 | – 機械の振動テストやチェック – 工具と機械の適切なメンテナンス |
加工物の歪み | – 加工物の取り付けを強化 – 加工環境の温度や湿度の管理 |
詳細情報
- トラブルシューティングの基本ステップ: 問題が発生した場合、まずは症状を詳細に把握し、どの部分で問題が発生しているのかを特定します。次に、その原因を分析し、仮説を立てます。原因が分かったら、最適な解決策を実施し、効果を確認します。もし再発の兆候が見られた場合は、再発防止策を講じます。
- 具体的なトラブル解決方法: 切削精度の低下や表面仕上がり不良などの問題には、工具や加工条件の調整、冷却液の管理などが有効です。オーバーヒートや異常音の発生は、冷却システムの点検や摩耗部品の交換を通じて解決できます。また、加工物の歪みは取り付けの安定化や切削力の調整で改善されます。
- 予防と再発防止策: トラブルを予防するためには、定期的なメンテナンスやチェックが重要です。特に、工具の交換、加工条件の適正化、冷却液の管理を行うことで、多くのトラブルの再発を防ぐことができます。また、加工物の取り付けや振動管理も重要な予防策となります。
予防策と定期的な点検
1. 予防策の重要性
予防策 | 詳細情報 |
---|---|
定期的なメンテナンス | – 機械や工具の状態をチェックし、摩耗や不具合を早期に発見して修理を行います。 – 機械が最適な状態で動作するようにすることで、長期的に安定したパフォーマンスを維持します。 |
工具の適切な管理 | – 工具の摩耗状態や性能を定期的に確認し、必要に応じて交換や研磨を行います。 – 使用頻度や材料によって最適な工具を選定し、過度な摩耗を防ぎます。 |
清掃と冷却システムの点検 | – 機械内部の清掃を定期的に行い、削りくずや汚れが機械の動作に支障をきたさないようにします。 – 冷却液の補充や交換を行い、冷却システムの効率を維持します。 |
加工条件の見直し | – 時折、切削条件(回転速度、切込み量、送り速度など)を再確認し、最適化します。 – 工具と材料に適した条件を選ぶことで、精度の向上とトラブルの予防が可能です。 |
2. 定期的な点検の実施
点検項目 | 詳細情報 |
---|---|
機械本体の点検 | – 機械の可動部分(スライド、リニアガイド、ボールネジ)の状態を定期的に点検します。 – 潤滑状態を確認し、必要に応じてグリースの補充や交換を行います。 |
電気系統の点検 | – 電気系統(モーター、配線、センサー)の状態をチェックし、異常がないか確認します。 – 配線の劣化や接触不良を防ぐため、定期的に点検とクリーニングを行います。 |
精度の確認 | – 加工精度を測定し、機械の精度が維持されているかチェックします。 – 定期的な校正とジグ、フィクスチャーの調整を行い、精度を保証します。 |
冷却システムの点検 | – 冷却液の量と品質を確認し、必要に応じて交換を行います。 – ポンプや配管の漏れや詰まりをチェックし、適切に冷却が行われているか確認します。 |
収納・保管の管理 | – 工具や部品の収納場所を整理し、使用前に状態を確認します。 – 工具の保管方法を見直し、錆や劣化を防ぐための対策を講じます。 |
3. 定期点検のスケジュール
点検項目 | 点検頻度 |
---|---|
機械本体の点検 | 月に1回または500時間ごと |
電気系統の点検 | 3ヶ月ごとまたは使用開始後2000時間ごと |
精度の確認 | 3ヶ月に1回または大規模な作業後 |
冷却システムの点検 | 1ヶ月に1回または機械の使用後1週間ごと |
工具・部品の管理 | 使用ごとまたは週に1回 |
詳細情報
- 予防策の重要性: 機械や工具のトラブルを未然に防ぐためには、定期的なメンテナンスと予防策が不可欠です。適切な工具の管理や清掃、冷却システムの点検を行うことで、機械の寿命を延ばし、加工精度を維持することができます。
- 定期的な点検の実施: 定期的な点検を実施することで、機械本体や電気系統の不具合を早期に発見し、修理や調整を行うことができます。特に、冷却システムや精度の確認を怠ると、加工不良や過熱の原因となるため、注意が必要です。
- 定期点検のスケジュール: 定期点検は、使用頻度や機械の使用状況に応じて行います。特に高頻度で使用される機械や精密な加工を行う場合には、細かな点検が求められます。
NCフライス盤の操作と設定
基本的な操作手順
操作手順 | 詳細情報 |
---|---|
1. 電源のオン | – 機械の電源を入れ、操作パネルの表示が正常であることを確認します。 – 非常停止ボタンが押されていないことをチェックします。 |
2. ツールの取り付け | – 適切な工具を選定し、工具ホルダーに取り付けます。 – 工具の取り付けがしっかりしていることを確認し、工具交換時の注意点を守ります。 |
3. 材料のセットアップ | – 材料をテーブルにセットし、クランプで固定します。 – 材料の位置と高さが正確であることを確認します。 |
4. ワーク座標の設定 | – ワークオフセットを設定します。 – X、Y、Z軸の基準点を確認し、正確に入力します。 |
5. プログラムのロード | – NCプログラムを読み込み、正しいプログラム番号が表示されているか確認します。 – プログラムの内容と順序を確認します。 |
6. 適切な切削条件の設定 | – 回転数、送り速度、切込み量を材料と工具に適した条件に設定します。 – 切削条件をプログラム内で設定し、必要に応じて手動で微調整します。 |
7. 動作テスト | – 空回転で動作確認を行い、工具と材料の位置を再確認します。 – 試運転を行い、異常音や動作不良がないかチェックします。 |
8. 本作業の開始 | – 作業を開始する前に、最終確認を行い、問題がないことを確認します。 – 本作業に移行し、監視しながら加工を進めます。 |
9. 完了後の確認 | – 加工が終了したら、機械の停止と工具の取り外しを行います。 – 加工結果を確認し、精度や仕上がりをチェックします。 |
操作のポイント
操作のポイント | 詳細情報 |
---|---|
正確な設定 | – 座標設定、工具設定、材料の位置が正確であることが重要です。 – 小さなズレでも加工に大きな影響を与えるため、細心の注意を払います。 |
安全確認 | – 作業前に必ず安全確認を行い、非常停止装置の確認や周囲の障害物を取り除きます。 – 防護具(眼鏡、手袋など)の着用を忘れずに行います。 |
切削条件の最適化 | – 切削条件は材料や工具に最適な設定を選びます。 – 高速回転や過度の切り込みは工具や機械に負荷をかけるため注意が必要です。 |
プログラムの確認 | – プログラムに誤りがないか、加工内容が正しいか確認してから動作を開始します。 – 事前にシミュレーションを行い、ミスを防ぎます。 |
機械の監視 | – 加工中は常に機械の動作を監視し、異常が発生した場合は即座に停止します。 – 異常音や振動、温度上昇などの兆候を早期に察知し、問題を未然に防ぎます。 |
詳細情報
- 基本的な操作手順: 操作手順は、機械が安全かつ精確に動作するために重要です。セットアップ作業から本作業開始までの流れを順を追って確認し、各工程でのチェックが求められます。特に、座標設定や工具の取り付け、材料の固定がしっかりしていないと、加工不良や事故の原因となります。
- 操作のポイント: 各操作は細心の注意を払いながら行うことが重要です。特に、切削条件の設定やプログラムのチェックは作業の精度に直結するため、十分に確認する必要があります。また、安全面にも配慮し、作業環境を整えてから作業に入ることが大切です。
プログラムの入力と編集
操作手順 | 詳細情報 |
---|---|
1. プログラムの準備 | – 作業に必要な加工内容をプログラムに記述します。 – CAD/CAMシステムを使用してプログラムを作成することもできます。 |
2. プログラムの入力 | – NCフライス盤の操作パネルにプログラムを入力します。 – プログラム番号や内容が正確であることを確認します。 |
3. プログラムの確認 | – 入力したプログラムを画面上で確認し、誤りがないかチェックします。 – エラーコードが表示された場合は、修正を行います。 |
4. プログラムの編集 | – 既存のプログラムを修正する場合、編集モードに切り替えます。 – 修正箇所を正確に指定し、必要なコードを追加・変更します。 |
5. プログラムの保存 | – 完成したプログラムを保存します。 – 保存したプログラムが適切なディレクトリに格納されているか確認します。 |
6. プログラムの実行 | – プログラムを実行して、設定した動作が正確に行われるか確認します。 – 最初は低速で実行して、動作を慎重に確認します。 |
7. プログラムの修正 | – 実行後に問題があれば、プログラムを修正し再実行します。 – 加工中に異常が発生した場合は即座にプログラムを停止し、修正します。 |
プログラムの入力時のポイント
ポイント | 詳細情報 |
---|---|
正確な入力 | – プログラムコードや座標設定が正確であることを確認します。 – 誤入力があると、加工ミスや機械の損傷につながります。 |
コードの整合性確認 | – コードの順番や文法が正しいか確認し、機械が理解できる形式であるかをチェックします。 – 事前にシミュレーションを行い、問題点を発見します。 |
必要なカスタム設定 | – 加工条件に応じて、特殊なコマンドや設定を追加することがあります。 – 例えば、工具交換のタイミングや停止位置をプログラムで指定する場合があります。 |
反復試験と修正 | – プログラムを実行する際には、最初に試験運転を行い、意図通りの動作を確認します。 – 問題があればプログラムを修正し、再度テストを行います。 |
詳細情報
- プログラムの入力: プログラムの入力は、NCフライス盤を操作する上で最も重要な工程のひとつです。正確な座標や動作、工具交換のタイミングなどを正しく記述しないと、加工ミスや機械の不具合を引き起こす原因になります。作成したプログラムは必ずシミュレーションで確認し、問題がないかチェックしてから実行することが求められます。
- プログラムの編集: プログラムの編集は、新たに作成したプログラムに変更を加える場合や、既存のプログラムに修正を施す場合に行います。プログラムを編集する際には、変更した内容が加工にどのように影響を与えるかを考慮し、慎重に行います。また、変更後は再度テスト運転を行い、問題がないか確認します。
- プログラムの実行: プログラム実行後、加工の進行状況を監視し、異常があればすぐに停止し修正を行います。最初に実行する際には低速での運転をお勧めします。これにより、異常の早期発見が可能となり、安全かつ精確な加工が行えます。
安全な作業環境の確保
1. 作業環境の整備
項目 | 詳細情報 |
---|---|
作業場の清掃 | – 機械周辺を常に清潔に保つことで、工具の取り扱いミスを防ぎます。 – 騒音や粉塵が発生する場合は、適切な掃除を行い、安全な作業環境を作ります。 |
作業スペースの確保 | – 作業エリアが狭すぎると、操作ミスや事故を引き起こす可能性が高くなります。 – 作業スペースを広く保ち、周囲の障害物を排除します。 |
照明の確保 | – 作業中の視認性を確保するために、十分な照明を整備します。 – 明るく、均等に照らされた環境が必要です。 |
通気性の確保 | – 切削作業による発生ガスや粉塵を排出できるよう、換気設備を整えます。 – 換気扇や空気清浄機を使って、作業場の空気環境を改善します。 |
2. 安全設備の使用
項目 | 詳細情報 |
---|---|
防護具の着用 | – 作業中は安全靴、保護メガネ、耳栓、手袋などの防護具を着用します。 – 防護具の着用は、事故や怪我を未然に防ぐために必要です。 |
防護カバーの設置 | – 機械には防護カバーを設置し、誤って手や身体が接触しないようにします。 – 自動運転中でも人身事故を防ぐためのカバーが重要です。 |
火災安全対策 | – 火災が発生した場合に備えて、消火器や火災報知器を設置します。 – 切削作業中に火花や高温物質が発生することを考慮し、安全対策を講じます。 |
3. 作業者の教育と訓練
項目 | 詳細情報 |
---|---|
定期的な安全教育 | – 作業者に対して定期的に安全教育を実施し、作業中の注意点や緊急時の対応方法を確認します。 – 新しい機械を導入する際や、作業手順が変更される場合には特に重要です。 |
作業手順の確認 | – 作業者が安全手順を守るため、明確な作業指示書を提供し、作業前に確認します。 – 作業手順に従わない場合のリスクや危険性についても教育します。 |
緊急時対応訓練 | – 万が一の事故発生時に迅速に対応できるよう、緊急時の避難経路や連絡方法について訓練します。 – 応急処置の方法を含めた安全管理の重要性を理解させます。 |
4. 機械設備の点検と保守
項目 | 詳細情報 |
---|---|
定期的な点検 | – 機械の定期的な点検を行い、異常があれば速やかに修理を行います。 – 点検記録を保存し、故障や不具合の履歴を追跡できるようにします。 |
適切なメンテナンス | – 機械が正常に動作するために必要なメンテナンスを定期的に行います。 – 切削油の交換や、工具の摩耗チェックも重要です。 |
操作前チェック | – 作業前には機械の動作確認を行い、安全装置が正常に機能するかを確認します。 – 操作ミスを防ぐため、機械が安全に動作する状態かを点検します。 |
詳細情報
- 作業環境の整備: 作業環境の清掃と整理は、安全で効率的な作業を行うために不可欠です。床面に工具や部品が散乱していないか、作業スペースに十分な余裕があるか、照明が適切かなど、作業者が安全に動ける環境を整えることが大切です。
- 安全設備の使用: 防護具や機械の防護カバーは、作業中に予期しない事故が発生するリスクを減らすために必須です。また、火災や異常時に備えて、消火器や火災報知器の設置も重要な安全対策です。
- 作業者の教育と訓練: 作業者が作業中に安全を確保するためには、教育と訓練が欠かせません。定期的な安全教育や作業手順の確認、緊急時対応の訓練を行い、作業者が危険を避けるために必要な知識と技術を身につけることが重要です。
- 機械設備の点検と保守: 定期的な機械点検と保守作業により、機械の故障やトラブルを未然に防ぎます。定期点検を怠ると、機械の不具合や事故の原因となることがあります。特に、操作前のチェックを徹底することで、機械の異常に早期に気づき、事故を防ぐことができます。
フライス盤の選び方と使い方
フライス盤選定のポイント
項目 | 詳細情報 |
---|---|
加工する材料の種類 | – 加工する材料に応じたフライス盤を選定します。 – 軽金属、鉄鋼、硬質合金など、素材の硬さや特性に適した機械を選ぶことが大切です。 |
加工サイズと精度 | – 加工する部品の大きさや精度要求に応じた機種を選びます。 – 小型部品の精密加工には高精度なミニフライス盤、大型部品には広い作業範囲を持つ機械を選ぶ必要があります。 |
加工の種類 | – 平面加工、溝加工、穴あけ、立体加工など、加工内容に応じて機能や装備を選びます。 – 複雑な加工が求められる場合、CNCフライス盤を選ぶと良いでしょう。 |
モーター出力 | – 加工する素材の硬さや、加工方法に応じたモーター出力を選びます。 – 高い出力が必要な場合は、モーターの強力な機種を選ぶことが求められます。 |
機械の剛性 | – 精密な加工を行うためには、フライス盤の剛性が重要です。 – 高剛性の機械を選ぶことで、振動や変形を防ぎ、精度の高い加工が可能となります。 |
操作性とメンテナンス | – 操作が簡便で、メンテナンスがしやすい機種を選びます。 – 長期間の使用を見越して、信頼性やアフターサービスが良好なメーカーを選ぶことが大切です。 |
詳細情報
- 加工する材料の種類: 加工する素材によってフライス盤の選定が大きく影響を受けます。例えば、鋼鉄や硬質合金のような硬い材料を扱う場合、強力なモーターや高剛性な機械が必要です。軽金属の加工では、あまり重い機械は必要ない場合もあります。
- 加工サイズと精度: 加工対象の部品のサイズや求められる精度に基づいて機械を選びます。精密な加工を行いたい場合は、精度の高い機種を選ぶべきです。また、加工する部品のサイズが大きければ、より広い作業範囲を持つ機械が必要になります。
- 加工の種類: 一部のフライス盤は、特定の加工方法に特化しているものがあります。例えば、CNCフライス盤は自動制御で複雑な加工を行うことができ、精密な繰り返し加工が可能です。反対に、手動で操作するフライス盤は、単純な平面加工や溝加工などに向いています。
- モーター出力: 加工する素材が硬くなるほど、モーター出力は大きな役割を果たします。モーターの強力さによって、効率的に切削ができ、機械の負担を減らすことができます。モーター出力が不足していると、機械の性能を十分に引き出せません。
- 機械の剛性: 剛性が高いフライス盤は、切削中の振動を抑え、安定した加工を可能にします。特に、高精度な加工を行う場合は、剛性が非常に重要となります。低剛性の機械では、振動や誤差が大きくなり、仕上がりに影響を与えます。
- 操作性とメンテナンス: フライス盤の操作が簡単で直感的であれば、作業効率が向上します。さらに、メンテナンスが容易な機種を選ぶことが、機械の長寿命化に繋がります。また、機械のメーカーが提供するサポートやアフターサービスも重要な選定基準です。
効率的なフライス加工のコツ
加工条件の最適化
項目 | 詳細情報 |
---|---|
切削速度 | – 切削速度は材料の硬さや工具の種類に基づいて適切に設定します。 – 高速切削を行うことで、加工時間を短縮できますが、過度な速度設定は工具の寿命を縮めることがあるため、適正な範囲を見極めます。 |
送り速度 | – 送り速度は、切削の効率と仕上がりに直結します。 – 速すぎると仕上がりが悪くなり、遅すぎると加工時間が長くなります。適切な速度を選ぶことが大切です。 |
切削深さ | – 切削深さを適切に調整することで、切削負荷を管理できます。 – 1回の切削で深く削りすぎると工具への負担が大きくなり、仕上がりが悪くなる場合があります。 |
切削液の使用 | – 切削液を適切に使用することで、工具の冷却と潤滑が改善され、切削効率が向上します。 – 適切な切削液を選ぶことで、工具の寿命も延ばせます。 |
適切な工具選定
項目 | 詳細情報 |
---|---|
工具の材質 | – 材料の種類に合わせた工具材質を選ぶことが重要です。 – 高硬度の材料には超硬工具、柔らかい材料にはHSS工具を使用することが一般的です。 |
工具の形状 | – 加工する形状に合わせた工具を選ぶことが必要です。 – 例えば、溝加工にはエンドミルを、穴あけにはドリルを使用するなど、最適な形状の工具を選びます。 |
工具の切れ味 | – 工具の切れ味が悪いと、加工面が荒れたり、切削効率が低下します。 – 工具の状態を定期的に確認し、必要に応じて交換することが重要です。 |
工作物のセットアップ
項目 | 詳細情報 |
---|---|
固定方法 | – 作業物をしっかり固定することで、加工精度が向上し、工具の寿命も延びます。 – クランプやチャックを使用して、作業物の位置ズレを防ぎます。 |
作業物の位置決め | – 加工前に作業物の位置決めを正確に行うことで、加工ミスを防ぎます。 – 定規やゲージを使って、正確な位置決めを行います。 |
工作物の平行度 | – 工作物の平行度が不正確だと、加工精度に悪影響を及ぼします。 – 作業物の平行度を調整することで、より高精度な加工が可能になります。 |
適切な加工順序
項目 | 詳細情報 |
---|---|
大きな部品から加工 | – 加工はまず大きな部品から始め、その後細部の加工を行うと効率的です。 – 大きな部分を先に加工することで、作業物の固定が安定し、精度が向上します。 |
仕上げ加工の順番 | – 仕上げ加工は最後に行い、粗削りの後に最終的な仕上げを行うことで、高精度な加工が可能になります。 – 仕上げを最初に行うと、後の粗削りによって仕上がりに影響が出ます。 |
詳細情報
- 加工条件の最適化:
- 切削速度、送り速度、切削深さなどを適切に調整することで、効率よく加工できます。これらの条件を最適化することで、加工時間を短縮し、工具の寿命を延ばすことが可能です。
- 適切な工具選定:
- 使用する材料や加工内容に応じた工具を選ぶことで、効率的な加工が可能になります。工具の材質や形状を材料に合わせて選定し、定期的なメンテナンスで切れ味を保つことが大切です。
- 工作物のセットアップ:
- 作業物を正確にセットアップすることで、加工精度が向上します。作業物の固定方法や位置決めを確認し、平行度を保つことで、誤差を減らすことができます。
- 適切な加工順序:
- 加工順序を適切に計画することで、作業効率が向上し、仕上がりの精度も高まります。粗削り後に仕上げを行うことで、最終的な加工精度が確保されます。
安全な操作と保守のアドバイス
操作時の安全対策
項目 | 詳細情報 |
---|---|
個人防護具の着用 | – 作業時には適切な個人防護具(PPE)を着用します。 – 作業に適した安全靴、手袋、保護メガネ、耳栓などを着用することで、作業中の事故や怪我を防ぎます。 |
作業エリアの清掃 | – 作業エリアは常に清潔で整理整頓されていることが重要です。 – 粉塵や油、金属片が床に散らばっていないか確認し、事故を防ぎます。 |
機械操作前の確認 | – 機械を操作する前には、各部品や工具が正常に取り付けられているかを確認します。 – 特に、回転部分や動作部分に異常がないかチェックが必要です。 |
緊急停止装置の確認 | – 機械には緊急停止装置が必ず備わっています。 – 作業前に緊急停止装置の位置を確認し、必要に応じてすぐに停止できるように準備しておきます。 |
作業中の注意点
項目 | 詳細情報 |
---|---|
監視と集中力 | – 操作中は常に機械の動作を監視し、異常音や振動がないかに注意します。 – 集中力を欠いた状態で作業しないように、休憩を適宜取ることも大切です。 |
動作確認の実施 | – 操作前に手動で動作を確認し、異常がないことを確認してから運転を開始します。 – 予期しない動きや不具合を防ぐために、細心の注意を払いましょう。 |
周囲の人とのコミュニケーション | – 作業中は周囲の人とのコミュニケーションをしっかりと行い、作業環境を共有します。 – 他の作業者との衝突を避けるため、確認しながら作業を進めます。 |
メンテナンスと保守
項目 | 詳細情報 |
---|---|
定期点検の実施 | – 機械や工具は定期的に点検を行い、消耗や異常を早期に発見して対応します。 – 点検リストを作成し、部品や機械の状態を確認することで、故障を未然に防ぎます。 |
清掃と潤滑 | – 機械や工具は定期的に清掃し、潤滑油を適切に補充します。 – 清掃と潤滑により、機械の寿命を延ばし、効率よく動作させることができます。 |
設備の修理 | – 異常を感じた場合、すぐに作業を中止し、修理を行います。 – 自分で修理ができない場合は、専門の技術者に依頼し、適切な修理を受けます。 |
部品の交換 | – 消耗品や劣化した部品は、定期的に交換することが必要です。 – 交換部品は必ず指定された部品を使用し、互換性のない部品を使わないようにします。 |
詳細情報
- 操作時の安全対策:
- 作業前には作業環境を整備し、個人防護具を着用することで、作業中の事故やけがを防ぎます。機械の異常を事前に確認し、緊急停止装置の位置を把握しておくことも安全作業において重要です。
- 作業中の注意点:
- 操作中は常に集中し、異常に気づいた場合は即座に作業を中止します。また、周囲の作業者とのコミュニケーションを欠かさず、安全に作業を進めることが大切です。
- メンテナンスと保守:
- 定期的な点検と清掃、潤滑を行い、機械の稼働状態を良好に保ちます。消耗品や部品は早期に交換し、故障のリスクを減らすことが効率的な運用に繋がります。