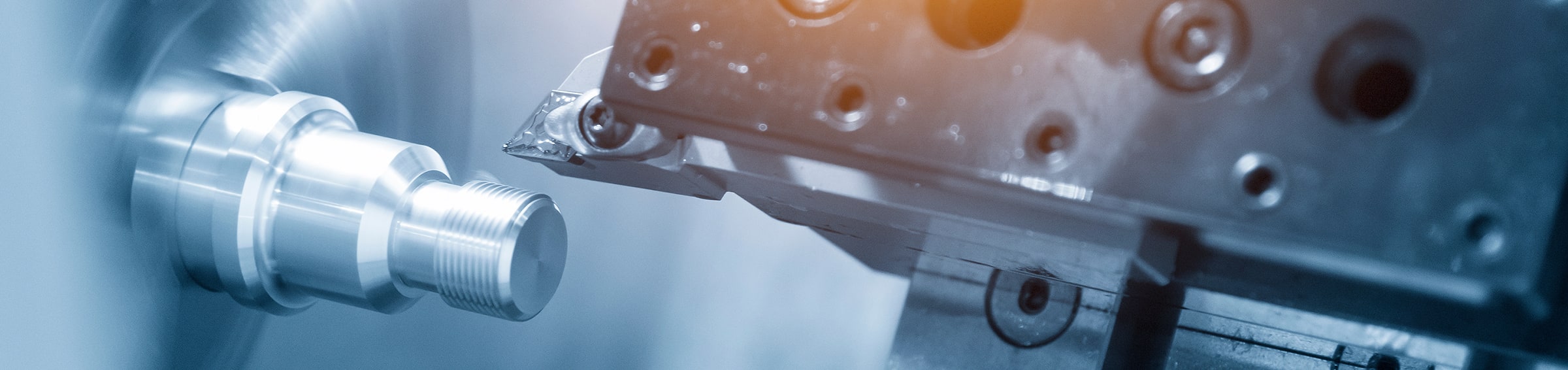
コラム column
C2600材の加工で成果を上げる!切削条件と注意すべき点
真鍮C2600の基礎知識
真鍮C2600は、銅を主体とした合金で、特にその高い加工性と良好な耐食性により、さまざまな産業で使用されています。以下にC2600材の基本的な情報と特性について解説します。C2600材とは
- 組成 C2600は、銅を基に、約70%の銅(Cu)を含み、残りの部分は主に亜鉛(Zn)で構成されています。この割合により、C2600は優れた加工性と優れた耐食性を持つ合金です。
- 用途 C2600は、主に電子機器の部品、建築金物、装飾用部品、機械部品などに使用されます。その美しい外観や高い耐食性が求められる製品に最適です。
- 加工性 高い加工性を持つため、切削や圧延、鍛造などの加工が比較的容易です。また、亜鉛の含有量が高いことから、溶接やハンダ付けにも適しています。
C2600の特性と切削性
- 耐食性 C2600は亜鉛が主成分の一部を占めており、海水や湿気に強いため、耐腐食性が高く、屋外や湿度の高い環境での使用にも適しています。
- 強度 この材質は適度な強度を有しており、一般的に機械的強度を求められる部品にも使用されますが、鋼材に比べると強度はやや劣ります。しかし、機械的な要求がさほど高くない部品では十分に機能します。
- 切削性 C2600は優れた切削性を持つため、旋盤やフライス盤などの機械を使用して簡単に加工できます。特に、細かい加工や複雑な形状の切削も比較的簡単に行える点が特徴です。そのため、高精度の部品を製造する際にも適しています。
- 成形性 この材質は引張強さと延性を兼ね備えており、冷間加工や熱間加工において優れた成形性を発揮します。また、圧延や鍛造によって薄板や細線に加工することができます。
- 熱処理 C2600は、熱処理により強度を高めることが可能ですが、他の材料に比べて熱処理の効果は限定的です。そのため、熱処理を行う際は、材料の特性に応じた温度管理が重要です。
真鍮C2600の切削加工
真鍮C2600は、その優れた加工性により、切削加工に非常に適した材料ですが、切削加工時にいくつかの注意点があります。ここでは、C2600の切削加工における基本的な考え方と注意点、さらに適切な切削工具の選び方について解説します。切削加工の基本
- 切削性の良さ 真鍮C2600は、優れた切削性を持っており、旋盤、フライス盤、ボール盤などでの加工が容易です。特に、加工時にチップが発生しやすく、良好な仕上がりが得られるため、精密加工にも向いています。
- 切削速度の設定 C2600の切削加工においては、適切な切削速度を設定することが重要です。過剰な切削速度は工具の摩耗を早める原因となり、品質にも影響を与えます。一方で、遅すぎる切削速度は加工効率を低下させます。一般的には中〜高切削速度を選択します。
- 切削油の使用 切削油を使用することで、切削面の品質が向上し、工具寿命を延ばすことができます。特に真鍮のような金属は、摩擦が発生しやすいため、切削油を使用することで加熱を防ぎ、スムーズな加工が可能になります。
C2600の切削加工での注意点
- 切削中の熱管理 C2600の切削加工では、金属の摩擦により発生する熱が問題になる場合があります。過度な加熱が発生すると、材料の変形や工具の摩耗を早める原因となるため、冷却を適切に行う必要があります。
- 切りくずの処理 C2600は切りくずが比較的大きくなりやすいため、適切な切りくず処理が重要です。切りくずが加工面に付着すると、仕上がりに影響を与えたり、作業効率が低下したりする可能性があります。切りくずを効率よく排出するために、適切な切削工具と冷却を使用することが推奨されます。
- 工具の選定と耐久性 C2600の切削には、耐摩耗性に優れた工具が必要です。工具の選定が不適切であると、工具の摩耗が早く、加工精度にも悪影響を及ぼします。工具寿命を最大化するためには、適切な工具の使用と管理が必要です。
真鍮加工に適した切削工具の選び方
- 高速度鋼(HSS)工具 高速度鋼(HSS)は、C2600の切削に最適な選択肢の一つです。HSSは耐摩耗性が高く、適度な靭性を持つため、細かい加工や複雑な形状の加工にも適しています。
- 超硬(カルバイド)工具 超硬工具は、高硬度のため長寿命を提供し、高速切削にも耐えることができます。C2600の切削で優れた性能を発揮するため、精密加工や高精度が求められる場合には最適です。ただし、加工時の振動や衝撃に弱いため、注意が必要です。
- チップ形状の選定 真鍮C2600の切削では、チップの形状も重要です。一般的に、平坦な表面仕上げが必要な場合は、片刃工具を使用することが推奨されます。曲線や複雑な形状を切削する際には、適切な形状の工具を選択することが精度を高めます。
- 工具コーティング C2600の切削では、工具の表面をコーティングすることが有効です。コーティングを施した工具は、摩耗や腐食に強く、加工中の摩擦を軽減するため、より高効率で高精度な加工が可能となります。
真鍮C2600のフライス加工テクニック
真鍮C2600は、その優れた加工性により、フライス加工においても高い効果を発揮します。しかし、効率的に加工を行うためには、いくつかのポイントとテクニックを押さえる必要があります。ここでは、フライス加工の基本からC2600材を使ったフライス加工のポイント、さらに工具寿命を延ばすコツについて解説します。フライス加工の基礎
- フライス加工とは フライス加工は、回転する工具(フライス盤)を用いて、金属の切削を行う加工方法です。金属の表面に対して様々な形状や凹凸を作ることができ、特に平面や溝、歯車、スロットなどの加工に適しています。
- 切削速度と送り速度 フライス加工における切削速度や送り速度の設定は非常に重要です。C2600材では、適切な切削速度を設定することで、効率的に加工が進みます。特に、送り速度を適度に調整することで、よりスムーズで高精度な加工が可能になります。
- 冷却と切削油の使用 フライス加工では、冷却剤や切削油を使用することで、摩擦を減少させ、加工面の品質を向上させます。これにより、工具の摩耗を減少させるだけでなく、加工精度も保たれます。
C2600材を使ったフライス加工のポイント
- 適切な切削条件の設定 C2600は比較的切削性が良いですが、適切な切削条件を設定することで、効率的な加工が可能となります。切削速度は300~400m/minを目安に設定し、工具の摩耗を抑えるために、送り速度や切込み深さを調整します。
- 工具の選定 フライス加工では、工具の材質や形状が非常に重要です。C2600のフライス加工には、耐摩耗性に優れた超硬工具や高速度鋼(HSS)工具が効果的です。特に、複雑な形状を加工する場合は、チップの形状や種類を選定することが精度向上に繋がります。
- 切りくずの処理 真鍮C2600は切りくずが大きくなることが多いため、効率的な排出が必要です。切りくずが加工面に絡みつくと、仕上げに悪影響を与えるため、定期的に切りくずを除去するようにしましょう。
- 仕上げの精度向上 フライス加工では、仕上げの精度が重要です。C2600のような金属は加工中に表面が滑らかになりやすいため、最後の仕上げ工程での微細な調整を行うことで、高精度な仕上がりが得られます。
フライス加工での工具寿命を延ばすコツ
- 切削油の選定と使用方法 適切な切削油を選定することにより、工具の冷却と潤滑が行われ、摩耗を防ぐことができます。特にフライス加工では、加工温度が上がりやすいため、冷却性能の高い切削油を選ぶことが重要です。
- 切削条件の最適化 切削条件(切削速度、送り速度、切込み深さ)を最適に設定することは、工具寿命を延ばすために重要です。過剰な切削負荷がかからないように調整し、工具の摩耗を抑えるようにします。
- 適切な切りくず処理 切りくずが溜まると、工具の摩耗を早めたり、加工精度を低下させる原因になります。定期的に切りくずを排出し、工具に負担をかけないように注意します。
- 工具の点検と交換 定期的に工具の状態を点検し、摩耗が進んでいる場合は早めに交換することが工具寿命を延ばすポイントです。また、異常な摩耗が見られた場合は、切削条件を見直すことが効果的です。
C2600材の切削条件の最適化
C2600(真鍮)は、その優れた加工性により、さまざまな切削加工に適していますが、最適な切削条件を設定することで、より効率的で高精度な加工を実現できます。ここでは、切削条件の基本要素からC2600材に最適な切削条件の設定方法までを解説します。切削条件の基本要素
- 切削速度(Vc) 切削速度は、工具の切削面が素材に接触する速さを示します。切削速度が適切でないと、工具の摩耗が早くなるだけでなく、加工面の仕上がりにも影響が出ることがあります。最適な切削速度は材質や加工目的に応じて選定します。
- 送り速度(Vf) 送り速度は、工具が加工物をどれだけの速さで移動するかを示します。適切な送り速度を設定することにより、切削力を適切に分散し、工具寿命の延長や加工精度の向上が可能となります。
- 切込み深さ(ap) 切込み深さは、工具が材料に食い込む深さを示します。深すぎる切込みは加工面に不均一な力を加えるため、工具の摩耗を早めます。適切な深さで切削を行うことが重要です。
- 回転数(n) 回転数は、工具が1分間に回転する回数を示します。回転数が高すぎると熱がこもりやすく、低すぎると切削効率が落ちます。適切な回転数を選定することが、効率的な切削を行うための鍵です。
銅や真鍮の種類別切削条件
- 銅(C1100) 銅は非常に柔らかい金属であり、切削性が良好です。一般的には、切削速度は約150~200 m/min、送り速度は0.1~0.2 mm/rev程度が推奨されます。銅の加工では切削熱を適切に処理することが重要で、冷却剤の使用が効果的です。
- 真鍮(C2600) 真鍮は、銅に亜鉛を加えた合金で、非常に優れた加工性を持っています。C2600は比較的硬さがあり、切削条件の設定には注意が必要です。切削速度は約300~400 m/minが理想的で、送り速度は0.1~0.3 mm/rev、切込み深さは0.2~0.5 mm程度が一般的です。
- 真鍮(C2800) C2800は亜鉛の割合が増えた真鍮で、C2600よりも少し硬度が高いです。C2800の加工には切削速度が200~300 m/min、送り速度は0.1~0.25 mm/rev、切込み深さは0.2~0.4 mm程度が推奨されます。
C2600材に最適な切削条件の設定
C2600は、適切な切削条件を設定することで、その優れた加工性を最大限に引き出すことができます。以下はC2600材に最適な切削条件を設定するためのポイントです。- 切削速度 C2600の適切な切削速度は、300~400 m/minです。これは、加工中に過度な熱の発生を避け、効率的に切削できる範囲です。高すぎる切削速度は工具の摩耗を加速させるため、注意が必要です。
- 送り速度 送り速度は、0.1~0.3 mm/revの範囲が適切です。切削速度と送り速度は互いに関連しているため、バランスよく設定することが求められます。送り速度が速すぎると切りくずの排出が難しくなり、加工品質が低下する可能性があります。
- 切込み深さ 切込み深さは、0.2~0.5 mmが一般的な範囲です。深すぎる切込みは、工具に過剰な負荷をかけることとなり、摩耗や欠損の原因となります。適切な深さを選定し、少しずつ切削を進めることが重要です。
- 冷却と切削油の使用 C2600材は切削熱が発生しやすいため、冷却と潤滑を適切に行うことが必要です。切削油を使用することで、工具の摩耗を抑えるだけでなく、加工面の仕上がりも良好になります。
- 工具の選定 C2600のような真鍮は比較的切削性が良いですが、適切な工具の選定も重要です。超硬工具や高速度鋼(HSS)工具が一般的に使用されますが、加工条件や求められる仕上げ品質に応じて、工具の材質や形状を選びましょう。
最適な切削条件を設定することで、C2600材の加工効率を最大化し、工具寿命を延ばしながら高精度な仕上がりを実現することができます。
切削工具の選択と管理
切削工具は、加工精度や効率を決定する重要な要素です。適切な切削工具を選び、管理することで、加工品質を向上させ、コストを削減できます。ここでは、長寿命な切削工具の選び方、切削工具のメンテナンスと交換時期、そして切削工具の性能を最大限に引き出すためのポイントを解説します。長寿命な切削工具の選び方
- 材質の選定 切削工具の材質は、加工する素材や使用する環境に応じて選ぶ必要があります。例えば、硬い材料を加工する場合には超硬工具(Carbide)やセラミック工具が適しています。一方、一般的な金属を加工する場合には高速度鋼(HSS)工具がコストパフォーマンスに優れています。
- コーティングの選定 切削工具には、耐摩耗性や耐熱性を高めるためのコーティングが施されています。コーティングの種類によって、工具の寿命や性能が大きく変わります。例えば、TiN(窒化チタン)コーティングは耐摩耗性を向上させ、TiAlN(窒化アルミニウム)は高温に強いため、高速切削に適しています。
- 工具の形状 切削工具の形状(エンドミル、ドリル、タップなど)は、加工方法に応じて選ぶべきです。例えば、鋭い切れ味が求められる場合や、硬い素材を削る場合には、特定の形状が有効です。また、工具の刃数や先端角度も重要な選定基準となります。
- 加工環境に合った工具選定 加工する材料の特性(硬さ、粘性など)や加工条件(切削速度、加工深さ)に応じて、適切な工具を選定することが大切です。例えば、硬い鋼を加工する場合は、耐摩耗性に優れた工具が必要です。
切削工具のメンテナンスと交換時期
- 定期的な点検とメンテナンス 切削工具は使用するごとに摩耗し、性能が低下します。定期的に点検を行い、摩耗状態をチェックしましょう。特に、工具の先端や切削面に摩耗が見られる場合は、性能が低下している可能性があります。
- 工具の刃先の研磨 切削工具の刃先は、定期的に研磨することで寿命を延ばすことができます。刃先が鈍ると、切削力が不足し、加工精度が低下します。研磨を行うことで、工具の切れ味を維持し、より効率的な加工が可能となります。
- 交換時期の判断 切削工具の交換時期を見極めることは重要です。交換時期を遅らせると、加工品質が低下し、工具の破損リスクが高まります。一般的に、工具の寿命は摩耗の進行具合や加工条件によって異なりますが、摩耗や傷が深刻になった場合、または加工精度が確保できなくなった時点で交換するべきです。
- 管理ツールの利用 現代では、工具管理ソフトウェアや工具寿命予測ツールを使用して、工具の状態を監視することができます。これにより、最適なタイミングでの交換が可能となり、無駄な交換や無駄な加工を防ぐことができます。
切削工具の性能を最大限に引き出すために
- 適切な切削条件の設定 切削工具の性能を最大限に引き出すためには、加工条件(切削速度、送り速度、切込み深さなど)を適切に設定することが重要です。過剰な切削速度や送り速度を設定すると、工具が過度に摩耗し、逆に効率が低下します。適切な条件で加工することで、工具の寿命を延ばし、最良の性能を発揮させることができます。
- 冷却と潤滑の管理 冷却と潤滑は、切削工具の性能を維持するために非常に重要です。適切な冷却剤や潤滑剤を使用することで、切削温度を抑え、工具の摩耗を抑制します。冷却や潤滑の方法を正しく選択し、効果的に活用することが、長寿命な切削工具を維持するための鍵となります。
- 適切な機械設定の利用 切削工具の性能を引き出すためには、機械設定の調整も重要です。機械の振動や不安定な動作が工具に負担をかけることがあります。機械の精度を確認し、安定した動作を維持することが、工具の性能を最大限に活用するための条件です。
切削工具を選択し、適切に管理することで、加工効率を高め、コストを削減することができます。また、適切なメンテナンスとタイムリーな交換により、工具の寿命を最大化し、安定した加工精度を維持することが可能です。
切削加工のトラブルシューティング
切削加工時にはさまざまな問題が発生することがありますが、これらのトラブルを早期に発見し、適切に対処することで加工の精度と効率を維持することができます。ここでは、一般的な切削加工時の問題とその対処法、真鍮C2600加工時の特有の問題点、さらにトラブルを予防するための解決策を紹介します。切削加工時の一般的な問題と対処法
- 切削不良(バリや溶け込み)
- 原因: 切削速度が速すぎる、または工具が鈍っていることが原因です。切削熱が発生しすぎて、材料が溶けたり、切削面にバリができたりすることがあります。
- 対処法: 切削速度や送り速度を適切に調整し、工具を定期的に交換するか、研磨します。また、冷却液を使用して切削熱を管理します。
- 表面仕上がりの不良
- 原因: 切削工具が摩耗している、または設定された加工条件が不適切な場合に、表面に傷や粗さが残ることがあります。
- 対処法: 使用する切削工具の材質やコーティングを見直し、精度の高い工具を使用します。加工条件(切削速度、送り速度、切り込み深さ)を再調整し、仕上げ工程での品質を向上させます。
- 振動(チャタリング)
- 原因: 機械の剛性不足や不適切な工具の取り付け、または不安定な切削条件が振動を引き起こす原因となります。
- 対処法: 切削条件を見直し、適切な送り速度と切削深さを設定します。また、工具の取り付けを確認し、機械の剛性を向上させることも有効です。
- 工具の摩耗
- 原因: 高速切削や硬い材料の加工によって工具が早期に摩耗することがあります。
- 対処法: 切削速度を適切に調整し、工具の選定を見直します。高品質なコーティング工具を使用したり、冷却や潤滑の方法を最適化することが効果的です。
真鍮C2600加工時の特有の問題点
- 切削熱の蓄積 真鍮C2600は良好な機械加工性を持ちますが、切削中に発生する熱が蓄積しやすいため、加工時の熱管理が重要です。過度な熱は工具の摩耗を加速させ、加工面の仕上がりに影響を与えることがあります。
- 対処法: 適切な切削速度と送り速度を設定し、冷却液を効果的に使用します。また、細かい切削深さで少しずつ加工する方法も有効です。
- 引きずりやすい切削面 真鍮は比較的柔らかい材料であるため、加工中に引きずりやすく、仕上がり面にムラが出やすいことがあります。
- 対処法: 切削条件を見直し、工具の刃先角度や形状を調整します。また、切削液を適切に使用して、切削面の潤滑を良好に保つことが大切です。
- 切削工具の摩耗 真鍮は比較的加工が容易ですが、軟らかいため、過度に深く切り込むと工具が摩耗しやすくなります。
- 対処法: 切削深さや送り速度を適切に設定し、切削工具の材質やコーティングを選定します。過度な負荷を避けるために切削条件を調整します。
切削加工トラブルの予防と解決策
- 適切な切削条件の設定 加工の初めに適切な切削条件を設定することで、トラブルを予防できます。材料に適した切削速度、送り速度、切り込み深さを選定し、加工精度を維持します。加えて、加工開始時に小さな切り込みから始めて、徐々に条件を最適化することが重要です。
- 冷却と潤滑の適切な管理 切削熱の蓄積や摩擦による問題を予防するために、冷却液や潤滑剤を適切に使用します。これにより工具の摩耗を減少させ、加工面の仕上がりを良好に保つことができます。
- 工具の定期的な点検と交換 定期的に工具の状態をチェックし、摩耗や損傷を早期に発見することがトラブルの予防につながります。工具が摩耗したまま使用し続けると、加工精度が低下し、余計なトラブルを引き起こします。
- 機械の定期的なメンテナンス 機械の精度や安定性を保つために、定期的なメンテナンスが必要です。機械の剛性が不足していたり、振動が生じると、加工中に問題が発生することがあります。定期的に機械を点検し、必要な修理や調整を行うことが、トラブルの予防につながります。
これらの対策を実行することで、切削加工中の問題を最小限に抑え、精度の高い加工を実現することができます。適切な条件設定、工具選定、冷却や潤滑の管理、そして定期的なメンテナンスを行うことで、トラブルを予防し、効率的な生産を維持することが可能です。
まとめ
C2600材の加工で成果を上げるためには、適切な切削条件と注意すべき点があります。C2600は切削性に優れた材料であり、適切な工具や切削速度、刃先形状などを選定することが重要です。加工時には適切な冷却や潤滑を行い、過度な摩擦や熱を防ぐことが肝要です。さらに、切削時の振動やひずみにも注意が必要です。これらの条件と注意点を把握することで、C2600材の加工において成果を上げることができます。C2680合金の選択: 機械的性質と化学成分の徹底比較
C2680合金の概要
C2680合金は、銅と亜鉛を主成分とする銅合金の一種で、優れた耐腐食性、加工性、電気伝導性を持つため、さまざまな産業で使用されています。この合金は、特に機械的特性が求められる用途や、熱処理による強度向上が必要な場面で重宝されています。C2680合金とは
C2680合金は、銅(Cu)と亜鉛(Zn)を主成分とした合金で、通常は銅の含有量が多いですが、亜鉛を一定量含むことで、機械的特性を改善し、腐食に対する耐性を強化します。加えて、鋳造性や延性にも優れており、加工や成形がしやすい特徴があります。 C2680合金は、材料の強度や硬度を高めるために、適切な熱処理を施すことが可能であり、その結果、さまざまな条件下で安定した性能を発揮します。これにより、製品の寿命を延ばし、信頼性の高い構造部品として利用されることが多いです。C2680合金の主な用途
C2680合金は、その特性を活かして、以下のような用途に広く利用されています:1. 電気機器
- コネクタや端子:C2680合金は電気伝導性が良好であるため、電子機器のコネクタや端子に使用されます。これにより、電流の流れがスムーズになり、電気機器の性能が向上します。
2. 機械部品
- 歯車やシャフト:機械的強度が要求される部品に使用されることが多いです。C2680合金は、摩耗に強く、耐久性に優れており、長期間の使用が可能です。
3. 自動車部品
- エンジン部品や冷却系統:C2680合金は、耐腐食性が高いため、車両の冷却系統やエンジン部品に適しています。特に温度変化が大きい環境でも安定して性能を発揮します。
4. 建設・産業用機器
- パイプやバルブ:耐腐食性と加工性に優れているため、建設や産業用機器のパイプやバルブにも使用されます。これにより、厳しい環境下での長期使用が可能になります。
5. 装飾用途
- ジュエリーや金属製品:C2680合金は、見た目の美しさと加工のしやすさから、装飾用途にも利用されます。金属製品やジュエリーに適した色合いと輝きを持っています。
C2680合金の特徴と利点
- 耐腐食性:湿気や化学物質に対する耐性が強いため、厳しい環境下でも使用可能。
- 優れた加工性:加工がしやすく、複雑な形状にも対応可能。
- 良好な電気伝導性:電子機器や電気部品に適しています。
- 高い機械的強度:強度が必要な機械部品に最適です。
C2680合金の化学成分
C2680合金は、主に銅と亜鉛を基にした銅合金で、その他の元素が少量含まれています。これらの化学成分は、合金の物理的特性、機械的特性、耐腐食性などに大きな影響を与えます。以下では、C2680合金の成分表と各成分の役割について説明します。C2680合金の成分表
成分 | 含有量(%) |
---|---|
銅 (Cu) | 60.0 – 63.0 |
亜鉛 (Zn) | 35.0 – 38.0 |
鉄 (Fe) | 最大 0.2 |
錫 (Sn) | 最大 0.1 |
銻 (Sb) | 最大 0.05 |
硫黄 (S) | 最大 0.03 |
その他 | 微量 |
各成分の役割と特性
銅 (Cu)
- 役割: C2680合金の主成分であり、強度、延性、導電性を提供します。銅はまた、合金の耐腐食性を高め、耐久性を向上させます。
- 特性: 銅は非常に優れた導電性を持つため、電気部品や電子機器でよく使用されます。また、耐食性が高く、酸化や腐食に強いという特性があります。
亜鉛 (Zn)
- 役割: 合金に強度を与え、銅よりも加工しやすくします。亜鉛はまた、合金をより硬くし、耐摩耗性を向上させます。
- 特性: 亜鉛を加えることで、C2680合金は耐摩耗性と強度が向上し、加工が容易になります。また、亜鉛は合金の低温での靭性を改善する役割も果たします。
鉄 (Fe)
- 役割: 少量の鉄が含まれることで、合金にさらなる強度と硬度を提供しますが、過剰な鉄は脆くなる可能性があるため、含有量は制限されています。
- 特性: 鉄は、合金の構造を補強し、機械的強度を増加させます。しかし、鉄の含有量が多すぎると、合金の延性が失われることがあります。
錫 (Sn)
- 役割: 錫は耐腐食性を向上させ、合金の安定性を高めるため、少量が添加されます。
- 特性: 錫は、合金に対して耐食性と抗酸化性を付与し、腐食環境での使用寿命を延ばします。
銻 (Sb)
- 役割: 銻は、亜鉛との相互作用により、合金の強度をさらに増加させる効果があります。
- 特性: 少量の銻は、合金に耐摩耗性を与え、強度を向上させる役割を果たします。
硫黄 (S)
- 役割: 硫黄は主に鋳造性を改善し、合金が流れやすくなるようにします。過剰な硫黄は合金の脆さを引き起こす可能性があるため、含有量は制限されています。
- 特性: 硫黄は合金の加工性を向上させるものの、過剰に含まれると機械的強度を低下させる恐れがあります。
化学成分が合金の性質に与える影響
C2680合金の化学成分は、合金の性質を大きく左右します。以下は、主要成分が合金の性質に与える影響の概要です:1. 強度と硬度
- 亜鉛の含有量が増えると、合金の強度と硬度が向上します。これにより、機械的負荷に対する耐性が増し、使用範囲が広がります。
2. 耐腐食性
- 銅の割合が高いことで、C2680合金は優れた耐腐食性を示します。また、少量の錫や銻が加えられることで、さらに耐食性が高まります。これにより、湿度や化学物質にさらされる環境でも使用が可能です。
3. 加工性と延性
- 亜鉛の影響により、C2680合金は加工しやすくなり、延性が向上します。これにより、複雑な形状の部品を製造する際にも優れた加工性を発揮します。
4. 導電性
- 銅が主成分であるため、C2680合金は高い電気伝導性を持ちます。これにより、電子機器や電気部品において広く利用されています。
5. 摩耗と機械的負荷への耐性
- 鉄や銻の少量添加により、C2680合金は摩耗に強く、機械的負荷に耐える能力が高くなります。この特性により、重機や自動車部品などの耐久性が求められる部品に使用されます。
C2680合金の機械的性質
C2680合金は、銅と亜鉛を基にした合金であり、その機械的性質は多くの工業用途において非常に重要です。特に強度、硬度、延性、靭性、疲労強度、耐久性などが重要な性能指標となります。これらの特性は、C2680合金を適切に使用するために理解しておくべき要素です。強度と硬度
C2680合金の強度と硬度は、主に亜鉛の含有量によって決まります。亜鉛を加えることで、合金の強度と硬度が向上し、耐摩耗性が増します。- 強度: C2680合金は、一般的に引張強度が400〜600 MPa程度であり、強度が高く、機械的な負荷に耐える能力を持っています。
- 硬度: 硬度は、ブリネル硬度(HB)で約100〜150程度で、標準的な銅合金と比較しても比較的高い硬度を示します。これにより、摩耗や摩擦に強い特性があります。
延性と靭性
C2680合金は、優れた延性と靭性を持つため、複雑な加工や成形が可能です。これにより、精密部品や耐久性が求められる部品の製造に向いています。- 延性: C2680合金は高い延性を有しており、引張り試験では引き延ばし可能な形状まで伸ばすことができます。この特性により、精密な成形や加工が可能です。
- 靭性: 靭性は、外力が加わった際に破壊せずに変形を続ける能力です。C2680合金は非常に高い靭性を持ち、衝撃や急激な温度変化に耐えることができます。
疲労強度と耐久性
C2680合金は、長期間の使用においても優れた耐久性を発揮します。また、疲労強度が高いため、繰り返し荷重に対しても耐えることができます。- 疲労強度: 疲労強度は、繰り返しの荷重に耐える能力を示します。C2680合金は高い疲労強度を持ち、繰り返し荷重がかかる環境でも、割れや亀裂の発生を防ぎます。
- 耐久性: 亜鉛と銅の組み合わせにより、C2680合金は高い耐久性を誇り、長期間使用しても性能が安定しています。腐食や摩耗に強いため、長寿命の部品に適しています。
機械的性質の試験方法
C2680合金の機械的性質を評価するために、いくつかの試験方法が使用されます。これらの試験方法により、合金の性能を定量的に測定することができます。1. 引張試験
引張試験は、合金の強度、延性、破断強度などを測定するために使用されます。試験片を引っ張っていき、破断するまでの荷重を測定することで、合金の引張強度や延性を確認できます。2. ブリネル硬度試験
ブリネル硬度試験は、合金の硬さを測定する方法で、鋼球を合金の表面に押し当てて、その圧痕の大きさを測定します。この試験で得られた硬度値は、合金の耐摩耗性や耐腐食性に関連しています。3. 疲労試験
疲労試験は、繰り返しの荷重に対する合金の耐性を測定するための試験です。この試験では、合金が繰り返し荷重を受けても破断しないか、ひび割れが発生しないかを評価します。4. 衝撃試験
衝撃試験では、合金の靭性を測定します。試験片に衝撃を加えて、その破壊に至るまでのエネルギーを測定することで、合金の靭性や脆さを評価します。C2680とC2801の違い
C2680合金とC2801合金は、どちらも銅合金ですが、それぞれ異なる化学成分、機械的性質、用途に特化しています。これらの合金は、さまざまな工業用途において使用されるため、比較して理解することが重要です。化学成分の比較
C2680合金とC2801合金は、基本的に銅を主体とする合金ですが、添加される元素の種類とその割合に違いがあります。成分 | C2680 合金 | C2801 合金 |
---|---|---|
銅 (Cu) | 約 90-96% | 約 90-96% |
亜鉛 (Zn) | 約 3-6% | 約 3-6% |
鉛 (Pb) | 約 1% | 約 1% |
その他 | 少量の鉄 (Fe)、アルミニウム (Al)、スズ (Sn) | 少量の鉄 (Fe)、スズ (Sn)、マンガン (Mn) |
- C2680合金は、亜鉛が主成分の一部であり、銅と亜鉛の合金で、主に耐摩耗性や加工性を高めるための成分が添加されています。
- C2801合金も同じく銅を基にした合金ですが、亜鉛に加え、スズやマンガンが成分として加えられ、より高い耐食性と機械的強度を提供します。
機械的性質の比較
C2680とC2801の機械的性質は、合金の成分に依存しており、特に強度、硬度、延性、疲労強度などに違いがあります。性質 | C2680 合金 | C2801 合金 |
---|---|---|
引張強度 | 400〜600 MPa | 450〜650 MPa |
硬度 | 100〜150 HB | 120〜160 HB |
延性 | 高い | 高い |
靭性 | 高い | 高い |
疲労強度 | 高い | より高い |
耐久性 | 高い | より高い |
- C2680合金は、非常に優れた延性と靭性を持ち、加工性に優れています。強度や硬度も十分高いですが、C2801と比較して若干低い強度を持つ場合があります。
- C2801合金は、C2680に比べて引張強度がやや高く、耐摩耗性と耐久性がさらに向上しています。特に耐食性が強化されており、過酷な環境下での使用に適しています。
用途と適合性の比較
C2680合金とC2801合金は、それぞれ異なる用途に適しています。主に製品の強度や耐久性が求められる場面で使用されます。用途 | C2680 合金 | C2801 合金 |
---|---|---|
電気・電子機器 | 使用されることはあるが、主に耐摩耗部品 | 電気端子やコネクタなど、耐食性が要求される部分に最適 |
自動車産業 | 部品や機械部品、コネクタ | 高負荷部品、耐食部品、エンジンパーツ |
配管・装置部品 | 配管やバルブ、機械部品 | 高温・高圧環境に対応する部品、耐食性が求められる部品 |
装飾用途 | 高い加工性を活かして装飾部品に使用 | 耐久性が求められる装飾部品、特に屋外用途 |
- C2680合金は、高い加工性と延性を活かし、機械部品や配管、バルブ部品などに多く使用されます。特に加工が必要な部品に最適です。
- C2801合金は、より高い耐久性と耐食性を提供するため、過酷な環境や高温・高圧が予想される場所に適しています。自動車や電気機器など、耐久性が要求される部品に広く使用されています。
真鍮C2680の材質と性質
真鍮C2680は、主に銅と亜鉛を基にした合金で、非常に優れた加工性、強度、耐久性を持っています。この合金は、特に金属加工において重要な役割を果たしており、さまざまな産業で利用されています。C2680は特に機械部品や電子機器など、耐久性や加工性が求められる用途に広く使われています。C2680の物理的特性
C2680合金は、物理的特性が非常に優れています。主な特性としては以下のような点が挙げられます。- 比重 (Density): 約 8.6 g/cm³ C2680は銅を基盤とした合金であるため、比較的重いですが、強度に対して非常に安定した物理的特性を持っています。
- 融点 (Melting Point): 約 900~940°C 銅ベースの合金であるため、比較的高い融点を持ち、過酷な環境にも耐えることができます。
- 引張強度 (Tensile Strength): 約 400~600 MPa 引張強度が高く、機械的な負荷をかけても変形しにくい特性を持っています。これにより、構造部品や耐摩耗部品として利用されています。
耐蝕性と耐熱性
C2680合金は、耐蝕性と耐熱性においても優れた特性を持っています。耐蝕性
- C2680合金は、亜鉛が一定割合含まれているため、耐蝕性が向上しており、湿気や化学的な攻撃を受けにくい特性があります。
- 海水や湿気の多い環境でも比較的腐食に強く、長期間使用可能な特性を持っています。特に、水中での使用においても高い耐蝕性が期待できます。
耐熱性
- C2680は耐熱性にも優れており、高温環境での使用にも適しています。
- 銅と亜鉛の合金であるため、熱膨張率が比較的小さく、温度変化に対して安定した性能を発揮します。
- 高温での長期的な使用にも強いため、エンジン部品や機械部品、さらには高温での金属加工に使われることがあります。
電気伝導性と熱伝導性
C2680合金は、銅をベースにしているため、優れた電気伝導性と熱伝導性を持っています。電気伝導性
- C2680合金は高い電気伝導性を持っており、電気機器や接点、配線部品としての利用に適しています。
- 銅が主成分であるため、高い導電率を有し、電気的な信号を迅速に伝えることができます。
熱伝導性
- C2680は熱伝導性にも優れており、熱を効率的に伝える能力を持っています。この特性は、放熱部品や熱交換器において重要です。
- そのため、加熱装置や冷却機器、電子機器の内部において熱を分散させるために使用されることが多いです。
C2680合金の加工性
C2680合金は、その優れた機械的特性と物理的特性により、さまざまな加工方法に適しています。この合金は、金属加工の現場で広く使用されており、適切な加工方法を選択することが重要です。ここでは、C2680合金の加工方法、加工時の注意点、および表面処理と仕上げについて説明します。加工方法と適性
C2680合金は、銅と亜鉛をベースにした合金であり、一般的な金属加工方法に広く適しています。主な加工方法としては以下のようなものがあります。- 切削加工 C2680は切削加工に適しており、フライス盤や旋盤を使用して精密な部品を作成することができます。加工がしやすく、工具の摩耗も比較的少ないため、精度の高い仕上がりを期待できます。
- 圧延加工 この合金は圧延加工にも適しています。圧延によって薄い板や帯を製造でき、特に薄板の製造において優れた加工性を発揮します。圧延時には高い塑性を持ち、形状の変更がしやすいため、成形性が向上します。
- 押出加工 C2680合金は押出加工にも適しており、長尺の部品や複雑な断面形状を製造することができます。押出成形は、特にアルミニウムの代替として使用されることが多いです。
- 鍛造加工 高温での鍛造加工も可能です。鍛造により、強度や靭性が向上するため、特に高負荷を受ける部品には有用です。鍛造時には熱間鍛造と冷間鍛造の両方に対応でき、適切な温度で行うことが求められます。
加工時の注意点
C2680合金の加工にはいくつかの注意点があります。これらを考慮することで、加工精度を高め、材料の特性を最大限に活用できます。- 熱膨張に注意 C2680合金は銅を含んでいるため、熱膨張率が高い特性を持っています。加工中に温度変化が大きい場合、部品の寸法が変化することがあるため、温度管理に十分な注意を払う必要があります。
- 工具の選定 銅合金は比較的加工しやすいですが、加工時に発生する摩擦によって工具が摩耗しやすいです。適切な工具素材を選び、切削速度や切削条件を最適化することで、工具の寿命を延ばすことができます。
- 切削油の使用 C2680合金を加工する際は、切削油や潤滑剤を使用して摩擦を減らし、切削温度を下げることが重要です。これにより、加工精度が向上し、工具の寿命も長くなります。
- 変形とひずみ 加工中に材料が変形することがあります。特に冷間加工時には注意が必要で、過度の力を加えるとひずみが生じ、部品の精度に影響を与えることがあります。
表面処理と仕上げ
C2680合金は、表面処理と仕上げが非常に重要です。表面処理を行うことで、耐食性や外観を改善し、部品の寿命を延ばすことができます。- メッキ処理 C2680合金はメッキ処理を施すことで、表面の耐食性を向上させることができます。特にニッケルメッキやクロムメッキが施されることが多く、これにより外観が向上し、腐食や摩耗に対する耐性が強化されます。
- 酸化処理 表面に酸化膜を形成することで、耐食性や外観の改善ができます。酸化処理は、特に高温環境での使用において有効です。
- 研磨と仕上げ C2680合金は研磨加工を行うことで、滑らかな表面を実現できます。これにより、外観が向上するだけでなく、摩擦を減らして機械的な効率が向上します。また、精密な仕上げが求められる部品においても優れた結果を得ることができます。
- パーティクルコーティング 特定の用途では、表面に特殊なコーティングを施すことで、耐久性や耐摩耗性を向上させることができます。パーティクルコーティングは、部品が極端な摩耗や腐食に直面する場合に有効です。
まとめ
C2680合金の選択において、機械的性質と化学成分が重要な要素となります。この合金は比較的硬度が高く、強度も十分であり、耐磨耗性にも優れています。さらに、耐食性に富んでいるため、さまざまな環境で使用されています。化学成分には銅と亜鉛が含まれており、その割合は合金の特性に大きな影響を与えます。 C2680合金を選択する際には、機械的性質と化学成分を徹底的に比較することが不可欠です。これにより、適切な用途に合わせた最適な合金を選定することができます。特に、耐摩耗性や耐食性が求められる場合には、その性質を重点的に検討することが重要です。黄銅と真鍮と砲金、見分け方と各素材の特性を徹底比較
黄銅、真鍮、そして砲金:基本を理解する
金属材料はその用途や性質によりさまざまに分類されますが、黄銅、真鍮、砲金は銅を基にした合金であり、いずれも幅広い用途で使用されています。それぞれの金属の特徴と利点について理解することが重要です。黄銅とは?その性質と用途
黄銅は、銅と亜鉛を主成分とする合金であり、銅の合金として最も一般的なもののひとつです。亜鉛を加えることにより、銅に比べて強度が増し、加工性も向上します。- 性質:
- 黄銅は、良好な耐腐食性を持ち、熱伝導性が高く、電気伝導性も良好です。
- 強度が高く、延性もあり、機械的な加工性に優れています。
- 金色に似た色をしており、見た目にも美しいです。
- 用途:
- 楽器(トランペット、サクソフォンなど)や装飾品(ジュエリー、メダルなど)に使用されることが多いです。
- 工業用途では、機械部品や自動車部品、配管などにも使用されます。
- 特に、腐食性が高い環境で使用されることが多いです。
真鍮の定義と特徴
真鍮は、黄銅の一種で、亜鉛含有量が異なるものを指します。亜鉛の割合を調整することにより、異なる機械的特性を持つ真鍮が作られます。これにより、異なる強度や硬さを持った真鍮が製造可能です。- 性質:
- 真鍮は加工がしやすく、切削性に優れています。
- 亜鉛を多く含む真鍮は強度が高く、耐摩耗性にも優れていますが、腐食には弱いこともあります。
- 低亜鉛のものは延性に優れ、さらに加工がしやすくなります。
- 用途:
- 軽量部品、細かい加工が必要な部品(ネジ、ボルト、ギア、楽器など)に多く使用されます。
- 電気部品や装飾品にも多く使用されています。
砲金の概要と利点
砲金は、銅とスズを主成分とする合金で、特に高い強度と耐摩耗性を持っています。スズを加えることにより、耐食性や耐摩耗性が向上し、鋳造性も改善されます。古くは砲身や銃器の製造に使用されていたことから「砲金」という名前がつけられました。- 性質:
- 砲金は非常に強く、耐食性や耐摩耗性が高いため、過酷な環境でも使用可能です。
- 冶金学的に安定しており、長期にわたりその性能を維持します。
- 音響性も良好で、特に重機や部品で求められる性質を持っています。
- 用途:
- 特に機械部品(軸受け、歯車、ポンプ部品など)や、耐摩耗性を要求される部品に広く使用されています。
- 自動車や産業機械の分野でも重宝されています。
黄銅と真鍮の特性
黄銅と真鍮は、どちらも銅と亜鉛を基にした合金ですが、成分の割合や特性にいくつか違いがあります。それぞれの合金は特定の用途に適した特性を持っており、理解することが重要です。黄銅と真鍮の成分の違い
- 黄銅:
- 主成分は銅(Cu)と亜鉛(Zn)で、亜鉛の含有量が通常5%から40%程度です。
- 他の元素(鉄、鉛など)を少量含むことがありますが、基本的には銅と亜鉛がメインの成分です。
- 真鍮:
- 真鍮も基本的には銅と亜鉛ですが、亜鉛の含有量が黄銅よりも多くなることがあります。特に亜鉛の割合が30%から45%程度に設定されることが多いです。
- また、真鍮には時折鉛(Pb)を含むことがあり、これによって切削性が向上します。
黄銅と真鍮の特性
- 黄銅:
- 強度が高く、加工性に優れています。
- 耐腐食性が良好であり、屋外や水中での使用に適しています。
- 見た目が金色に似ており、装飾用途にも適しています。
- 延性に優れており、複雑な形状への加工が可能です。
- 真鍮:
- 加工性が非常に良く、細かい部品や複雑な形状にも対応できます。
- 耐摩耗性が高く、強度もありながら適度な柔軟性を持っています。
- 亜鉛が多いため、硬度が高くなり、磨耗や摩擦に強いです。
- 色合いは黄銅に比べてやや黄色が強く、金属の表面が滑らかで美しいです。
真鍮と砲金の違いを専門家が解説
真鍮と砲金は、いずれも銅をベースにした合金ですが、成分や性質にいくつかの顕著な違いがあります。以下に、両者の違いを成分や性質、加工性、耐久性の観点から比較してみましょう。成分と性質の違い
- 真鍮:
- 主に銅(Cu)と亜鉛(Zn)を含み、亜鉛の含有量は通常30%から45%程度です。
- 真鍮の成分に鉛(Pb)を少量加えることもありますが、これは主に加工性を向上させるためです。
- 性質としては、加工性が良好で、耐摩耗性に優れています。見た目が美しく、金色に近い色合いを持つため、装飾用途にもよく使われます。
- 砲金:
- 砲金は、主に銅(Cu)にスズ(Sn)を加えた合金で、銅の含有率が大半を占めます。スズの割合は約5%から15%程度です。
- 砲金の特徴は、高い耐腐食性と強度を兼ね備えていることです。また、スズが加わることによって、耐摩耗性や耐熱性も向上します。
- 砲金は、色合いがやや赤みを帯びた黄銅色で、耐久性が高く、機械部品や高温環境でも使用可能です。
加工性と耐久性の比較
- 真鍮:
- 加工性においては非常に優れており、切削や成形が容易です。特に機械加工や精密加工において、高い精度が要求される部品でも問題なく加工できます。
- 耐久性は、亜鉛の含有量によって異なりますが、亜鉛の比率が高いため硬度が高く、耐摩耗性にも優れていますが、過度に強い圧力や衝撃には弱い場合があります。
- 砲金:
- 加工性については、真鍮ほどの加工性は持っていませんが、それでも他の金属材料に比べると比較的良好です。ただし、スズを含むため、若干硬度が高くなり、加工には一定の技術と適切な工具が必要です。
- 耐久性は非常に優れており、特に耐腐食性や耐摩耗性が求められる用途に最適です。水中での使用や、高温環境下でも長期間の使用に耐えうる性能を持っています。
青銅と黄銅の違い
青銅と黄銅は、いずれも銅をベースにした合金ですが、成分や特性、用途においていくつかの顕著な違いがあります。それぞれの特徴を比較し、識別方法と適用場面について解説します。青銅と黄銅の成分比較
- 青銅:
- 主に銅(Cu)にスズ(Sn)を加えた合金です。スズの含有量は約5%から20%の範囲です。
- 他にも、微量の鉛(Pb)やアルミニウム(Al)、マンガン(Mn)が添加されることがあります。
- 黄銅:
- 主に銅(Cu)と亜鉛(Zn)を含む合金で、亜鉛の含有量は通常30%から45%程度です。
- 一部の黄銅合金には鉛(Pb)を加えることで加工性を向上させることがあります。
見た目と特性で識別する方法
- 青銅:
- 色: 青銅は赤銅色をしており、スズの含有によって若干暗めの色合いを持っています。
- 特性: 青銅は、耐腐食性や耐摩耗性に優れ、硬度も比較的高いです。特に、海水や湿度が高い環境でも腐食しにくいため、船舶や海洋機器に適しています。
- 黄銅:
- 色: 黄銅は金色または黄褐色の色合いを持ち、亜鉛の比率によって色のトーンが変わることがあります。
- 特性: 黄銅は、加工性が良好で、切削や成形が容易です。また、耐摩耗性や耐久性も高いですが、青銅に比べると耐腐食性は劣る場合があります。
それぞれの用途と適用場面
- 青銅:
- 主な用途: 青銅は、特に耐腐食性が求められる環境で使用されます。例えば、海洋機器、船舶の部品、音楽器(シンバルや鐘)などです。
- 適用場面: 鉱山機械や発電機の部品、ブロンズ像、硬貨などでも利用されることが多いです。
- 黄銅:
- 主な用途: 黄銅は、主に装飾用途や精密部品に使われます。例えば、配管部品、機械部品、コイン、楽器の部品などです。
- 適用場面: その美しい金色が特徴的であるため、装飾品やジュエリーにもよく使用されます。また、電気接点や電子機器の部品にも利用されています。
まとめ
黄銅、真鍮、砲金はそれぞれ異なる特性を持ち、見分けることができます。黄銅は銅と亜鉛の合金で、真鍮も同様に銅と亜鉛の組み合わせですが、黄銅よりも亜鉛の含有量が多い特性があります。一方、砲金は銅と亜鉛、錫の合金で、真鍮よりも錫の含有量が多い特徴があります。これらの素材を比較することで、それぞれの違いや利用方法について理解することができます。C1100銅合金の機械的性質と化学成分の完全ガイド
C1100銅合金の概要
C1100銅合金は、非常に高い導電性を持つ銅合金で、主に電気伝導性が要求される用途に使用されます。この合金は、純度が99.9%以上の銅を基にしており、主に電線や電気機器の部品として広く利用されています。C1100合金はその優れた導電性と耐腐食性により、特に電気・電子産業で重要な役割を果たします。C1100銅合金とは
C1100銅合金は、ほとんど純粋な銅からなる合金で、銅にわずかな不純物を含みます。その特徴的な性質は、非常に高い電気伝導性と熱伝導性を持つことです。これにより、電気回路や電力伝送、さらには冷却システムなどで多くの用途に適しています。C1100は、銅の化学的性質を最大限に活かした合金であり、優れた耐食性も有しています。銅合金の分類と特徴
銅合金は大きく分けて、以下のように分類されます。- 純銅: C1100のように、99.9%以上の銅を含む合金で、非常に高い導電性を持つ。
- 黄銅(Brass): 銅に亜鉛を加えた合金で、耐食性や機械的特性が強化されます。家庭用品や装飾品に使用されることが多いです。
- 青銅(Bronze): 銅にスズを加えた合金で、非常に優れた耐摩耗性や強度を持ちます。主に機械部品や鋳物に使用されます。
- 銅ニッケル合金: 銅にニッケルを加えた合金で、海水腐食に対する耐性が高いのが特徴です。
C1100の産業における利用
C1100銅合金は、さまざまな産業で利用されていますが、主に以下の分野での利用が顕著です。- 電気産業: 電線、ケーブル、コンデンサ、コイルなど、電気の伝導が求められる部分に多く使用されます。C1100の高い導電性がこれらの部品にとって非常に重要です。
- 電子機器: 精密機器の内部部品や、端子、接続端子などの電子機器部品に利用されます。高い導電性と耐腐食性が求められるため、C1100銅は最適な選択肢です。
- 冷却システム: 熱伝導性が優れているため、冷却システムや熱交換器にも使用されます。特に、空調機器や発電所で冷却材を運ぶ管路などに利用されます。
C1100銅合金の化学成分
C1100銅合金は、主に純銅で構成されており、その化学成分は非常に高い純度の銅を特徴としています。その他にも微量元素が含まれており、合金の特性や加工性を高めています。以下に、C1100銅合金の化学成分について詳しく解説します。主要成分の解説
C1100銅合金の主要成分は、以下の通りです:- 銅 (Cu): 99.9%以上
- C1100の最も重要な成分であり、合金全体の99.9%以上を占めています。これにより、非常に高い導電性と熱伝導性が確保されています。
- 酸素 (O): 最大0.04%
- 純銅において酸素は不純物として含まれることがあり、酸化による腐食のリスクがあります。しかし、C1100合金では酸素の含有量は非常に低く抑えられ、良好な耐腐食性を保持しています。
含有する微量元素
C1100銅合金には、銅以外にも微量元素が含まれることがありますが、その含有量は極めて少ないです。これらの微量元素が合金の機械的性質や耐食性を改善します。主な微量元素は次の通りです:- 鉄 (Fe): 最大0.05%
- 鉄は銅合金中に微量で存在し、合金の強度に影響を与えることがありますが、C1100においてはその含有量は非常に低く、特に導電性を損なうことはありません。
- リン (P): 最大0.01%
- フォスファーは、銅の酸化を防ぐ役割を持ち、耐腐食性を向上させることがあります。C1100合金では、微量に含まれており、耐食性を向上させる役割を果たします。
- その他の微量元素: 微量の金属元素(例: 硅素、アルミニウムなど)が含まれている場合がありますが、その影響は限定的です。
化学成分の規格と基準
C1100銅合金は、JIS(日本工業規格)、ASTM(アメリカ材料試験協会)、およびその他の国際規格に基づいてその化学成分が規定されています。以下は、代表的な規格におけるC1100の化学成分基準です:- JIS H 3100(日本工業規格): C1100は「高純度銅」に分類され、純度は99.9%以上、酸素含有量は最大0.04%となっています。
- ASTM B170(アメリカ規格): C1100は、ASTM B170の規定にも準拠し、銅含有量は99.9%以上であり、酸素含有量は最大0.04%以下であることが求められます。
C1100銅合金の機械的性質
C1100銅合金は、高純度の銅を基にした合金であり、優れた導電性、耐食性、そして加工性を持っています。特に電気機器や配線などで広く使用される素材ですが、その機械的性質は製品の性能や耐久性に大きな影響を与えます。ここでは、C1100銅合金の主な機械的性質について詳しく見ていきます。引張強度とは
引張強度は、材料が引っ張られた際にどれだけの力に耐えることができるかを示す指標であり、材料の強さを評価する重要な性質です。C1100銅合金の引張強度は比較的低めですが、その柔軟性が他の材料と比べて優れた加工性を提供します。引張強度はおおよそ210〜250MPa(メガパスカル)程度で、これは銅の純度が高いため、強度よりも加工性や導電性が重視されることを意味します。伸びと硬度
C1100銅合金は、引張強度が高いわけではありませんが、非常に高い伸び(塑性)を持っています。この伸びにより、C1100銅合金は加工が容易であり、曲げや成形などの加工において非常に優れた特性を示します。硬度については、銅は比較的軟らかいため、C1100銅合金も他の金属と比べて低い硬度を持ちます。通常、ブリネル硬度(HB)は50〜70程度です。これにより、C1100銅合金は機械加工や成形に適しており、特に高精度の部品製造に向いています。導電性と熱伝導性
C1100銅合金は、非常に高い導電性を持つ材料です。銅の純度が高いため、電気や熱を効率よく伝えることができます。電気伝導率はおおよそ101〜102%IACS(国際銅業協会基準)であり、これは電気機器や配線材料にとって非常に重要な特性です。 また、C1100銅合金は熱伝導性にも優れており、高い熱伝導率を持っています。これにより、熱を効率よく伝える必要がある機器や装置に使用されることが多いです。熱伝導率は、約398W/m・K(ワット毎メートル・ケルビン)であり、非常に効率的に熱を移動させることができます。C1100銅合金の加工性
C1100銅合金は、その高い導電性や熱伝導性が特徴的であり、様々な工業用途で重要な役割を果たしています。その優れた特性を最大限に活かすためには、適切な加工方法とその影響を理解することが重要です。ここでは、C1100銅合金の加工性に関する重要な要素、加工方法、熱処理とその機械的性質への効果、さらには冷間加工と熱間加工の比較について詳しく解説します。加工方法とその影響
C1100銅合金は、他の銅合金に比べて柔軟性と延性に優れており、加工が比較的容易です。主な加工方法としては、圧延、引き抜き、絞り、切削、溶接などが挙げられます。- 圧延: C1100銅合金は、圧延加工を行うことで厚さや形状を調整することが可能です。このプロセスでは、温度管理が重要であり、過度の熱処理を行わないように注意する必要があります。
- 引き抜き: これは、銅合金の導線や細い部品の製造に使われる方法であり、C1100銅合金はその延性を活かして、細い線や高精度の部品に加工することができます。
- 切削: 銅合金は比較的柔らかいため、切削工具による加工も容易です。特に高精度の機器や部品製造には適しており、加工後の仕上がりも良好です。
- 溶接: C1100銅合金は、TIG溶接やMIG溶接においても良好な結果を得ることができ、耐食性と導電性を保ったまま、接合が可能です。
熱処理と機械的性質への効果
C1100銅合金は、熱処理を施すことでその機械的性質が大きく変化します。特に、強度や硬度を高めるための熱処理方法は重要であり、最適なプロセスを選択することが必要です。- アニール処理: アニール処理を行うことで、C1100銅合金は内部応力を解放し、延性や柔軟性を向上させることができます。アニール後のC1100銅合金は、引張強度が若干低くなりますが、加工性が格段に向上します。
- 焼き入れ: C1100銅合金は焼き入れにより硬度が向上しますが、これは熱伝導性や導電性を若干低下させる可能性があります。特に、電気機器に使用する場合には、過度の焼き入れが問題となることもあるため、バランスの取れた熱処理が求められます。
冷間加工と熱間加工の比較
C1100銅合金の加工において、冷間加工と熱間加工はそれぞれ異なる利点と特性を持っています。それぞれの方法について詳しく見ていきます。冷間加工
冷間加工は、材料が常温で加工される方法です。C1100銅合金では、冷間加工により強度や硬度が向上しますが、延性が若干失われることがあります。冷間加工の主な利点は以下の通りです。- 精度の向上: 冷間加工は、より精密な部品を作成するために使用されます。特に、薄い板や細かい部品の製造に向いています。
- 表面仕上げの向上: 冷間加工により、製品の表面が滑らかで高精度な仕上がりとなります。
- 強度の向上: 冷間加工を行うことで、引張強度や硬度が向上し、耐久性が増します。
熱間加工
熱間加工は、材料が高温に加熱された状態で加工される方法であり、C1100銅合金の場合、より容易に形状変更が可能です。主な利点としては以下の点があります。- 加工の容易さ: 高温での加工により、材料が柔らかくなり、複雑な形状の部品を容易に作成できます。
- 低い加工力: 高温によって銅合金が柔らかくなるため、加工に必要な力が少なく、加工機械にかかる負荷が軽減されます。
- 延性の向上: 高温で加工することで、銅合金の延性が向上し、より大きな変形が可能となります。
冷間加工と熱間加工の選択
- 冷間加工: 精度重視の小型部品や表面仕上げが重要な場合に適しています。
- 熱間加工: 複雑な形状や大きな部品の加工に最適です。
C1100銅合金の耐久性と腐食抵抗性
C1100銅合金は、高い導電性と加工性を誇る金属ですが、その耐久性と腐食抵抗性も非常に重要な特性です。特に電気機器や配管、接続部分で使用されることが多いこの合金は、長期的な使用に耐えるために、その耐久性と腐食抵抗性が求められます。ここでは、C1100銅合金の耐久性と腐食抵抗性に関する評価方法や、影響を与える要因について詳しく説明します。耐久性の評価方法
C1100銅合金の耐久性は、主にその使用環境や条件によって異なります。耐久性を評価するためには、以下の方法が一般的に使用されます。- 引張試験: 引張試験は、C1100銅合金の機械的強度を評価するための基本的な方法です。この試験では、材料が破断するまでにどれだけの引っ張り力を耐えられるかを測定します。引張強度や伸び率を確認することで、長期間の使用に耐えられるかを評価できます。
- 疲労試験: 疲労試験では、C1100銅合金に繰り返しの応力を加え、破断までのサイクル数を測定します。これにより、材料が何度の応力を繰り返し耐えられるかを評価し、長期使用における耐久性を確認します。
- 熱衝撃試験: 温度変化が激しい環境下での耐久性を測定するために、熱衝撃試験を行うことがあります。C1100銅合金が急激な温度変化に対してどれほど耐えられるかを確認することで、実際の使用環境をシミュレーションし、耐久性を予測します。
腐食抵抗性の要因
C1100銅合金の腐食抵抗性は、その使用環境において重要な要素となります。特に銅合金は、化学的な攻撃に対して敏感な部分がありますが、いくつかの要因によってその腐食抵抗性が強化されます。- 酸素と水分: 銅合金は酸素と水分と反応しやすいですが、C1100銅合金は酸化層が形成されることで腐食が遅くなります。この酸化層は保護的な役割を果たし、さらなる腐食を防ぎます。しかし、強い酸性やアルカリ性環境では、この酸化層が劣化しやすくなるため、腐食が進行する可能性があります。
- 塩分と湿度: 高湿度や塩分を含む環境(例:海岸地帯)では、C1100銅合金が速やかに腐食する可能性があります。特に塩分は、銅の表面に亀裂や腐食を引き起こしやすいため、使用環境に合わせた適切な対策が必要です。
- 化学物質の影響: C1100銅合金は、特定の化学物質に対して脆弱です。例えば、硫化物やアンモニアなどは銅合金に対して腐食を引き起こすことがあります。このため、化学的に過酷な環境では、C1100銅合金の使用を避けるか、適切な保護処置を施す必要があります。
合金の長期安定性
C1100銅合金の長期安定性は、その構造と組成に依存します。純度の高い銅を使用したC1100銅合金は、比較的安定した物理的特性を持ち、長期間の使用でもその特性を保持することができます。長期安定性を確保するためには、以下の点が重要です。- 合金の純度: C1100銅合金は、99.9%以上の純度を誇ります。この高い純度により、他の不純物や合金元素が腐食を引き起こす可能性を低減させ、長期間の安定した性能を維持することができます。
- 製造プロセスの一貫性: C1100銅合金は、その製造過程において品質が厳密に管理されています。均一な品質が確保されることで、合金全体の長期的な安定性が保証されます。
- 使用環境に応じた処理: 特に過酷な環境で使用される場合、C1100銅合金は熱処理や表面処理を施すことで、耐食性を向上させ、長期的な安定性を維持することができます。
まとめ
C1100銅合金は機械的性質と化学成分について詳細な情報を提供しています。この合金は非常に高い導電率を持ち、耐食性に優れています。さらに、溶接や加工性に優れており、多くの産業で幅広く使用されています。化学成分の偏りや不均一性によって機械的性質が変化することもあるため、品質管理には注意が必要です。C1100銅合金を使用する際は、それぞれの特性を理解して適切に取り扱うことが重要です。C4641材料の性質徹底解説!強度・比重・ヤング率の基本情報
真鍮C4641の基本と性質
真鍮C4641とは
真鍮C4641は、銅を主成分とする合金で、特に耐食性や加工性に優れた特性を持つ素材です。C4641は、銅(Cu)に亜鉛(Zn)を主成分とし、その他に微量の鉛(Pb)や錫(Sn)を含むことが特徴です。この真鍮は、特に機械的特性や耐摩耗性に優れているため、さまざまな工業用途に使用されます。C4641の耐食性と成分
C4641真鍮は耐食性に優れ、海水や湿気の多い環境でも安定した性能を維持します。特に亜鉛の含有量が適切に調整されているため、耐食性が向上しています。以下がC4641の主な成分です:- 銅 (Cu):主成分であり、真鍮の基礎となる金属です。高い耐腐食性と導電性を提供します。
- 亜鉛 (Zn):強度を向上させるための主要成分で、真鍮の特性に大きな影響を与えます。
- 鉛 (Pb):加工性を向上させるために微量含まれており、特に切削加工の際に有効です。
- その他の成分:微量の錫やその他の金属が含まれることもあり、耐食性や強度を高める役割を果たします。
真鍮の物理的性質
真鍮C4641は、物理的にも非常に優れた特性を持っています。主な物理的性質には以下の点が挙げられます:- 硬度:真鍮C4641は比較的硬い材料で、摩耗に強いという特性を持っています。ただし、亜鉛含有量によって硬さは調整可能で、柔軟性とのバランスが取れた特性を実現しています。
- 導電性:銅合金であるため、高い導電性を有しており、電気部品にも利用されます。特に低い温度環境でも性能を発揮します。
- 耐摩耗性:真鍮C4641は摩擦に強く、機械的な部品やシャフトなどで頻繁に使用されます。長期間の使用にも耐えることができ、メンテナンスの手間を減らします。
- 展性と引張強度:加工性が非常に良く、引張強度も高いため、さまざまな形状への加工が可能です。特に精密な部品の製造にも適しています。
真鍮の特性や性質
真鍮の化学的特性
真鍮は主に銅と亜鉛を含む合金で、その他に微量の鉛や錫などの元素を含むことがあります。これにより、真鍮は以下のような化学的特性を持っています:- 耐食性:真鍮は錆びにくく、耐食性に優れています。特に、亜鉛の含有量が多い場合、湿気や塩水環境でも強い耐食性を発揮します。これにより、海洋設備や配管などで広く使用されます。
- 酸化:銅の合金であるため、酸化しやすい性質を持っています。酸化が進むと、表面に緑青(銅の酸化物)が生成され、これが真鍮の特徴的な外観を作り出します。酸化が進むことで、さらに耐食性が向上する場合もあります。
- 化学的安定性:化学反応に対して比較的安定しており、多くの酸や塩基に耐性がありますが、強い酸性または塩基性の環境では腐食が進行する可能性があります。
真鍮の熱的特性
真鍮は熱的に安定しており、特に熱伝導性が高いという特性があります:- 熱伝導性:真鍮は良好な熱伝導性を持っており、熱が素早く伝わるため、熱交換器や冷却部品に利用されます。銅の高い熱伝導性に亜鉛を加えることで、熱伝導性が良好であり、電子機器などで効果的に利用されます。
- 膨張率:真鍮は金属中でも比較的膨張率が低いため、温度変化による膨張や収縮が抑えられます。これにより、温度変化の激しい環境でも安定した性能を発揮します。
- 融点:真鍮の融点は約900°C前後で、銅と亜鉛の比率によって融点は若干異なります。亜鉛が多いほど融点が低くなり、加工が容易になります。
真鍮の電気的特性
真鍮は電気伝導性にも優れており、銅と亜鉛の組み合わせによって、特定の用途において非常に高い性能を発揮します:- 電気伝導性:真鍮は銅を基にしているため、良好な電気伝導性を持ち、電気機器の接点や端子、コネクタに利用されます。電気的な抵抗は銅より若干高いものの、伝導性は十分に高く、電気的な接触に適しています。
- 接触特性:真鍮は金属間の接触部品としても使用され、接点や端子が摩耗しにくく、安定した電気的性能を長期間維持できます。また、亜鉛含有量によって、摩擦抵抗や耐摩耗性も向上し、電気機器で広く使われています。
- 絶縁性:純粋な銅よりも電気絶縁性は低くなりますが、亜鉛が含まれているため、純銅よりは絶縁性に劣ります。そのため、真鍮は主に電気回路の導電部分に使用され、絶縁部分には適していません。
黄銅(真鍮)のメリットとデメリット
黄銅のメリット
黄銅(真鍮)は、銅と亜鉛を主成分とする合金で、以下のような多くのメリットを持っています:- 優れた耐食性:黄銅は水分や湿気、塩水環境に対して強い耐食性を持っています。これにより、海洋設備や水道管、船舶部品、金属製の装飾品などの用途に適しています。
- 優れた加工性:黄銅は加工がしやすい素材で、切削、鍛造、圧延、溶接など多くの加工方法に対応できます。これにより、精密な部品を必要とする産業で利用されています。
- 高い耐摩耗性:亜鉛を含むことにより、摩擦に強く、耐摩耗性が向上します。これにより、機械部品やギア、軸受けなどで使用されることが多いです。
- 優れた電気伝導性:銅を含んでいるため、良好な電気伝導性を持ち、電気機器や接点、端子などの電子機器に適しています。
- 美しい外観:黄銅は光沢があり、金色の外観を持っているため、装飾品や家具、建築材としても利用されます。
黄銅のデメリット
黄銅は多くのメリットを持っていますが、いくつかのデメリットもあります:- 強度の限界:黄銅は他の金属に比べて比較的強度が低いため、高強度を要求される部品や構造物には向いていません。例えば、重機や高荷重がかかる部品には不向きです。
- 亜鉛の腐食問題:亜鉛を含むため、酸性環境や高温にさらされると、黄銅は「デンプラゼーション現象(亜鉛腐食)」を起こし、亜鉛が溶け出して機械的強度が低下する可能性があります。これにより、耐久性が低くなることがあります。
- 高価:黄銅は純粋な銅や他の金属合金に比べて高価な場合があり、特に亜鉛含有量が高い場合はコストが上昇することがあります。そのため、大量生産には不向きな場合もあります。
使用環境における考慮点
黄銅を使用する際には、以下の点を考慮する必要があります:- 温度の影響:黄銅は高温環境下での性能がやや低下するため、高温で使用する場合には、適切な温度管理や熱処理が必要です。
- 腐食環境の対策:酸性またはアルカリ性の環境での使用には注意が必要です。特に湿気や塩水環境では亜鉛の腐食が進む可能性があるため、表面処理やコーティングを施すことが望ましいです。
- 荷重の考慮:重い荷重がかかる部品に使用する場合、強度や耐久性に注意が必要です。強度が求められる用途には、より強い金属や合金を選ぶべきです。
ネーバル黄銅C4641の性質と特性
ネーバル黄銅の定義と特徴
ネーバル黄銅(Naval Brass)は、主に銅(Cu)と亜鉛(Zn)を主成分とし、少量の錫(Sn)を加えた合金です。錫の添加により、特に海水や湿気の多い環境下で優れた耐腐食性を発揮します。この合金は、耐久性が高く、機械的性質が良好であり、金属の摩耗に対する耐性が向上します。ネーバル黄銅は、特に海洋産業において重要な材料として広く使用されています。C4641の耐海水性
C4641は、ネーバル黄銅の一種であり、海水環境における耐食性に優れています。錫の含有量が高いため、海水による腐食や湿気、塩分に対して強力な防御力を持っています。これにより、C4641は海上機器、船舶部品、海洋設備において非常に信頼性の高い材料となっています。- 耐海水性:C4641は、塩水や海水環境での使用に適しており、腐食の影響を受けにくいです。この特性は、特に船舶の構造部品、船舶のプロペラ、海底ケーブル、海洋プラットフォームなどで重要です。
- 耐摩耗性:海水や砂粒などによる摩耗に強いため、長期間使用しても磨耗しにくい特性を持っています。
ネーバル黄銅の応用分野
ネーバル黄銅は、主に次のような分野で利用されています:- 船舶産業:船のプロペラ、ハル(船体)、バルブ、ポンプなど、海水に常にさらされる部品に使用されています。耐腐食性と耐摩耗性を活かして、船舶の長寿命化に貢献しています。
- 海洋設備:海底ケーブル、海洋プラットフォーム、漁業機器など、厳しい海水環境下でも耐久性を保持する必要のある部品に使用されます。
- 機械部品:摩擦が多い環境で使用されるギア、軸受け、歯車などにも適しています。耐摩耗性と強度が必要な部品において広く利用されています。
伸銅・真鍮C4641の強度
強度とは
強度とは、材料が外部の力や負荷に対して破壊せずにどれだけ耐えることができるかを示す特性です。通常、強度は引っ張り強度(引張強度)や降伏強度(降伏点)で測定されます。強度が高い材料は、構造物や部品として使用する際に耐久性が求められる場面において重要です。C4641の機械的強度
真鍮C4641は、良好な機械的強度を持つ合金であり、特に強度と耐久性が求められる応用分野で使用されています。C4641は、銅と亜鉛の合金に錫を加えたことで、耐食性を高めつつ、機械的特性も改善されています。- 引張強度:C4641の引張強度は、他の金属と比較して高く、外的な力に対して良好な耐性を持っています。特に、海洋環境や摩擦が発生する部品に使用される際に重要です。
- 降伏強度:降伏強度とは、材料が変形を始めるポイントを示すもので、C4641は一定の強度を保持し、曲げや引っ張りなどの力が加わる状況でも破損しにくい特性を持っています。
ヤング率とC4641
ヤング率(弾性率)は、材料が引っ張り力を受けた際にどれだけ変形するかを示す物理的特性です。ヤング率が高い材料は、変形に対して抵抗力が強く、硬いとされています。- C4641のヤング率:C4641のヤング率は、約100 GPa(ギガパスカル)程度で、比較的高い弾性を持つ金属です。これにより、C4641は強度が高く、かつ変形しにくい特性を持っています。この特性は、機械的負荷を受ける部品や構造物にとって非常に重要です。
まとめ
C4641材料は、耐食性が高く、機械的強度も優れています。この材料は、銅やベリリウム、クロム、ニッケルなどの成分で構成されており、これらの成分が優れた性能をもたらしています。強度や比重、ヤング率などの基本情報を理解することで、C4641材料の特性を活かした効果的な利用が可能となります。これらの情報を把握することは、材料を使用する際に重要な要素となります。高強度C3604真鍮の魅力!引張強度と比重を解析
ご覧の皆様、本日は高強度C3604真鍮についてご紹介いたします。引張強度や比重などの物理的性質に焦点を当て、その魅力を解析していきます。高強度C3604真鍮は、その特性からさまざまな産業分野で重要な役割を果たしています。この記事では、この素材の特性について深く掘り下げるとともに、どのようなメリットや活用方法があるのかについて詳しく解説していきます。それでは、魅力あふれる高強度C3604真鍮の世界へ、一緒に旅してみましょう。
Contents
C3604真鍮とは
C3604真鍮の基本的な特徴
C3604真鍮は、その高い引張強度と適度な比重で注目されています。まず結論から言うと、C3604は様々な工業製品や部品に使用されるための理想的な材料です。その理由は、物理的性質が非常にバランスが良く、高い強度を持ちながら加工しやすいという特徴にあります。具体的には、この真鍮合金は引張強度が約370〜520MPaと高く、しかも比重が約8.4g/cm³と金属としては比較的軽量であるため、自動車の部品や電子機器のコネクタといった用途に適しています。また、耐食性や機械的性質が良いため、精密な部品加工にも頻纍します。従って、C3604真鍮はその強度と重量のバランスから、幅広い産業での採用が進んでおり、その魅力は多方面にわたることが再確認されます。
C3604の化学的組成
高強度C3604真鍮は、その卓越した引張強度と適度な比重により、工業材料としての魅力が高いです。引張強度とは、材料が破断するまでに耐えうる最大の引張応力のことであり、C3604真鍮はその強度が非常に高いため、耐久性が要求される部品に適しています。また、その比重はおおよそ8.5であり、金属材料としては比較的軽量で加工しやすい特徴を持ちます。例えば、精密機械の部品や電子機器のコネクタ、装飾品など幅広い用途で利用されています。これらの物理的性質は、C3604真鍮が多岐にわたる産業分野において重宝される理由と言えるでしょう。まとめると、C3604真鍮はその高い引張強度と適度な比重を活かして、様々な産業で必要とされる耐久性と加工性を兼ね備えた材料であり、その魅力は今後も高まることでしょう。
C3604真鍮の物理的性質
高強度C3604真鍮は、その優れた引張強度と適度な比重で、工業用途に非常に魅力的な材料です。C3604真鍮は、特に機械加工性に優れた銅合金として知られ、その物理的性質により幅広い用途で利用されています。この合金の引張強度は一般的な真鍮よりも高く、これにより耐久性の高い部品や構造物の製造に適していることが分かります。例えば、高い耐久性を要求される自動車部品や精密機器のコンポーネントでの使用が挙げられます。また、比重は鉄などの他の金属に比べて低く、重量削減が求められる分野においても利点となります。このように、C3604真鍮はその引張強度と比重のバランスにより、多岐にわたる産業分野で重宝される材料であると結論づけることができるのです。
C3604真鍮の引張強度
引張強度とは
高強度C3604真鍮は、その優れた物理的性質により、工業界で注目されています。特に、C3604真鍮の引張強度と比重は、その使用範囲を広げる重要な指標です。引張強度が高いということは、材料が破断に至るまでに大きな力に耐えられる能力を意味しており、比重は材料の密度を示し、強度と密度のバランスが求められる製品に選ばれます。
例えば、C3604の引張強度は一般的な鋼材と比較しても高く、耐久性が必要な自動車部品や精密機械に利用されることが多いです。さらに、比重が一定で強度が高いため、物を支える構造部材としても最適です。
結論として、C3604真鍮の引張強度と比重は工業用途におけるその魅力を形作る核心となる属性であり、その物理的性質によって様々な産業での使用が期待されます。高強度とばね性能を両立させたC3604は、未来も明るい材料の一つといえるでしょう。
C3604真鍮の強度特性
C3604真鍮はその優れた引張強度と適度な比重で多くの工業分野で重宝されています。この合金は、特に機械的負荷がかかる部品に使用されることが多く、その理由は物理的性質のバランスの良さにあります。例えば、C3604は引張強度が360-370 MPa程度に達し、比重は約8.5となっているため、耐久性と加工のしやすさを兼ね備えています。このように、C3604はその性質を生かして自動車や家電製品の部品から、精密機器のコンポーネントまで幅広い用途で利用されています。また、真鍮特有の腐食に強い特性もこの合金の長所であり、耐久性が求められるアプリケーションにおいて信頼性を高めています。まとめると、C3604真鍮は引張強度と比重をはじめとする物理的性質の組み合わせによって、工業製品の信頼性と効率性を向上させる魅力的な材料です。
引張強度の測定方法
高強度C3604真鍮は、優れた物理的性質を持つことで知られています。特に、この材料の引張強度と比重は、その使用範囲を広げる上で重要な要素です。引張強度は材料が引っ張り力に対してどれだけの抵抗を示すかを示す指標であり、C3604真鍮ではこの値が高いことが魅力の一つです。この高い引張強度によって、耐久性が要求される機械部品や建築資材に適しており、信頼性の高い製品作りに不可欠です。
また、比重は材料の密度を示す値で、材料の質感や重量感の調整に影響を与えます。C3604真鍮は適度な比重を持つため、加工性に優れながらも、しっかりとした重量感を保持することができるのです。例えば、高級感を出したい筐体材料や装飾品に使用することで、上質な質感を演出することができます。
これらの物理的性質は、空間の美観を損ねることなく、機能性と耐久性を兼ね備えた製品を作るためには欠かせない要素です。その結果、高い引張強度と適度な比重を持つC3604真鍮は、さまざまな産業で重宝されているのです。
C3604真鍮の比重
比重とは
高強度C3604真鍮は、その物理的性質において多くの産業で重宝されています。中でも、引張強度と比重は、この材料が選ばれる大きな理由です。C3604というのは、銅と亜鉛を主成分とする真鍮の一種であり、高い引張強度を持っています。これは、材料がどれだけの力を受けた際に折れたり、壊れたりしないかを示す指標で、高い数値を示すほど丈夫とされます。例えば、工業部品や建築材料など、強度が求められる用途にはこのC3604真鍮が適しています。
また、比重というのは、材料の密度を表す物理量で、その値によって重さと強度のバランスが考えられます。C3604真鍮の比重は8.5程度と、他の金属材料と比較して適度な重さを持っており、そのため機械部品などにもよく使用されます。軽すぎず、かつ丈夫な材料は、様々な製品の信頼性と耐久性を保証する要素となり得ます。
このように、C3604真鍮は高い引張強度と適切な比重を兼ね備えており、そのために多くの分野で活躍しています。強度が必要な場面や、重さと強度のバランスが求められる製品設計において、C3604真鍮は魅力的な選択肢と言えるでしょう。
C3604の比重とその影響
C3604真鍮は、その優れた物理的性質により、幅広い工業製品に使用されています。特に、引張強度と比重は、この素材を選択する際の決定的な要因となっています。引張強度は、材料が引っ張りに耐えられる力の大きさを示し、C3604真鍮は高強度でありながら加工が容易であるため、精密機械部品や電気部品の製造に適しています。
また、比重は、材料の密度を表す数値であり、C3604真鍮の比重は約8.5 g/cm³です。これは鉄よりも軽く、同じ体積の鉄製品と比較して重量が軽減されるため、自動車や家電製品において重量削減が求められる部品に用いられることが多いです。
具体的な例として、C3604真鍮は自動車のバルブやコネクタ、建築材料のドアノブや水栓金具などに使用されます。これらの部品は、強度が要求されるとともに、重量削減も重要なポイントです。C3604真鍮はこれらの要求を満たし、長期にわたり信頼性の高い性能を保持することができます。
結論として、C3604真鍮はその高い引張強度と適度な比重のバランスにより、様々な産業で重宝されているのです。耐久性と加工性を兼ね備えるこの素材は、今後も多岐にわたるアプリケーションでの使用が期待されます。
比重測定の方法
高強度C3604真鍮の性質には、特に引張強度と比重が際立っています。この合金は、その物理的性質から幅広い産業で利用されており、耐久性が求められる部品に不可欠です。例えば、C3604の引張強度は一般的な真鍮よりも高く、精密な機械部品や耐食性が要求される電子部品に適しています。一方で、比重は約8.4~8.7と特に高いわけではありませんが、この程度の比重は、強度を保ちながらも加工しやすいことを示しています。具体的な使用例としては、自動車の燃料供給システムや水道の配管接続部など、安定した性能が求められる箇所での採用が挙げられます。このようにC3604真鍮は、優れた引張強度と適度な比重を兼ね備えており、その魅力は多岐にわたる用途で発揮されています。
C3604真鍮の加工のポイント
加工性の概要
C3604真鍮はその高い引張強度と適度な比重で、多様な産業で重宝されています。この合金は、特に機械部品や電子部品の製造において、その物理的性質が求められる場面が多いのです。C3604の引張強度は、部品が受ける力に対する耐久性を示し、これが高いほど、部品の信頼性が増します。また、比重が適度であることは、軽量であることに加え、安定した物質で形成されていることを意味します。具体例として、精密機器のギアや、楽器の吹き口など、精度と耐久性が要求される部分に利用されています。さらに、C3604は優れた加工性を持つため、高い精度で複雑な形状に加工することが可能です。このように、C3604真鍮は、引張強度と比重のバランスの良さが、さまざまな用途での利用を促進しているのです。
C3604真鍮の切削加工
高強度C3604真鍮は、その物理的性質が様々な分野で高く評価されています。特に引張強度は真鍮の中でも際立っており、これにより耐久性と信頼性が求められる環境下での使用に適しています。比重は約8.5と他の金属と比較しても適度で、このバランスの取れた特性が加工のしやすさをもたらしています。
例えば、C3604真鍮は自動車のバルブやコネクタといった部品に使われることが多いです。これらの部品は、高い強度と安定した重量が重要視されるため、C3604真鍮の特性が非常に適しているのです。また、水道管の継手材料としても使用されることがあり、その耐食性と強度が安全な水の供給を支えます。
結論として、C3604真鍮は引張強度が高く、比重に優れており、これにより加工性にも優れていると言えます。このような物理的性質が、幅広い用途での利用を可能にし、多くの製造業界において重宝されています。
熱処理と表面処理
C3604真鍮は、その優れた物理的性質から、工業部品や建築材料として広く採用されています。特に引張強度と比重は、この材料の特長を際立たせる要素となっており、その魅力を深く解析することで、なぜC3604が選ばれ続けているのかが明らかになります。具体的に、C3604は高い引張強度を有しており、これは材料が大きな力に耐えうる能力を意味します。そのため、耐久性が求められる機械部品や建築金具などに理想的です。さらに、C3604の比重は真鍮の中でも適度であり、重量感のある製品に求められる質感と強度を両立しています。
また、熱処理により物理的性質が向上することが多く、柔軟性と硬さのバランスを利用した加工が可能です。表面処理を施すことで、耐食性や美観を高めることができるため、見た目と機能性を兼ね備えた製品作りに不可欠です。これらの性質から、C3604真鍮は多様な産業で使われることが期待され、引き続き重宝されることでしょう。
C3604真鍮の用途
一般的な用途と事例
C3604真鍮は、その優れた引張強度と適度な比重により、多くの工業製品に利用されている存在です。一般的な真鍮よりも高い引張強度を誇るこの材料は、耐久性が必要な部品や構造物に好まれます。例えば、精密機械部品や自動車の小部品、建築資材などに使用されており、これらの用途では材料の信頼性が求められます。C3604真鍮は、物理的性質としても安定しており、加工しやすさも兼ね備えているため、幅広い分野での活用が可能です。複雑な形状を作り出す際にも、その加工の容易さが生産性向上に寄与しています。そして、比重が適度であることから、重量を抑えたい部品にも最適です。このように、C3604真鍮はその物理的性質を活かし、多方面での需要が絶えず、今後も引き続き、その魅力が評価される素材であると結論づけられます。
特殊な用途と事例
C3604真鍮は、優れた引張強度を持つことで知られ、その比重も物理的性質を理解する上で重要な指標です。この合金はその高強度から、耐久性が要求される機械部品や電気部品に多く用いられています。例を挙げると、精密機器のコネクタや自動車のバルブなどがC3604真鍮で作られており、これらの部品は一定の負荷がかかる環境下でも信頼性を維持できる必要があります。
C3604真鍮の比重は約8.4~8.5であり、これによって強度と重量のバランスを見極めることができます。また、この比重は真鍮の中でも特に重く、機械的な強度を求められる用途に適していると言えるでしょう。
高強度C3604真鍮は、その物理的性質から様々な工業製品に不可欠な材料としての地位を確立しています。引張強度と比重のバランスが取れたこの合金は、耐久性と信頼性を要求される多くの分野で使われ続けることでしょう。
C3604真鍮とRoHS対応
RoHS指令とは
高強度C3604真鍮は、その卓越した引張強度と適度な比重という物理的性質により、工業用途に広く利用されています。この素材は特に機械部品や電気部品の製造において、その強度と耐久性で選ばれています。C3604は引張強度が高く、比重が約8.5と、他の一般的な金属素材と比べ重さと強度のバランスが取れているため、精密さが求められる部品に最適です。例えば、小型のギアや連結部品など、精緻な加工が施された製品にC3604が用いられることが多いです。また、高い導電性も持ち合わせているため、電子機器の接点材料としても使用されます。これらの理由から、高強度C3604真鍮は多岐にわたる産業分野で重宝され、その魅力は高い評価を受けています。強度と比重のバランスが求められる用途では、C3604真鍮の使用はこれからも増え続けることが予想されます。
C3604真鍮のRoHS対応状況
C3604真鍮は、RoHS指令に適合する非鉛素材として、その引張強度と比重の優れた物理的性質により、電子機器や自動車部品など幅広い分野で注目を集めています。この真鍮合金は高い引張強度を有しており、そのため機械部品や装飾品の素材として非常に信頼されています。具体的には、C3604真鍮は引張強度が500~700MPaとされ、他の一般的な真鍮材料と比較しても高い値を示しています。また、比重が約8.4のため、重量をある程度保ちながらも、硬度と耐久性を兼ね備えることができるのです。
さらに、C3604真鍮は切削性にも優れており、精密な加工が必要な部品にも適しています。このような物理的性質の結果、C3604真鍮は多岐にわたる産業で利用される有望な材料として広く認知されており、今後もその需要は拡大していくことが予測されます。引張強度の高さと適度な比重が、C3604真鍮の魅力を形作っていると言えるでしょう。
環境への影響
高強度C3604真鍮は、その卓越した物理的性質から、多くの産業分野で重宝されています。特に、引張強度と比重は、C3604真鍮の利点として挙げられます。まず結論から申し上げると、C3604真鍮の高い引張強度は、耐久性が求められる部品に適しているのです。
その理由は、引張強度が高い材料は、負荷がかかった時に破損しにくいという特性を持っているためです。C3604真鍮は、機械部品や電子機器の接続部によく使用され、信頼性の高いパフォーマンスが期待できます。特に、強度が必要なギアやベアリングなどに使用されることが多く、これらの部品は高い精度と耐久性が求められるため、C3604真鍮が好まれるのです。
また、比重に関しては、C3604真鍮は適度な重量を有し、その結果、安定した質量感が要求される部品において重量バランスを取るのに役立ちます。例えば、楽器のトランペットのように、特定の重量感が求められる製品には、C3604真鍮が使用されることがあります。
結局のところ、高い引張強度と適切な比重を持つC3604真鍮は、高い信頼性と特定の重量バランスを必要とする各種アプリケーションにおいて、その魅力を発揮します。
C3604真鍮の強度と耐食性
耐食性の重要性
高強度C3604真鍮は、その引張強度と比重において特筆すべき物理的性質を有しています。この合金は、製造工程が容易でありながらも高い機械的強度を誇ります。まず、引張強度が特に重視されるのは、製品の耐久性と信頼性を高めるためです。C3604真鍮はこの点で優れた性能を示し、様々な産業で部品や装置の材料として重宝されています。例えば、自動車の精密部品や水道の蛇口などに利用されており、これらの製品が強度を必要とする場面では、C3604の高い引張強度が大きなアドバンテージとなります。また、比重に関しても、C3604は適度な重量感を持ち、安定した設置や動作が期待でき、振動吸収などの特性にも寄与しています。このようにC3604真鍮は、引張強度と比重をバランス良く兼ね備えており、その結果、幅広い用途で高い評価を受けているのです。
C3604真鍮の耐食性能
C3604真鍮は、その優れた物理的性質から幅広い産業で利用されています。特に引張強度と比重のバランスが注目されているのです。引張強度とは、材料が破断するまでの強さを示し、C3604真鍮は一般的な真鍮に比べて高強度を持っています。このため、耐久性が求められる部品や構造材に適しており、自動車や電子機器の精密部品に用いられることが多いです。また、比重に関しては、C3604真鍮は他の金属に比べて軽量で、その結果、材料の経済性が向上します。
これらの特性から、C3604真鍮は高い強度を維持しつつ、マシニング加工が容易であるため、多様な形状の部品製造に最適です。例えば、高負荷を受けるギアや接続部品に利用されることがあります。耐食性にも優れているため、機械の長期間の使用に耐えることができます。その結果、製品の寿命を延ばすことが可能になるのです。
以上の理由から、C3604真鍮は引張強度が高く、比重が適度で加工性に優れた物質として評価されており、工業製品にとっての魅力的な選択肢と言えるでしょう。
耐食性向上のための工夫
高強度C3604真鍮はその引張強度と適度な比重によって多くの分野で活用されています。この真鍮合金は、耐食性に優れており機械部品や電気部品に適しております。引張強度が高いとは、材料が引っ張られたときにどれだけの強さで抵抗できるかを示す指標です。C3604は、特に高い引張強度を持っているため、強度が要求される部品や構造物に使用されます。例えば、自動車のエンジン部品や建築資材などがあります。一方で、比重が重くなりすぎないため、携帯性にも優れているという利点もあります。これにより、携帯電話やカメラの小型部品などの精密機器にも採用されているのです。最終的に、これらの物理的性質が組み合わさって、C3604真鍮は機能性と実用性を兼ね備えた、非常に魅力的な材料であると結論付けられます。
C3604真鍮の物理的性質と応用
熱伝導性と電気伝導性
C3604真鍮はその卓越した引張強度と適度な比重で知られ、工業用途における魅力的な材料です。その物理的性質は、機械部品や電子部品の製造において、信頼性の高い性能を提供します。例えば、真鍮は引張強度が370~410N/mm²と高く、加工性に優れるため、精密な部品制作に適しています。また、比重は約8.4と、金属の中でも比較的軽量でありながら強度を保持できるため、航空宇宙や自動車産業での利用が見られます。このように、C3604真鍮はその物理的性質を活かして広範な産業分野における需要が高まっており、引張強度と比重のバランスが求められる場面で特にその真価を発揮する素材であると言えるでしょう。
磁性と反磁性
C3604真鍮は、その優れた物理的性質のため、工業分野で広く利用されています。特に、引張強度と比重のバランスが、この材料を選択する際の大きな魅力となっています。C3604真鍮の引張強度は一般的な真鍮に比べて高く、機械部品や電子部品の製造において信頼性の高い選択肢として考えられています。また、比重が高いため、小さなサイズでも重量を持たせることが可能であり、精密なバランスが求められる部品にも適しています。
たとえば、時計の精密部品や楽器のバルブなど、耐久性と精度が要求される製品にC3604真鍮はしばしば使用されます。その結果、C3604は高強度ながら加工が容易であるため、多岐にわたる産業での需要が高まっているのです。
最終的に、C3604真鍮は引張強度と比重の優れた組み合わせにより、物理的性質が要求される多種多様なアプリケーションにおいて、価値の高い材料としてその地位を確立しています。高い信頼性と幅広い応用が、C3604真鍮の魅力を決定づける要因なのです。
物理的性質に基づく応用例
高強度C3604真鍮はその抜群の物理的性質により、幅広い産業で信頼されています。特に、その引張強度と比重はC3604真鍮が工業部品や建築材料に適していることを示しています。引張強度が高いということは、材料が大きな力に耐えることができ、耐久性のある製品作りに不可欠です。一方、比重は材料がどの程度の重さであるかを示すため、軽量かつ強度が必要な用途に適しています。
例えば、精密機械の部品や楽器の吹き口に使用されることが多く、その加工性と耐食性も工業分野で高く評価されています。また、C3604真鍮は、家庭用の水栓金具や配管部品などの建材としても広く用いられ、その耐久性と維持管理の容易さから、長期にわたり多くの家庭で利用され続けています。
こうしたC3604真鍮の引張強度と比重のバランスがとれた物理的性質は、その多用途性をさらに高めています。製品の性能を左右する重要な指標として、これらの特性は今後も多くの産業で価値を認められるでしょう。
C3604真鍮の未来
技術開発の動向
高強度C3604真鍮は、その優れた物理的性質から様々な工業製品に利用されています。特に引張強度と比重のバランスが魅力となっており、これにより耐久性と加工性に優れた材料として認識されています。例えば、精密機器の部品や自動車の継手に使用されることが多いです。このC3604真鍮は、引張強度が360〜440MPaと非常に高く、しかも比重は8.5程度と比較的軽量であるため、重量を抑えつつも強度が要求される部品に理想的です。さらに、優れた耐食性もこの材料の強みの一つであり、長期にわたる使用でも品質が落ちにくいという利点があります。このような理由から、C3604真鍮は幅広い分野でその利点を活かされており、今後もその需要は続くと考えられます。高強度かつ軽量、そして耐食性に優れるC3604真鍮は、まさに工業製品にとっての強力な味方と言えるでしょう。
産業界での新しい応用
高強度C3604真鍮は、その卓越した引張強度と適度な比重により、産業界で新たな応用を広げています。この物質は、耐食性や加工性に優れ、電気部品から水道の配管に至るまで幅広い用途に利用されています。C3604真鍮の引張強度は通常の真鍮に比べて高く、その強度は約370~410 MPaとされており、高度な強度を求められる部品製造に適しています。また、比重は約8.4~8.7の範囲で、金属としては重過ぎず、様々な製品の質量管理にも適しています。例えば、高精度を要する機械部品や耐久性が必要な建築金物に使用されることで、その性能を発揮します。このように、C3604真鍮の物理的性質は特定の工業製品の品質向上に寄与し、それが産業界における新しい応用へと繋がっているのです。
持続可能性と真鍮の役割
高強度C3604真鍮は、その優れた物理的性質により、多くの工業分野で注目されています。特に、この真鍮の引張強度と比重は、その使用範囲を広げる重要な要素です。C3604真鍮の引張強度は、耐久性の高い設計に不可欠で、産業機械や自動車部品などの要求が厳しい環境下でも信頼性を保てるため、広く利用されています。また、この真鍮の比重は約8.5g/cm³で、この値は、部品の質量が重要な要素となる精密機器や音響機器の設計において好都合です。例えば、高品質な楽器の金属部分にC3604真鍮が選ばれることが多く、その特性が、楽器のクリアな音色を生み出すうえで役立っています。結論として、C3604真鍮は引張強度と比重のバランスが優れており、それが多岐にわたる産業での採用につながっているのです。
まとめ
高強度C3604真鍮は、その引張強度と比重の点で注目されています。その物理的性質は優れており、様々な産業で幅広く利用されています。これは、機械部品や建築材料など様々な分野での需要が高い理由の一つです。高い引張強度と比重を持つC3604真鍮は、その信頼性と耐久性によって多くの産業で重宝されています。
C2801銅合金の機械的性質完全ガイド
C2801銅合金とは
C2801銅合金は、主に銅と亜鉛を基にした合金で、一般的には「真鍮」の一種として分類されます。この合金は、高い導電性、良好な加工性、耐食性を有しており、さまざまな産業分野で利用されています。C2801銅合金の概要
C2801銅合金は、主に銅に亜鉛を加えた合金で、その特性は亜鉛の含有量によって異なります。通常、亜鉛の含有量が20~25%程度の範囲で、この割合により合金の強度や耐腐食性が向上します。C2801は、比較的柔軟で加工しやすく、電気的・熱的な導電性が高いため、機械的強度が要求される部品や電子機器にも広く使用されています。真鍮とは:C2801の位置づけ
真鍮は、銅と亜鉛の合金を指し、その亜鉛の含有量によって特性が大きく変化します。C2801銅合金はその中でも、亜鉛の含有量が高めで、強度や耐摩耗性に優れた真鍮の一種です。C2801は、亜鉛含有率が20~25%で、一般的に「黄銅」とも呼ばれるタイプの合金に位置づけられます。この合金は、他の真鍮合金と比較して、強度が高く、機械加工性も優れているため、精密部品や構造部品に使用されることが多いです。C2801銅合金の産業での利用
C2801銅合金は、その特性によりさまざまな産業で利用されています。以下のような用途が代表的です。- 電子機器: 高い導電性を活かして、配線や接続部品などに使用されます。
- 自動車産業: 高い耐摩耗性を生かして、機械部品や精密部品に利用されることがあります。
- 建築: 耐食性が良いため、建築用の金属部品や装飾部品にも使われます。
- 産業機械: 金型やその他の機械部品として使用され、耐摩耗性や強度が求められる部品に広く使用されています。
C2801銅合金の化学成分
C2801銅合金は、銅と亜鉛を主成分とした合金で、その他の元素も微量に含まれています。これらの化学成分によって、C2801は優れた機械的特性や耐腐食性、加工性を持つ合金となっています。C2801の主要成分
C2801銅合金の主成分は以下の通りです:- 銅 (Cu): 約75%~80%
- 亜鉛 (Zn): 約20%~25%
- その他の元素: 微量で含まれることが多い(例えば、鉛、鉄、錫など)
合金元素と特性の関係
C2801銅合金の特性は、含有されている各元素の比率によって大きく変わります。- 銅 (Cu): 銅の比率が高いことで、C2801銅合金は優れた導電性と耐食性を示します。これは、電気機器や配線材料に適した特性となります。
- 亜鉛 (Zn): 亜鉛の添加により、合金は強度が増し、耐摩耗性や耐久性が向上します。これにより、C2801は機械的な負荷を受ける部品にも適しています。
- その他の元素: 微量の鉄(Fe)や鉛(Pb)などが含まれる場合、強度、加工性、潤滑性が向上します。これにより、機械加工や精密部品の製造にも適しています。
C2801銅合金の機械的性質
C2801銅合金は、その高い機械的特性から、多様な用途で使用されている合金です。以下では、C2801銅合金の強度、硬度、伸び、応力-ひずみ曲線、疲労強度、耐久性、衝撃特性について詳述します。強度と硬度
C2801銅合金は、比較的高い強度を持ちながらも、良好な加工性を備えています。具体的には、亜鉛の添加により、合金の強度が向上します。この合金の引張強さは、約 500 MPa から 650 MPa の範囲です。硬度については、ロックウェル硬さ(HRB)で約 60~90 となり、一般的な真鍮合金と同等の硬さを持っています。これにより、耐摩耗性が向上し、精密部品や金型材料にも適用可能です。伸びと応力-ひずみ曲線
C2801銅合金は、良好な延性を持ち、亜鉛の含有率によってその伸びが変わります。典型的な伸び率は 25%~40%程度であり、加工が容易で、延性を重視する用途に適しています。応力-ひずみ曲線においては、弾性範囲が広く、初期のひずみが弾性的に戻るため、衝撃や振動の多い環境下でも耐性があります。また、合金が塑性変形に入ると、徐々に応力が増加する特性が見られます。疲労強度と耐久性
C2801銅合金は、疲労強度が高く、繰り返し荷重に対する耐性を持っています。疲労限度は約 150 MPa ~ 200 MPa の範囲で、長期間使用される機械部品においても高い耐久性を発揮します。これにより、振動やサイクル荷重がかかる環境下でも使用可能です。また、耐久性が高いため、構造的に安定した部品や部材に多く用いられます。衝撃特性
C2801銅合金は、衝撃に対しても一定の耐性を持ちますが、鋼のように非常に高い衝撃強度を持つわけではありません。衝撃試験では、特に高温や急冷時に強度が低下することがあるため、過度の衝撃荷重を受ける用途では、適切な設計や熱処理が求められます。しかし、通常の使用環境においては、十分な衝撃吸収能力を発揮します。 C2801銅合金はこれらの機械的特性により、様々な産業分野で使用され、特に機械加工や精密部品、さらには電子機器や自動車産業において広く採用されています。真鍮C2801の加工性
真鍮C2801は、その優れた加工性から、さまざまな製造工程で利用される合金です。加工時に求められる精度や品質を確保するためには、C2801の特性を理解し、適切な方法を選択することが重要です。以下では、C2801の加工性に影響を与える因子や、特に切削加工、曲げ加工、成形性に焦点を当てて説明します。加工性に影響を与える因子
C2801の加工性にはいくつかの要因が影響を与えます。主な要因としては、以下の点が挙げられます:- 合金の成分:C2801の亜鉛含有量が、切削性や成形性に大きく影響します。亜鉛の含有比率が高いほど、加工がしやすくなりますが、過剰な亜鉛は脆性を高めることがあり、注意が必要です。
- 硬度:C2801の硬度は、加工の難易度に影響を与えます。硬度が高いと、工具の摩耗が早くなるため、適切な切削条件や冷却剤を使用することが求められます。
- 温度管理:加工時の温度が高くなると、金属が柔らかくなり、加工性が向上します。適切な温度管理が、精度の向上に繋がります。
C2801の切削加工性
C2801は比較的良好な切削加工性を有し、旋盤やフライス盤などを使用した切削が容易に行えます。特に中程度の切削速度で安定した加工が可能で、工具の寿命を延ばしつつ、品質の高い仕上がりが得られます。以下の点に注意することで、切削性を最適化できます:- 切削速度の調整:高速での切削は、工具摩耗の原因となることがあります。中程度の速度での切削が推奨されます。
- 冷却剤の使用:冷却剤を使用することで、加工中の温度を管理し、工具の摩耗を減らすとともに、仕上がりの精度を向上させることができます。
- 適切な工具の選定:C2801の切削には、炭化物工具や高速度鋼工具が一般的に使用されます。
曲げ加工と成形性
C2801は、良好な曲げ加工性を持ち、曲げ角度や圧力を調整することで、精密な成形が可能です。曲げ加工を行う際には、以下の点に注意が必要です:- 曲げ半径の調整:C2801の曲げ加工を行う際、過度の曲げ半径が小さいと、亀裂が生じることがあります。適切な半径を選定することが重要です。
- 温度管理:冷間加工と温間加工のどちらも可能ですが、高温での加工はより容易で、成形性を向上させます。
加工時の注意点
C2801の加工時に注意すべき点として、以下があります:- 工具の摩耗:C2801は比較的硬度が高いため、切削工具が摩耗しやすいです。工具の選定や切削条件の調整を行い、摩耗を最小限に抑えることが重要です。
- 亀裂の防止:過度の応力が加わると、亀裂が生じる可能性があるため、加工中の圧力や温度の調整が求められます。
- 表面処理:C2801は表面処理を行うことで、腐食耐性を高めることができます。加工後に表面処理を施すことで、耐久性や美観が向上します。
C2801銅合金の熱処理と効果
C2801銅合金は、その優れた機械的特性と加工性から、広範な産業で使用されています。熱処理を適切に行うことにより、銅合金の機械的性質を向上させることができます。以下では、C2801銅合金における熱処理の種類とその目的、熱処理が機械的性質に与える影響、そして実践的な熱処理プロセスについて詳述します。熱処理の種類と目的
C2801銅合金の熱処理には、主に以下の種類があります:- アニーリング(焼きなまし):アニーリングは、材料を加熱してからゆっくり冷却する熱処理です。このプロセスにより、材料内の内部応力を除去し、加工性を改善します。C2801の場合、特に加工前にアニーリングを施すことが一般的です。
- 硬化処理(焼き入れ):C2801は通常、焼き入れによって硬度を高めることができます。焼き入れでは、合金を高温で加熱し、その後急冷することで強度を向上させます。
- 焼き戻し:焼き戻しは、焼き入れ後に材料を再度加熱し、硬度や脆性を調整するプロセスです。C2801では、焼き戻しを行うことで、過度に硬くなった合金の脆性を抑制し、耐久性を向上させます。
熱処理が機械的性質に与える影響
C2801銅合金の熱処理は、主に以下の機械的性質に影響を与えます:- 硬度:アニーリングや焼き入れを行うことで、C2801銅合金の硬度が向上します。硬度の向上は、摩耗や引っかき傷への耐性を高めるため、特に機械部品や耐摩耗性が求められる製品に適しています。
- 引張強度:焼き入れ処理により、引張強度が高まり、製品がより高負荷に耐えることが可能になります。これにより、構造部材や機械部品としての強度が確保されます。
- 伸び:アニーリング後、銅合金はより良好な伸び性能を発揮し、加工性が向上します。柔軟性が高くなり、精密加工や成形の際に有利となります。
- 靭性:焼き戻し処理を行うことで、C2801の靭性が向上し、脆性を低減することができます。これにより、衝撃荷重や急激な温度変化に対する耐性が強化されます。
実践的な熱処理プロセス
C2801銅合金の熱処理プロセスを実践する際の基本的な手順は以下の通りです:- アニーリング(焼きなまし)
- 温度設定:C2801を約300~600°Cの温度範囲で加熱します。
- 保持時間:一定時間その温度を維持し、内部応力を除去します。
- 冷却方法:空冷または炉冷で徐々に冷却します。
- 焼き入れ(硬化処理)
- 加熱:C2801を約800~900°Cの高温に加熱します。
- 急冷:急速に冷却するため、冷却媒体(油や水)を使用します。
- 確認:硬度が必要な範囲に達したか確認します。
- 焼き戻し(軟化処理)
- 温度設定:焼き入れ後、200~400°Cで加熱します。
- 保持時間:焼き入れで硬化した部分の脆性を減少させるため、一定時間その温度で保持します。
- 冷却方法:空冷または炉冷で冷却します。
真鍮C2801の材料選定
真鍮C2801は、その優れた機械的特性と加工性から、多くの産業で利用される材料です。材料選定の際には、特定の用途や要求に合わせた基準や考慮点が重要です。ここでは、C2801の材料選定基準、考慮点、さらに類似材料との比較について説明します。材料選定の基準と考慮点
C2801銅合金の材料選定にあたり、以下の基準や考慮点が重要です:- 機械的特性 C2801は高い強度と優れた耐摩耗性を持っており、特に摩擦の多い環境や高負荷の機械部品に適しています。選定時には、強度や硬度の要件を満たしているかを確認する必要があります。
- 加工性 C2801は、切削加工、曲げ加工、圧延加工などの加工が容易であり、高い加工性を誇ります。複雑な形状や精密な加工が求められる場合、この特性は重要です。
- 耐腐食性 C2801は優れた耐腐食性を持っており、特に湿気や化学薬品に対する耐性が求められる場合に選ばれます。材料選定時には、使用環境を考慮した耐腐食性が必要です。
- 価格と経済性 C2801は比較的コストパフォーマンスが良く、コスト効率の良い材料選定が求められる場合に適しています。他の高価な合金と比較して、性能とコストのバランスが良い点が特徴です。
- 重量と比重 C2801は銅合金であり、軽量な材料が必要な場合に有利です。比重を考慮し、他の金属と比較して最適な材料を選定することが重要です。
類似材料との比較
C2801銅合金は他の真鍮や銅合金と比較されることが多いですが、以下のような類似材料との比較が行われます:- C3600(自由切削真鍮) C3600はC2801と比較して、さらに優れた切削性を持ちますが、強度や耐摩耗性はC2801に劣ることがあります。切削性を重視する場合はC3600を選定することがありますが、強度や耐久性を重視する場合にはC2801が適しています。
- C2700(黄銅) C2700は一般的に強度が高く、耐食性にも優れていますが、C2801よりもやや硬度が低いため、摩耗に強い部品にはC2801が有利です。また、C2700はC2801に比べて若干の加工性の差があり、特に精密な加工が要求される場合にはC2801が選ばれやすいです。
- C2200(デザイン用銅合金) C2200は耐食性に優れていますが、強度や耐摩耗性ではC2801に劣ります。装飾用途などで使用されることが多いため、機械的性能が重視される場合にはC2801の方が適しています。
C2801銅合金の耐食性と対策
C2801銅合金は、優れた耐食性を持つことで知られていますが、特定の腐食環境ではその耐性に限界があるため、環境に応じた対策が必要です。ここでは、C2801の耐食性、腐食環境が与える影響、および耐食性を高めるための対策について詳しく解説します。C2801の耐食性能
C2801銅合金は、一般的に良好な耐食性を持ち、湿気や海水、空気中の酸素に対して強い耐性があります。特に、以下の特徴を持っています:- 大気中の耐食性 大気中で使用する場合、C2801は酸化しにくく、錆びにくい特性を持っています。銅とその合金は、表面に保護膜(酸化膜)を形成するため、腐食の進行を抑制します。
- 海水や湿気に対する耐性 C2801は海水や湿気の多い環境でも耐食性を発揮します。特に、塩分や湿度が高い場所での利用が可能ですが、極端に長期間使用される場合や、特殊な化学物質が含まれる環境では追加の対策が求められることがあります。
- 酸やアルカリ性環境への耐性 C2801は弱酸性や弱アルカリ性の環境においても耐久性を示しますが、強酸や強アルカリ環境下では耐食性が低下することがあります。そのため、強い化学薬品が関与する環境での使用には慎重な評価が必要です。
腐食環境とその影響
C2801銅合金が直面する腐食環境には、以下のような種類があります。それぞれの環境によって腐食の進行度や発生メカニズムが異なります。- 海水環境 海水は、塩分が高いため、特に腐食に対する影響が大きいです。海水中では、C2801の表面に塩化銅や酸化銅が生成され、これが腐食の原因となります。しかし、C2801は比較的耐海水性が高い銅合金です。
- 酸性環境 強酸性の環境(例えば硫酸、塩酸など)では、C2801の耐食性が低下します。酸により合金成分が溶出しやすく、耐久性が損なわれる恐れがあります。
- アルカリ性環境 アルカリ性が強い環境(例えば水酸化ナトリウムなど)でも、C2801は耐性が低く、腐食が進行する可能性があります。アルカリ性の影響で銅合金表面が腐食し、強度や耐久性が損なわれます。
- 高温環境 高温環境では、C2801銅合金は酸化膜の形成が進むため、耐食性が向上することもありますが、過度の高温や長時間の高温曝露は、材料に悪影響を及ぼす可能性があるため注意が必要です。
耐食性を高めるための対策
C2801銅合金の耐食性をさらに高めるために、以下の対策を講じることができます:- 表面処理 C2801の表面をコーティングすることにより、耐食性を向上させることが可能です。例えば、クロム酸化処理や亜鉛メッキなどを施すことで、腐食に対する抵抗力を高めることができます。
- 合金元素の調整 C2801の合金成分に微量の他の金属(例えば、リンやスズ)を加えることで、耐食性が向上する場合があります。これにより、特定の腐食環境での耐久性を改善することができます。
- 適切な保護膜の維持 C2801は表面に酸化膜を形成することで耐食性を持っています。この酸化膜を損なわないように使用条件を管理し、例えば高温や強い酸性、アルカリ性環境から保護することが重要です。
- 定期的なメンテナンス 定期的な清掃や点検を行うことで、表面の汚れや腐食を早期に発見し、対策を講じることができます。これにより、長期間にわたって高い耐食性を保つことができます。
真鍮C2801の溶接と接合
真鍮C2801は、一般的に溶接性に優れていますが、特定の溶接方法を選ぶことが重要です。C2801の溶接特性、適切な溶接方法、接合強度の確保、そして品質管理について詳しく解説します。C2801の溶接特性
C2801銅合金は、優れた導電性と耐食性を持ち、溶接性も良好ですが、いくつかの注意点があります:- 熱伝導性が高い C2801は熱伝導性が高いため、溶接時に高い熱エネルギーが必要になります。これにより、熱影響を受けやすく、溶接部の変形や応力が発生しやすくなるため、溶接時の温度管理が重要です。
- 酸化膜の問題 C2801の表面には酸化膜が形成されることがあり、これが溶接において問題を引き起こす場合があります。酸化膜は溶接ビードの付着を妨げ、接合強度が低下する恐れがあります。酸化膜の除去が重要です。
- 熱処理後の変化 溶接後に熱処理を行う場合、C2801は熱処理で特性が変化することがあります。適切な熱処理を行わないと、溶接部の強度や耐食性が低下する可能性があるため、注意が必要です。
溶接方法とその選択
C2801の溶接にはいくつかの方法がありますが、最も適した方法は以下の通りです:- TIG溶接(Tungsten Inert Gas溶接) C2801銅合金には、TIG溶接が最も適しています。TIG溶接は、精密で高品質な溶接が可能で、酸化膜の影響を最小限に抑えることができます。溶接中に不純物が少なく、溶接ビードが美しく仕上がります。
- MIG溶接(Metal Inert Gas溶接) MIG溶接もC2801に使用可能ですが、TIG溶接ほど精密さは求められません。MIG溶接では高速な溶接が可能で、大きな構造物の溶接には有効ですが、溶接部のクリーンさに注意が必要です。
- ガス溶接 ガス溶接も可能ですが、C2801のような銅合金では、比較的精度が低くなるため、高い強度と品質が要求される接合には避けるべきです。ただし、小規模な修理や細かい作業には適しています。
- スポット溶接 薄い板を接合する場合、スポット溶接が効果的です。C2801の高い熱伝導性を活かして、局所的な加熱で溶接を行います。スポット溶接は、急速に作業が進むため、効率的に接合が可能です。
接合強度と品質管理
C2801銅合金の溶接接合部では、以下の点を考慮して接合強度と品質を管理する必要があります:- 溶接部の強度確保 溶接後、接合部の強度を確保するためには、適切な溶接パラメータ(電流、電圧、速度など)を設定する必要があります。これにより、均一な溶融が得られ、強度が向上します。また、溶接後の冷却速度も重要で、急激な冷却はひび割れを引き起こす可能性があるため、温度管理が重要です。
- 品質検査 溶接後の接合部には、目視検査、超音波検査、X線検査などを行い、亀裂や空洞などの欠陥を確認します。これらの検査により、製品が要求される強度基準を満たしているかを確認できます。
- 溶接部の仕上げ 溶接後は、溶接ビードの研磨や酸化膜の除去を行い、表面を平滑に保つことが必要です。これにより、後続の加工や使用時における耐食性や機械的特性を維持します。
- 熱処理 溶接後には、応力を除去し、強度を高めるための適切な熱処理が推奨されます。焼きなましなどの熱処理を施すことで、溶接部の残留応力を軽減し、耐久性を向上させることができます。
まとめ
C2801銅合金は、その機械的性質や化学成分について詳細に解説しています。この合金は機械的な強度が高く、耐食性にも優れています。そのため、様々な産業分野で幅広く使用されています。また、その成分には銅と亜鉛が主成分となっており、これによって耐久性や加工性が向上しています。C2801銅合金は、機械部品や建築材料など、多岐に渡る用途に使用されています。「C2680材料の加工時に気をつけたい注意点とその対策」
真鍮C2680の基礎知識
真鍮C2680の材質と一般的な用途
真鍮C2680は、銅を主成分とし、亜鉛を加えた合金で、一般的に「青銅」としても知られる材料です。この素材は、良好な加工性、耐食性、そして高い機械的特性を持っているため、様々な産業で利用されています。 一般的な用途には、以下のようなものがあります:- 精密機器: 銅合金としての特性から、精密機器や電子機器の部品に使われます。
- 自動車部品: 耐摩耗性と強度を生かして、自動車部品にも広く使用されます。
- 金具: 装飾性が高く、耐食性も優れているため、金具や装飾的な部品に多く用いられます。
C2680の化学的成分と物理的性質
真鍮C2680の主な化学成分は、銅(Cu)を約60%から70%、亜鉛(Zn)を約30%から40%含んでおり、必要に応じて微量の他の元素が加えられることもあります。この合金は、良好な耐食性と共に、優れた可鍛性、鋳造性、機械的性質を有しています。 主な化学成分:- 銅 (Cu): 60〜70%
- 亜鉛 (Zn): 30〜40%
- 微量の鉛 (Pb) や 鉄 (Fe) が含まれることもあります。
- 密度: 約 8.4 g/cm³
- 引張強度: 約 400 MPa
- 硬度: 約 100〜150 HB(ブリネル硬度)
他の真鍮材料との比較
真鍮C2680は、他の真鍮合金(例えばC3600やC5100)と比べて、特に耐食性と機械的性質において優れたバランスを持っています。- C3600: より高い可加工性と切削性が特徴で、主に精密機器の部品に使われることが多いですが、耐食性においてはC2680に劣ります。
- C5100: 高い弾性率と強度を有し、耐摩耗性にも優れるため、機械的なストレスがかかる用途に向いていますが、C2680ほどの耐食性はありません。
真鍮C2680の加工方法の概要
切削加工とは
切削加工とは、素材から不要な部分を取り除くことによって目的の形状に仕上げる加工方法です。真鍮C2680は、銅と亜鉛を主成分とする合金であり、その性質により切削加工がしやすく、精密な加工が可能です。この特性により、複雑な形状を作り出すことができます。 切削加工には、さまざまな技術が用いられますが、真鍮C2680の場合、以下の方法が一般的です:- 旋盤加工: 円筒状の形状を切削するための基本的な加工方法で、真鍮C2680のような金属でも広く使用されます。
- フライス加工: 平面や溝を削る加工法で、複雑な形状の部品にも対応可能です。
- ドリル加工: 穴を開けるための方法で、精密な穴開けが求められる場合に適しています。
加工方法の種類と特徴
真鍮C2680の加工方法にはいくつかの選択肢があり、それぞれに特徴があります。- 切削加工:
- 真鍮C2680は比較的柔らかく、切削性に優れるため、精密な切削加工が可能です。
- 切削時の工具摩耗が少なく、表面仕上がりも良好です。
- 圧延加工:
- 材料を圧力を加えて延ばす方法で、特に板材や棒材の生産に使われます。真鍮C2680は延性が良いため、圧延加工にも適しています。
- 鍛造加工:
- 加熱した素材をハンマーやプレスで加工する方法で、高い強度を得られます。真鍮C2680は比較的容易に鍛造が可能です。
- 鋳造加工:
- 溶かした金属を型に流し込んで成形する方法で、大きな部品や複雑な形状の部品作成に使用されます。真鍮C2680の良好な鋳造性を活かすことができます。
真鍮C2680の適切な加工環境
真鍮C2680の加工において重要なのは、適切な加工環境を整えることです。以下の点に留意することが望まれます:- 切削条件:
- 切削速度や送り速度は適切に設定することが重要です。真鍮C2680は比較的柔らかいため、切削速度を速く設定しすぎると、切削工具の摩耗が早くなります。
- 潤滑:
- 切削時には潤滑油や冷却剤を使用して、加工温度の上昇を防ぎ、工具の摩耗を抑えることが大切です。特に高速切削の場合、冷却材の使用が推奨されます。
- 工具の選定:
- 真鍮C2680は硬度が低いため、一般的な金属用工具で問題なく加工できますが、表面仕上げの精度を求める場合は、特に高精度な切削工具を使用することが効果的です。
- 加工後の処理:
- 加工後には、表面の仕上げを行うことで製品の精度と外観を向上させます。表面処理や洗浄が必要な場合もあります。
C2680の切削性と加工時の注意点
C2680の切削性に影響を与える要因
C2680(真鍮)の切削性は、その化学成分と物理的特性に基づいて異なります。以下の要因が切削性に大きく影響を与えます:- 銅と亜鉛の比率:
- C2680は主に銅と亜鉛を基にした合金です。この比率が切削性に影響を与えます。亜鉛含有量が高い場合、切削時に比較的柔らかく、切削がしやすくなります。一方、亜鉛が少ないと硬度が上がり、切削が難しくなる可能性があります。
- 硬度:
- 真鍮C2680は比較的低い硬度を持つため、切削性は優れています。ただし、硬度が高すぎる場合や熱処理後に硬度が増す場合には、切削性が悪化することがあります。
- 表面仕上げ:
- 表面が滑らかであると切削がスムーズになりますが、表面が粗い場合は工具に負担がかかり、切削性能が低下します。
- 温度と潤滑:
- 高温下での切削や不十分な潤滑は切削性に悪影響を与える可能性があります。適切な冷却と潤滑が切削性を向上させます。
切削工具の選定と保守
切削工具の選定は、C2680の切削性を最大限に活用するために重要です。以下のポイントに留意して選定します:- 工具材質の選定:
- C2680のような真鍮合金には、高速鋼(HSS)や硬質合金(カーバイド)工具が適しています。硬質合金は高い耐摩耗性を持っており、高速切削や高精度加工に有効です。
- 工具の形状:
- 切削工具の形状(刃先角度やコーナー半径)を適切に選定することで、切削中の振動や熱を減少させ、加工精度を向上させます。例えば、細かい加工には細い工具を使用し、太い工具は大きな切削力を要求します。
- 工具の保守と管理:
- 切削工具は定期的に点検し、摩耗や欠損が見られたら早急に交換することが重要です。摩耗した工具を使用すると、切削精度や表面仕上がりが悪化するため、品質管理が求められます。
加工速度とフィード率の最適化
C2680の切削性を最大化するためには、適切な加工速度(回転数)とフィード率(送り速度)の設定が必要です。これらを最適化するためのポイントは以下の通りです:- 加工速度(回転数)の設定:
- 加工速度は素材の硬さや工具の材質に合わせて設定する必要があります。C2680は比較的柔らかいため、一般的には高速回転が適していますが、回転数が高すぎると工具の摩耗が早くなるため、バランスが重要です。
- フィード率(送り速度):
- フィード率は加工品の表面品質に影響を与える要因です。フィード率を適切に設定することで、切削効率が向上し、切削熱の発生を抑制できます。一般的に、低いフィード率はより精密な仕上がりを実現しますが、加工速度を遅くするため効率が低下します。
- 最適化の調整:
- 最適な加工速度とフィード率は、試験的に調整することが推奨されます。例えば、切削温度や加工後の表面仕上がりを確認しながら、設定を微調整することが重要です。過度な加工作業や不適切な設定は、熱や摩耗を引き起こす可能性があるため注意が必要です。
真鍮C2680切削加工の品質向上策
切削液の選択と管理
切削液は加工精度と工具寿命に大きな影響を与えるため、適切な選定と管理が重要です。- 切削液の役割:
- 切削液は、主に冷却、潤滑、洗浄の役割を果たします。真鍮C2680の切削では、適切な冷却と潤滑が摩耗を防ぎ、加工効率を向上させます。
- 高速での切削や深い切削を行う場合、冷却効果が強い切削液を選ぶことで熱の蓄積を防ぎます。
- 切削液の種類:
- 水溶性切削液(乳化液)や油性切削液がありますが、真鍮C2680には水溶性の切削液が適しています。水溶性切削液は冷却性が高く、特に熱による摩耗を防止するのに有効です。
- 油性切削液は潤滑性に優れ、摩擦が少ないため、仕上げ加工や精密加工に向いていますが、冷却性には限界があります。
- 切削液の管理:
- 切削液は定期的に交換・清掃する必要があります。長期間使用することで切削液が汚れ、効率が低下するため、定期的なメンテナンスが求められます。
- pH値や温度を適切に管理し、異常を早期に発見することで、加工精度を維持します。
チップ形状と切削角度の調整
チップ形状や切削角度は、加工精度や表面品質を向上させるための重要な要素です。- チップ形状の選定:
- 真鍮C2680のような柔らかい金属では、切削チップの形状が大きく影響します。刃先が鋭利なものや、切れ味が良いチップを選ぶことで、スムーズな切削を実現できます。
- 具体的には、漸進的に刃先が鋭くなるチップや、トラバース角度が小さいチップが適しています。
- 切削角度の調整:
- 切削角度は、切削抵抗を最小限に抑え、効率的な切削を行うために調整が必要です。特に負荷が高い部分では、切削角度を大きくすることで、加工中の摩擦を減少させ、熱を抑制できます。
- 鋭角の切削角度を用いることで、切削中の荷重を軽減し、加工精度を向上させます。
- チップの選定基準:
- 高精度の仕上げ作業では、切削チップの材質にも注意が必要です。例えば、超硬チップやコーティングチップを使用することで、耐摩耗性を向上させ、長時間安定した加工が可能になります。
振動と熱の管理
切削時の振動や熱の管理は、加工品質に直結する重要な要素です。- 振動の抑制:
- 振動は加工精度を損なう原因となり、特に精密加工や高精度の仕上げ作業では問題となります。振動の原因は、工具の不安定な取り付け、過剰な切削負荷、機械の動作精度不足などです。
- 振動を抑えるためには、工具の取り付けを確実に行い、適切な切削条件を設定することが重要です。また、機械の剛性を高めるために、加工機の選定も慎重に行います。
- 熱の管理:
- 高速切削や大きな切削負荷がかかる場合、熱が発生しやすく、工具や材料にダメージを与える可能性があります。これを防ぐためには、十分な冷却と適切な切削液の使用が必要です。
- 熱が発生した場合、表面品質が低下し、切削精度も損なわれます。適切な切削液の選定と冷却方法の設定が重要です。
- 熱膨張の抑制:
- 高温下での加工は、材料の熱膨張を引き起こし、精度を損なう原因となります。冷却方法や加工条件を調整することで、熱膨張を最小限に抑え、安定した加工が可能になります。
真鍮C2680加工時のトラブルとその対応
切削加工で起こりやすい問題点
真鍮C2680を切削加工する際、いくつかのトラブルが発生することがあります。これらの問題は、加工精度や生産性に影響を与えるため、早期に把握し対処することが重要です。- 切削不良や表面粗さ:
- 切削中に表面が荒れたり、加工面に傷がつくことがあります。この問題は、過剰な切削負荷や不適切な工具選定が原因となることが多いです。
- 工具の摩耗:
- 長時間の使用や高負荷によって工具が摩耗し、切削性能が低下することがあります。これにより加工精度が落ち、表面仕上げが悪くなる場合があります。
- チップの詰まり:
- 切削中にチップが工具の隙間に詰まることがあります。これが原因で切削力が不安定になり、加工が停止する場合があります。
- 焼けや熱変形:
- 高速切削や過度の切削熱によって、真鍮の表面が焼けることや、部品が熱変形することがあります。これにより製品の品質が低下する可能性があります。
トラブル発生時の対処法
トラブルが発生した際には、速やかに適切な対策を講じることが重要です。- 切削不良や表面粗さの対処法:
- 切削条件の見直し: 切削速度や送り速度を調整し、適切な条件に設定します。また、工具の種類や状態を確認し、必要に応じて交換します。
- 切削液の確認: 切削液の供給量や品質を確認し、冷却・潤滑効果が十分でない場合は適切な切削液を使用します。
- 工具の摩耗に対する対処法:
- 工具の交換: 摩耗した工具を速やかに交換し、加工精度を維持します。特に精密加工が求められる場合、工具交換のタイミングを適切に管理します。
- 切削条件の再評価: 切削負荷が過度でないか確認し、切削速度や送り速度を再調整します。
- チップの詰まりの対処法:
- 工具の清掃: 切削中にチップが詰まった場合、工具を取り外し、詰まりを取り除きます。また、工具の隙間や刃先にチップが溜まらないよう、適切な切削液を使用してチップ排出を促進します。
- 切削条件の改善: 過度の送り速度や切削深さが原因の場合、条件を見直し、チップの排出をスムーズにします。
- 焼けや熱変形の対処法:
- 冷却条件の改善: 切削時に十分な冷却を行うため、切削液の供給量や冷却方法を調整します。冷却液を適切に使うことで、熱の発生を抑え、焼けや変形を防止します。
- 切削速度の調整: 切削速度が速すぎると熱が溜まりやすいため、速度を適切に調整し、熱の発生を抑制します。
予防策と定期メンテナンス
トラブルを未然に防ぐための予防策と、定期的なメンテナンスが非常に重要です。- 予防策:
- 適切な切削条件の設定: 加工の開始時に最適な切削条件を設定し、切削速度、送り速度、切削深さを適切に管理することで、問題を未然に防ぎます。
- 工具の適切な選定: 加工内容に合わせた工具の選定を行い、工具の摩耗を防ぎます。加工前に工具が適切か確認することが大切です。
- 切削液の管理: 切削液を定期的に交換し、冷却と潤滑効果を保ちます。切削液が汚れていると切削不良や摩耗の原因となります。
- 定期メンテナンス:
- 機械設備の点検: 定期的に機械の整備や点検を行い、振動や異常な音がないか確認します。機械のメンテナンスを怠ると、振動や精度低下の原因となります。
- 工具の点検と交換: 使用中の工具は定期的に点検し、摩耗や欠損があれば交換します。工具が悪化する前に交換することで、精度と品質を保ちます。
まとめ
C2680は加工時に気をつけたい注意点とその対策についてご紹介します。この材料は切削性が高いという特徴がありますが、それに加えて注意が必要です。まず、切削時には適切な刃物を使用し、十分な潤滑剤を塗布することで切削の精度を向上させることができます。また、切削時の温度管理にも注意が必要です。加工が熱を帯びると硬度が上がるため、冷却を行いながら加工を行うことが重要です。以上の点に気をつけながらC2680材料の加工を行うことで、作業効率を向上させることが可能です。工業用C2600合金の成分と耐食性に関する総合情報
真鍮C2600の基礎知識
真鍮は、銅を主成分とし、亜鉛を含む合金で、一般的には良好な機械的性質と優れた耐食性を持つため、幅広い用途に利用されています。真鍮C2600は、その中でも特に一般的に使用される銅-亜鉛合金の一種で、さまざまな産業で重要な役割を果たしています。真鍮とは:定義と一般的な特性
真鍮は、主に銅(Cu)と亜鉛(Zn)を合金化した材料で、合金の成分比率によってさまざまな種類があります。一般的に、銅の比率が高いほど耐食性が向上し、亜鉛の比率が高いほど強度や硬度が増します。真鍮は、以下のような特性を持っています:- 高い耐食性:銅が主成分であるため、空気や水分に対する耐食性が高いです。
- 優れた加工性:切削加工や成形加工が容易であり、精密な形状が作りやすいです。
- 美しい外観:金色に輝く外観から、装飾品や楽器、電気機器などでよく使用されます。
- 良好な伝導性:銅の伝導性を持ち、電気や熱の伝導性が良好です。
真鍮C2600の比重とその意義
真鍮C2600は、銅を主成分とする合金で、亜鉛を含み、特に優れた機械的性質と耐食性を持っています。比重(密度)は、一般的に8.4 g/cm³程度であり、これは鋼などの鉄系材料に比べて軽く、加工性や成形性に優れるため、様々な用途で活用されます。比重の高さは、金属の強度や耐久性に関連していますが、軽さと耐食性のバランスが良いため、特に装飾品や小型部品に適しています。C2600の材料特性:銅と黄銅の比較
真鍮C2600は、銅(Cu)と亜鉛(Zn)の合金であり、その成分比率に応じて性能が異なります。C2600は、典型的な黄銅の合金であり、銅が主成分で、亜鉛の含有量が約 60% 程度となっています。これにより、以下の特性が得られます:- 強度と硬度:黄銅C2600は、亜鉛を多く含むため、純粋な銅よりも強度や硬度が向上しています。これにより、機械的な負荷に耐える能力が高くなります。
- 耐食性:銅が主成分であるため、C2600は非常に優れた耐食性を持ち、特に水中や湿度が高い環境でも耐久性を発揮します。
- 加工性:銅よりも加工性はやや低くなりますが、それでも非常に良好であり、複雑な形状を作成するのに適しています。例えば、切削や圧延、鍛造などの加工が可能です。
- 電気伝導性:純銅に比べて伝導性は低くなりますが、電気機器の一部で使用されることもあります。
C2600の成分とその役割
真鍮C2600は、銅を主成分とし、亜鉛を加えた合金で、特に優れた機械的特性、耐食性、および加工性を持っています。この合金は、産業や日常生活のさまざまな用途で重要な役割を果たしています。C2600合金の主要成分
真鍮C2600は、主に銅(Cu)と亜鉛(Zn)から成る合金ですが、少量の他の元素も含まれることがあります。以下はC2600合金の主要成分です:- 銅(Cu):主成分であり、合金全体の約60~70%を占めます。銅は、耐食性や電気伝導性、熱伝導性を提供します。
- 亜鉛(Zn):約30~40%を占め、銅に比べて強度を高める役割を果たします。亜鉛の割合によって、真鍮の硬度や強度が増します。
- 微量の他の元素:少量の鉄(Fe)や鉛(Pb)が含まれることがあります。鉄は合金の強度をわずかに向上させ、鉛は加工性を向上させる目的で添加されます。
合金元素と性質の関係
C2600合金の特性は、主に銅と亜鉛の比率と微量成分によって決まります。以下のように、それぞれの成分が合金の性質に与える影響があります:- 銅(Cu):銅は真鍮において、耐食性や電気伝導性、熱伝導性を提供します。銅が多いほど、腐食に対する耐性が高まり、長期間にわたって安定した性能を維持できます。また、銅の成分は加工性や延性を高めるため、加工しやすいという特性も持ちます。
- 亜鉛(Zn):亜鉛は銅に強度を与え、合金の硬度を向上させます。亜鉛が増えるほど、強度や硬度が増し、摩耗に対する耐性が向上しますが、同時に延性や加工性はやや低下します。また、亜鉛が多くなることで合金はより安価になり、コストパフォーマンスが向上します。
- 微量元素(Fe、Pbなど):微量成分は、合金の特性を細かく調整する役割を果たします。鉄は合金の機械的強度をわずかに増加させ、鉛は加工性を向上させ、精密な成形を可能にします。
C2600の化学的組成と耐食性
C2600合金の耐食性は、主に銅が主成分であることに起因します。銅は自然環境での耐食性が非常に優れており、湿度の高い環境や海水中でも腐食しにくい特性を持っています。亜鉛を加えることで、合金は強度が増すとともに、耐食性も向上しますが、亜鉛が過剰になると、腐食や変色が発生する可能性があるため、適切な成分バランスが重要です。 特に、C2600合金は耐海水性や耐酸性に優れており、これらの特性により、海洋設備や水道管、装飾品などの用途に適しています。また、耐食性をさらに高めるために、表面処理やコーティングを施すことが一般的です。これにより、外観の美しさと機能性が長期間維持されます。真鍮合金C2600の耐食性
真鍮C2600は、主に銅と亜鉛から成る合金であり、その特性の中でも耐食性は特に優れています。真鍮合金の耐食性は、使用環境や合金の化学組成に大きく依存しており、さまざまな産業で広く利用されています。以下では、C2600合金の耐食性について詳しく説明します。耐食性とは:基本概念
耐食性とは、材料が腐食環境に対してどれだけ耐えられるかを示す特性です。腐食は、金属が化学反応を起こすことによって、物理的特性が劣化する現象を指します。腐食が進行すると、金属の強度が低下したり、見た目が劣化したりするため、耐食性は非常に重要な要素となります。 金属の耐食性は、その合金の成分、表面処理、そして使用される環境に密接に関連しています。特に、湿度、温度、化学薬品の存在などが耐食性に影響を与える要因です。C2600の耐食性能と応用
真鍮C2600は、主成分が銅であるため、基本的に耐食性が高いという特徴があります。銅はその化学的安定性と酸化しにくい特性により、腐食に対して非常に強い金属です。亜鉛を加えることで、合金の強度が向上する一方で、耐食性も強化されます。これにより、C2600合金は以下のような環境でも優れた耐食性能を発揮します:- 湿気の多い環境:湿気の多い地域で使用される場合でも、C2600は耐久性があり、錆びにくい特性を持っています。
- 海水環境:海水中でも使用できる耐腐食性を持ち、海洋産業や船舶の部品、装飾品に広く使用されています。
- 化学薬品に対する耐性:C2600は、一部の化学薬品に対しても耐性を持ち、特に酸性環境や塩基性環境でも耐久性があります。
環境による耐食性の違い
真鍮C2600の耐食性は、使用環境によって大きく異なります。具体的には以下のような環境条件で耐食性が変化します:- 塩水環境:海水や塩水にさらされると、ピット腐食やガルバニック腐食が進行する可能性があります。C2600は塩水に対して比較的強い耐性を示しますが、長期間使用する場合は表面処理が推奨されます。
- 乾燥環境:乾燥した環境では、C2600の耐食性は高く、腐食が進行しにくいです。しかし、極端に乾燥した環境では、酸化膜が形成され、表面が黒く変色することがあります。
- 高温環境:高温環境下では、亜鉛の成分が溶け出しやすく、耐食性が低下することがあります。特に高温多湿な環境での長期使用には注意が必要です。
銅合金の種類
銅合金は、主に銅を基にした合金であり、さまざまな金属を添加することによって、特性を調整します。銅合金は、強度や耐食性、加工性などにおいて優れた特性を持っているため、建設業、機械工業、電気工業など多岐にわたる分野で使用されています。以下に銅合金の分類と特徴、およびC2600と他の銅合金との比較を説明します。銅合金の分類と特徴
銅合金は、添加する金属によって分類されます。代表的な分類には以下のようなものがあります:- 黄銅(ブラス):
- 黄銅は、銅と亜鉛の合金であり、最も一般的な銅合金です。亜鉛の含有量によって性質が異なり、C2600などがその一例です。黄銅は加工性に優れ、耐食性も高いことから、配管、接続金具、電気機器の部品などで広く使用されます。
- 特徴:高い強度と耐食性、良好な機械的性質。
- 青銅(ブロンズ):
- 青銅は、銅とスズの合金であり、優れた耐食性と機械的性質を持っています。これにより、海洋産業や高耐食性が求められる場面で使用されます。
- 特徴:優れた耐腐食性と耐摩耗性、高強度。
- 銅-ニッケル合金:
- この合金は、銅とニッケルを主成分とし、特に耐食性に優れています。海水中でも使用可能なため、海洋産業で多く使用されます。
- 特徴:高い耐食性、特に塩水や酸性環境下での耐久性が強い。
- 銅-アルミニウム合金:
- 銅とアルミニウムの合金で、主に耐食性や耐摩耗性の向上を目的として使用されます。軽量で、耐久性が求められる部品に利用されます。
- 特徴:軽量、耐腐食性が強い。
C2600と他の銅合金との比較
C2600は、黄銅(銅と亜鉛の合金)に分類され、亜鉛含有量が26%と特徴的です。この合金は、優れた耐食性、良好な機械的性質、優れた加工性を誇り、主に機械部品や電気部品に使用されています。C2600と他の銅合金との比較を以下に示します。C2600と青銅との比較
C2600は、青銅と比較して耐食性は高いものの、青銅のように海水環境に特化した耐久性を持つわけではありません。青銅は、特に高い強度と耐摩耗性が求められる環境に最適です。青銅は主に海洋産業などで使用されますが、C2600はコスト面でも優れており、一般的な機械部品や電気部品に適しています。C2600と銅-ニッケル合金との比較
銅-ニッケル合金は、特に海水中で使用される機器や船舶部品に最適な素材ですが、C2600と比べてコストが高くなる傾向にあります。耐食性では銅-ニッケル合金が上回り、特に塩水環境に強い特性を持っています。C2600は一般的な環境で使用されることが多く、価格面での優位性があります。C2600と銅-アルミニウム合金との比較
銅-アルミニウム合金は、海水などの過酷な環境での耐食性が優れ、軽量かつ高強度という特性を持っていますが、C2600はそのような環境には最適とは言えません。C2600はコストパフォーマンスに優れ、耐食性と強度がバランス良く、日常的な使用環境に適しています。銅-アルミニウム合金は主に航空機部品や船舶部品で使用されます。真鍮C2600の加工性と利用上の注意点
C2600は、真鍮の中でも高い加工性を誇る合金であり、広範囲な産業で使用されています。この合金は、切削加工や成形加工が容易で、良好な機械的性質と耐食性を備えています。しかし、加工時に注意すべき点もあり、それらを理解し、適切な加工方法を選ぶことが重要です。以下では、C2600の加工性について、加工時の注意事項と推奨される方法を説明します。C2600の加工性について
C2600は、銅と亜鉛を主成分とする黄銅合金であり、その特性により、加工が比較的容易です。主に以下の特徴があります:- 切削性:C2600は、一般的な黄銅合金と比較して優れた切削性を持っています。これにより、高精度な部品の製造が可能です。
- 溶接性:溶接性も高く、熱処理を行わずに加工が可能です。これにより、さまざまな形状の部品を容易に製造できます。
- 引張強度:強度は十分に高いですが、加工後に適切な表面処理を行うことが推奨されます。
加工時の注意事項と推奨される方法
C2600の加工にはいくつかの注意点があります。適切な加工法を選択することで、部品の品質や生産効率を向上させることができます。主な注意点と推奨される方法を以下に示します:- 冷却液の使用:
- C2600の切削時には冷却液を使用することが推奨されます。冷却液は、切削中の温度上昇を抑えるとともに、工具の寿命を延ばす効果があります。
- 切削速度の管理:
- C2600は、適切な切削速度で加工することで、良好な仕上がりが得られます。速度が速すぎると工具の摩耗が早くなり、仕上がりが悪化する可能性があるため、慎重に設定することが重要です。
- 工具選定:
- C2600の加工には、適切な切削工具を使用することが大切です。一般的に、硬度の高い工具を選ぶことで、加工精度を保ちながら効率的に作業を進めることができます。
- 引張強度の低下に注意:
- C2600は加工性が高い一方で、加工後に引張強度が若干低下することがあります。そのため、強度が要求される部品では、必要に応じて表面処理や熱処理を行うことが推奨されます。
- 表面仕上げ:
- 加工後の表面仕上げにおいては、仕上げが粗いと、腐食や摩耗が進行しやすくなるため、適切な仕上げを行うことが重要です。研磨やメッキ処理を施すことで、耐久性を向上させることができます。
- 成形加工:
- C2600は、圧延や鍛造といった成形加工にも適しています。圧延や鍛造後の処理を行うことで、部品の耐久性を向上させることができます。
まとめ
C2600合金は、銅や亜鉛を主成分とする合金であり、その耐食性は非常に高いことで知られています。環境にさらされる場合でも、銅の耐食性によって長期間安定した性能を維持することができます。C2600合金は工業用途に広く使用されており、その成分組成と耐食性に関する知識を正しく理解することが重要です。この情報を活用することで、製品の耐久性や安定性を向上させることが可能です。真鍮C3602とC3604の違いとは?用途・特性を徹底解説
真鍮とは:基本的な理解
真鍮は、銅と亜鉛を主成分とする合金で、亜鉛の含有量によってその特性が大きく変わります。金色に輝く外観と優れた耐腐食性、加工性が特徴です。これらの特性から、真鍮は多くの産業で利用されています。真鍮の定義と一般的な用途
真鍮は、銅と亜鉛を組み合わせた合金で、その割合によって異なる種類が存在します。最も一般的な用途としては、楽器、装飾金具、電気接点部品、機械部品などが挙げられます。例えば、サックスやトランペットなどの管楽器に使われるほか、建材としては扉のハンドルや照明器具、また機械部品ではギアやバルブ、ベアリングなどが真鍮製です。これらの用途において、真鍮はその美しい金色を活かしつつ、耐久性と優れた加工性が求められます。真鍮の種類とその特性
真鍮の種類には、亜鉛含有量やその他の合金成分によってさまざまなバリエーションがあります。それぞれ異なる特性を持っており、用途に応じて選ばれます。例えば、黄銅(C2800)は最も一般的な真鍮で、亜鉛が55〜70%含まれており、加工しやすく耐腐食性に優れています。赤銅(C2200)は銅成分が多く、耐腐食性がさらに向上するため、海洋環境などでの使用に適しています。白銅(C7100)は特に強度が高く、海水環境においてもその特性を発揮します。真鍮の特徴
真鍮の主な特徴は、耐腐食性と美観にあります。亜鉛が加わることで、酸や水分に対する耐久性が向上し、長期間の使用が可能です。また、金色に輝く美しい外観を持つため、装飾用途にも非常に適しています。さらに、加工性が高く、圧延、鍛造、鋳造といった多様な加工方法に対応できる点も大きな利点です。真鍮の加工方法
真鍮はその特性から、さまざまな加工方法が適用されます。高温で圧延して薄い板状にする圧延法や、溶かして型に流し込む鋳造法が一般的です。鋳造は複雑な形状を作るのに適しており、真鍮の美しい外観を保ちつつ形状を作成できます。また、鍛造では高温で叩いて形を作るため、高い強度を持つ部品を作成することができます。真鍮は加工が容易で精密部品の製造にも向いており、高精度な機械加工にも対応できます。真鍮の加工の利点
真鍮の加工における大きな利点はその高い加工性です。柔らかく加工しやすいため、複雑な形状や精密な部品を作ることができます。さらに、美しい金色の仕上がりを保ちながら製造できるため、外観が重要な部品にも広く使用されています。快削黄銅の特徴
快削黄銅は、通常の黄銅に鉛を添加した合金で、特に機械加工において優れた性能を発揮します。鉛の添加により、切削性が大幅に向上し、高速加工が可能となります。この特性から、精密部品や大量生産において非常に重宝される材料です。快削黄銅とは
快削黄銅は、銅と亜鉛を基にした合金に、鉛を加えることで作られます。鉛の含有量が高いほど、切削性が向上し、加工がしやすくなります。一般的に、鉛の割合は1%から3%程度ですが、合金の種類によってはそれ以上の割合で添加されることもあります。鉛の存在は、工具の摩耗を軽減し、切削中の温度を低く保ちながら滑らかな表面仕上げを可能にします。快削黄銅の加工性能
快削黄銅の最大の特徴は、その優れた加工性です。鉛が添加されることで、材料の切削抵抗が減少し、工具の摩耗が抑えられるため、長時間の連続加工が可能になります。また、切削中に発生する熱を抑制し、加工中の熱膨張を最小限に抑えることができるため、非常に精密な加工が可能です。これにより、特に自動車部品や電気機器部品など、精密な加工を必要とする部品の製造に適しています。 さらに、快削黄銅は、機械加工時に得られる良好な表面仕上げも特徴です。鋳造による表面の粗さが少なく、切削によって高い精度が維持されるため、仕上がりの美しさも求められる部品に最適です。快削黄銅の加工の利点
- 優れた切削性:鉛添加により、切削中の摩擦が減り、高速で精密な加工が可能です。
- 長寿命の工具:工具の摩耗を減少させ、長期間の使用が可能となります。
- 良好な表面仕上げ:加工後の表面が滑らかで、精度が高い仕上がりになります。
- 高精度な加工:熱膨張を抑え、精密な寸法の部品を製造できます。
真鍮C3602の特徴
C3602は、真鍮合金の一種で、特に高い加工性と耐腐食性を誇る材料です。亜鉛を主成分としており、比較的高い強度と良好な導電性を兼ね備えています。このため、C3602は機械部品や電気機器の部品など、幅広い用途に利用されています。C3602の化学的組成
C3602の主な化学的組成は以下の通りです:- 銅 (Cu):約 60〜63%
- 亜鉛 (Zn):約 35〜37%
- 鉛 (Pb):約 2〜3%
- その他:微量の鉄 (Fe)、アルミニウム (Al) などが含まれることもあります。
C3602の物理的特性
C3602は、金属として非常に優れた特性を持っています。以下はその主な物理的特性です:- 比重:8.4〜8.7 g/cm³
- 引張強度:約 500 MPa
- 伸び(延性):15%(最小)
- 硬度:約 90〜110 HRB(ブリネル硬度)
- 導電率:良好な導電性を持ち、電気機器にも適しています。
C3602の物理的特性の利点
- 高い引張強度と延性により、強度と柔軟性を兼ね備えた部品が作成できます。
- 優れた耐腐食性により、屋外や湿気の多い環境でも耐久性が高いです。
- 良好な導電性があり、電気機器にも適用可能です。
C3602の加工性能
C3602は、鉛が添加されているため、非常に高い加工性を誇ります。切削性が良好で、精密部品や複雑な形状を作る際に適しています。特に、以下の加工方法においてその特性が発揮されます:- 旋盤加工:C3602は旋盤加工において、非常に滑らかな仕上がりを得ることができます。
- フライス加工:フライス加工でも、優れた切削性を発揮し、スムーズな加工が可能です。
- ねじ切り加工:ねじ切り加工でも高い精度が得られるため、精密なねじ部品の製造にも適しています。
C3602の加工性能の利点
- 高い切削性:摩擦が少なく、工具の寿命が長いため、効率的な加工が可能です。
- 精密な加工:複雑な形状や高精度な部品を作成できます。
- 加工時間の短縮:優れた加工性により、高速での大量生産が可能です。
真鍮C3604の特徴
C3604は、優れた加工性と耐食性を持つ真鍮合金で、特に機械加工や精密部品の製造に適しています。この合金は、電気機器や自動車部品、精密機械部品など、幅広い分野で利用されています。C3604は、C3602と似た特性を持ちつつも、若干異なる用途や特性を有するため、特定の環境下での性能を最適化することができます。C3604の化学的組成
C3604の主な化学的組成は次の通りです:- 銅 (Cu):約 60〜64%
- 亜鉛 (Zn):約 35〜39%
- 鉛 (Pb):約 1.5〜2.5%
- その他:微量の鉄 (Fe) やアルミニウム (Al) など
C3604の物理的特性
C3604は、優れた機械的特性を持つため、さまざまな用途に適しています。以下はその主な物理的特性です:- 比重:8.4〜8.6 g/cm³
- 引張強度:約 490 MPa
- 伸び(延性):約 15〜20%
- 硬度:約 80〜100 HRB(ブリネル硬度)
- 導電率:比較的良好な導電性
C3604の物理的特性の利点
- 高い引張強度と延性:強度と柔軟性を兼ね備え、耐衝撃性が求められる部品に適しています。
- 優れた耐腐食性:湿気や化学物質に対する耐性が高く、長寿命の部品に最適です。
- 良好な導電性:電気機器や配線部品にも使用できるため、電気的な要求を満たします。
C3604の加工性能
C3604は、鉛が少なめに添加されているため、C3602よりもやや硬度が高いですが、それでも非常に高い加工性を持ちます。特に以下の点で優れた性能を発揮します:- 旋盤加工:C3604は旋盤加工時に、非常に滑らかな仕上がりが得られます。切削性が良好で、工具の摩耗を抑えながら高精度な加工が可能です。
- フライス加工:C3604はフライス加工にも適しており、複雑な形状の部品を効率的に製造することができます。
- ねじ切り加工:ねじ切りの際も優れた精度を発揮し、精密なねじ部品を作成できます。
C3604の加工性能の利点
- 優れた切削性:滑らかな仕上がりと効率的な加工が可能です。
- 高精度な加工:精密な部品や複雑な形状の加工が得意です。
- 工具の寿命:工具の摩耗が少ないため、長時間の連続加工に対応できます。
- 加工の柔軟性:冷間加工および熱間加工の両方で良好な性能を発揮します。
真鍮C3602とC3604の違い
C3602とC3604は、いずれも高い加工性と耐食性を持つ真鍮合金ですが、いくつかの特性において異なる点があります。以下では、化学組成、物理的特性、そして加工性能について比較していきます。化学組成の比較
C3602とC3604は、どちらも銅(Cu)と亜鉛(Zn)を主成分とする合金ですが、鉛(Pb)の含有量に違いがあります。- C3602:
- 銅(Cu):約 60〜65%
- 亜鉛(Zn):約 35〜39%
- 鉛(Pb):約 2〜3%
- C3604:
- 銅(Cu):約 60〜64%
- 亜鉛(Zn):約 35〜39%
- 鉛(Pb):約 1.5〜2.5%
物理的特性の比較
C3602とC3604は、共通の特性を持ちながらも、いくつかの物理的な点で違いが見られます。- C3602:
- 比重:8.4〜8.6 g/cm³
- 引張強度:約 450 MPa
- 延性:約 20〜25%
- 硬度:約 80〜100 HRB
- 導電率:良好
- C3604:
- 比重:8.4〜8.6 g/cm³
- 引張強度:約 490 MPa
- 延性:約 15〜20%
- 硬度:約 80〜100 HRB
- 導電率:良好
物理的特性の主な違い
- C3602は延性が高く、柔軟性が求められる用途に適しています。
- C3604は引張強度が高く、強度が求められる部品に適しています。
加工性能の比較
両者は加工性に優れていますが、鉛の含有量により、加工時の特性に違いが見られます。- C3602:
- 旋盤加工:非常にスムーズで仕上がりが良好。
- フライス加工:複雑な形状や精密部品の加工が得意。
- ねじ切り加工:優れた精度でねじ部品の製作が可能。
- C3604:
- 旋盤加工:C3602と比較して若干硬度が高いため、仕上げに注意が必要。
- フライス加工:精密加工において高精度な仕上がりを提供。
- ねじ切り加工:ねじ精度が非常に高く、連続加工にも適しています。
加工性能の主な違い
- C3602は加工が容易で、特に複雑な形状や精密部品に適しています。
- C3604は加工時の強度と耐久性が優れており、強度を重視した部品や精密加工に最適です。
材質選びのポイント
材質の選定は製品の性能や耐久性、コストに大きく影響を与えるため、適切な選択が重要です。以下では、用途に応じた材質の選定方法、コストと性能のバランス、加工方法との関係について解説します。用途に応じた材質の選定
材質選びにおいて最も重要なポイントは、用途に適した特性を持つ材料を選ぶことです。製品が求める性能に合った材質を選定することで、長期間安定した品質を保つことができます。以下の要素を考慮しましょう:- 耐食性: 屋外や腐食環境で使用する場合、耐食性が重要です。例えば、海水にさらされる部品や化学薬品を取り扱う機器では、耐食性に優れたステンレス鋼や特殊な合金が適しています。
- 強度: 機械部品や構造物には、強度や耐衝撃性が求められます。高強度鋼やアルミニウム合金などが適しています。
- 柔軟性: 曲げや引張りなどの応力に対して柔軟性が必要な場合、銅合金やアルミニウム合金、真鍮などが良い選択です。
- 耐摩耗性: 摩擦が発生する部分には、耐摩耗性が求められます。硬度の高い合金やセラミックが最適です。
コストと性能のバランス
材質選びにおいて、コストと性能のバランスを取ることも非常に重要です。高性能な素材は一般的に高価ですが、性能が低い材質を選んでしまうと、製品の寿命や品質に問題が生じることがあります。- 高性能材: 高価ですが、長寿命で高い耐久性が求められる場合に使用します。例えば、航空機部品や医療機器などには高性能なチタンや特殊合金が使われます。
- コスト重視材: 一定の性能が求められるが、コストを抑えたい場合には、鋼やアルミニウム合金、標準的な真鍮などが選ばれます。
- 中程度の性能とコスト: 一部の性能を犠牲にしてコストを抑えたい場合、例えば自動車部品や一般的な機械部品には、ステンレス鋼や一般的な銅合金が選ばれることがあります。
加工方法と材質の関係
材質の選定においては、加工方法との相性も重要な要素です。材質の硬さや靭性、延性などによって、加工性が大きく異なります。- 鋼材: 鋼材は非常に加工しやすく、熱処理によって硬度を調整することが可能です。しかし、鋼の硬さが高い場合、加工には高精度な機械が必要となります。
- アルミニウム合金: 軽量で加工が容易なため、切削や溶接がしやすいです。精密加工にも向いており、機械加工が簡単です。
- 銅合金: 真鍮や青銅は、加工性が良好であり、ねじ切りやフライス加工にも適しています。ただし、硬度が高い銅合金では、加工中に摩耗や工具の劣化が早く進むため、適切な工具の選定が重要です。
- プラスチックや複合材料: プラスチックや複合材料は、軽量で成形が簡単であり、射出成形や圧縮成形などで大量生産に向いています。
加工方法と材質の主な関係
- 鋼材やアルミニウム合金は加工が比較的簡単で、切削やフライス加工に向いています。
- 高硬度材料は加工が難しく、特別な工具や設備が必要です。
- プラスチックや複合材料は大量生産に適しており、型成形や射出成形が可能です。