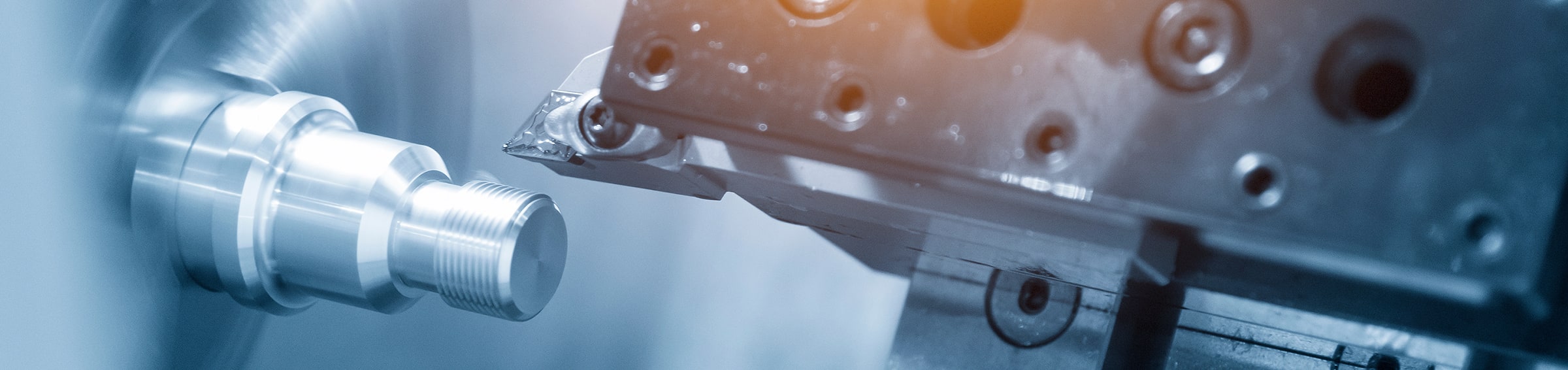
加工技術 column
C2600材の加工で成果を上げる!切削条件と注意すべき点
真鍮C2600の基礎知識
真鍮C2600は、銅を主体とした合金で、特にその高い加工性と良好な耐食性により、さまざまな産業で使用されています。以下にC2600材の基本的な情報と特性について解説します。C2600材とは
- 組成 C2600は、銅を基に、約70%の銅(Cu)を含み、残りの部分は主に亜鉛(Zn)で構成されています。この割合により、C2600は優れた加工性と優れた耐食性を持つ合金です。
- 用途 C2600は、主に電子機器の部品、建築金物、装飾用部品、機械部品などに使用されます。その美しい外観や高い耐食性が求められる製品に最適です。
- 加工性 高い加工性を持つため、切削や圧延、鍛造などの加工が比較的容易です。また、亜鉛の含有量が高いことから、溶接やハンダ付けにも適しています。
C2600の特性と切削性
- 耐食性 C2600は亜鉛が主成分の一部を占めており、海水や湿気に強いため、耐腐食性が高く、屋外や湿度の高い環境での使用にも適しています。
- 強度 この材質は適度な強度を有しており、一般的に機械的強度を求められる部品にも使用されますが、鋼材に比べると強度はやや劣ります。しかし、機械的な要求がさほど高くない部品では十分に機能します。
- 切削性 C2600は優れた切削性を持つため、旋盤やフライス盤などの機械を使用して簡単に加工できます。特に、細かい加工や複雑な形状の切削も比較的簡単に行える点が特徴です。そのため、高精度の部品を製造する際にも適しています。
- 成形性 この材質は引張強さと延性を兼ね備えており、冷間加工や熱間加工において優れた成形性を発揮します。また、圧延や鍛造によって薄板や細線に加工することができます。
- 熱処理 C2600は、熱処理により強度を高めることが可能ですが、他の材料に比べて熱処理の効果は限定的です。そのため、熱処理を行う際は、材料の特性に応じた温度管理が重要です。
真鍮C2600の切削加工
真鍮C2600は、その優れた加工性により、切削加工に非常に適した材料ですが、切削加工時にいくつかの注意点があります。ここでは、C2600の切削加工における基本的な考え方と注意点、さらに適切な切削工具の選び方について解説します。切削加工の基本
- 切削性の良さ 真鍮C2600は、優れた切削性を持っており、旋盤、フライス盤、ボール盤などでの加工が容易です。特に、加工時にチップが発生しやすく、良好な仕上がりが得られるため、精密加工にも向いています。
- 切削速度の設定 C2600の切削加工においては、適切な切削速度を設定することが重要です。過剰な切削速度は工具の摩耗を早める原因となり、品質にも影響を与えます。一方で、遅すぎる切削速度は加工効率を低下させます。一般的には中〜高切削速度を選択します。
- 切削油の使用 切削油を使用することで、切削面の品質が向上し、工具寿命を延ばすことができます。特に真鍮のような金属は、摩擦が発生しやすいため、切削油を使用することで加熱を防ぎ、スムーズな加工が可能になります。
C2600の切削加工での注意点
- 切削中の熱管理 C2600の切削加工では、金属の摩擦により発生する熱が問題になる場合があります。過度な加熱が発生すると、材料の変形や工具の摩耗を早める原因となるため、冷却を適切に行う必要があります。
- 切りくずの処理 C2600は切りくずが比較的大きくなりやすいため、適切な切りくず処理が重要です。切りくずが加工面に付着すると、仕上がりに影響を与えたり、作業効率が低下したりする可能性があります。切りくずを効率よく排出するために、適切な切削工具と冷却を使用することが推奨されます。
- 工具の選定と耐久性 C2600の切削には、耐摩耗性に優れた工具が必要です。工具の選定が不適切であると、工具の摩耗が早く、加工精度にも悪影響を及ぼします。工具寿命を最大化するためには、適切な工具の使用と管理が必要です。
真鍮加工に適した切削工具の選び方
- 高速度鋼(HSS)工具 高速度鋼(HSS)は、C2600の切削に最適な選択肢の一つです。HSSは耐摩耗性が高く、適度な靭性を持つため、細かい加工や複雑な形状の加工にも適しています。
- 超硬(カルバイド)工具 超硬工具は、高硬度のため長寿命を提供し、高速切削にも耐えることができます。C2600の切削で優れた性能を発揮するため、精密加工や高精度が求められる場合には最適です。ただし、加工時の振動や衝撃に弱いため、注意が必要です。
- チップ形状の選定 真鍮C2600の切削では、チップの形状も重要です。一般的に、平坦な表面仕上げが必要な場合は、片刃工具を使用することが推奨されます。曲線や複雑な形状を切削する際には、適切な形状の工具を選択することが精度を高めます。
- 工具コーティング C2600の切削では、工具の表面をコーティングすることが有効です。コーティングを施した工具は、摩耗や腐食に強く、加工中の摩擦を軽減するため、より高効率で高精度な加工が可能となります。
真鍮C2600のフライス加工テクニック
真鍮C2600は、その優れた加工性により、フライス加工においても高い効果を発揮します。しかし、効率的に加工を行うためには、いくつかのポイントとテクニックを押さえる必要があります。ここでは、フライス加工の基本からC2600材を使ったフライス加工のポイント、さらに工具寿命を延ばすコツについて解説します。フライス加工の基礎
- フライス加工とは フライス加工は、回転する工具(フライス盤)を用いて、金属の切削を行う加工方法です。金属の表面に対して様々な形状や凹凸を作ることができ、特に平面や溝、歯車、スロットなどの加工に適しています。
- 切削速度と送り速度 フライス加工における切削速度や送り速度の設定は非常に重要です。C2600材では、適切な切削速度を設定することで、効率的に加工が進みます。特に、送り速度を適度に調整することで、よりスムーズで高精度な加工が可能になります。
- 冷却と切削油の使用 フライス加工では、冷却剤や切削油を使用することで、摩擦を減少させ、加工面の品質を向上させます。これにより、工具の摩耗を減少させるだけでなく、加工精度も保たれます。
C2600材を使ったフライス加工のポイント
- 適切な切削条件の設定 C2600は比較的切削性が良いですが、適切な切削条件を設定することで、効率的な加工が可能となります。切削速度は300~400m/minを目安に設定し、工具の摩耗を抑えるために、送り速度や切込み深さを調整します。
- 工具の選定 フライス加工では、工具の材質や形状が非常に重要です。C2600のフライス加工には、耐摩耗性に優れた超硬工具や高速度鋼(HSS)工具が効果的です。特に、複雑な形状を加工する場合は、チップの形状や種類を選定することが精度向上に繋がります。
- 切りくずの処理 真鍮C2600は切りくずが大きくなることが多いため、効率的な排出が必要です。切りくずが加工面に絡みつくと、仕上げに悪影響を与えるため、定期的に切りくずを除去するようにしましょう。
- 仕上げの精度向上 フライス加工では、仕上げの精度が重要です。C2600のような金属は加工中に表面が滑らかになりやすいため、最後の仕上げ工程での微細な調整を行うことで、高精度な仕上がりが得られます。
フライス加工での工具寿命を延ばすコツ
- 切削油の選定と使用方法 適切な切削油を選定することにより、工具の冷却と潤滑が行われ、摩耗を防ぐことができます。特にフライス加工では、加工温度が上がりやすいため、冷却性能の高い切削油を選ぶことが重要です。
- 切削条件の最適化 切削条件(切削速度、送り速度、切込み深さ)を最適に設定することは、工具寿命を延ばすために重要です。過剰な切削負荷がかからないように調整し、工具の摩耗を抑えるようにします。
- 適切な切りくず処理 切りくずが溜まると、工具の摩耗を早めたり、加工精度を低下させる原因になります。定期的に切りくずを排出し、工具に負担をかけないように注意します。
- 工具の点検と交換 定期的に工具の状態を点検し、摩耗が進んでいる場合は早めに交換することが工具寿命を延ばすポイントです。また、異常な摩耗が見られた場合は、切削条件を見直すことが効果的です。
C2600材の切削条件の最適化
C2600(真鍮)は、その優れた加工性により、さまざまな切削加工に適していますが、最適な切削条件を設定することで、より効率的で高精度な加工を実現できます。ここでは、切削条件の基本要素からC2600材に最適な切削条件の設定方法までを解説します。切削条件の基本要素
- 切削速度(Vc) 切削速度は、工具の切削面が素材に接触する速さを示します。切削速度が適切でないと、工具の摩耗が早くなるだけでなく、加工面の仕上がりにも影響が出ることがあります。最適な切削速度は材質や加工目的に応じて選定します。
- 送り速度(Vf) 送り速度は、工具が加工物をどれだけの速さで移動するかを示します。適切な送り速度を設定することにより、切削力を適切に分散し、工具寿命の延長や加工精度の向上が可能となります。
- 切込み深さ(ap) 切込み深さは、工具が材料に食い込む深さを示します。深すぎる切込みは加工面に不均一な力を加えるため、工具の摩耗を早めます。適切な深さで切削を行うことが重要です。
- 回転数(n) 回転数は、工具が1分間に回転する回数を示します。回転数が高すぎると熱がこもりやすく、低すぎると切削効率が落ちます。適切な回転数を選定することが、効率的な切削を行うための鍵です。
銅や真鍮の種類別切削条件
- 銅(C1100) 銅は非常に柔らかい金属であり、切削性が良好です。一般的には、切削速度は約150~200 m/min、送り速度は0.1~0.2 mm/rev程度が推奨されます。銅の加工では切削熱を適切に処理することが重要で、冷却剤の使用が効果的です。
- 真鍮(C2600) 真鍮は、銅に亜鉛を加えた合金で、非常に優れた加工性を持っています。C2600は比較的硬さがあり、切削条件の設定には注意が必要です。切削速度は約300~400 m/minが理想的で、送り速度は0.1~0.3 mm/rev、切込み深さは0.2~0.5 mm程度が一般的です。
- 真鍮(C2800) C2800は亜鉛の割合が増えた真鍮で、C2600よりも少し硬度が高いです。C2800の加工には切削速度が200~300 m/min、送り速度は0.1~0.25 mm/rev、切込み深さは0.2~0.4 mm程度が推奨されます。
C2600材に最適な切削条件の設定
C2600は、適切な切削条件を設定することで、その優れた加工性を最大限に引き出すことができます。以下はC2600材に最適な切削条件を設定するためのポイントです。- 切削速度 C2600の適切な切削速度は、300~400 m/minです。これは、加工中に過度な熱の発生を避け、効率的に切削できる範囲です。高すぎる切削速度は工具の摩耗を加速させるため、注意が必要です。
- 送り速度 送り速度は、0.1~0.3 mm/revの範囲が適切です。切削速度と送り速度は互いに関連しているため、バランスよく設定することが求められます。送り速度が速すぎると切りくずの排出が難しくなり、加工品質が低下する可能性があります。
- 切込み深さ 切込み深さは、0.2~0.5 mmが一般的な範囲です。深すぎる切込みは、工具に過剰な負荷をかけることとなり、摩耗や欠損の原因となります。適切な深さを選定し、少しずつ切削を進めることが重要です。
- 冷却と切削油の使用 C2600材は切削熱が発生しやすいため、冷却と潤滑を適切に行うことが必要です。切削油を使用することで、工具の摩耗を抑えるだけでなく、加工面の仕上がりも良好になります。
- 工具の選定 C2600のような真鍮は比較的切削性が良いですが、適切な工具の選定も重要です。超硬工具や高速度鋼(HSS)工具が一般的に使用されますが、加工条件や求められる仕上げ品質に応じて、工具の材質や形状を選びましょう。
最適な切削条件を設定することで、C2600材の加工効率を最大化し、工具寿命を延ばしながら高精度な仕上がりを実現することができます。
切削工具の選択と管理
切削工具は、加工精度や効率を決定する重要な要素です。適切な切削工具を選び、管理することで、加工品質を向上させ、コストを削減できます。ここでは、長寿命な切削工具の選び方、切削工具のメンテナンスと交換時期、そして切削工具の性能を最大限に引き出すためのポイントを解説します。長寿命な切削工具の選び方
- 材質の選定 切削工具の材質は、加工する素材や使用する環境に応じて選ぶ必要があります。例えば、硬い材料を加工する場合には超硬工具(Carbide)やセラミック工具が適しています。一方、一般的な金属を加工する場合には高速度鋼(HSS)工具がコストパフォーマンスに優れています。
- コーティングの選定 切削工具には、耐摩耗性や耐熱性を高めるためのコーティングが施されています。コーティングの種類によって、工具の寿命や性能が大きく変わります。例えば、TiN(窒化チタン)コーティングは耐摩耗性を向上させ、TiAlN(窒化アルミニウム)は高温に強いため、高速切削に適しています。
- 工具の形状 切削工具の形状(エンドミル、ドリル、タップなど)は、加工方法に応じて選ぶべきです。例えば、鋭い切れ味が求められる場合や、硬い素材を削る場合には、特定の形状が有効です。また、工具の刃数や先端角度も重要な選定基準となります。
- 加工環境に合った工具選定 加工する材料の特性(硬さ、粘性など)や加工条件(切削速度、加工深さ)に応じて、適切な工具を選定することが大切です。例えば、硬い鋼を加工する場合は、耐摩耗性に優れた工具が必要です。
切削工具のメンテナンスと交換時期
- 定期的な点検とメンテナンス 切削工具は使用するごとに摩耗し、性能が低下します。定期的に点検を行い、摩耗状態をチェックしましょう。特に、工具の先端や切削面に摩耗が見られる場合は、性能が低下している可能性があります。
- 工具の刃先の研磨 切削工具の刃先は、定期的に研磨することで寿命を延ばすことができます。刃先が鈍ると、切削力が不足し、加工精度が低下します。研磨を行うことで、工具の切れ味を維持し、より効率的な加工が可能となります。
- 交換時期の判断 切削工具の交換時期を見極めることは重要です。交換時期を遅らせると、加工品質が低下し、工具の破損リスクが高まります。一般的に、工具の寿命は摩耗の進行具合や加工条件によって異なりますが、摩耗や傷が深刻になった場合、または加工精度が確保できなくなった時点で交換するべきです。
- 管理ツールの利用 現代では、工具管理ソフトウェアや工具寿命予測ツールを使用して、工具の状態を監視することができます。これにより、最適なタイミングでの交換が可能となり、無駄な交換や無駄な加工を防ぐことができます。
切削工具の性能を最大限に引き出すために
- 適切な切削条件の設定 切削工具の性能を最大限に引き出すためには、加工条件(切削速度、送り速度、切込み深さなど)を適切に設定することが重要です。過剰な切削速度や送り速度を設定すると、工具が過度に摩耗し、逆に効率が低下します。適切な条件で加工することで、工具の寿命を延ばし、最良の性能を発揮させることができます。
- 冷却と潤滑の管理 冷却と潤滑は、切削工具の性能を維持するために非常に重要です。適切な冷却剤や潤滑剤を使用することで、切削温度を抑え、工具の摩耗を抑制します。冷却や潤滑の方法を正しく選択し、効果的に活用することが、長寿命な切削工具を維持するための鍵となります。
- 適切な機械設定の利用 切削工具の性能を引き出すためには、機械設定の調整も重要です。機械の振動や不安定な動作が工具に負担をかけることがあります。機械の精度を確認し、安定した動作を維持することが、工具の性能を最大限に活用するための条件です。
切削工具を選択し、適切に管理することで、加工効率を高め、コストを削減することができます。また、適切なメンテナンスとタイムリーな交換により、工具の寿命を最大化し、安定した加工精度を維持することが可能です。
切削加工のトラブルシューティング
切削加工時にはさまざまな問題が発生することがありますが、これらのトラブルを早期に発見し、適切に対処することで加工の精度と効率を維持することができます。ここでは、一般的な切削加工時の問題とその対処法、真鍮C2600加工時の特有の問題点、さらにトラブルを予防するための解決策を紹介します。切削加工時の一般的な問題と対処法
- 切削不良(バリや溶け込み)
- 原因: 切削速度が速すぎる、または工具が鈍っていることが原因です。切削熱が発生しすぎて、材料が溶けたり、切削面にバリができたりすることがあります。
- 対処法: 切削速度や送り速度を適切に調整し、工具を定期的に交換するか、研磨します。また、冷却液を使用して切削熱を管理します。
- 表面仕上がりの不良
- 原因: 切削工具が摩耗している、または設定された加工条件が不適切な場合に、表面に傷や粗さが残ることがあります。
- 対処法: 使用する切削工具の材質やコーティングを見直し、精度の高い工具を使用します。加工条件(切削速度、送り速度、切り込み深さ)を再調整し、仕上げ工程での品質を向上させます。
- 振動(チャタリング)
- 原因: 機械の剛性不足や不適切な工具の取り付け、または不安定な切削条件が振動を引き起こす原因となります。
- 対処法: 切削条件を見直し、適切な送り速度と切削深さを設定します。また、工具の取り付けを確認し、機械の剛性を向上させることも有効です。
- 工具の摩耗
- 原因: 高速切削や硬い材料の加工によって工具が早期に摩耗することがあります。
- 対処法: 切削速度を適切に調整し、工具の選定を見直します。高品質なコーティング工具を使用したり、冷却や潤滑の方法を最適化することが効果的です。
真鍮C2600加工時の特有の問題点
- 切削熱の蓄積 真鍮C2600は良好な機械加工性を持ちますが、切削中に発生する熱が蓄積しやすいため、加工時の熱管理が重要です。過度な熱は工具の摩耗を加速させ、加工面の仕上がりに影響を与えることがあります。
- 対処法: 適切な切削速度と送り速度を設定し、冷却液を効果的に使用します。また、細かい切削深さで少しずつ加工する方法も有効です。
- 引きずりやすい切削面 真鍮は比較的柔らかい材料であるため、加工中に引きずりやすく、仕上がり面にムラが出やすいことがあります。
- 対処法: 切削条件を見直し、工具の刃先角度や形状を調整します。また、切削液を適切に使用して、切削面の潤滑を良好に保つことが大切です。
- 切削工具の摩耗 真鍮は比較的加工が容易ですが、軟らかいため、過度に深く切り込むと工具が摩耗しやすくなります。
- 対処法: 切削深さや送り速度を適切に設定し、切削工具の材質やコーティングを選定します。過度な負荷を避けるために切削条件を調整します。
切削加工トラブルの予防と解決策
- 適切な切削条件の設定 加工の初めに適切な切削条件を設定することで、トラブルを予防できます。材料に適した切削速度、送り速度、切り込み深さを選定し、加工精度を維持します。加えて、加工開始時に小さな切り込みから始めて、徐々に条件を最適化することが重要です。
- 冷却と潤滑の適切な管理 切削熱の蓄積や摩擦による問題を予防するために、冷却液や潤滑剤を適切に使用します。これにより工具の摩耗を減少させ、加工面の仕上がりを良好に保つことができます。
- 工具の定期的な点検と交換 定期的に工具の状態をチェックし、摩耗や損傷を早期に発見することがトラブルの予防につながります。工具が摩耗したまま使用し続けると、加工精度が低下し、余計なトラブルを引き起こします。
- 機械の定期的なメンテナンス 機械の精度や安定性を保つために、定期的なメンテナンスが必要です。機械の剛性が不足していたり、振動が生じると、加工中に問題が発生することがあります。定期的に機械を点検し、必要な修理や調整を行うことが、トラブルの予防につながります。
これらの対策を実行することで、切削加工中の問題を最小限に抑え、精度の高い加工を実現することができます。適切な条件設定、工具選定、冷却や潤滑の管理、そして定期的なメンテナンスを行うことで、トラブルを予防し、効率的な生産を維持することが可能です。
まとめ
C2600材の加工で成果を上げるためには、適切な切削条件と注意すべき点があります。C2600は切削性に優れた材料であり、適切な工具や切削速度、刃先形状などを選定することが重要です。加工時には適切な冷却や潤滑を行い、過度な摩擦や熱を防ぐことが肝要です。さらに、切削時の振動やひずみにも注意が必要です。これらの条件と注意点を把握することで、C2600材の加工において成果を上げることができます。C1100銅の加工性能と最適な切削条件
C1100銅の基本とその加工性能
C1100銅とは
C1100銅は、純度99.9%以上の高純度銅であり、電気伝導性や熱伝導性に優れているため、電気機器や電子機器の部品、配線材料などに広く使用されます。C1100銅は、純銅とも呼ばれ、その高い導電性から、特に電気配線や電気接点、通信機器において重要な役割を果たします。さらに、C1100銅は優れた延性や耐食性を持つため、さまざまな加工においても扱いやすい特性を示します。C1100銅の物理的・化学的特性
C1100銅の物理的および化学的特性は以下の通りです:- 導電性:C1100銅は非常に高い電気伝導率を持ち、銅の中でも最も優れた電気伝導特性を示します。これにより、電気回路や配線に最適です。
- 熱伝導性:高い熱伝導性を持ち、熱の拡散が迅速に行われます。そのため、熱管理が重要な機器で利用されます。
- 延性:C1100銅は非常に延性が高く、容易に引き伸ばしたり圧延したりすることができます。この特性により、さまざまな形状に加工することが可能です。
- 耐食性:空気中での腐食に対して比較的耐性がありますが、塩水や酸性環境では腐食が進行する可能性があります。
- 強度:純銅であるため、強度は高くありませんが、他の合金に比べてしなやかさと柔軟性に優れています。
加工性能とは
C1100銅の加工性能は、その物理的・化学的特性に基づきます。加工性能の主要な要素は以下の通りです:- 切削性:C1100銅は比較的柔らかく、延性が高いため、切削加工がしやすい素材です。しかし、加工時に発生する熱を効率よく取り除くためには適切な冷却と切削条件が必要です。
- 成形性:C1100銅は高い延性を持ち、圧延や引き伸ばしが可能です。金型やロールを使用した加工が得意で、板、線、棒状に加工することができます。
- 溶接性:C1100銅は溶接性が良好で、TIG溶接やMIG溶接を使用しても高品質な接合が可能です。ただし、溶接中に酸化が進行しやすいため、溶接部の処理が重要となります。
- 圧延性:C1100銅は圧延加工が非常に得意で、薄い板やフィルム状に加工することができます。熱間圧延や冷間圧延が可能で、さまざまな厚さや形状に対応できます。
- 曲げ性:柔らかいため、簡単に曲げ加工ができ、配管や配線用の製品などで使われます。しかし、極度に曲げる場合や冷間加工を繰り返す場合には、疲労破壊に注意が必要です。
C1100銅の切削性に関する概要
切削性の基礎知識
切削性とは、材料がどれだけ効率よく切削工具で加工できるかを示す特性です。これには材料の硬度、靭性、熱伝導性、延性などが大きな影響を与えます。硬度が高いと摩擦が増え、工具の摩耗が進みやすくなりますが、靭性が高い材料は割れやすくなることがあり、脆い材料では加工中に亀裂が生じる可能性が高くなります。また、熱伝導性が良い材料は加工中に発生する熱を効率よく拡散し、切削温度を下げるため、加工精度が向上します。延性が高い材料は切削中に粘りがあり、良好な表面仕上げを得やすくなります。C1100銅の切削性の特徴
C1100銅は、特に延性が高く、良好な導電性を持つため、切削加工において非常に優れた性能を発揮します。この銅は、比較的柔らかく延性が高いため、他の硬い金属と比較しても摩擦が少なく、切削中の工具の負担が軽減されます。そのため、C1100銅は精密加工や表面仕上げに非常に適しており、精度の高い加工を行うことができます。また、C1100銅は熱伝導性が高いことから、加工中に発生する熱が効率よく拡散され、切削温度を管理しやすくなります。これにより工具の寿命が延び、加工精度も保たれます。切削性に影響を与える要因
C1100銅の切削性は、いくつかの要因によって影響を受けます。まず、切削速度が重要です。C1100銅は高い切削速度でも良好な加工が可能ですが、切削速度が速すぎると発生する熱がうまく管理できず、工具の摩耗が早く進むことがあります。したがって、適切な切削速度を選定することが重要です。 次に、工具の選定が切削性に大きく影響します。C1100銅は比較的柔らかい素材であるため、工具には高速度鋼(HSS)や超硬合金が適しています。工具の材質や形状を適切に選ぶことで、切削中の摩耗を最小限に抑えることができます。 冷却剤や潤滑剤の使用も重要です。これにより切削中に発生する熱を抑制し、工具の寿命を延ばすことができます。エアブローや油性冷却剤を使用することで、切削温度を下げ、より安定した加工が可能になります。 さらに、切削深さや送り速度の設定もC1100銅の加工において重要です。過度の切削深さや過剰な送り速度は、加工中にかかる力を増加させ、工具の摩耗を早める原因となります。そのため、適切な切削条件を選定することが求められます。 最後に、C1100銅の均一性も加工性に影響を与えます。材料の純度が高いほど、加工が容易で表面仕上げが良好に保たれます。このように、C1100銅の切削性は多くの要因に左右されるため、最適な条件で加工を行うことが非常に重要です。C1100銅の切削条件の基準
切削速度の選定
C1100銅の切削速度は、使用する工具の種類や加工条件によって異なりますが、一般的に銅は高い切削速度で加工が可能です。銅の高い熱伝導性と良好な延性により、切削速度を適切に設定することで、摩耗を抑え、加工精度を高く保つことができます。通常、切削速度は200m/minから500m/minの範囲で設定されることが多いですが、工具の耐久性や加工の仕上がりを考慮し、最適な切削速度を選ぶ必要があります。高すぎる切削速度は工具の寿命を縮め、低すぎると加工効率が悪化するため、バランスを取った選定が求められます。フィード率とは
フィード率は、切削工具がワークに対して進む速度を示し、加工精度や表面仕上げに影響を与えます。C1100銅の加工では、比較的高いフィード率を設定することができます。フィード率が高すぎると、加工中に発生する力が増加し、工具の摩耗が速くなりますが、適切なフィード率を設定することで、加工効率を高めることができます。通常、フィード率は0.1mm/revから0.3mm/rev程度で設定されることが多く、具体的な条件に合わせて調整することが大切です。切削深さの設定
切削深さは、一度の切削で削る材料の厚さを指し、加工精度や仕上がりに影響します。C1100銅は延性が高いため、比較的深い切削深さでも良好な加工が可能ですが、過度な切削深さは工具に過度の負荷をかけ、摩耗や振動の原因となることがあります。一般的に、切削深さは0.5mmから2mm程度で設定されることが多いですが、切削条件や加工する部品の形状によって調整が必要です。深すぎる切削は、ワークピースや工具に過度の熱を発生させるため、適切な設定を心掛けましょう。銅の加工方法と最適な切削条件
旋削加工とその条件
銅の旋削加工は、非常にスムーズで効率的な加工が可能であり、主に円形部品や軸の加工に使用されます。旋削加工を行う際には、切削速度を高めに設定することができますが、工具の摩耗を抑えるために冷却剤を使用することが重要です。一般的な旋削加工の条件としては、切削速度は200m/min〜500m/min、フィード率は0.1mm/rev〜0.3mm/rev、切削深さは0.5mm〜2mm程度が適切です。工具の選定としては、超硬やコーティング工具が一般的に使用され、長寿命化と精度向上が期待できます。フライス加工とその条件
銅のフライス加工では、平面や溝などの複雑な形状を精密に加工できます。フライス加工における最適な切削条件は、切削速度を高めに設定することが可能ですが、熱が発生しやすいため冷却を十分に行うことが重要です。一般的には、切削速度は200m/min〜400m/min程度、フィード率は0.1mm/rev〜0.3mm/rev、切削深さは0.5mm〜2mm程度が推奨されます。加工の際には、高い表面精度を要求する場合が多いため、仕上げ加工時には切削条件を低めに設定することもあります。ドリル加工とその条件
銅のドリル加工では、比較的低い切削速度で効率よく穴あけが行えますが、ドリルの刃先が摩耗しやすいため、適切な冷却を行うことが大切です。切削速度は30m/min〜80m/min、送り速度は0.05mm/rev〜0.15mm/rev、切削深さは使用するドリルの長さに合わせて調整します。銅は柔らかく延性があるため、ドリル加工の際に引っかかりやすいことがあるため、工具の鋭さや冷却条件を適切に管理することが重要です。研削加工とその条件
銅の研削加工では、精度の高い仕上げが求められます。研削加工においては、切削速度がやや低めに設定され、精密な仕上げ加工を行うことができます。切削速度は15m/s〜30m/s程度、送り速度は0.01mm〜0.05mm/rev、切削深さは非常に小さいため、数μm単位で調整します。研削時には熱が発生しやすいので、適切な冷却を行い、工具の寿命を延ばしつつ精度を保つことが求められます。銅の研削は高精度な加工が必要なため、十分な冷却と細かな条件調整が重要です。加工トラブルとその対処法
よくある加工トラブルとその原因
銅を加工する際に発生するトラブルは、以下のようなものがあります。- 工具の摩耗:
- 原因: 銅は比較的柔らかいため、長時間の加工により工具が摩耗しやすい。特に高い切削速度や不適切な冷却が原因で工具の寿命が短くなることが多いです。
- 加工中の引っかかりや振動:
- 原因: 銅は延性が高いため、加工中に切削屑が工具に絡みやすいです。また、切削中の振動が大きくなることもあります。これらは切削速度や送り速度の設定不良、工具の鋭利さの不足が原因です。
- 表面仕上げの不良:
- 原因: 切削条件が適切でない場合、加工面に凹凸や焼けが生じることがあります。特にフライス加工や研削加工で表面精度を保つのが難しくなることがあります。
- 熱変形:
- 原因: 銅は熱伝導性が高いため、加工中に熱が集中すると部品の寸法が変わることがあります。冷却不足や過剰な切削深さが主な原因です。
切削条件の最適化によるトラブルの防止
加工トラブルを防ぐためには、切削条件の最適化が重要です。以下の方法で改善できます。- 切削速度の調整: 銅の加工には適切な切削速度が必要です。過度な切削速度を避け、工具の摩耗を最小限に抑えるよう設定します。
- 冷却方法の見直し: 冷却不足がトラブルの原因になるため、適切な冷却剤を使用し、加工中に冷却効果を高めることが重要です。高圧のエアやオイルを使用することも有効です。
- 工具選定とメンテナンス: 銅の特性に合った工具を選び、定期的に点検・交換を行うことで、摩耗や振動を抑えます。
- フィード率と切削深さの最適化: 過度なフィードや切削深さはトラブルを引き起こします。設定を適切に調整し、最適な範囲内で加工を進めることが大切です。
トラブル発生時の対処法
加工中にトラブルが発生した場合、迅速な対応が必要です。以下の対処法があります。- 工具の点検と交換:
- 摩耗や損傷が見られた場合は、即座に工具を交換し、再度最適な切削条件で作業を行います。
- 冷却条件の改善:
- 加工中の熱が原因で変形が発生している場合、冷却方法を強化することが重要です。冷却液を増量する、冷却圧を上げるなどの対応を行います。
- 切削条件の再調整:
- 振動や引っかかりが発生している場合、切削速度や送り速度を調整して、加工の安定性を確保します。特に加工初期にフィード速度を低めに設定することが有効です。
- 仕上げ加工の見直し:
- 表面仕上げが不良の場合は、仕上げ用の工具や切削条件を再調整し、必要に応じて精密な仕上げ加工を追加します。
切削技術者必見!C2801材の加工時の注意点まとめ
真鍮C2801の基本と加工技術
真鍮C2801の物性と特徴
真鍮C2801は、銅(Cu)と亜鉛(Zn)を主成分とする合金で、一般的に「高精度真鍮」として知られています。C2801は、耐食性や機械的特性に優れた金属で、加工性にも優れ、特に切削加工や圧延加工に適しています。銅と亜鉛の割合によって調整され、C2801は優れた耐摩耗性、耐食性を持ち、腐食に強いため、屋外や水回りでの使用に適しています。また、電気的伝導性にも一定の特性があり、電子機器の部品にも利用されます。さらに、金属の色合いが美しいことから、装飾品や精密機械にも使用されます。C2801材の切削性について
C2801の切削性は、他の金属材料と比較して非常に良好です。高い加工性を誇り、切削加工が容易で、切りくずがスムーズに除去されます。これにより、精密部品を効率的に製造することが可能です。真鍮自体が比較的柔らかいため、工具の摩耗も少なく、長時間の加工が可能です。ただし、切削時に発生する熱の影響を抑えるため、冷却剤や潤滑剤を使用することが推奨されます。C2801は圧延と引き抜き加工にも適しており、円形や複雑な形状の部品を高精度で製造できます。加工技術者が押さえるべきC2801の基礎知識
加工技術者がC2801を扱う際に重要なのは、以下の点です:- 切削工具の選定: C2801は加工性が良好ですが、工具の選定は非常に重要です。鋭い刃先と高硬度を持つ工具を使用することで、精度高く加工が可能です。特に高回転数の加工では工具の冷却を十分に行うことが必要です。
- 切削条件の最適化: C2801は柔らかいため、切削速度が速すぎると材料が溶けたり、過剰な摩耗が発生したりすることがあります。適切な回転数と送り速度を選定し、均等な切削力をかけることが大切です。
- 熱の管理: 加工中に発生する熱を適切に管理することが重要です。冷却剤の使用や切削油の活用により、工具や材料への熱影響を抑えることができます。
- 仕上げ加工: 真鍮C2801は表面の仕上がりが良いため、最終的な仕上げ加工を行うことで、精度の高い部品を作り出すことが可能です。細かい表面処理やバリ取りなどを適切に行うことが求められます。
真鍮C2801の切削加工での注意点
切削工具の選定と管理
真鍮C2801の切削加工において、切削工具の選定は非常に重要です。C2801は比較的柔らかい材料であり、高い切削性能を持っているため、工具選びには注意が必要です。適切な工具の選定は、加工精度や工具寿命に大きな影響を与えます。- 工具の材質: 高速鋼(HSS)や超硬工具が一般的に使用されますが、真鍮に適した耐摩耗性と耐熱性を持つ工具が望ましいです。
- 刃先形状: 鋭利な刃先を使用することで、切削抵抗が減少し、仕上がり精度が向上します。また、工具の摩耗を抑えるためにも、適切な形状の刃先を選定することが重要です。
- 工具管理: 工具の摩耗や欠けを防ぐために、定期的に点検・管理することが必要です。切削中に異常を感じた場合は、すぐに工具の交換を行うようにしましょう。
切削条件の設定
切削条件の設定は、真鍮C2801の加工性を最大限に活かすために重要です。適切な切削条件を設定することで、加工効率を高め、製品の品質を向上させることができます。- 切削速度: C2801は切削性が良いため、比較的高い切削速度で加工できます。ただし、過度な速度設定は工具の摩耗を早める可能性があるため、適切な範囲で設定しましょう。
- 送り速度: 高い送り速度を設定することで、切削力を均一に分散させ、加工精度を保ちやすくなります。適切な送り速度を選ぶことで、表面仕上げが向上し、作業効率も向上します。
- 切削深さ: 切削深さは、加工する部品や使用する機械に応じて適切に設定します。浅すぎると加工時間が長くなり、深すぎると工具や材料に負担がかかるため、適切なバランスを見つけましょう。
切削液の使用とその影響
切削液は、真鍮C2801の切削加工において非常に重要な役割を果たします。切削液を適切に使用することで、工具の摩耗を抑え、切削温度の管理ができ、仕上がり品質が向上します。- 冷却作用: 切削中に発生する熱を抑えるために、冷却性能の高い切削液を使用することが推奨されます。これにより、過度な熱膨張を防ぎ、工具や材料の寿命を延ばすことができます。
- 潤滑作用: 切削液は、切削面の潤滑を提供し、摩擦を減らすことで工具の摩耗を抑制します。潤滑効果を高めることで、加工精度が向上し、部品の仕上がりが滑らかになります。
- 選定: 真鍮C2801の加工には、適切な切削液を選ぶことが重要です。水溶性の切削液や油性の切削液があり、加工条件や機械の仕様に合わせて選定する必要があります。
加工温度と切削速度の関係
加工温度は切削加工において非常に重要であり、切削速度と密接に関連しています。温度管理をしっかり行うことで、加工品質を保ちながら効率的に作業を進めることができます。- 切削温度の影響: 高すぎる加工温度は、工具の摩耗を早め、部品の変形や品質低下を引き起こす可能性があります。また、材料自体が変質することもあるため、温度管理が重要です。
- 切削速度と温度の関係: 切削速度が高いほど、発生する熱も多くなります。高速度で加工すると熱の発生が激しくなるため、冷却効果の高い切削液を使用することが推奨されます。切削速度を適切に設定し、加工中の温度上昇を抑えることが重要です。
切削挙動と加工精度の向上
切削挙動の基本
切削挙動は、切削加工中に材料がどのように反応するか、またその影響がどのように現れるかを理解することです。切削力や切削面の状態、工具の摩耗具合などがその要素です。これらの要素は、適切な切削条件や機械設定によって調整できるため、良好な加工結果を得るためには、切削挙動をしっかり把握することが必要です。切削力が大きすぎると、工具の摩耗が早く進んだり、仕上がり面が粗くなることがあり、加工中に発生する熱も材料の変形を引き起こす原因となります。切削面の状態も、切削条件によって大きく左右され、滑らかな仕上がりを得るためには、適切な設定が求められます。真鍮C2801の加工時の挙動特性
真鍮C2801は銅を主成分とした合金で、切削加工性に優れています。その特性として、切削時に発生する摩擦や発熱が比較的少ないことが挙げられます。これにより、工具の寿命が延び、精度の高い加工が可能となります。しかし、切削速度や深さ、冷却管理が不適切であると、摩耗が進んだり、発熱による問題が生じたりする可能性があります。過剰な切削速度や不適切な冷却は、加工精度を悪化させる原因となるため、これらの要素を調整することが重要です。 また、真鍮C2801は比較的柔らかいため、良好な仕上がり面を得やすい素材ですが、切削中の振動や工具選定が重要な要素となります。切削力が強すぎたり、工具が不適切であったりすると、仕上がり面に傷がついたり、寸法精度が低下したりする可能性があります。精度向上のための工夫と技術
真鍮C2801の加工精度を向上させるためには、切削条件の最適化が必要です。切削速度や送り速度、切削深さを調整することで、発生する切削力や発熱を適切に管理できます。過剰な切削速度や不適切な送り速度は、工具の摩耗や仕上がり面に悪影響を与えることがあるため、これらのパラメータを調整し、最適な条件を見つけることが求められます。 また、工具選定にも注意が必要です。真鍮C2801は切削性が良いとはいえ、精度の高い加工を行うためには、適切な工具を選ぶことが重要です。特に、摩耗が少なく、耐熱性の高い超硬工具を使用することで、精度を維持しつつ効率的な加工が可能です。工具が適切であれば、加工中の振動を抑え、より高精度な仕上がりを実現できます。 さらに、切削液や冷却剤の使用は加工精度を向上させるために不可欠です。冷却液を適切に選定し、使用することで、加工中に発生する熱を抑えることができ、材料の変形や工具の摩耗を防ぎます。冷却効果が高い切削液を使うことで、温度が上昇しにくくなり、加工中の精度を維持できます。 振動の管理も重要です。加工中に発生する振動は仕上がりに悪影響を与えることがあるため、振動を抑制するための機械設定や加工方法の見直しが求められます。振動が最小限に抑えられれば、寸法精度や表面粗さが向上し、より精密な加工が可能になります。 これらの工夫を実施することで、真鍮C2801の加工精度を大幅に向上させ、高品質な製品を効率よく製造することができるようになります。真鍮の特性を活かした切削加工のコツ
C2801の特性に合わせた加工方法
真鍮C2801は、その特性により切削加工が比較的容易で、柔らかく加工しやすい素材です。しかし、その柔らかさゆえに切削時に摩耗が発生しやすいため、切削工具の選定が重要となります。C2801を加工する際は、適切な切削工具を選ぶことで、作業効率を上げることが可能です。例えば、超硬工具やコーティングされた工具を使用すると、摩耗を抑え、長寿命で安定した加工が期待できます。 また、切削速度は適度に設定することが重要です。過度な切削速度は、熱や摩耗の原因となり、工具寿命を縮める可能性があります。適切な切削速度と送り速度を設定し、冷却管理を行うことで、長時間の加工でも精度を保ちながら進められます。切削加工時のバリ発生と対策
バリの発生は、切削加工における一般的な問題であり、特に柔らかい金属や合金で顕著です。真鍮C2801の加工時にも、バリが発生することがあります。バリを最小限に抑えるためには、切削工具の状態を常に確認し、摩耗を避けることが必要です。工具が鈍くなると、材料がきれいに切断されず、バリが発生しやすくなります。 さらに、切削条件の最適化もバリ発生を減らすための重要なポイントです。切削速度や送り速度が適切でない場合、バリが大きくなる可能性があるため、これらのパラメータを慎重に調整します。また、切削液を使用することで、材料の断面が滑らかになり、バリの発生を抑制することができます。冷却・潤滑の効果によって、切削面がきれいになり、バリを削り落とす手間が減少します。表面仕上げと加工精度
真鍮C2801はその柔らかさと滑らかさから、良好な表面仕上げが得やすい素材です。ただし、加工精度と仕上げ面の滑らかさを高めるためには、切削条件や工具選定に工夫が必要です。適切な切削速度や送り速度を設定し、過度な力を加えないことが大切です。適正な加工条件を設定することで、滑らかで高精度な仕上げ面が得られます。 また、加工精度を維持するためには、加工中の工具摩耗を最小限に抑えることが重要です。摩耗した工具は加工精度を低下させるため、適切なタイミングで工具を交換し、常に最適な状態で作業を進めることが求められます。さらに、加工後に仕上げ作業を行う際には、手作業での研磨やバリ取りを行い、最終的に美しい表面を仕上げることができます。 これらの工夫を実施することで、真鍮C2801の切削加工時の品質が向上し、優れた仕上げ面と高精度の製品を製造することができます。銅および真鍮加工の際の一般的な注意点
銅系材料の加工における共通の問題点
銅および真鍮は、柔らかく加工しやすい金属材料ですが、その特性が加工時に特有の問題を引き起こすことがあります。特に、銅系材料は切削時に高温になりやすく、工具の摩耗が速く進むことが多いため、適切な切削工具の選定が求められます。さらに、銅は切削中に付着しやすく、工具の切れ味を維持するためには、定期的な工具交換やメンテナンスが必要です。 また、銅や真鍮はバリが発生しやすい材料です。バリが大きくなると、後工程での処理が必要となるため、加工時にバリを最小限に抑えるための切削条件の最適化が欠かせません。バリの発生を減らすために、適切な切削液の使用や切削工具の角度の調整が効果的です。切削加工における環境と安全性
銅および真鍮を加工する際の環境および安全性にも十分に配慮が必要です。切削中に発生する高温や火花、さらには切削液の飛散などが安全リスクとなるため、加工エリアの安全対策は重要です。作業者は、適切な防護具(眼鏡、手袋、作業服など)を着用し、切削液が飛び散らないようにシールドを設置するなど、安全管理を徹底する必要があります。 また、銅や真鍮は加工中に細かい粉塵を発生することもあります。これらの粉塵は呼吸器系に影響を与える可能性があるため、作業場には十分な換気設備を整え、空気清浄機や集塵装置を導入することが推奨されます。作業後の清掃も重要であり、粉塵が残らないように適切に処理することが安全な作業環境を確保します。長期的な加工安定性の確保方法
銅および真鍮の加工において長期的な安定性を確保するためには、定期的なメンテナンスとチェックが重要です。切削工具の摩耗状況を常に監視し、切れ味が落ちる前に適時工具を交換することが加工精度の維持につながります。また、加工中に発生する熱を適切に管理するために、冷却・潤滑の役割を果たす切削液の使用も欠かせません。切削液はその効果が薄れることがあるため、定期的に交換することが推奨されます。 さらに、加工条件(切削速度、送り速度、切削深さなど)を工場環境や材料特性に合わせて最適化することが、長期間にわたる安定した加工を実現するために不可欠です。加工条件が不適切な場合、部品精度にばらつきが生じたり、加工時間が長くなったりすることがありますので、常に最適な設定を維持することが重要です。 これらの点を踏まえた上で、銅および真鍮の加工を行うことで、安定した品質と生産性を保ちつつ、安全に作業を進めることができます。【完全ガイド】C3604合金の切削性を高める方法
C3604合金の基礎知識
C3604合金とは
C3604合金は、銅合金の一種で、特に切削性が優れた材料として知られています。この合金は主に銅を基にしており、微量の鉛や亜鉛、その他の元素が加えられています。これにより、C3604は優れた加工性と機械的特性を持つため、精密機械部品や装置の製造に広く使用されています。C3604合金は、強度や耐久性が要求される部品においてもその特性を活かすことができ、特に金属加工において注目されています。C3604合金の特性と用途
C3604合金の主な特性には、優れた切削性、優れた耐摩耗性、優れた導電性、耐腐食性があります。これらの特性により、C3604は精密加工が必要な部品、特に耐摩耗性を必要とする部品に使用されます。具体的には、自動車部品や電子機器、電気コネクター、精密機器の構造部品などに用いられます。 C3604合金の高い切削性と優れた加工性が特に評価されており、加工時に発生する熱や摩耗を抑えることができるため、加工コストの削減にも貢献します。また、鉛を含んでいることから、切削加工における摩擦が低減し、工具の寿命も延びます。C3604合金の切削性に関する一般的な理解
C3604合金は、銅合金の中でも非常に高い切削性を持っており、機械加工において非常に扱いやすい材料です。この合金に含まれる鉛が、切削中に発生する摩擦を減少させ、切削中の熱を抑える効果をもたらします。そのため、C3604合金は高精度な加工を可能にし、加工時間を短縮することができます。 さらに、C3604合金はその優れた加工性により、加工時に発生する材料のひずみや変形が少なく、精密な寸法を維持しやすいという特長があります。また、切削性が良好であることから、工具の寿命も長くなるため、経済的にも優れた選択肢となります。 この合金の切削性の高さは、特に高精度部品の大量生産においてメリットとなり、製造工程を効率化するための重要な要素となっています。そのため、C3604合金は多くの製造業で使用されており、精密部品の大量生産において重宝されています。C3604合金の切削性向上のための準備
切削工具の選定
C3604合金はその高い切削性が特徴的ですが、適切な切削工具を選ぶことが加工効率を最大化するために重要です。C3604は比較的柔らかい材料であるため、工具には高い耐摩耗性を持つものを選ぶ必要があります。特に、硬度が高く、耐久性に優れた超硬工具やコーティングされた工具が最適です。工具の材質には、TiN(チタン窒化物)やTiAlN(チタンアルミニウム窒化物)のコーティングが施されたものが推奨されます。これにより、切削中の摩擦が減少し、工具の寿命が延びます。 また、工具の形状にも注意が必要です。C3604合金の切削性を最大限に引き出すためには、チップの形状が切削力を均等に分散できるように設計されたものが良いです。特に、耐熱性や耐摩耗性が求められる場合は、チップの角度や切削刃の形状に工夫が必要です。切削液の種類と効果
切削液はC3604合金の加工において非常に重要な役割を果たします。適切な切削液を使用することで、切削時の摩擦を減少させ、工具の冷却効果を高め、加工精度を向上させます。また、切削液は材料表面の汚れを防ぎ、仕上がりの品質を向上させる効果もあります。 C3604合金の切削性向上には、特に水溶性の切削液や油性切削液が効果的です。水溶性切削液は冷却性能が高く、発生した熱を効率的に逃がすことができます。一方、油性切削液は潤滑性能が優れており、摩擦を抑えることにより、工具の寿命を延ばし、加工面の仕上がりを良くします。使用する切削液の種類は、加工する部品の材質や加工条件に応じて選定することが重要です。加工機械の設定とメンテナンス
C3604合金を効率的に加工するためには、加工機械の設定やメンテナンスが重要です。加工機の回転数、切削速度、送り速度などを適切に設定することで、加工効率を最大化し、工具の摩耗を抑えることができます。C3604合金は切削性が良いため、通常の金属と比較して高い切削速度で加工することが可能ですが、過度な速度設定は摩耗を早める可能性があるため注意が必要です。 また、機械の定期的なメンテナンスも欠かせません。加工精度を保つために、機械のガイドやスライド部分に定期的な清掃や潤滑を行い、摩耗を防ぐことが必要です。これにより、長期的に高精度な加工を維持することができます。機械の設定やメンテナンスが適切であれば、C3604合金の加工はより効率的で高品質な仕上がりを実現することができます。C3604合金の加工方法とその注意点
加工前の材料処理
C3604合金を加工する前に、材料の準備が重要です。材料表面の不純物や油分を取り除くために、十分な清掃を行うことが推奨されます。これにより、加工中のトラブルを防止し、加工精度を向上させます。また、C3604合金は比較的柔らかいため、予備の熱処理を施すことで、硬さや強度を調整し、よりスムーズな加工が可能になります。 熱処理を行う際には、適切な温度と時間の管理が重要です。例えば、焼入れや焼戻しなどの熱処理は、材料の特性を大きく変化させるため、加工前にその状態を最適化することが必要です。これにより、材料の脆性や柔軟性をコントロールでき、加工のしやすさが向上します。切削性を考慮した加工プロセスの計画
C3604合金は優れた切削性を持つため、加工の際にはその特性を最大限に活用することが重要です。まず、切削条件を慎重に計画することが求められます。切削速度、送り速度、切り込み深さなどは、材料の特性に合った設定を行うことが重要です。C3604合金は比較的軟らかく、切削時に発生する熱が少ないため、高速切削が可能です。 ただし、切削条件が不適切だと、加工中に発生する熱が原因で材料が変形したり、加工面が荒れることがあります。そのため、加工前に試験加工を行い、最適な条件を見つけることが推奨されます。また、C3604合金は良好な表面仕上げを得るために、高精度な加工を心がけることが大切です。加工中の温度管理とその重要性
C3604合金の加工中には、温度管理が非常に重要です。切削中に発生する熱は、工具の摩耗や材料の加工性に大きな影響を与えるため、温度を適切にコントロールする必要があります。高温が発生すると、材料の熱膨張が原因で寸法精度が低下し、表面仕上げが粗くなる可能性があります。 そのため、切削液を使用して工具や加工部位の冷却を行うことが重要です。切削液の選定は温度管理に大きな役割を果たし、冷却効果を高めるためには、冷却能力の高い切削液を選択することが推奨されます。また、加工中に発生する熱を効率的に逃がすため、適切な切削液の供給や、加工機械の冷却システムの維持が必要です。 加工後の部品の温度を適切に管理することによって、加工精度を保ち、最終製品の品質を向上させることができます。高温による熱膨張や歪みを防ぐために、適切な冷却と時間管理を行うことが加工中の成功に直結します。C3604合金の旋盤加工のポイント
旋盤加工の基本
旋盤加工は、回転する素材を固定し、切削工具を用いて材料を削る加工方法です。この方法は、円形部品や円筒形の加工に広く用いられます。C3604合金はその高い切削性と良好な機械的特性から、旋盤加工において非常に適しています。しかし、加工時にはいくつかのポイントに注意する必要があります。 まず、旋盤加工においては、適切な切削速度と送り速度を設定することが重要です。C3604合金は比較的軟らかいため、高速で切削することが可能ですが、過度に高速な切削は工具の摩耗を早める原因となるため、適切な切削条件を選定することが求められます。旋盤加工でのC3604合金の切削性の注意点
C3604合金の切削性は比較的良好で、切削中の熱発生が少なく、工具の寿命を延ばすことができます。しかし、加工時に注意すべき点がいくつかあります。- 工具摩耗: C3604合金は比較的軟らかいため、切削工具への負担が少ないと考えがちですが、工具の角度や材質によっては摩耗が早まる可能性があります。特に、低速での切削時に工具摩耗が目立つことがあるため、工具の選定に注意が必要です。
- 表面仕上げ: C3604合金は良好な表面仕上げを得ることができますが、高速切削にすることで表面が荒れることもあります。そのため、適切な切削条件を選び、加工後に仕上げを行うことが求められます。
- 切りくずの処理: C3604合金は比較的切りくずが多く発生しやすいため、切りくずの処理方法を考慮することが重要です。切りくずが工具に絡みつくことを防ぐため、切削液の供給量や切りくず排出システムの管理が必要です。
旋盤加工に最適な工具とパラメータの選択
C3604合金の旋盤加工には、適切な工具と切削パラメータの選択が重要です。- 工具の選定: C3604合金においては、炭化物工具や超硬工具が一般的に使用されます。これらの工具は硬度が高く、耐摩耗性が優れているため、長期間安定した切削性能を発揮します。また、工具の形状や角度(特に前角と後角)も切削性に大きな影響を与えるため、C3604合金に適した角度設定が重要です。
- 切削パラメータ: 切削速度は中程度の速さで設定することが推奨されます。一般的には、C3604合金の旋盤加工では、切削速度は100~200m/min程度が適切とされています。送り速度と切込み深さは、加工する形状や精度要求に応じて設定しますが、通常は小さめの切込み深さと適度な送り速度が最適です。
- 切削液の使用: 旋盤加工中に切削液を適切に使用することで、工具の冷却と切りくずの排出が効果的に行えます。切削液は、工具の温度管理をサポートし、表面仕上げの向上にも寄与します。
C3604合金のフライス加工のコツ
フライス加工の基礎知識
フライス加工は、回転する切削工具を使用して、材料の表面を削る加工方法であり、平面や溝、複雑な形状を作り出すために広く用いられます。この加工方法は、横送り、縦送り、または斜め送りなど、さまざまな動きで行われ、非常に柔軟な加工方法です。C3604合金は、その優れた切削性により、フライス加工でも効率的に作業が進む材料ですが、適切な切削条件と工具選定が重要です。フライス加工におけるC3604合金の切削性のポイント
C3604合金は、良好な切削性を持ち、フライス加工においては他の材料と比べて比較的加工が容易ですが、いくつかのポイントを押さえることで、より効率的に加工することができます。- 切削速度: C3604合金は銅合金の中でも比較的柔らかいため、高速でのフライス加工が可能です。しかし、過度に高い切削速度を設定すると、工具の摩耗が進み、加工精度が低下することがあるため、適切な範囲で設定することが求められます。通常、切削速度は120~200m/minが適切とされています。
- 送り速度と切込み深さ: 送り速度や切込み深さを適切に設定することが、効率的なフライス加工には重要です。C3604合金は柔らかいため、比較的小さい切込み深さと中程度の送り速度での加工が推奨されます。過度の切込み深さは、工具に過剰な負担をかける可能性があります。
- 工具摩耗: C3604合金はその高い加工性を誇りますが、特に長時間の加工や過度な切削負荷がかかると、工具摩耗が発生しやすいです。切削中の温度管理と工具の冷却をしっかり行うことが、工具寿命を延ばし、良好な加工精度を維持するために重要です。
- 切りくずの処理: C3604合金は加工中に切りくずが大量に発生することがあり、これを効率的に排出しないと工具が詰まる原因となり得ます。切削液の供給や切りくずの排出システムを工夫し、切りくずが工具に絡まないようにすることが求められます。
効率的なフライス加工のための技術と戦略
C3604合金のフライス加工をより効率的に行うためには、以下の技術と戦略を考慮することが重要です。- 工具の選定: C3604合金のフライス加工には、超硬工具や炭化物工具が推奨されます。これらの工具は高い耐摩耗性と高強度を持っており、長期間にわたって安定した性能を発揮します。また、工具の形状や角度(特に前角や後角)は、切削性を大きく左右しますので、適切に設計された工具を選定することが重要です。
- 切削液の選定: 切削液はフライス加工中の工具の冷却と潤滑に重要な役割を果たします。C3604合金のフライス加工では、適切な切削液を使用することで、切削温度を下げ、工具摩耗を減らすとともに、良好な表面仕上げを得ることができます。水溶性の切削液や油性の切削液を使用することが一般的ですが、加工内容に応じて選定が必要です。
- 加工パラメータの最適化: 切削速度、送り速度、切込み深さは、加工する部品や形状に応じて最適化する必要があります。C3604合金は比較的軟らかいため、過度な切込み深さや高い送り速度を避け、安定した切削条件を維持することが大切です。
- 定期的なメンテナンスと点検: フライス加工機械の定期的なメンテナンスと点検を行うことで、加工精度を保ち、工具の寿命を延ばすことができます。特にフライス加工中に発生する振動や不安定な動きを防ぐために、機械の精度を定期的に確認することが求められます。
C3604合金加工の効率化と品質向上
加工効率を高めるための工夫
C3604合金はその優れた加工性により、効率的な切削が可能ですが、加工効率をさらに高めるためにはいくつかの工夫が必要です。- 最適な切削条件の設定: 加工効率を最大化するためには、最適な切削条件(切削速度、送り速度、切込み深さ)を設定することが不可欠です。適切な設定を行うことで、加工時間を短縮し、工具摩耗を最小限に抑えることができます。例えば、C3604合金は比較的柔らかいため、高速切削が可能ですが、あまりにも高すぎる切削速度は工具に過度な負担をかけるため、最適なバランスを見極めることが重要です。
- 高効率な切削工具の選定: 加工効率を高めるためには、ツールの選定も重要です。C3604合金に適した切削工具(例えば超硬工具や炭化物工具)を使用することで、耐摩耗性や強度が向上し、長時間の加工が可能となります。また、工具の形状やコーティングを最適化することで、切削力が軽減され、効率的に加工が進みます。
- 適切な切削液の使用: 切削液は切削温度を抑え、工具の冷却と潤滑を助けます。C3604合金に適した切削液(例えば水溶性または油性のもの)を使用することで、切削効率が向上し、工具の寿命を延ばすことができます。切削液の選定は加工の種類に応じて適切に行うことが大切です。
精度を保つための工程管理
加工精度を保つためには、工程管理が非常に重要です。特にC3604合金のような柔らかい材料を加工する際には、精度の確保に注意を払う必要があります。- 定期的な測定とチェック: 加工中には定期的に製品の寸法を測定し、目標精度に達しているかを確認することが重要です。これにより、加工中に問題が発生していないかを早期に発見し、修正することができます。
- 機械の安定性と振動管理: 機械の安定性が悪いと加工中に振動が生じ、精度が低下します。加工機械は定期的にメンテナンスを行い、振動や不安定な動きを抑えるために機械の精度を保つことが大切です。
- 加工順序の最適化: 加工順序を最適化することで、誤差の蓄積を防ぐことができます。特に複雑な形状を加工する場合は、加工順序を慎重に決定し、最も効率的で精度を保つ方法を選ぶことが重要です。
加工後の仕上げと品質チェック
加工後の仕上げと品質チェックは、製品の品質を保証するために不可欠です。C3604合金の仕上げと品質チェックに関しては、以下のポイントを押さえることが重要です。- 仕上げ加工の実施: 加工後の仕上げ作業(バリ取り、面取り、研磨など)は、製品の外観や寸法精度を向上させるために重要です。特にC3604合金は銅合金のため、仕上げ加工を適切に行うことで、良好な表面状態を維持することができます。
- 品質検査の実施: 加工後の品質検査では、寸法精度、表面状態、材料の物理的特性が求められる仕様を満たしているかをチェックします。寸法測定機器や表面粗さ計を使用して、製品が設計通りであるかを確認し、不良品を防止することが求められます。
- 耐久性テスト: 加工後の製品が耐久性を保っているかを確認するために、耐摩耗試験や強度試験などを行うことがあります。特にC3604合金は高い機械的特性を有しているため、その性能を最大限に引き出すための品質チェックが不可欠です。
マシニング完全ガイド:プロセスから設備まで詳しく学ぶ
マシニングとは、加工プロセスにおける重要な要素の一つです。この完全ガイドでは、マシニングの基本的な概念から、実際の機械設備に至るまで、詳しく解説します。マシニングが何か、どのように機能するのか、興味を持たれた方も多いのではないでしょうか?加工業界における重要な技術であるマシニングについて、このガイドを通じて理解を深めていきましょう。
マシニングとは
マシニングの基本概念
マシニングとは、工作機械を使って金属やプラスチックなどの素材を削り出す加工方法のことです。このプロセスは、精密な部品や製品を製造する際に欠かせません。例えば、自動車や航空機のエンジン部品などがマシニングのおかげで製造されています。マシニングは、コンピューター制御された機械を使い、素材を高い精度で削り取ることができます。
マシニングの設備には、旋盤やフライス盤などがあります。これらの機械は、工業製品から日常生活に欠かせない製品まで、さまざまなものを作るのに活用されています。また、最新の技術を取り入れたマシニング設備は、効率的で精密な加工が可能です。
マシニングは製造業において重要な役割を果たしており、高い技術力と熟練した技術者が求められています。今後も技術の進化とともに、さらなる発展が期待される分野です。
マシニングの歴史と発展
マシニングは、工作機械を使って金属やプラスチックなどの素材を削る加工方法です。この技術は機械工学の中核をなすものであり、製造業において重要な役割を果たしています。マシニングの歴史は古く、工業革命以前から存在していました。しかし、近年のテクノロジーの発展により、精度や効率が飛躍的に向上しました。
現代のマシニングプロセスでは、コンピューター制御によるCNC(コンピューターナメリカルコントロール)が一般的に使われています。これにより、複雑な形状やデザインも正確に加工することが可能となりました。例えば、自動車や航空機の部品、医療機器など、さまざまな産業でマシニング技術が活用されています。
マシニングの進化は止まるところを知らず、常に新しい技術や設備が開発されています。この分野は今後もさらなる発展が期待され、製造業を支える重要な要素として今後もますます注目されるでしょう。
現代におけるマシニングの役割
現代におけるマシニングの役割は非常に重要です。マシニングとは、工作機械を使用して加工することを指します。自動車産業や航空産業など幅広い産業で利用されており、高精度で複雑な部品を製造するのに欠かせない技術です。
マシニングは、コンピュータ制御により高い精度と効率を実現します。例えば、航空機のエンジン部品や自動車のエンジンブロックなど、厳しい要件を満たす部品を製造する際に重要な役割を果たしています。
さらに、マシニング技術の進歩により、金属やプラスチックなどさまざまな素材を加工できるようになりました。このことから、製造業においてマシニングは欠かせない技術となっています。マシニングの進化は、製造業の生産性向上や製品の品質向上に貢献しています。
マシニングセンターとは
マシニングセンターの定義
マシニングセンターとは、工作機械の一種で、金属やプラスチックなどの素材を切削加工する際に使用される装置です。マシニングセンターは、工業製品や部品の製造に広く利用されており、精密な加工作業を行うことができます。
マシニングセンターは、コンピュータ制御システムによって操作され、高度な自動化が可能です。このため、効率的な生産プロセスを確保することができます。例えば、自動車産業では、エンジン部品やブレーキディスクなどの加工にマシニングセンターが活用されています。
さらに、マシニングセンターは、精度の高い加工が可能なため、航空宇宙産業や医療機器製造業など、高い品質基準が求められる分野でも重要な役割を果たしています。マシニングセンターの技術革新は、製造業全体の発展に貢献しており、今後もその重要性はますます高まることが期待されています。
マシニングセンターの種類と特徴
マシニングセンターの種類と特徴は、様々な形状やサイズで提供されています。マシニングセンターは、工作機械の一種であり、材料を削るプロセスを自動的に行うことができます。これにより、精密な部品や部品を大量に生産する際に非常に効率的です。
マシニングセンターには、垂直マシニングセンターや水平マシニングセンターなど、さまざまなタイプがあります。垂直マシニングセンターは、主軸が垂直方向に設置されており、上方向に切削される特徴があります。一方、水平マシニングセンターは、主軸が水平に配置されており、水平方向に切削される特徴があります。
これらの機械は、自動工具交換や数値制御システムを備えており、高精度で効率的な加工を実現します。マシニングセンターは、自動車産業から航空宇宙産業まで幅広い産業で利用されており、その重要性はますます高まっています。
マシニングセンターの適用範囲
マシニングセンターの適用範囲は非常に広いです。これらの装置は、金属やプラスチックなどの素材を切削するために使用されます。例えば、自動車部品や航空機部品などの精密な部品を製造する際に活用されています。マシニングセンターは、高い精度と信頼性を持ち、複雑な形状を作成することができます。
その他にも、医療機器や電子機器の製造にもマシニングセンターが欠かせません。例えば、人工関節や精密機器の部品など、高度な技術と精密さが求められる製品を生産する際に利用されます。このような分野では、最新の技術と高度な設備が求められるため、マシニングセンターが重要な役割を果たしています。
このように、マシニングセンターはさまざまな産業分野で重要な役割を果たしており、その応用範囲はますます広がっています。
マシニングセンタ完全入門
機械加工の基本
機械加工は、工業製品を作る上で欠かせない基本的なプロセスです。金属やプラスチックなどの素材を削ったり形作ったりすることで、精密な部品や製品を製造することができます。この技術は、自動車や航空機、家電製品などの製造に広く活用されています。
例えば、自動車のエンジン部品や航空機の構造部品は、機械加工によって高い精度で加工されています。これにより、安全性や性能が確保され、製品の信頼性が高まります。
機械加工には、CNC(コンピュータ数値制御)マシンなどの最新の設備が使われており、高度な技術が求められます。このような技術は、製造業の発展に不可欠であり、製品の品質向上や生産効率の向上に貢献しています。
マシニングセンタの基本操作
マシニングセンタの基本操作について解説します。マシニングとは、工作機械を使って金属加工をすることを指します。マシニングセンタは、工作を自動で行う装置であり、精密な加工が可能です。この装置は、コンピュータで制御され、設計図通りに加工を行います。
マシニングセンタは、さまざまなプロセスを経て製品を作り出します。例えば、フライス加工やボーリング加工などがあります。これらの作業が正確に行われることで、製品の精度や品質が向上します。
また、マシニングセンタは航空宇宙産業や自動車産業など、さまざまな産業で利用されています。高度な技術を要する分野であり、設備の近代化や技術者の育成が重要です。
マシニングセンタの基本操作について理解することで、製造業の技術革新や製品の品質向上に貢献することができます。
安全なマシニングセンタの使用方法
マシニングとは、工作機械を使って金属やプラスチックなどの素材を切削加工する方法です。マシニングセンタは、工作機械の一種であり、自動的に素材を加工することができます。安全なマシニングセンタの使用方法にはいくつかのポイントがあります。
まず、作業を始める前に必ずマシンの取扱説明書をよく読み、正しく使用方法を理解しましょう。安全装置の確認や作業範囲の設定など、基本的な手順を守ることが重要です。
さらに、作業中は保護メガネや手袋などの安全具を着用し、素材が飛散するのを防ぐため作業場をきれいに保ちましょう。作業後はマシンの電源を切り、周囲を整理整頓することも忘れずに行いましょう。
これらの安全対策を守ることで、マシニングセンタを安全に効果的に使用することができます。
CNC加工とは何ですか?
CNC加工の基本
マシニングとは、工作機械を使って金属やプラスチックなどの素材を削り出す加工方法のことです。CNC加工とは、コンピュータによって制御される自動化システムを使用して行われる加工方法です。この方法は、高い精度と効率性を提供し、さまざまな産業で広く利用されています。
具体的な例を挙げると、自動車産業ではエンジン部品や車体部品の製造にCNC加工が活用されています。また、航空宇宙産業では、航空機部品の精密加工にもCNC技術が重要な役割を果たしています。
要するに、マシニングは精密加工において不可欠な技術であり、CNC加工はその中でも高度な自動化を実現する手法です。産業界においてこれらの技術を理解し活用することが、競争力を維持するために重要な要素となります。
CNCマシニングプロセスの概要
CNCマシニングとは、コンピュータ制御された工作機械を使って金属やプラスチックなどの素材を削り取る加工方法のことです。このプロセスは精密で効率的な加工が可能であり、製品の精度や仕上がりに高い品質を求められる産業で広く使用されています。
マシニングのプロセスには、工具の選択、加工速度の調整、切削深さの設定など、さまざまな要素が関わります。例えば、自動車産業ではエンジン部品の製造でCNCマシニングが重要な役割を果たしています。高精度な部品を大量生産する際には、CNCマシニングが非常に効果的です。
工業界だけでなく、アートやデザインの分野でもCNCマシニングが活用され、独創的な製品の制作に役立っています。したがって、CNCマシニングは現代の製造業や創造産業において重要な技術となっています。
CNCプログラミングの基礎
CNCプログラミングは自動機械加工の基本です。この技術では、コンピュータプログラムによって工作機械が操作され、精密な部品が製造されます。CNCプログラミングは、工業製品から家庭用品まで幅広い分野で使われています。
CNCプログラミングの利点は多岐にわたります。まず、高い精度で加工が可能なため、部品の品質が向上します。また、大量生産にも適しており、効率的な生産が可能です。具体例として、自動車産業ではエンジン部品や歯車など、精密加工が求められる部品がCNCプログラミングで製造されています。
結論として、CNCプログラミングは製造業において欠かせない技術であり、日本の製造業界でも重要な役割を果たしています。技術の発展により、CNCプログラミングはますます進化し、製造プロセスの効率化に貢献しています。
初めてのマシニングセンタ導入ガイド
マシニングセンタの基礎知識
マシニングセンタは、工作機械の一種で、工作物を削るための装置です。工作物を固定し、切削工具を使って形を整えることができます。この装置は、自動的に作業を行うことができるため、生産性が向上します。
マシニングセンタは、自動車、航空宇宙、医療機器など、さまざまな産業で利用されています。例えば、自動車部品の精密加工や航空機の部品製造などに使われています。さらに、最新のテクノロジーを取り入れることで、より高度な加工が可能となり、製品の品質向上にもつながります。
マシニングセンタの基礎知識を理解することで、製造業の現場での生産性向上や製品品質の向上につながることが期待されています。工業分野において重要な役割を果たすマシニングセンタの活用は、今後さらに注目されるでしょう。
マシニングセンタの選び方
マシニングセンタの選び方は重要です。マシニングとは、工作機械を使って金属を削り出すことです。マシニングセンタは、工作機械を一つに統合し、自動で加工する装置です。選ぶ際のポイントは、まず、加工する材料や精度、加工する形状などを考えることです。たとえば、複雑な形状の部品を作る場合は、5軸マシニングセンタが適しています。また、作業スペースの広さや加工速度、精度なども重要です。さらに、メンテナンスやサポート体制も確認しましょう。適切なマシニングセンタを選ぶことで、効率的な加工が可能となります。このように、マシニングセンタの選び方をしっかり考えることが重要です。
導入時のチェックリスト
マシニングとは、工作機械を使って金属やプラスチックなどの素材を切削加工する製造技術のことです。この工程は、自動車部品や航空機部品、家電製品など、さまざまな製品の製造に欠かせない重要なプロセスです。
マシニングのプロセスには、旋削、フライス、ボーリングなどがあります。例えば、フライスは工作物を回転させながら切削する方法で、高い精度が求められる場面で利用されます。また、ボーリングは穴を開ける加工方法で、エンジン部品やベアリングなどの製造に使用されます。
マシニングでは、CNC(コンピュータ数値制御)システムを使用することで、高度な自動化が可能となり、生産性が向上します。今後も技術の進化により、より精密で効率的なマシニングが期待されています。
CNC機械加工アクリルの完全ガイド
アクリルとは
マシニングとは、工作機械を用いて金属やプラスチックなどの材料を削る加工方法のことです。このプロセスは工業製品や部品の製造に広く利用されています。
マシニングの主な利点の1つは、高い精度で加工が可能であることです。例えば、自動車や航空機などの高度な技術が必要な製品の製造において、マシニングは不可欠な技術となっています。
また、マシニングは大量生産にも適しており、短時間で多くの製品を作成することができます。これにより、生産性を向上させることができ、企業の競争力を高めることができます。
さらに、マシニングは材料の種類によらず幅広く対応可能であり、金属だけでなくプラスチックやセラミックスなどの加工も可能です。このような柔軟性が、マシニングの魅力の一つと言えます。
アクリルのCNC機械加工
マシニングとは、工作機械を使って金属やプラスチックなどの素材を切削加工する方法です。アクリルのCNC機械加工は、コンピュータ制御による精密な加工技術の一つで、アクリル素材を使った製品を作る際に重要です。この方法は、設計図面をコンピュータに入力し、機械に加工を指示することで、高い精度で加工することができます。
アクリルのCNC機械加工は、広告業界や工業製品の製造業界などで幅広く活用されています。例えば、看板やディスプレイ、部品加工などによく使われており、綺麗な仕上がりや高い精度が求められる製品に適しています。
このように、マシニングの一環としてのアクリルのCNC機械加工は、製品の精度や品質を向上させるために欠かせない技術と言えます。
アクリル加工における注意点
マシニングとは、工作機械を使用して加工することを指します。このプロセスは、金属やプラスチックなどの素材を削ったり形作ったりする際に利用されます。例えば、車のエンジン部品や電子機器の筐体など、様々な製品の製造に使われています。
マシニングには、CNC(コンピュータ数値制御)マシンを使用する自動化された方法や、従来の手動操作による方法などいくつかの手法があります。この技術は、精密な加工が求められる産業分野で広く利用されています。
注意点として、適切な切削速度や刃先の選定、加工時の冷却や潤滑などが重要です。これらの要素を適切に管理することで、素材への負担を軽減し、高品質な加工を実現することが可能となります。マシニングは製造業において欠かせない技術であり、その適切な理解と実践が重要です。
マシニングプロセスから設備まで
マシニングプロセスの流れ
マシニングは工作機械を使って金属やプラスチックなどの素材を切削加工するプロセスです。このプロセスは、工作物を所定の寸法や形状に加工する際に使用されます。まず、CAD(コンピュータ支援設計)によってデザインされた図面を基に、CNC(コンピュータ数制御)システムが工作機械を制御します。
マシニングは、自動車部品や航空機部品など、精密なパーツを作る際に重要な役割を果たしています。例えば、エンジン部品や歯車などの部品がこれに該当します。これらの部品は、高い精度で加工される必要があります。
さらに、マシニングは製造業において効率的な生産を実現するためにも重要です。自動化されたマシニングプロセスによって、短時間で多くの部品を生産することが可能となります。このように、マシニングは製造業において欠かせない技術となっています。
マシニングに必要な設備
マシニングに必要な設備は、高度な加工を可能とする機器や工具が含まれます。例えば、コンピュータ数値制御(CNC)マシンは、精密な金属やプラスチック部品を作成するのに必要不可欠です。これらの機械は、プログラムされた指示に基づいて素材を切削、削り取ることができます。加工には、刀具や刃物を保持するための専用のホルダーや治具も重要です。さらに、冷却や潤滑を行うための装置も必要です。これらの設備が整っていることで、効率的かつ正確な加工が行われ、製品の品質が向上します。マシニングにおいては、適切な設備を整備することが大切です。
設備のメンテナンスとトラブルシューティング
マシニングは、工作機械を使って金属やプラスチックなどの素材を削る加工方法のことです。このプロセスでは、コンピューター制御された機械が精密な作業を行い、製品を仕上げます。マシニングは、自動車部品や航空機の部品など、さまざまな工業製品の製造に広く使われています。
マシニングの設備のメンテナンスとトラブルシューティングは、製品の品質や生産性を維持するために重要です。例えば、切削工具の研ぎ直しや交換、潤滑油の定期交換などが挙げられます。また、機械の異常や故障が発生した際には、すばやく原因を特定し修理することが必要です。
これらの対応を適切に行うことで、マシニング設備の効率を向上させることができ、生産ライン全体の安定した稼働を確保することができます。その結果、製品の品質向上や生産コストの削減につながるでしょう。
マシニング技術の応用
複雑形状の加工方法
マシニングは、工作物を形作るための重要なプロセスです。工作物に複雑な形状を与えることができ、精密な加工が可能となります。例えば、複雑な部品や金型を作る際にマシニングが活躍します。工作機械によって切削や穴あけなどが行われ、高い精度で仕上げられます。特に航空宇宙産業や自動車産業などの分野では、マシニングが欠かせない技術として重要視されています。さらに、最新のテクノロジーを導入することで、効率的な加工が可能となります。これによって、製品の品質向上や生産性の向上が期待されます。マシニング技術は、産業界において重要な役割を果たす技術であり、その進化は今後も続くことが予想されます。
高精度加工のための技術
マシニングは、高精度な加工を行うための技術です。このプロセスは、コンピューター制御を用いて金属やプラスチックなどの素材を削り取り、所定の形状に加工する方法です。例えば、自動車や航空機の部品製造など、幅広い産業で利用されています。マシニングは、精密さと効率性に優れており、微細な部品や複雑な形状を作成することが可能です。技術の進歩により、より高速かつ正確な加工が可能になり、製品の品質向上に貢献しています。さらに、最新のマシニング設備は、省エネや環境負荷の低減にも配慮して設計されています。これにより、製造プロセス全体が持続可能性を考慮したものとなっています。
マシニングと他の製造技術の組み合わせ
マシニングと他の製造技術の組み合わせは、製造業において重要な役割を果たしています。マシニングは、精密加工に適した技術であり、精密な部品や部品を効率的に製造するのに最適です。加工対象の材料や形状によって、マシニングだけでは難しい場合もあります。そのため、他の製造技術と組み合わせて使われることがあります。
たとえば、3Dプリンターとマシニングを組み合わせることで、複雑な形状の部品を効率的に製造することが可能となります。また、レーザー加工やエッチングなどの技術と組み合わせることで、さらに高度な加工が実現できます。マシニングと他の製造技術を組み合わせることで、より効率的で緻密な製品製造が可能となります。このように、マシニングは他の製造技術と組み合わせることで、さまざまな産業分野で活躍しています。
マシニングの未来と技術革新
マシニング技術の最新動向
マシニング技術の最新動向についてご紹介します。マシニングとは、工作機械を利用して金属やプラスチックなどの素材を削り出す加工方法のことです。最新の技術では、コンピューター制御により高精度な加工が可能となり、製品の品質向上や生産効率の向上が図られています。
近年、マシニングの技術はさらに進化し、3Dプリンティングと組み合わせることで複雑な形状の部品も効率的に製造できるようになりました。例えば、航空機や自動車産業では、高度なマシニング技術が求められており、燃費や安全性の向上に貢献しています。
このように、マシニング技術の最新動向は産業界に革新をもたらし、製造業の発展に大きく寄与しています。今後もさらなる技術革新が期待される分野です。
産業におけるマシニングの新たな役割
マシニングは、製造業において重要な役割を果たしています。工場での生産ラインにおいて、金属やプラスチックなどの素材を加工する際に使用される方法です。例えば、自動車産業や航空産業において、エンジン部品や航空機部品などの精密加工に欠かせない技術です。
マシニングの工程は、コンピュータ制御を用いて素材の形状を加工することができます。このような高度な技術は、製品の品質や精度を向上させることに貢献しています。さらに、製造業における効率的な生産を可能にし、市場競争力を維持する上でも重要な要素となっています。
マシニング技術の進化は、製造業全体の生産性向上につながることが期待されています。このように、マシニングは製造業における新たな役割を果たし、技術の発展と産業の発展に貢献しているのです。
持続可能なマシニングへの取り組み
マシニングは、工作機械を用いて金属やプラスチックなどの素材を切削加工するプロセスです。この技術は製造業において重要であり、製品の形状を作り出す際に欠かせないものです。マシニングは高い精度と効率性が求められるため、最新の設備や技術が導入されています。
近年、マシニングにおいて持続可能な取り組みが注目されています。環境への配慮やエネルギー効率などが重要視され、省エネの取り組みや再利用可能な材料の使用などが増加しています。例えば、新しい素材を使用して切削時の廃棄物を減らす取り組みや、省エネ型の機械を導入することで環境負荷を低減することが挙げられます。
これらの取り組みにより、マシニング業界は持続可能な方向へと進化を遂げています。環境への配慮やエネルギー効率の向上が進むことで、製造業全体の持続可能性を高める一助となることが期待されています。
実践!マシニングセンタの活用
初心者向けプロジェクト例
マシニング完全ガイド:プロセスから設備まで詳しく学ぶ
マシニングとは、工作機械を使って金属やプラスチックなどの素材を形作るプロセスです。この技術は製造業で幅広く利用されており、自動車や航空機、医療機器などの製造に欠かせないものです。
マシニングのプロセスは、まず設計図面を元に加工する素材を選定し、工作機械で切削や削り取りを行います。例えば、自動車のエンジン部品や航空機のフレームなど、高精度な加工が求められます。
マシニングには様々な種類があり、旋盤やフライス盤、ボール盤などが一般的です。これらの設備を適切に選定し、プロセスを正確に実行することが製品の品質向上につながります。
マシニングの理解を深めることで、製造業における技術革新や生産性向上に貢献することができるでしょう。マシニングの知識を習得することで、製造現場での活躍の幅がさらに広がること間違いありません。
中級者向けのチャレンジ
マシニングとは、工作機械を使用して金属やプラスチックなどの素材を削る加工技術のことです。このプロセスは、精密な部品や製品を作るのに重要です。マシニングは、自動車部品や航空機部品、医療機器などさまざまな産業で使われています。例えば、エンジン部品や歯科用具などが挙げられます。
マシニングを行うためには、専用の設備が必要です。数値制御(CNC)マシンや旋盤、フライス盤などが一般的に使用されます。これらの機器を操作するためには、専門知識や技術が必要ですが、訓練を積めば誰でも上達することが可能です。
マシニングの技術を習得することで、製造業や産業界でのキャリアパスを広げることができます。高度な技術と精度が求められるため、専門家としての地位を築くことができるでしょう。マシニングは、製造業において欠かせない技術であり、その重要性は今後も高まることが予想されます。
専門技術の習得と活用
マシニングとは、金属やプラスチックなどの素材を工作するための専門技術のことです。この技術を習得し、活用することは製造業において重要です。例えば、自動車や航空機の部品製造に幅広く利用されています。マシニングは、精密な加工が求められる産業で欠かせない技術と言えます。
専門技術を持つマシニング技術者は、CAD/CAMソフトウェアを使用して設計図面を読み取り、必要な工具や材料を選定します。その後、旋益やフライス盤などの機械を操作して加工作業を行います。このような専門技術を活用することで、高品質な部品を効率的に製造することが可能となります。
マシニングの技術は日々進化しており、より効率的かつ精密な加工が求められています。そのため、専門技術の習得と活用は、製造業における競争力を高めるために重要な要素となっています。
まとめ
マシニングとは工作機械を用いて金属を形作る製造プロセスのことを指します。このプロセスでは、自動化された工具や機械を用いて金属を削る、切る、あるいは形作ることが可能です。マシニングには様々な種類があり、CNC(Computer Numerical Control)マシニングやレーザーカッティングなどがあります。これらの技術を習得することで、製造業における生産性や精度を向上させることができます。また、新たな設備や技術の導入によって、マシニングのプロセス自体も進化を遂げています。
真鍮切削のコツを伝授!美しい仕上がりを実現する方法
真鍮を切削する際に美しい仕上がりを実現するには、何かコツが必要ですよね。そこで、この記事では、真鍮切削のテクニックをご紹介します。真鍮とは素敵な素材であり、その魅力を最大限に引き出すためには、正しい切削方法が欠かせません。本稿では、真鍮切削の基本から応用までを丁寧に解説します。美しい加工を実現したい方、ぜひご覧になってください。
真鍮切削の基礎知識
真鍮とは – 物質の特性と概要
真鍮は、銅と亜鉛からなる合金であり、金属加工において広く使用されています。真鍮は耐食性が高く、美しい光沢を持ち、加工しやすい特性があります。真鍮切削は、美しい仕上がりを実現するために重要です。切削する際に注意すべきポイントは、適切な切削速度と切削深さを確保することです。また、刃先の形状や刃先の素材も切削品質に影響を与えます。例えば、スピンドル速度を調整することで真鍮の切削品質を向上させることができます。真鍮切削の技術を磨くことで、綺麗な仕上がりを実現し、作業効率も向上させることができます。真鍮切削は、正しい方法で行うことで、高品質な加工が可能となります。
真鍮の加工しやすさについて
真鍮は加工しやすく、美しい仕上がりを実現することができます。真鍮は硬くても柔らかいため、切削や加工が比較的容易です。例えば、旋盤を使用して円筒形に加工する際、真鍮は滑らかに削られるため、綺麗な仕上がりが期待できます。また、フライス加工などでも真鍮は細かい部分まで精密に加工できます。
真鍮は耐食性や耐久性にも優れており、装飾品や工芸品など幅広い用途で利用されています。例えば、時計や楽器などの部品、建築材料、インテリアデザインにも使われています。そのため、真鍮を切削する際には、正確な計画と適切な工具を使うことが重要です。
真鍮の特性を理解し、適切な切削や加工方法を使うことで、美しい仕上がりを実現することができます。そのため、真鍮加工の際には、素材の特性を考慮しながら丁寧に作業を行うことが大切です。
真鍮切削加工の一般的な用途
真鍮切削は、さまざまな用途で活躍する加工方法です。真鍮は美しい光沢と耐久性を持ち、インテリアや装飾品、機械部品など幅広い分野で利用されています。例えば、真鍮製の飾り板やインテリア雑貨は高級感があり、家具や照明器具にもよく使われます。また、機械部品では、真鍮の耐食性や加工しやすさから、精密機器や精密部品にも多く使われています。真鍮切削には、高い技術と知識が求められますが、熟練した職人の手にかかれば、美しい仕上がりを実現することができます。真鍮切削は、その優れた特性から、さまざまな産業分野で重要な役割を果たしています。
真鍮の加工時の注意点
切削工具の選定
真鍮を切削する際に美しい仕上がりを実現するためには、適切な切削工具の選定が重要です。真鍮は柔らかい金属であり、正しい工具を使わないと加工がうまくいきません。例えば、ハイスや硬質合金の刃物が適しています。これらの刃物は真鍮の特性に合わせて設計されており、切削時に熱や摩擦をうまくコントロールすることができます。
また、刃物の選定だけでなく、適切な切削速度や切削量も重要です。速度が速すぎると刃物がすぐに摩耗してしまい、逆に遅すぎると切削不良が生じます。適切な条件で加工することで、美しい仕上がりが得られるのです。
したがって、真鍮を切削する際には適切な切削工具を選び、適切な条件で加工することがポイントです。これらのポイントを押さえれば、美しい仕上がりを実現することができます。
切削条件の設定
真鍮を切削する際に、美しい仕上がりを実現するためには、適切な切削条件の設定が重要です。まず、切削速度や切削深さ、切削量などを適切に設定することが必要です。これにより、真鍮を綺麗に加工することが可能となります。
理由は、適切な切削条件を設定することで、切削時の摩擦や熱の発生を抑えることができ、加工面の質を向上させることができるからです。
具体的な例を挙げると、切削速度が速すぎると真鍮が焼けてしまい、加工面が荒れてしまう可能性があります。一方、速度が遅すぎると切削不良が生じる恐れがあります。適切な切削条件を設定することで、美しい仕上がりを実現することができます。
したがって、真鍮切削においては、適切な切削条件の設定が重要であり、これをしっかりと把握することが美しい加工面を実現する秘訣となります。
潤滑と冷却の重要性
真鍮切削において、潤滑と冷却は非常に重要です。切削時に適切な潤滑剤を使用することで、切削過程での摩擦を減らし、工具の寿命を延ばすことができます。また、冷却効果により加工物の温度上昇を抑え、精度の高い加工が可能となります。例えば、真鍮は高温で加工すると変色してしまうため、適切な冷却を行うことで美しい仕上がりを保つことができます。
さらに、潤滑と冷却は加工時の切りくず除去や加工表面の仕上げにも影響を与えます。適切な潤滑と冷却を行うことで、切削時の作業効率が向上し、加工物の品質も向上します。したがって、真鍮切削においては、潤滑と冷却を適切に行うことが美しい仕上がりを実現するために欠かせないポイントと言えます。
真鍮加工時の一般的な問題と対策
真鍮を切削する際に一般的に発生する問題とその対策についてお伝えします。真鍮は美しい仕上がりを実現できる素材ですが、切削時に注意が必要です。まず、真鍮は柔らかい金属であり、切削時に振動や歪みが生じやすい特徴があります。これを避けるためには、切削速度を適切に設定し、刃先を鋭利に保つことが重要です。さらに、切屑や切削油の適切な管理も欠かせません。これらの対策を講じることで、真鍮の切削作業を効果的に行うことができます。美しい仕上がりを実現するために、真鍮切削時の問題に対処するポイントをしっかり押さえて作業に臨みましょう。
真鍮切削の実践的加工方法
切削プロセスの計画
真鍮を切削する際のコツを伝授します。美しい仕上がりを実現するためには、まず切削プロセスを計画することが重要です。なぜなら、正確な計画がなければ、素材が損傷する可能性があるからです。例えば、適切な工具や刃物の選択が必要です。次に、適切な切削速度や切削深さを設定します。これにより、真鍮がスムーズに切られ、仕上がりが美しくなります。さらに、切削中には冷却液を使うことも重要です。冷却液がないと素材が過熱し、切削精度が低下する可能性があります。以上のポイントを抑えることで、真鍮の切削作業を効果的に行い、美しい仕上がりを実現できます。
ラフィングとフィニッシングの違い
真鍮切削のポイントをマスターし、美しい仕上がりを実現しましょう。真鍮は金属の一種であり、切削に特定の技術が必要です。まず、切削の理由を理解することが重要です。真鍮は柔らかい金属であり、切削時に熱を発生しやすいため、適切な冷却液を使うことが必要です。さらに、切削工具の選択も重要です。硬度と形状に応じて適切な工具を選ぶことで、切削作業が効率的に行えます。
具体的な例を挙げると、適切な刃先やスピードを選ぶことで、真鍮の切削作業がスムーズに進行します。また、切削面の仕上げにも気を配ることで、美しい仕上がりを実現できます。これらのポイントを押さえることで、真鍮切削において上手な技術を身につけることができます。
真鍮の適切なラフィング方法
真鍮を切削する際、美しい仕上がりを実現するためには、適切なラフィングが重要です。まず、切削する前に真鍮の表面をきれいに洗浄し、油や汚れを取り除きます。次に、適切な工具を使用してラフィングを行います。ラフィングは、真鍮の表面を滑らかにし、仕上がりを美しくするための作業です。適切な圧力とスピードで工具を操作することがポイントです。
例えば、真鍮の切削には専用のラフィングツールを使用することで、効果的な仕上がりを実現できます。また、適切な冷却液を使うことで、切削時の摩擦熱を抑えることができます。これにより、真鍮の変色や歪みを防ぎ、綺麗な仕上がりを保つことができます。適切なラフィング方法を実践することで、真鍮をきれいに切削することができ、美しい仕上がりを実現することができます。
美しい仕上がりを得るフィニッシング技術
真鍮切削のコツを伝授します。美しい仕上がりを実現するためには、正しいフィニッシング技術が肝心です。まず、切削時には適切な刃物を使用して、真鍮の硬度に合った工具を選びましょう。次に、切削速度や切削量を適切に設定することが重要です。適切なスピードや深さで切削することで、仕上がりにムラが生じず、美しい表面を確保できます。
さらに、切削時には冷却液を使用することもおすすめです。冷却液を使うことで熱による変形や加工精度の低下を防ぎ、作業効率を向上させます。最後に、切削後は適切な仕上げ工程を施して、真鍮の美しい輝きを引き出しましょう。これらのポイントを抑えることで、美しい仕上がりを得ることができます。
真鍮加工のための工具と機械の選び方
工具の材質と形状
真鍮切削のコツを伝授します!美しい仕上がりを実現するためには、工具の材質と形状が重要です。真鍮は柔らかい金属であり、切削時に熱を生じやすい特性があります。したがって、切削用の工具は熱に強い高速度鋼や硬質合金などが適しています。
工具の形状も重要です。例えば、切削刃の角度や刃先の形状が切削時の仕上がりに影響を与えます。適切な刃形状を選ぶことで、真鍮の削りカスやバリを最小限に抑え、美しい加工面を実現できます。
さらに、切削時の切削速度や切削量も重要です。適切な速度と量を設定することで、真鍮の切削時にかすやほこりが発生せず、綺麗な仕上がりを実現できます。
これらの要点を抑えて、適切な工具と切削条件を選ぶことで、美しい真鍮加工を実現できます。
CNC機械と従来の機械
真鍮切削は、美しい仕上がりを実現するための重要な工程です。真鍮は加工が難しい素材であり、正しい切削方法が必要です。まず、切削速度を適切に設定することが重要です。高速すぎると工具がすぐに摩耗してしまいますが、低速だと切削面に悪影響を与えます。次に、適切な切削油や冷却液を使用することも重要です。これにより摩擦を減らし、切削工程をスムーズに行うことができます。さらに、適切な工具や切削条件を選択することで、作業効率が向上し、美しい仕上がりを実現できます。真鍮切削には注意が必要ですが、正しい方法を取ることで良い成果を得ることができます。
切削速度と送り速度の調整
真鍮を切削する際に重要な要素は、切削速度と送り速度の調整です。切削速度が速すぎると刃が摩耗しやすくなり、逆に遅すぎると切削面が荒れてしまいます。同様に、送り速度が速すぎると刃先に過度の摩擦が生じ、逆に遅すぎると切屑が詰まってしまいます。例えば、真鍮の場合、切削速度は適切に設定することで美しい仕上がりを実現できます。切削速度と送り速度を適切に調整することで、真鍮を効率よく加工することができます。これらの工程に注意を払うことで、高品質な製品を生産することが可能となります。
切削技術の応用とトラブルシューティング
複雑な形状の切削
真鍮の切削は、美しい仕上がりを実現するためのコツがあります。複雑な形状の真鍮を切削する際には、まず適切な刃物を選ぶことが重要です。硬さと扱いやすさを兼ね備えた刃物を選ぶことで、精密な切削が可能となります。さらに、適切な切削速度や刃の角度を設定することも大切です。正確な設定によって、切削時の振動や摩擦を最小限に抑え、綺麗な仕上がりを実現できます。
例えば、複雑なデザインが施された真鍮の装飾品を制作する場合、適切な刃物を使い、正確な切削速度で加工することが必要です。これにより、細部まで美しい仕上がりを確保することができます。真鍮切削においては、慎重な設定と注意深い作業が重要です。【MADE UP EXAMPLE】
真鍮加工における精度の管理
真鍮切削において、美しい仕上がりを実現するためには、精度の管理が重要です。切削作業を行う際には、正確な作業手順と適切な切削工具を使用することがポイントです。例えば、適切な刃先形状を選択したり、適切な刃先加工をすることで、切削時の振動を軽減して精度を向上させることができます。
さらに、切削速度や切削深さなどのパラメーターも適切に設定することで、仕上がりの品質を向上させることができます。また、冷却材の適切な使用や切削面の清掃も忘れてはいけません。これらの工夫により、真鍮切削における精度の向上と美しい仕上がりを実現することが可能です。
切削中のトラブルとその解決策
真鍮切削のコツを伝授!美しい仕上がりを実現する方法
真鍮を切削する際に生じるトラブルを解決するためのコツをお伝えします。真鍮は美しい仕上がりが特徴ですが、切削時に問題が起こることもあります。
まず、切削速度を適切に設定することが重要です。速度が速すぎると真鍮が熱くなり、切削面が粗くなる可能性があります。逆に速度が遅すぎると切削刃が詰まりやすくなります。適切な切削速度を選ぶことがキーです。
また、切削油の使用も効果的です。切削油を適量使用することで切削時の摩擦を減らし、切り屑の排出をスムーズにします。
これらのコツを実践することで、真鍮切削において美しい仕上がりを実現することができます。
安全で効率的な真鍮切削作業のために
安全な作業環境の構築
真鍮切削において美しい仕上がりを実現するためには、安全な作業環境の構築が不可欠です。切削作業中は、顔や手を保護するために安全メガネや手袋を着用することが重要です。また、切削機械の取り扱いには専門知識と経験が必要なため、未経験者は指導者のもとで作業を行うことが大切です。具体的な例を挙げると、切削作業での金属の飛散を防ぐために作業エリアは清潔に保ち、周囲には安全柵を設置して作業者の安全を確保します。安全対策を怠らず、正確かつ安全に作業を行うことで、美しい仕上がりを実現できます。
効率的な作業フローの計画
真鍮切削のコツを伝授!美しい仕上がりを実現する方法
真鍮を切削する際に美しい仕上がりを得るためには、いくつかのポイントがあります。まず、切削工程に入る前にしっかりと計画を立てることが重要です。作業フローを効率的に進めるために、切削工具や加工方法を選定しましょう。例えば、適切な刃先形状や刃先角度を選ぶことで、切削時の振動を抑えて綺麗な仕上がりを実現できます。
さらに、適切な切削速度や切りくず排出方法も重要です。適切な切りくず排出によって刃先や加工面がキズ付かず、作業効率が向上します。
これらのコツを実践することで、真鍮切削において美しい仕上がりを実現し、満足のいく成果を得ることができます。
真鍮切削のための保守とメンテナンス
真鍮切削を行う際に美しい仕上がりを実現するためには、適切な保守とメンテナンスが欠かせません。真鍮は美しい光沢が特徴ですが、切削時には注意が必要です。切削工程での冷却や潤滑が十分でないと、切削面が荒れてしまうことがあります。適切な潤滑剤や冷却液を使用し、正確な切削速度と刃先の選定が重要です。
例えば、真鍮の切削時に刃先の温度が上昇しすぎると、刃先が焼損してしまうことがあります。これを防ぐためには、適切な冷却方法を取ることで刃先を保護することができます。また、切削条件や工具の状態を確認しながら作業を進めることで、美しい仕上がりを実現することができます。真鍮切削においては、適切な保守とメンテナンスを行うことで、高品質な加工が可能となります。
まとめ
真鍮の切削作業には、適切な工具と技術が必要です。切削時には適切な刃物と切削速度を選ぶことが重要です。また、適切な冷却液を使用して工具と切削面を冷やすことで、美しい仕上がりを実現することができます。正しい切削技術を身につければ、真鍮の切削作業をより効率的かつ精密に行うことができます。
工作機械を使った真鍮切削のテクニックとその注意点
工作機械を使った真鍮切削のテクニックとその注意点について、興味を持っている方も多いことでしょう。工作機械を駆使して真鍮を加工する魅力は、その精密さや緻密さにあります。この記事では、真鍮切削におけるテクニックや注意点について詳しく探求していきます。真鍮という素材の特性を生かしながら、工作機械を駆使してどのように切削を行っていくのか、そのポイントを解説していきます。ぜひ、真鍮加工に興味がある方は、この記事を参考にしてみてください。
真鍮切削の基本
真鍮とは:特性と利点
真鍮は、銅と亜鉛の合金であり、金属の一種です。その特性として、真鍮は錆びにくく、耐久性に優れています。真鍮は切削加工に適しており、工作機械を使用して精密な加工が可能です。切削技術によって、真鍮の素材から様々な形状を作ることができます。
真鍮切削の際に注意すべき点は、適切な刃物や切削速度、切削深さを選定することです。切削時に過度な熱が発生すると、真鍮が変形しやすくなるため、適切な冷却や切削液の使用が重要です。また、正確な測定や機械のメンテナンスも欠かせません。
真鍮切削を行う際には、これらのポイントに留意することで、効率的かつ精密な加工が可能となります。工作機械を使った真鍮切削は、製造業などさまざまな分野で重要な技術となっています。
切削加工の原理
工作機械を使った真鍮切削のテクニックとその注意点
真鍮は硬い金属であり、切削加工の原理を理解することが重要です。工作機械を使用して真鍮を切削する際には、適切な工具と刃先形状を選ぶことがポイントです。例えば、硬い真鍮を切削する場合は、刃先に適切な角度と刃先形状を持つ工具を使用することが効果的です。
さらに、切削速度や刃先の冷却、適切な切削量なども重要な要素です。適切な切削速度を設定し、刃先を過熱させないように冷却することで切削精度を向上させることができます。
注意点としては、真鍮の切削時に発生する切屑や粉塵を適切に処理することが重要です。安全性を考慮し、切削作業を行う際には保護メガネや保護マスクを着用するようにしましょう。これらのテクニックと注意点を守ることで、効果的かつ安全な真鍮切削が可能となります。
真鍮切削の一般的な用途
真鍮切削は、工作機械を使って真鍮を削る技術です。真鍮切削の一般的な用途は、金属加工や製造業における部品加工などです。真鍮は耐食性や導電性に優れており、さまざまな産業で広く使用されています。例えば、自動車部品や電気機器の部品などが挙げられます。
真鍮切削の際には、注意点もあります。工具の刃を適切に研ぐことや適切な冷却方法を選択することが重要です。また、加工速度や切削深さなどのパラメーターを適切に設定することも、品質と効率の向上につながります。
結論として、真鍮切削は重要な工程であり、正確なテクニックと適切な注意を払うことで、効果的に素材を加工することができます。
真鍮切削のテクニック
適切な工具の選択
工作機械を使った真鍮切削において、適切な工具の選択は非常に重要です。適切な工具を使用することで作業効率が向上し、切削品質が向上します。例えば、硬度の高い真鍮を切削する場合は硬度に耐えられる適切な切削工具を選択することが重要です。また、切削速度や切削深さに応じて適切な工具を選ぶことも必要です。適切な工具の選択を怠ると、作業効率が低下し、加工精度が損なわれる可能性があります。したがって、真鍮切削を行う際には、適切な工具の選択に注意することが重要です。
切削条件の設定
工作機械を使った真鍮切削のテクニックとその注意点
切削条件の設定は、素材と工具に合わせて適切に行うことが重要です。例えば、真鍮は柔らかい素材であるため、適切な刃先形状や切削速度を選ぶ必要があります。加工中に過度の摩擦や熱が発生すると、切削品質が低下し、工具の寿命も短くなってしまいます。
切削条件を設定する際には、刃先形状や切削速度の他に、適切な切削量や切屑排出方法も考慮する必要があります。また、工作機械の適切なメンテナンスや冷却液の効果的な使用も重要です。
真鍮切削においては、切削条件を適切に設定することで加工効率を向上させると共に、加工精度や工具の寿命を確保することができます。適切な切削条件の設定に注意して、安全かつ効率的な作業を行いましょう。
冷却液の使用法
工作機械を使った真鍮切削のテクニックとその注意点
真鍮は耐久性が高く、加工性も良い素材です。真鍮を切削する際に重要なのは、適切な切削速度や切削深さを選ぶことです。工作機械を使用する際は、冷却液の使用も欠かせません。冷却液は切削時に熱が発生するのを抑え、工具や加工面の摩耗を軽減します。
切削時には、適切な冷却液の量や適正な供給方法を確保することが重要です。過剰な冷却液の使用は加工面の質を損なう可能性があるため、適量を使用するように注意しましょう。また、工作機械の取扱いには注意が必要であり、安全装置の確認や指定された作業手順に従うことが重要です。
真鍮切削においては、適切な技術と注意を払うことで、高品質な加工結果を得ることができます。
工作機械の調整
工作機械を使った真鍮切削のテクニックとその注意点
真鍮切削を行う際、工作機械の調整が重要です。切削の精度や効率を向上させるために、機械の調整を適切に行うことが必要です。
まず、切削速度や切削量を適切に設定することが重要です。真鍮は柔らかい材料であり、高速で切削すると摩擦熱によって変形しやすくなります。適切な切削速度と切削量を設定することで、切削時の摩擦や熱を抑え、品質の向上につながります。
さらに、切削刃の研磨や冷却液の使用など、細かな調整も大切です。切削刃の状態や冷却液の供給量を適切に管理することで、切削時の摩耗や熱を軽減し、切削面の仕上がりを向上させることができます。
工作機械の調整には細かな点が多く、慎重な作業が求められます。適切な調整を行うことで、真鍮切削において効率的かつ品質の高い加工が可能となります。
真鍮旋盤加工のコツ
旋盤操作の基本
工作機械を使った真鍮切削のテクニックとその注意点
真鍮を切削する際には、正しいテクニックと注意が必要です。まず、切削を行う前に適切な工具を用意し、切削速度や刃の選定を慎重に行うことが重要です。続いて、適切な切削油を使用して、加工時の摩擦を減らすことがポイントです。これにより切削表面の仕上がりを向上させることができます。
例えば、真鍮製の歯車を旋盤で加工する際には、適切な速度と刃の選定が重要です。切削時には、適度な圧力を加えながら安定した加工を心掛けましょう。また、切削終了後には作業場をきれいに片付けることも大切です。
これらのテクニックと注意点を守ることで、真鍮切削作業をスムーズに行うことができます。安全を確保しつつ、品質の高い加工を目指しましょう。
真鍮加工向け旋盤の特徴
真鍮切削において、工作機械として旋盤が広く利用されています。真鍮は切削しやすく、精密な加工が可能なため、旋盤を使用することで高品質な加工が行えます。例えば、真鍮の棒を旋盤で回転させながら切削することで、きめ細かい部品を作ることができます。
注意点としては、真鍮は軟らかい金属であるため、適切な工具や切削条件を選択することが重要です。刃先が磨耗している工具を使用すると、加工精度が低下したり、切削音が大きくなる可能性があります。切削条件も適切に設定することで、加工効率が向上し、加工面の仕上がりも良くなります。
真鍮切削においては、旋盤を使用する際に適切な工具と切削条件を選択することで、高品質な加工が可能となります。
加工精度を高める方法
真鍮を切削する際に工作機械を使用する際、加工精度を高める方法は慎重に行うことが重要です。まず、正確な寸法を得るために、適切な刃物や工具を選択することが必要です。また、適切な切削速度や刃先形状を選定することも肝要です。例えば、適切な冷却液の使用や加工時の振動を抑えることで、切削時の振れを最小限に抑えることができます。
さらに、真鍮の材質特性を考慮して適切な切削条件を設定することも大切です。例えば、真鍮は柔らかい材料であるため、過剰な力を加えると変形や割れのリスクがあります。したがって、正確な切削条件を選定し、適切な工具の保守管理を行うことで、加工精度を高めることができます。
旋盤加工の効率化
工作機械を使った真鍮切削のテクニックとその注意点
真鍮切削は、工作機械を使用する際に重要なテクニックと注意点があります。例えば、適切な切削速度や刃物の選択がポイントです。高い切削速度を選ぶと真鍮が過熱して変色する可能性がありますが、低すぎる速度だと切削がうまく進まないことがあります。刃物の選択も重要で、適切な刃物を選ぶことで切削の精度や寿命が向上します。
さらに、真鍮は柔らかい素材であり、振動が起こりやすいため、適切な固定や工具の選択も重要です。加工中に適切な冷却を行うことで切削面の仕上がりを向上させることもできます。これらの注意点を遵守することで、より効率的に真鍮切削を行うことができます。
真鍮加工時の注意点
切削速度と給進の調整
真鍮切削において重要なテクニックは、切削速度と給進の調整です。切削速度が速すぎると刃物の寿命が短くなり、正確な加工が難しくなります。逆に遅すぎても切削が不十分になります。給進は、加工面仕上げや加工効率に直結します。適切な給進を設定することで、切削時間を短縮し、品質の向上が期待できます。例えば、真鍮の切削では、切削速度を適正に設定して強度を損なわずに効率良く加工することが重要です。切削する材料や刃物の種類によって最適な条件が異なるため、事前に確認しておくことが大切です。適切なテクニックを身につけることで、真鍮切削で高品質な加工を実現できます。
バリ取りと仕上げ
工作機械を使用して真鍮を切削する際に重要なテクニックと注意点があります。真鍮は加工が難しい素材の一つであり、適切な工具や刃物を選ぶことが重要です。切削速度や切削深さなど、加工条件を適切に設定することも肝要です。
例えば、刃先の角度やクリアランス角を正しく設定することで、真鍮の切削性能を最大限に引き出すことができます。また、工作機械の適切なメンテナンスや冷却液の使用も切削品質向上につながります。
このように、正しいテクニックと適切な条件設定を行うことで、真鍮の切削作業を効果的に行うことができます。確実な加工品質を求める際には、技術者の知識と経験が重要になります。
加工時の安全対策
真鍮切削を行う際には、工作機械を使用することが一般的です。しかし、この作業は注意が必要です。まず、加工時の安全対策をしっかりとることが重要です。切削時には、しっかりとした保護メガネや手袋を着用し、怪我や事故を防ぎましょう。
また、機械の取り扱いには専門知識と経験が必要です。操作マニュアルを正しく理解し、機械の故障やトラブルを未然に防ぐことが大切です。例えば、機械のメンテナンスや清掃を定期的に行うことで、切削品質を向上させることができます。
これらの注意点を守りながら、工作機械を使用した真鍮切削を行うことで、効率的かつ安全な加工が可能となります。ご自身の安全を第一に考え、作業に取り組むことをお勧めします。
工具の摩耗と管理
工作機械を使った真鍮切削において、工具の摩耗と管理は重要なポイントです。工具が摩耗すると、切削品質が低下し、生産性が損なわれる可能性があります。そのため、定期的な確認と適切な管理が必要です。
摩耗を防ぐためには、適切な切削条件を設定することが重要です。切削速度や刃先加工などを適切に調整することで、工具の寿命を延ばすことができます。さらに、切削液の使用や冷却効果も重要です。
例えば、適切な切削条件で真鍮を切削すると、工具の寿命が延び、切削面の仕上がりも向上します。摩耗が進んだ工具を放置せず、定期的に交換することで生産性を維持できます。
工具の摩耗と管理に注意することで、真鍮切削作業を効率的に行うことが可能となります。
業者選択のポイント
加工業者の評価基準
工作機械を使った真鍮切削は、製造業において重要なテクニックの一つです。真鍮は加工しやすい素材ですが、適切な技術と注意が必要です。例えば、適切な切削速度や刃物の選択が重要です。また、切削時には適切な冷却方法を用いることも重要です。これにより、切削時の摩擦や熱を抑え、精密な加工を実現することができます。
さらに、真鍮切削の際には加工機械のメンテナンスも欠かせません。定期的な点検や清掃を行うことで、機械の性能を維持し、安全な作業環境を確保することができます。
真鍮切削は製造業において幅広く利用されていますが、適切なテクニックと注意を守ることが重要です。正しい取り組みを行うことで、効率的な加工が可能となります。
フィリールとは:サービス紹介
工作機械を使った真鍮切削のテクニックとその注意点
真鍮は加工がしやすく、様々な工業製品に利用されています。真鍮切削において、まず重要なのは適切な工作機械を使用することです。切削工程では、工作機械の刃先の形状や回転数、進行速度などが影響を与えます。
例えば、高速鋼の切削工具を使用すると、真鍮の切削精度が向上し、作業効率も向上します。また、冷却液を使用して熱を逃がすことで切削品質を維持することができます。
注意点としては、刃先が摩耗することによる切削品質の低下や、加工途中での振れなどが挙げられます。これらの問題を避けるためには、定期的な刃先交換や適切な切削速度管理が必要です。
工作機械を使った真鍮切削は、正確な加工を行うためには技術と注意が必要です。適切な機械と注意を払いながら作業を行うことで、高品質な真鍮製品を生産することができます。
オーダーメイド加工のメリット
工作機械を使った真鍮切削は、精密な加工技術であり、さまざまな製品に利用されています。真鍮は耐食性があり、美しい光沢があるため、装飾品や工芸品などで広く使われています。この技術を行う際には、注意点もあります。例えば、材料の特性を理解して適切な切削速度や切削量を設定する必要があります。また、適切な冷却や潤滑を行うことで切削品質を向上させることができます。
真鍮切削のテクニックをマスターするためには、熟練した技術と正確な計画が欠かせません。工作機械の知識や操作方法を習得し、安全に作業を行うことが重要です。さらに、切削工程での監視や適切なメンテナンスも重要です。これらのポイントを押さえることで、真鍮切削における高品質な製品を生産することが可能となります。
加工方法と材料の選定
真鍮の種類と選定基準
真鍮の種類には、黄銅と鉄という主な成分からできているものがあります。真鍮を切削する際に重要なのは、適切な切削工具を選ぶことです。硬度の異なる真鍮には、それぞれ適した工具があります。例えば、柔らかい真鍮を切削する場合には、高速度鋼が適しています。一方、硬い真鍮を切削する際には、硬い材料に対応した切削工具が必要です。
真鍮を切削する際には、切削速度や刃先の形状、切削量などにも注意が必要です。切削速度が速すぎると工具の摩耗が進み、逆に遅すぎると切削面が荒れてしまいます。また、適切な切削量を設定することで、作業効率を向上させることができます。
真鍮切削においては、適切な工具と適切な切削条件を選定することが重要です。これらのテクニックを理解し、注意点を押さえることで、効果的な真鍮切削を行うことができます。
加工方法の比較
工作機械を使った真鍮切削のテクニックとその注意点
真鍮を切削する方法にはいくつかの選択肢があります。切削の成功には、適切な工具や設定が欠かせません。例えば、高速度鋼の切削工具は真鍮に適しています。これは真鍮の特性を考慮して設計されているため、効率的かつ精密な切削を実現できます。
また、切削速度や切削深さなどのパラメーターを正確に設定することも重要です。適切な切削速度と切削深さを選択することで、作業効率が向上し、品質の向上につながります。
さらに、切削中には工作機械の振動や異常音に注意する必要があります。これらのサインがある場合は、すぐに作業を中断して問題を調査することが大切です。
真鍮切削においては、適切なテクニックと注意を払うことで、高品質な加工が可能となります。
材料ごとの加工性能
真鍮切削は工作機械を使用して行われる重要なプロセスです。真鍮は耐食性や加工性に優れ、機械部品や装飾品など様々な分野で利用されています。真鍮を切削する際には、適切なテクニックと注意点があります。
まず、切削速度と切削深さを適切に設定することが重要です。高速回転の切削工具を使用すると良好な切削面が得られますが、適切な速度設定が必要です。また、適切な刃先形状や切削油の使用も品質向上につながります。
例えば、真鍮製の歯車を切削する際には、切削速度を適切に制御し、刃先に適切な冷却を行うことが重要です。これにより切削時の摩擦や熱を抑え、歯車の精度を高めることができます。
真鍮切削には様々なテクニックがありますが、適切な設定と注意を守ることで効率的かつ品質の高い加工が可能となります。真鍮切削に挑戦する際には、これらのポイントを押さえて作業を行うことが大切です。
真鍮切削の応用例
装飾品としての真鍮加工
真鍮は、装飾品として広く使用されており、その加工技術も重要です。真鍮は美しい見た目と耐久性から、アクセサリーや装飾品の製作に人気があります。真鍮を切削する際には、適切な工作機械を使用することが重要です。例えば、CNC旋盤やフライス盤を使用することで、精密な加工が可能となります。また、切削速度や切削深さなどの設定も注意が必要です。適切な条件で真鍮を切削することで、綺麗な仕上がりを実現できます。さらに、刃物の定期的なメンテナンスや刃先の交換も忘れずに行うことが大切です。真鍮加工は技術と注意が必要ですが、美しい装飾品を作るために欠かせない技術と言えるでしょう。
機械部品としての真鍮加工
工作機械を使った真鍮切削は、機械部品製造において重要な工程です。真鍮は耐久性があり、加工しやすい特性を持つため、様々な部品に利用されています。このプロセスにはいくつかの注意点があります。
まず、切削速度を適切に設定することが重要です。速度が速すぎると真鍮が熱を持ち、刃や部品が損傷する可能性があります。逆に速度が遅すぎると、切削が効率的に行われず、時間がかかるため生産性が低下します。
また、適切な切削油や冷却液を使用することで切削時の摩擦や熱を軽減し、加工精度を高めることができます。さらに、適切な刃物や工具を選択し、定期的なメンテナンスを行うことも重要です。
これらのテクニックと注意点を守ることで、効率的かつ正確な真鍮切削が可能となり、品質の高い機械部品を製造することができます。
特殊な加工技術とその展望
工作機械を使用した真鍮切削は、製造業における重要な工程の一つです。真鍮は加工が比較的容易であるため、精密な部品や装置に広く使用されています。しかし、真鍮を切削する際には、いくつかの注意点があります。
まず、適切な工作機械と切削工具の選択が重要です。真鍮は柔らかい材料のため、適切な回転数や切削速度を設定することが必要です。また、適切な冷却液を使用して過熱を防ぐことも重要です。
例えば、自動車部品の製造において、真鍮を切削する際は最新の工作機械を使うことが求められます。これにより、高精度な部品を効率的に製造することができます。
真鍮切削のテクニックを熟知し、注意点を守ることで、製造業における生産性向上や品質向上につながることが期待されます。
プロの技:真鍮加工の秘訣
長年の経験から学ぶ
工作機械を使った真鍮切削のテクニックとその注意点
真鍮切削は、工作機械を使った重要な加工方法です。真鍮は加工しやすい金属ですが、正しいテクニックを使わないと失敗する可能性があります。例えば、適切な切削速度や刃先の選定が重要です。
理由は、真鍮は柔らかい金属であり、高速で切削すると加熱しやすくなります。適正な切削速度を保つことで、切削表面の品質を向上させることができます。また、刃先の選定も重要であり、適切な刃先を使用することで切削精度を確保できます。
具体的な注意点として、切削時に適切な冷却液を使用することや、刃先の状態を定期的に確認することが挙げられます。これらのポイントに気を付けることで、効率的で正確な真鍮切削を実現することができます。
加工精度を左右する要因
工作機械を使った真鍮切削のテクニックとその注意点
真鍮の切削において、加工精度を左右する要因はさまざまです。切削速度、切削深さ、切削量などがそれに含まれます。特に、切削速度は重要であり、適切な速度での切削は品質向上に繋がります。また、切削深さや切削量も適切に設定することで、加工精度を向上させることができます。
例えば、適切な刃先の選択や冷却方法の工夫など、細かな工夫が加工精度に影響を与えます。特に真鍮は加工時に熱を持ちやすいため、冷却対策が欠かせません。こうした注意点を押さえることで、工作機械を使った真鍮切削においてより良い成果を得ることができます。
真鍮加工のトラブルシューティング
工作機械を使った真鍮切削は、精密な技術が必要です。切削時には、適切な速度と刃物の選択が重要です。切削速度が速すぎると刃先がすぐに摩耗し、逆に遅すぎると加工が不均一になります。さらに、適切な切削油の使用も重要です。切削油が不十分だと真鍮表面が酸化しやすくなります。
また、真鍮切削の際には振動や加熱による歪みにも注意が必要です。振動があると切削が粗くなるだけでなく、加熱によって真鍮の性質が変わる可能性もあります。これらのトラブルを避けるためには、適切な刃物と工作機械のメンテナンスが欠かせません。真鍮切削においては、技術と注意が求められる作業であることを肝に銘じてください。
真鍮加工の未来と発展
技術革新と真鍮加工
工作機械を使った真鍮切削は、工業製品の製造において重要な技術革新の一つです。真鍮は加工しやすく、耐久性に優れているため、様々な製品に利用されています。例えば、自動車部品や時計の歯車など、身近な製品に真鍮が使われています。
工作機械を使用する際には、刃物やクーラントの適切な使用が重要です。刃物が適切に研がれていることやクーラントが適切に供給されていることによって、切削品質が向上し、加工効率も向上します。また、作業中には機械の安全性にも留意することが大切です。
真鍮切削は精密な作業を要するため、経験豊富な技術者が技術を駆使して行うことが求められます。慎重かつ正確な加工により、高品質な製品を生み出すことができます。技術革新により、真鍮切削の技術はますます進化し、製造業において重要な役割を果たしています。
環境への配慮と真鍮のリサイクル
工作機械を使った真鍮切削のテクニックとその注意点
真鍮は環境にやさしい素材として知られていますが、その製造過程や加工においても環境への配慮が重要です。工作機械を使用した真鍮の切削では、適切な冷却液の使用が不可欠です。これは切削時に発生する熱を逃がし、工具や材料を保護する役割があります。さらに、切削速度や切削深さも適切に設定することで、作業効率が向上し、切削時の摩擦や摩耗を抑えることができます。
例えば、自動車部品や時計の歯車など、真鍮はさまざまな製品に使われています。これらの製品が高品質で安定した仕上がりを持つのは、正確な真鍮切削が可能な工作機械の技術があるからこそです。したがって、環境への配慮と技術革新を融合させた真鍮切削の実践が重要です。
新しい分野への真鍮の応用
工作機械を使った真鍮切削のテクニックとその注意点
真鍮は、金属加工において重要な素材です。工作機械を使用して真鍮を切削する際、正しいテクニックや注意点が重要です。例えば、切削速度や刃具の選択は切削品質に大きく影響します。また、適切な冷却や潤滑も工具の寿命や切削精度に影響を与えます。
真鍮切削の成功には、適切な工作機械の選択が欠かせません。例えば、旋盤やフライス盤など、素材や加工する形状に合わせた機械を選ぶことが重要です。確実な加工を行うためには、適切な切削条件を設定し、定期的なメンテナンスも欠かせません。
これらのポイントを押さえることで、工作機械を使った真鍮切削の効率性や品質を向上させることができます。真鍮の加工に取り組む際には、これらのテクニックと注意点をしっかりと把握して、安定した加工を目指しましょう。
まとめ
工作機械を使用した真鍮の切削には、特定のテクニックと注意点があります。真鍮は切削時に熱を持ちやすいため、十分な冷却が必要です。適切な切削速度と刃物の選択が重要であり、これにより切削時の熱を最小限に抑えることができます。また、切削時の過剰なピッチや刃の摩耗が問題となることがあるため、定期的な刃のメンテナンスが欠かせません。
真鍮フライス加工入門|工作機械の選び方と加工のコツ
真鍮フライス加工とは、独特な魅力を持つ技術の一つです。その美しい仕上がりや精密さは、多くの人々を惹きつけます。本記事では、真鍮フライス加工の入門に焦点を当て、工作機械の選び方や加工のコツについて解説します。これから真鍮フライス加工を始めたいと考えている方々にとって、貴重な情報を提供します。技術の基本から応用まで、真鍮フライス加工の世界を一緒に探検していきましょう。
真鍮フライス加工の基礎知識
真鍮とは – 特性と一般的な用途
真鍮は銅と亜鉛の合金で、耐食性や加工性に優れ、金属加工や装飾品など幅広い用途に使われています。真鍮の特性を活かした加工方法の一つに「フライス加工」があります。
真鍮フライス加工は精密な加工が可能であり、例えば時計部品や自動車部品の製造に活用されています。工作機械を選ぶ際には、高い精度や安定した性能を持つ機械が重要です。さらに、適切な切削速度や刃先形状を選ぶこともポイントです。
真鍮の特性を理解し、適切な工作機械と加工方法を選択することで、効率的かつ精度の高い加工が可能となります。真鍮フライス加工のコツをマスターすることで、さまざまな産業分野で活躍できるでしょう。
フライス加工とは – 基本的なプロセスの解説
真鍮フライス加工は、機械加工の一種であり、素材を削ることで形を作る加工方法です。フライス加工は、工作機械を使用して行われる精密な加工方法です。真鍮は加工が比較的容易であり、耐食性や耐熱性に優れているため、様々な産業で使用されています。
フライス加工を行う際に重要なのは、適切な工作機械の選択です。機械の性能や精度、加工範囲を考慮して選ぶことが重要です。例えば、XYZ軸を備えた3軸フライス機は、複雑な形状の加工に適しています。
また、加工のコツとして、適切な切削速度や切削深さなどのパラメーターの設定が重要です。素材や加工する形状によって最適な設定が異なるため、実際の加工前に慎重に計画を立てることが必要です。真鍮フライス加工は工業製品から工芸品まで幅広い分野で活用されており、正確な加工が求められる重要な技術の一つです。
真鍮フライス加工の難しさと一般的な課題
真鍮フライス加工は、金属を削る工程で高い精度が求められるため、様々な難しさや課題が存在します。例えば、真鍮は柔らかい素材であるため、削りすぎると加工物が傷つきやすくなります。また、適切な工具や適正なスピードを選ばなければ、加工面の仕上がりが悪くなることもあります。
さらに、真鍮は熱膨張率が大きいため、加工中に工具やワークが熱されると寸法が変化しやすくなります。このため、加工後の仕上がりを確認する工程や、定期的な機械のメンテナンスが重要となります。
これらの課題に対処するためには、適切な工作機械と工具の選択が不可欠です。加工条件を適切に設定し、経験と技術を生かして問題を解決することが真鍮フライス加工の成功のカギとなります。
真鍮C3604とその他の真鍮合金の比較
真鍮加工において、材料の選択は重要です。特に真鍮C3604は一般的な真鍮合金ですが、その他の真鍮合金と比較するとどうでしょうか。真鍮C3604は優れた加工性や耐食性を持ち、機械的性質も安定しています。一方、他の真鍮合金には弾性率や強度に優れたものもあります。加工を行う際には、使用状況や必要な特性に合わせて適切な真鍮合金を選択することが重要です。例えば、機械部品には強度が求められるため、適切な合金を選ぶことが必須です。おそらく、使用する工作機械や加工方法によっても、適した材料が異なる可能性があります。真鍮加工の際は、材料選択に細心の注意を払い、最適な成形を行うことが肝要です。
工作機械の選び方
フライス加工に適した工作機械の種類
真鍮のフライス加工に適した工作機械の種類は、主に数々の切削作業を行うことができるマシンが必要です。例えば、マシニングセンターや旋盤などが挙げられます。これらの機械は、高い精度や効率性を持ち、真鍮の硬さや粘り強さに対応することができます。また、フライス加工では回転するカッターを使用して加工を行うため、これらの機械が適しています。さらに、工作機械を選ぶ際には、加工精度や生産性、耐久性などを考慮することが重要です。真鍮の特性を理解し、それに最適な工作機械を選ぶことで、効果的なフライス加工を行うことができます。
真鍮加工に最適な工作機械の特徴
真鍮加工において、適切な工作機械を選ぶことは非常に重要です。真鍮は柔らかく、加工が比較的容易な素材であり、フライス加工に適しています。真鍮加工に最適な工作機械の特徴はいくつかあります。
まず、高い加工精度が求められます。真鍮は繊細な素材であり、正確な加工が必要です。そのため、工作機械の精度が高いことが重要です。
さらに、加工速度も考慮すべき点です。効率的な加工を行うためには、工作機械の加工速度が適切であることが求められます。
具体的な例として、精密な部品加工に適した5軸フライス盤や、小ロット生産に適したマシニングセンターが挙げられます。
真鍮加工を行う際には、これらの特徴を持つ工作機械を選ぶことで、効率的かつ精密な加工が可能となります。
初心者におすすめの工作機械とその選定基準
真鍮フライス加工は工作の基本となる技術の一つです。真鍮は加工しやすく、美しい仕上がりが得られるため、初心者にもおすすめです。フライス加工は精密さが求められる作業ですが、適切な工作機械を選ぶことで効率的に加工することが可能です。
工作機械を選ぶ際には、まず加工する寸法や形状に適した機械を選定することが重要です。例えば、小さな部品を加工する場合はベンチトップミルが適しています。また、自動給排仕様の機械を選ぶことで作業効率が向上します。
このように、適切な工作機械を選ぶことで真鍮フライス加工をより効率的に行うことができます。初心者でも挑戦しやすいこの技術を通じて、工作の楽しさや魅力を体感してみてください。
フライス加工のコツと最適な方法
真鍮C3604のフライス加工の手順
真鍮C3604のフライス加工は、工作機械を使用して行われる加工方法です。この加工手順をマスターすることで、より正確で効率的な加工が可能となります。まず、適切な工作機械を選ぶことが重要です。真鍮の特性を考慮し、適切なフライス機を選定しましょう。
次に、加工のコツとして、適切な切削速度や刃先の選定が重要です。真鍮は柔らかい金属なので、適切な刃先を使用することでスムーズな加工が可能となります。加工中は適切な冷却剤を使用して加工熱を逃がすことも忘れずに。
最後に、加工が終了したら、仕上げ作業を丁寧に行いましょう。正確な加工が品質向上につながります。真鍮C3604のフライス加工を通じて、工作技術の向上と効率化を目指しましょう。
真鍮フライス加工時の切削条件の設定
真鍮フライス加工時の切削条件の設定は重要です。真鍮は加工しやすく、美しい仕上がりを得ることができます。まず、切削速度や送り速度を適切に設定することがポイントです。高速で切削すれば、真鍮は熱で柔らかくなり、加工がスムーズに進みます。ただし、速度が速すぎると刃物が早く摩耗する可能性があるため、適切なバランスが必要です。
さらに、切削液の使用も効果的です。切削液は切削時に発生する熱を逃がし、刃先と加工面を冷やす役割を果たします。これにより、刃物の寿命を延ばし、作業効率を向上させることができます。
例えば、真鍮製の部品を精密に加工する際、切削速度を適切に設定し、切削液を効果的に使用することで、高品質な仕上がりを実現できます。真鍮フライス加工において、適切な切削条件の設定は成功の鍵と言えるでしょう。
加工精度を高めるための工夫
真鍮フライス加工では、加工精度を高めるための工夫が重要です。まず、適切な工作機械を選ぶことが不可欠です。精度の高いミーリングマシンや旋盤を用いることで、きめ細やかな加工が可能になります。次に、適切な切削条件を設定することも重要です。切削速度や刃先加工量を適切に調整することで、素材の性質に合った最適な加工が実現できます。例えば、真鍮の場合は熱や摩擦に弱い性質を考慮して、適切な切削条件を選択する必要があります。
さらに、工具の適切な管理も精度向上に不可欠です。定期的な点検や交換を行うことで、加工品質を安定させることができます。これらの工夫を組み合わせることで、真鍮フライス加工における精度向上が期待できます。
加工中のトラブルとその対処法
真鍮フライス加工において、加工中に起こるトラブルは避けられません。例えば、切削音が変化したり、加工精度が低下したりすることがあります。これらのトラブルが発生した場合、まずは原因を見極めることが重要です。切削速度や切削量の調整、適切な冷却液の使用など、加工条件を確認しながら対処することがポイントです。
具体的には、刃先の摩耗や破損が原因で加工精度が低下することがあります。この場合、定期的な刃先交換や適切な刃物の選択が必要です。また、真鍮の特性を考慮して適切な切削条件を設定することも重要です。加工中に問題が生じた際は、慌てずに冷静に対処することで、効果的にトラブルを解決できるでしょう。
真鍮をきれいに加工するテクニック
表面仕上げを良くするための方法
真鍮フライス加工は、工作機械を使って真鍮を形作るプロセスです。真鍮は耐食性や見た目の美しさから広く使われています。フライス加工は、切削工具を回転させながら素材を削り出す技術です。この技術を使う際には、適切な工作機械を選ぶことが重要です。
まず、フライス加工に適した工作機械を選ぶ際には、加工精度や安全性、生産性などが考慮されます。例えば、CNCフライス盤は自動化された操作で精密な加工が可能です。
さらに、加工のコツとしては、適切な切削速度や切削深さを設定し、適切な冷却液を使用することが挙げられます。これによって真鍮の表面仕上げを向上させることができます。
結果として、適切な工作機械の選定と適切な加工方法の選択により、真鍮フライス加工における表面仕上げを向上させることができます。
真鍮加工時の冷却液の役割と選び方
真鍮フライス加工時には、冷却液が非常に重要です。これは、加工中に発生する熱を効果的に逃がし、工具や材料の寿命を延ばすために必要です。冷却液は加工時の摩擦を減らし、切削抵抗を低減する役割も果たします。
適切な冷却液を選ぶ際には、真鍮の性質を考慮することが重要です。通常、真鍮は加工時に熱を吸収しやすいため、高温になりやすい特性があります。そのため、冷却液の冷却効果が高いことが求められます。
具体的な例を挙げると、炭化エステル系の冷却液は真鍮の加工に適しています。このような冷却液は、高温になりがちな真鍮を十分に冷やしながら、切削作業を効果的に行うことができます。
真鍮フライス加工を行う際には、適切な冷却液の選定が重要であることを覚えておきましょう。
ツール選択とメンテナンスの重要性
真鍮フライス加工は工作機械の中でも重要な技術の一つです。機械を選ぶ際には、ツール選択とメンテナンスの重要性を理解することがポイントです。適切なツールを選ぶことで、作業効率が向上し、品質も向上します。また、定期的なメンテナンスを行うことで機械の寿命を延ばし、安定した加工品質を維持することができます。
例えば、真鍮の硬さや特性に合った適切なフライスツールを使うことで、切削時の振動や摩擦を最小限に抑えることができます。これにより、加工精度が向上し、作業効率もアップします。定期的なメンテナンスを怠らずに行うことで、機械の性能を最大限に引き出し、安定した加工を実現できます。真鍮フライス加工を行う際には、ツール選択とメンテナンスに注意して取り組むことが重要です。
真鍮加工のためのフィード速度とスピンドル速度の調整
真鍮加工のためのフィード速度とスピンドル速度の調整は重要です。なぜなら、真鍮は加工しやすい材料である一方で、適切な速度で加工しなければなりません。例えば、高いフィード速度やスピンドル速度で加工すると、真鍮が過熱して変形してしまう可能性があります。逆に、速度が遅すぎると加工時間が長くなり、効率が悪くなります。
そのため、真鍮を効果的に加工するためには、適切なフィード速度とスピンドル速度のバランスを見極めることが重要です。例えば、低いスピンドル速度であれば、高めのフィード速度が適しています。これにより、効率的に真鍮を加工することが可能となります。適切な速度設定を行うことで、品質の高い加工が実現し、作業効率も向上するでしょう。
真鍮加工の理論
真鍮の加工法とその特徴
真鍮の加工法には、様々な選択肢があります。真鍮はその硬さと耐食性から、工作機械を使ったフライス加工が一般的です。フライス加工では、回転するカッターを使って真鍮の形状を切削します。この方法は精密な加工が可能であり、さまざまな形状を作ることができます。例えば、真鍮のネジや歯車などを製作する際に活用されます。
フライス加工を行う際には、適切な工作機械を選ぶことが重要です。特に真鍮は柔らかい金属であるため、適切な刃物の選択やスピード設定が必要です。適切な工具を使用することで、品質の高い真鍮加工が可能となります。
真鍮の加工は多くの工業製品や装飾品に使用されており、その特徴的な色合いや耐久性から幅広い用途に利用されています。工作機械を上手に活用し、真鍮の魅力を引き出す加工を行うことが重要です。
真鍮の加工における欠点とその対策
真鍮の加工において、熱に弱い性質があるのが欠点です。例えば、フライス加工の際に高温が加わると、真鍮が割れたり変形したりする可能性があります。そのため、加工中に適切な冷却を行うことが重要です。冷却方法としては、切削液や空気を使った方法があります。これにより、真鍮の加工精度を高め、品質を保つことができます。また、切削速度や刃先の選定も重要です。適切な条件を設定することで、真鍮の加工効率を向上させることができます。これらの対策を講じることで、真鍮の加工における欠点を克服し、効果的に作業を行うことが可能です。
加工品質を左右する材料の特性
真鍮は、工作機械での加工において重要な材料です。真鍮は、耐食性や可鍛性に優れており、美しい金属光沢も特徴です。これらの特性を活かすためには、正しい工作機械の選択が欠かせません。例えば、フライス加工では、高い精度が求められるため、適切なフライス盤を選ぶことが重要です。また、加工中に適切な冷却剤を使用することで、切削時の摩擦や熱を抑え、加工精度を向上させることができます。つまり、真鍮の特性を最大限に活かし、高品質な加工を実現するためには、工作機械の選定と適切な加工手法が重要です。
最新の真鍮フライス加工技術の動向
最新の真鍮フライス加工技術の動向は、工作機械の選び方と加工のコツに大きく影響を与えています。真鍮は加工性が高く、耐食性に優れた素材であり、様々な産業で広く使用されています。特に精密な部品や装飾品の製造において真鍮フライス加工は欠かせない技術となっています。例えば、時計製造や航空機部品の加工などが挙げられます。
工作機械の選定において、真鍮の特性を理解し、正確かつ効率的な加工を行うことが重要です。適切な切削速度や刃先の選定、冷却液の使用などが加工の品質に影響を与えます。また、最新のCNCマシンを活用することで高精度な加工が可能となります。
技術の進化により、真鍮フライス加工はさらに効率化され、精度が向上しています。工作機械の選択と加工のコツを理解し、最新の技術を活用することで、真鍮加工の可能性はますます広がるでしょう。
実践!プロジェクトに役立つ加工のポイント
プロジェクトごとの真鍮選択の考慮事項
真鍮フライス加工入門|工作機械の選び方と加工のコツ
真鍮は、機械加工の際に重要な材料の一つです。フライス加工において、適切な真鍮の選択はプロジェクトの成功に不可欠です。なぜなら、真鍮の種類や特性は加工の結果に直接影響を与えるからです。
まず、材料の強度や耐久性を考慮して真鍮を選択することが重要です。特定のプロジェクトに適した強度や耐久性を持つ真鍮を選ぶことで、製品の品質が向上し、加工時の効率も向上します。
例えば、高級な真鍮合金は、精密な部品や装飾品の加工に適しています。一方、一般的な真鍮は、一般的な機械部品の加工に適しています。
適切な真鍮の選択は、加工工程をスムーズにし、製品の品質向上につながります。プロジェクトごとに適した真鍮を選ぶことで、加工のコツを身につけることができます。
加工プランの立案と効率的な進め方
真鍮フライス加工は、加工プランを立案する際に効率的な進め方が重要です。まず、加工のコツは、適切な工作機械を選ぶことから始まります。例えば、回転数や切削速度を適切に設定することで、真鍮材料を効率的に加工することができます。具体例として、適切なカッターを選んで刃先を研ぐことで、高精度な加工が可能となります。さらに、適切な冷却液を使用することで、加工時の熱を逃がし、質の高い仕上がりを得ることができます。これらの工夫を取り入れることで、真鍮フライス加工を効果的かつ効率的に行うことができます。
品質管理と検査のポイント
真鍮フライス加工は、工作機械の選び方と加工のコツが重要です。真鍮は加工しやすく、耐久性に優れた素材です。加工する際には、適切なフライス盤を選ぶことがポイントです。例えば、高速回転数に対応した刃物が必要です。また、刃先の材質や硬度も適切でなければなりません。正確な加工を行うためには、工作機械のメンテナンスも欠かせません。油の注入や刃物の研ぎ直しを定期的に行うことが重要です。
さらに、加工のコツとして、適切な切削速度や切削深さを把握することも大切です。真鍮は柔らかい素材なので、適切な加工条件を設定することで、効率的に加工することができます。工作機械の選定と適切な加工条件の把握をしっかりと行うことで、品質管理と効率的な加工が可能となります。
真鍮フライス加工のコスト削減と生産性向上のコツ
真鍮フライス加工は、材料を削るための重要な工程です。このプロセスを効果的に行うためには、コスト削減と生産性向上のためのコツがあります。
まず、適切な工作機械を選ぶことが重要です。高品質で信頼性のある機械を選ぶことで、加工の精度と効率が向上します。例えば、自動給油や高速回転機能を備えた機械は、作業時間を短縮し、生産性を向上させます。
さらに、適切な切削工具を選ぶことも重要です。真鍮に適した刃物を使用することで、切削面の仕上がりを向上させることができます。
これらのコツを実践することで、真鍮フライス加工のコストを削減し、生産性を向上させることができます。適切な機械と工具を選び、効率的に加工を行うことで、より良い成果を得ることができるでしょう。
よくある質問と答え
真鍮加工に関するFAQ
真鍮フライス加工では、工作機械の選び方と加工のコツが重要です。真鍮は加工しやすく、美しい仕上がりが得られることから人気があります。適切な工作機械を選ぶことで、効率的に加工することができます。
まず、工作機械の選び方です。真鍮の硬さや形状に合ったフライス機を選ぶことが大切です。素材によっては切削速度や刃の形状も異なりますので、それに応じた選択が必要です。
加工のコツとしては、適切な切削速度や刃先の角度を使うこと、定期的な切削油の使用、安定した加工温度の維持が挙げられます。これらのポイントを押さえることで、真鍮フライス加工をスムーズに行うことができます。
トラブルシューティングガイド
真鍮フライス加工は、工作機械の選び方や加工のコツを理解することが重要です。真鍮は硬く、加工が難しい素材ですが、適切な工具と技術を使えば綺麗な仕上がりを得ることができます。まず、適切なフライス盤を選ぶことがポイントです。硬い素材を切削するためには、十分な剛性と精度が必要です。次に、適切な切削速度と刃先の選択が重要です。適切な切削速度で加工すれば、真鍮の表面を傷つけずに綺麗に加工できます。また、刃先は適切なものを選ぶことで効率的に仕上げ作業ができます。これらのポイントを押さえて真鍮フライス加工を行うことで、きれいな加工面を実現できます。
真鍮フライス加工に関する専門用語の解説
真鍮フライス加工とは、真鍮材料を工作機械を使って形を整える加工方法です。真鍮は加工しやすく、美しい仕上がりが特徴です。この加工方法では、フライス盤やCNCマシンなどの工作機械を使用します。
真鍮フライス加工の専門用語を理解することは重要です。例えば、「切削速度」とは切削工具が材料に対して移動する速度のことで、加工表面の仕上がりに影響を与えます。また、「切削深さ」は工具が材料にどれだけ深く切り込むかを示し、加工効率に影響します。
適切な工作機械を選ぶことも成功の鍵です。真鍮フライス加工には、材料の硬さや形状に合った工作機械を選ぶ必要があります。これらのポイントを理解して、効果的な真鍮フライス加工を行いましょう。
真鍮フライス加工に役立つリソースと参考文献
真鍮フライス加工は、工作機械の中でも重要な技術の一つです。真鍮は加工しやすい素材であり、精密な部品が作成できます。真鍮フライス加工のコツとして、適切な工作機械の選定が重要です。例えば、高精度なフライス盤や適切な切削工具を使用することがポイントです。
さらに、加工時に適切な切削速度や切削深さを設定することも大切です。これにより、綺麗な仕上がりや効率的な加工が可能となります。真鍮の特性を理解し、適切な加工条件を設定することで、高品質な部品が生産できます。
一方、真鍮フライス加工に役立つリソースとして、専門書やインターネットの情報が挙げられます。これらの参考文献を活用することで、より効果的な加工方法やテクニックを身に付けることができます。真鍮フライス加工の基本を理解し、熟練した技術を身につけることが重要です。
まとめ
真鍮フライス加工は工作機械を使用して、真鍮を形作るプロセスです。真鍮は加工しやすい素材であり、初心者にもおすすめの素材です。加工する際には、適切な切削速度や刃先形状を選ぶことが重要です。加工には専用のフライス盤や旋盤が必要であり、これらの工作機械を購入する際には、使用目的や予算に合った機種を選ぶことが大切です。また、正しい切削油の使い方や加工温度の管理も加工のコツとなります。
フライス加工のプロが伝授!真鍮の正確な穴あけ方法
真鍮フライス加工の基礎
真鍮は、さまざまな産業で広く使用される金属であり、その加工性や物理的特性により、多くの部品に利用されています。フライス加工は、金属を削り取る方法の一つで、特に精密な加工が可能です。ここでは、真鍮の特性やフライス加工の基本について説明し、真鍮フライス加工の応用事例を紹介します。真鍮とは:特性と利点
真鍮は、主に銅と亜鉛の合金で、通常は70%程度の銅と30%程度の亜鉛から成り立っています。銅と亜鉛の比率を変更することで、真鍮の特性を調整することができます。特性
- 優れた加工性: 真鍮は、比較的柔らかくて加工しやすい材料です。そのため、切削やフライス加工においても、工具の摩耗が少なく、精度の高い加工が可能です。
- 優れた耐腐食性: 真鍮は、耐食性が高いため、湿気や空気中の酸素に対して強い耐性を持っています。これにより、装飾品や機械部品としても広く使用されます。
- 美しい外観: 美しい金色の光沢が特徴で、主に装飾用途や高級感を必要とする部品に用いられます。
- 良好な電導性: 真鍮は、銅をベースにしているため、電気伝導性も高いです。
利点
- 加工性が良好で、精密な部品製造が可能
- 耐食性が高く、長期間の使用に耐える
- 軽量でありながら、強度も備えている
- 美しい外観を持つため、装飾用途にも適している
フライス加工とは:基本的な概要
フライス加工は、旋盤加工と並ぶ代表的な切削加工方法で、回転する切削工具を用いて材料を削り取る方式です。フライス盤を使用して、平面や溝、ねじ山、複雑な形状の部品を精密に加工できます。基本的なプロセス
- 工具の選定: フライス加工では、使用する工具によって仕上がりや加工スピードが大きく異なります。真鍮加工においては、細かい切削を実現するため、切削工具の材質や形状が重要です。
- 切削条件の設定: 切削速度や送り速度、切込み深さを適切に設定することで、加工効率を高め、工具の寿命を延ばすことができます。
- 冷却材の使用: 真鍮は比較的柔らかい材料ですが、フライス加工中には熱が発生するため、冷却材を使用して切削部分を冷却し、摩耗を抑えます。
主な加工方法
- 平面フライス加工: 平らな面を削る加工方法です。複数の工程を経て、最終的に精密な寸法を実現します。
- 成形フライス加工: 複雑な形状の部品を作成するための方法です。異なる形状の工具を使用して、精度の高い成形を行います。
真鍮のフライス加工での穴あけ
真鍮は、良好な加工性と優れた耐食性を持つため、穴あけ加工にもよく使用されます。フライス加工における穴あけは、特に精度が求められますが、いくつかの課題も存在します。ここでは、真鍮のフライス加工における穴あけのプロセスや課題、その原因と対策について説明します。穴あけ加工のプロセス
フライス加工での穴あけは、基本的には以下の手順で行われます。- 工具の選定: 穴あけには通常、ドリルやカウンターボアなどの工具を使用します。真鍮のような軟らかい材料には、切れ味の良い工具が必要です。
- 位置決め: 穴をあける位置を精密に決定します。フライス盤には、定規や目視による確認が必要な場合がありますが、精密な位置決めを行うためには、定規やジグを使用することもあります。
- 穴あけの開始: 穴あけは、適切な切削条件と回転速度を設定した後に開始されます。真鍮の切削は比較的簡単ですが、工具の摩耗や熱の発生に注意が必要です。
- 切削条件の調整: 穴の深さや径に応じて切削条件(送り速度、切削深さなど)を調整し、精度よく加工します。
穴あけにおける一般的な課題
真鍮の穴あけ加工においては、いくつかの課題が発生することがあります。これらの課題を理解し、適切な対策を講じることが、品質向上につながります。1. 工具の摩耗
真鍮は比較的軟らかい素材ですが、長時間の使用で工具が摩耗することがあります。これにより、穴の精度が低下し、仕上がりに影響を及ぼすことがあります。2. 熱の発生
切削中に発生する熱が工具や加工部品に影響を与えることがあります。高温によって、工具の寿命が短くなったり、真鍮の表面が変質することがあります。3. バリの発生
穴あけの際に、加工物の周囲にバリが発生することがあります。バリが残ると、部品の品質が低下し、追加の処理が必要になることがあります。4. 穴の真直度の確保
フライス加工における穴あけは、真直度を確保することが難しい場合があります。加工中に工具のブレや振動が生じることがあり、精度が低下する原因となります。穴あけ失敗の原因と対策
穴あけの失敗を防ぐためには、原因を特定し、適切な対策を講じることが重要です。1. 原因:工具の摩耗
- 対策: 適切な切削条件(切削速度や送り速度)を設定し、必要に応じて工具を交換する。工具の材料やコーティングを選定することで摩耗を抑制する。
2. 原因:熱の発生
- 対策: 冷却液を使用することで、工具と加工部品の温度を下げ、摩耗や表面変質を防ぐ。適切な冷却を行い、熱が蓄積しないようにする。
3. 原因:バリの発生
- 対策: 穴あけ後にバリ取りを行うことが一般的ですが、予防策として、切削条件を適切に設定し、送り速度を調整することでバリの発生を抑える。
4. 原因:穴の真直度が取れない
- 対策: 穴あけ時に工具が振動しないように、フライス盤の安定性を確認する。また、固定具やジグを使って部品をしっかりと固定し、工具のブレを最小限に抑える。
黄銅のフライス加工での切削速度
黄銅(真鍮)は、その優れた加工性と良好な機械的特性から、多くの製造業で利用されています。特にフライス加工においては、切削速度を適切に設定することが重要です。ここでは、黄銅のフライス加工における切削速度の基本、適切な切削速度の決定方法、および切削速度の調整と最適化について説明します。切削速度の基本
切削速度は、切削工具と加工物との接触点での速度を指します。この速度は、工具が加工物を切削する速度であり、材料の種類や工具の材質、加工の目的によって適切な値を設定することが必要です。切削速度は、通常、単位時間あたりの進行距離(m/min)で表されます。 切削速度の基本は以下の式で計算されます: [ V_c = \frac{\pi \times D \times N}{1000} ]- (V_c):切削速度(m/min)
- (D):工具の直径(mm)
- (N):回転数(rpm)
真鍮加工に適した切削速度の決定
黄銅のフライス加工においては、適切な切削速度を設定することが重要です。黄銅は比較的軟らかい金属であり、適切な切削速度を選ばないと、加工効率が悪くなる場合があります。1. 材質に適した範囲の選定
黄銅の切削速度は、工具や加工条件により異なりますが、一般的な範囲としては、以下のような設定が推奨されます:- 低速切削(100~150 m/min):粗加工や初期加工
- 中速切削(150~250 m/min):精密加工や中程度の切削
- 高速切削(250~350 m/min):仕上げ加工や高精度要求
2. 工具の材質とコーティング
黄銅の加工には、高速鋼(HSS)や硬質合金(WC-Co)などの工具が使われます。工具の材質によっても適切な切削速度は異なり、硬質合金の工具を使用することで、より高い切削速度を選ぶことができます。切削速度の調整と最適化
黄銅のフライス加工では、切削速度を適切に調整することが、加工効率と仕上がりの品質を向上させるために重要です。以下の方法で、切削速度を調整および最適化することができます。1. 回転数の調整
回転数を調整することで、切削速度を変更できます。加工中に工具の摩耗が早い場合は、回転数を下げ、逆に切削効率が悪いと感じる場合は、回転数を上げてみます。2. 切削条件の最適化
切削速度の調整に加えて、送り速度や切削深さなどの切削条件も調整する必要があります。これらをバランスよく調整することで、黄銅のフライス加工における効率を最大化できます。3. 冷却と潤滑
適切な冷却と潤滑を使用することで、切削温度を抑えることができ、工具の寿命を延ばし、より高い切削速度での加工が可能になります。特に真鍮などの非鉄金属は熱の伝導が良いため、冷却液を使用して切削温度を管理することが重要です。真鍮の切削加工の基礎知識
真鍮は、銅と亜鉛を主成分とする合金で、加工性に優れ、広く使用されています。特に機械加工においては、切削性の良さから、様々な形状の部品や製品に加工されます。本章では、真鍮の物理的・化学的性質、切削工具の選択、そして切削液の使用とその重要性について解説します。真鍮の物理的・化学的性質
真鍮は銅を主成分とし、亜鉛を加えた合金です。これにより、真鍮は非常に優れた加工性を持ちながらも、強度や耐食性を兼ね備えています。- 硬度と強度: 真鍮は比較的軟らかい金属であり、切削性が高く、機械加工が容易です。また、加工後も硬度や強度はある程度保持されます。
- 耐食性: 真鍮は錆びにくく、耐腐食性に優れ、特に湿気や水分に対して強い特性を持っています。
- 熱伝導性: 真鍮は熱伝導性が良好で、高温環境下でも安定して使用することができます。
- 導電性: 電気伝導性も良好で、電子部品や電気機器にも多く使用されています。
切削工具の選択
真鍮の切削加工には、適切な切削工具を選ぶことが非常に重要です。真鍮は比較的軟らかいため、鋼や炭素工具でも十分に加工できますが、加工精度や寿命を考慮した選択が求められます。- 工具材質:
- 高速度鋼(HSS): 真鍮の切削には一般的に使用される工具材質です。安価であり、加工に適しています。
- 硬質合金(WC-Co): より高精度が求められる場合や、高速切削を行う場合には硬質合金が選ばれます。硬質合金は耐摩耗性が高く、工具寿命が長いため、長時間の加工にも適しています。
- チップコーティング: TiN(チタンナイトライド)やTiAlN(チタンアルミナイトライド)のようなコーティングを施した工具は、摩擦を減らし、切削性能を向上させる効果があります。
- 工具形状:
- フライス工具: 真鍮の切削においては、一般的に平面加工や溝加工が多く、フライス工具が使用されます。工具の形状は、加工する形状に応じて選定します。
切削液の使用とその重要性
切削液は、切削加工において非常に重要な役割を果たします。真鍮の切削加工でも、切削液を使用することで、以下のような効果が得られます。- 冷却効果: 切削中に発生する熱を効率よく取り除き、工具や加工物の過熱を防ぎます。これにより、工具の摩耗を抑制し、加工精度を保ちます。
- 潤滑効果: 切削液は切削面を潤滑することで、摩擦を低減し、加工時の熱発生を抑えます。これにより、工具寿命が延び、加工精度が向上します。
- 除去効果: 切削中に発生する切屑を効率よく除去することで、切屑の絡みつきや工具へのダメージを防ぎます。
真鍮の加工法と特徴
真鍮はその優れた加工性と物理的特性により、機械加工に広く使用される金属ですが、加工時には特定の注意点が必要です。以下では、真鍮の主な加工法やその特徴、加工時の挑戦とその解決策、さらに真鍮の欠点とその対処法について解説します。加工法の種類と特徴
真鍮の加工には、主に以下の方法が使用されます。それぞれの特徴を理解することで、最適な加工法を選択することが可能です。- 切削加工: 真鍮は軟らかい金属であるため、切削加工は比較的容易です。特にフライス加工や旋盤加工、ボーリングなどが一般的です。切削中の摩耗が少なく、表面仕上げがきれいに仕上がるため、精密部品の製造に適しています。
- 圧延加工: 真鍮は圧延加工にも適しています。圧延により、薄板や帯板を作成することができ、配管や電気機器部品などの用途に使用されます。
- 鋳造: 真鍮は鋳造にも使用されます。鋳造法は、金型に溶かした真鍮を流し込み、固化させて部品を製造する方法です。特に複雑な形状や大量生産に適しています。
- 鍛造: 真鍮は熱間鍛造にも適しており、鍛造により強度を向上させることができます。鍛造された真鍮は、機械部品や構造部品として高い耐久性を発揮します。
真鍮加工の際の挑戦と解決策
真鍮はその特性により加工が容易な金属ですが、いくつかの挑戦もあります。これらを解決するための方法を以下に紹介します。- 切削中の切屑の処理: 真鍮は比較的軟らかい金属であるため、切削中に切屑が絡まりやすく、工具や加工物に影響を与えることがあります。これを防ぐためには、切削液を使用して冷却と潤滑を行うことが重要です。また、切削条件を適切に設定し、切屑がスムーズに流れるようにすることも効果的です。
- 摩耗と工具の寿命: 真鍮は金属的には軟らかいため、切削工具の摩耗は比較的少ないですが、加熱されすぎると摩耗が早まることがあります。これを防ぐためには、適切な切削速度や切削液の使用が推奨されます。また、工具材質やコーティングを選定することで、工具寿命を延ばすことができます。
- 変形やひび割れ: 真鍮は熱処理後に変形したり、ひび割れが生じることがあります。これを防ぐためには、適切な冷却速度と加熱温度で熱処理を行うことが必要です。鋳造時の温度管理も重要です。
真鍮の欠点とその対処法
真鍮にはいくつかの欠点がありますが、適切な対処法を取ることでその欠点を克服することが可能です。- 腐食: 真鍮は耐腐食性に優れていますが、特に塩水や酸性の環境においては腐食しやすいことがあります。これを防ぐためには、表面処理(例えば、ニッケルメッキやクロムメッキ)を施すことが効果的です。また、定期的なメンテナンスと清掃も重要です。
- 高温に弱い: 真鍮は高温に弱く、長時間高温にさらされると、硬度が低下し、変形や損傷を引き起こすことがあります。この問題を防ぐためには、高温環境での使用を避けるか、耐熱性を持つ合金を使用することが推奨されます。
- 強度の限界: 真鍮は強度が比較的低いため、高い負荷がかかる部品には不向きです。この問題に対処するためには、真鍮合金の種類を選ぶことが重要です。例えば、銅の含有量が高い真鍮は強度が高く、機械部品に適しています。
真鍮フライス加工で気をつけるべきポイントとは?
真鍮フライス加工とは、熟練した技術と知識が求められる加工方法の一つです。この記事では、真鍮フライス加工において気をつけるべきポイントについて詳しく解説します。真鍮とはどのような素材なのか、フライス加工の基本原理について、そして成功するためのコツまで、初心者から上級者まで幅広く役立つ情報を提供していきます。真鍮フライス加工に興味をお持ちの方や技術を磨きたい方々にとって、必見の内容となっています。加工技術の世界に踏み込む前に、この記事でしっかりと準備をしてみませんか?
真鍮フライス加工の基礎知識
真鍮とは – 特性と利点
真鍮は、銅と亜鉛を合金化した素材であり、金属加工に広く使用されています。真鍮の特性としては、耐食性があり、錆びにくいため、美しい見た目を長期間保つことができます。また、加工性が高く、切削加工やフライス加工などでも扱いやすい特性があります。このため、真鍮は建築や工芸品などさまざまな分野で利用されています。
真鍮をフライス加工する際に気をつけるべきポイントは、適切な切削条件を選択することです。切削速度や切削量などの条件を適切に設定することで、加工精度や加工品質を向上させることができます。また、刃先や切削油の選定も重要であり、これらの条件を適切に管理することで効率的な真鍮フライス加工が可能となります。
フライス加工の概要
真鍮フライス加工は、精密な加工技術の一つです。真鍮は硬くて加工が難しい素材ですが、フライス加工を行うことで高精度な形状を作ることができます。この技術を行う際に気をつけるべきポイントがいくつかあります。
まず、適切な切削速度と切削量を設定することが重要です。適切なパラメーターを設定することで、真鍮を効率的に加工することができます。また、適切な冷却液を使用することも大切です。冷却液を使うことで加工時の摩擦熱を抑え、工具の寿命を延ばすことができます。
さらに、加工時には適切な工具の選択も重要です。適切な工具を選ぶことで、精密な加工が可能となります。これらのポイントに気をつけることで、真鍮フライス加工をスムーズに行うことができます。
真鍮フライス加工の産業における役割
真鍮フライス加工は、工業分野において重要な役割を果たしています。真鍮は耐食性や可塑性に優れており、機械部品や精密部品の製造に広く使用されています。そのため、真鍮フライス加工は精密さが求められる産業において欠かせない技術と言えます。
例えば、自動車産業では、エンジン部品やブレーキ部品などに真鍮フライス加工が活用されています。その精度と耐久性から、自動車の性能向上や安全性確保に貢献しています。
さらに、電子機器の製造においても真鍮フライス加工は重要な役割を果たしています。電子部品のケースやネジなど、細かい部品の製造に真鍮が使われることが多く、高い精度が求められています。
このように、真鍮フライス加工は産業界において幅広く活用されており、その重要性は今後もさらに高まっていくことが期待されています。
真鍮フライス加工の技術的ポイント
適切な切削工具の選定
真鍮フライス加工において重要なポイントは何でしょうか? 真鍮は加工時に注意が必要な素材です。まず、切削工具の選定が重要です。硬度の高い真鍮を綺麗に削るためには、適切な切削工具を選ぶことが必要です。たとえば、ハイスや硬質合金製のフライスカッターが効果的です。これらの工具を使用することで、真鍮材料の加工がスムーズに行えます。選んだ切削工具が作業の質や効率に大きく影響することを忘れないでください。真鍮フライス加工を行う際には、切削工具の選定が成功の鍵となります。
切削条件の最適化
真鍮フライス加工で気をつけるべきポイントとは?真鍮材料のフライス加工において、切削条件の最適化が重要です。切削条件とは、切削速度や送り速度、切削深さなどの加工条件のことです。適切な切削条件を設定することで、加工効率を向上させることができます。例えば、高速での切削や適切な切削深さを設定することで、真鍮材料を効率よく加工することが可能です。また、適切な切削条件を設定することで、刃物の摩耗を抑えることもできます。真鍮材料の特性を考慮しながら、適切な切削条件を選定することが重要です。切削条件の最適化により、品質の向上や加工効率の向上が期待できます。
加工精度を高めるための工夫
真鍮フライス加工において、加工精度を高めるための工夫が重要です。真鍮はやわらかい金属であり、切削時に振動が生じやすいため、工具やマシンの安定性が要求されます。例えば、切削速度や刃先形状の最適化、冷却剤の適切な使用などがポイントです。また、加工時に過剰な切り込みや進め方は歪みやすくなりますので、適切な切削条件を設定することが重要です。具体的には、工具の交換タイミングや刃先の状態の確認も大切です。これらの工夫により、真鍮フライス加工において高い加工精度を実現することができます。
真鍮加工に適した冷却剤の使用
真鍮フライス加工において、重要なポイントの一つは適切な冷却剤の使用です。真鍮は加工中に熱を持ちやすいため、冷却剤を使うことで加工品質を保ち、工具の寿命を延ばすことができます。例えば、冷却剤を使用しない場合、真鍮が過熱してしまい、加工精度が低下したり、工具がすぐに摩耗したりする可能性があります。
冷却剤の中でも、水や油系のものが一般的に使われます。水は安価で環境に優しい反面、真鍮の錆びを促進する可能性があるため、注意が必要です。一方、油系の冷却剤は錆びにくいですが、取り扱いには火災の危険性があるため、安全に取り扱うことが不可欠です。
真鍮フライス加工を円滑に進めるためには、適切な冷却剤を選び、正しく使用することが重要です。正しい冷却剤の選択と適切な取り扱いにより、加工効率を向上させることができます。
快削黄銅のフライス加工におけるコツ
快削黄銅と一般黄銅の違い
真鍮フライス加工では、快削黄銅と一般黄銅の違いを理解することが重要です。快削黄銅は切削時に刃先がすぐれて摩耗するため、高速での切削が可能です。一方、一般黄銅は研削粒子が均一でないため切削時に摩耗が進みにくい特徴があります。快削黄銅は高速切削向きであり、一般黄銅は研削が進む速度が比較的遅いです。例えば、快削黄銅は精密機械部品の加工に適しています。一方、一般黄銅は建築用金物や装飾品などに使用されています。したがって、使用する材料に合わせた加工方法を選択することが重要です。真鍮フライス加工においては、材料特性を考慮し、適切な工具と加工条件を選定することがポイントです。
快削性を活かした加工方法
真鍮フライス加工では、表面の仕上げや精度が重要です。真鍮は柔らかく、熱に弱い性質がありますので、加工時には気をつける必要があります。例えば、適切な切削速度と刃先形状を選ぶことが重要です。速度が速すぎると真鍮が溶けるおそれがあり、逆に遅すぎると加工がうまくいかないことがあります。また、刃先が適切でないと表面が荒れやすくなるため、加工品の仕上がりに影響が出ます。このようなポイントに留意することで、真鍮フライス加工をより効果的に行うことができます。
精度と速度を上げるためのテクニック
真鍮フライス加工において気をつけるべきポイントは何でしょうか? 真鍮は加工しやすい素材ですが、加工時に注意すべき点があります。まず、刃物の選択が重要です。硬い真鍮を綺麗に加工するためには、適切な刃物を選ぶことが必要です。また、適切な切削速度や切削量もポイントです。加工時の適切な速度や量を守ることで、作業効率が向上し精度も高まります。例えば、高速回転での加工は加工面が滑らかになりますが、適切な切削速度を守ることで刃物の寿命が延びるという利点もあります。真鍮フライス加工を行う際は、これらのポイントに気をつけて効果的に作業を行いましょう。
真鍮切削加工時の注意点
加工時の変形に注意
真鍮フライス加工を行う際には、加工時の変形に注意が必要です。真鍮は加工中に熱を加えると加工後に変形する可能性があります。この変形は素材の性質から避けることが難しい場合があります。そのため、適切な冷却技術や適切な工具を使用して、変形を最小限に抑える必要があります。例えば、加工途中で適度に冷却を行うことで、変形を軽減することができます。また、加工時に適切な切削速度や切削深さを設定することも重要です。これらのポイントに注意することで、真鍮フライス加工において変形を最小限に抑えることができます。
表面仕上げの品質管理
真鍮フライス加工において品質を保つために注意すべきポイントがあります。真鍮は美しい光沢が特徴であり、正確な寸法や仕上げが求められます。まず、切削工具の選択が重要です。高品質な切削工具を使用することで、綺麗な仕上がりを実現できます。さらに、適切な切削速度と切削量を設定することも重要です。適切な設定で加工することで、真鍮の熱による変形を防ぎます。具体例として、加工中に冷却液を使用して適切な温度を保つことが挙げられます。最後に、加工後の品質チェックを欠かさず行うことで、問題があれば早期に発見し修正できます。これらのポイントを押さえることで、真鍮フライス加工において品質を維持することができます。
切りくずの処理と環境への配慮
真鍮フライス加工では、切りくずの処理と環境への配慮が重要です。真鍮は、金属部品や装飾品などに広く使用されています。加工時に発生する切りくずは、環境への負荷となる可能性があります。そのため、切りくずの適切な処理が必要です。例えば、リサイクルや再利用が一般的な方法です。また、加工現場での切りくずの飛散を防ぐため、作業環境を清潔に保つことも大切です。環境への配慮は、今後ますます重要となるでしょう。真鍮フライス加工業界が持続可能な方法で成長するためには、環境への配慮が欠かせません。今後も、環境に配慮した取り組みが求められることでしょう。
金属加工の手法と真鍮加工の応用
金属加工の基本手法概要
真鍮のフライス加工を行う際に気をつけるべきポイントはいくつかあります。まず、真鍮は比較的柔らかい金属であるため、適切な工具や刃物を使用することが重要です。また、適切な切削速度や切削深さを設定することも欠かせません。これにより、加工精度を高めることができます。
さらに、冷却液を用いて加工を行うことで、真鍮の加工時に発生する熱を逃がし、加工効率を向上させることができます。例えば、切削中に過度に熱を加えると、真鍮が変色してしまう可能性があるため、冷却液の適切な使用は重要です。
以上のポイントに気をつけながら真鍮のフライス加工を行うことで、効率的かつ高品質な加工が可能となります。
真鍮フライス加工の応用事例
真鍮フライス加工は、金属を削る工程で使われる加工方法の一つです。この加工方法は、精密な部品を作る際に重要な役割を果たします。真鍮は耐食性に優れ、美しい外観が特徴です。そのため、真鍮フライス加工は高級な時計や宝飾品、車の部品などの製造に広く活用されています。
真鍮フライス加工を行う際に気をつけるべきポイントはいくつかあります。まず、適切な切削速度と刃先の選定が重要です。また、素材の硬さや形状によって適切な工具を選ぶことも大切です。さらに、加工中に十分な冷却を行うことで、部品の精度や仕上がりを向上させることができます。
真鍮フライス加工を行う際には、これらのポイントをしっかり押さえて作業を行うことが大切です。そのようにすることで、高品質な部品を効率よく製造することができます。
真鍮加工技術の将来性と発展
真鍮フライス加工では、気をつけるべきポイントがいくつかあります。まず、適切な切削速度や切削深さを設定することが重要です。これにより、作業効率を向上させるだけでなく、加工精度も確保できます。また、適切な冷却液の使用も欠かせません。冷却液が不十分だと切削工具が摩耗しやすくなり、加工精度が低下します。
さらに、作業中には定期的に工具の状態を確認し、交換やメンテナンスを行うことも大切です。劣化した工具を使い続けると、加工品質が損なわれるばかりか、安全面でもリスクが高まります。そのため、定期的な点検と保守が欠かせません。
これらのポイントに気をつけることで、真鍮フライス加工の品質向上と作業効率の向上が期待できます。加工業界において、これらの技術を熟知することが将来性を見据えた重要な要素となります。
金属加工における一般的な注意点と対策
機械のメンテナンスと安全管理
真鍮のフライス加工では、特定のポイントに気をつける必要があります。まず、真鍮は加工時に切削抵抗が大きく、工具の摩耗が激しいため、適切な切削条件を設定することが重要です。この点に気をつけないと、工具の寿命が短くなり、コストがかさんでしまいます。
さらに、真鍮は熱や振動に弱い性質を持っていますので、適切な冷却や潤滑を施すことも重要です。例えば、適切な切削液を使用することで、加工時の熱を逃がし、切削精度を高めることができます。
そのため、真鍮のフライス加工を行う際には、切削条件や冷却方法に注意を払うことが大切です。これらのポイントを守ることで、効率的かつ安全な加工が可能となります。
加工誤差の原因と対策
真鍮のフライス加工を行う際に気をつけるべきポイントはいくつかあります。まず、加工誤差の原因として、切削速度や切削量、冷却方法などが挙げられます。これらが適切でないと、加工精度が低下し、不良品が増える可能性があります。そのため、適切な切削条件を設定し、適切な冷却を行うことが重要です。例えば、適切な刃先形状や刃先材質を選択することで、加工品質を向上させることができます。また、加工中の振動や歪みも加工精度に影響を与えるため、適切な工具の選択や固定方法も考慮する必要があります。これらの対策を講じることで、真鍮のフライス加工において良好な加工精度を確保することができます。
効率的な生産体制の構築
真鍮フライス加工を行う際に気をつけるべきポイントについて考えてみましょう。真鍮は、加工性が良い金属であり、正確な加工が求められます。まず、切削速度や切削量を適切に設定することが重要です。切削速度が速すぎると工具の消耗が早くなり、逆に遅すぎると切れ味が悪くなります。また、適切な冷却液や潤滑剤を使用することも大切です。これにより、切削時の摩擦や熱を抑えることができ、加工精度を高めることができます。さらに、工具の定期的なメンテナンスや交換も忘れてはいけません。適切な加工条件の下で作業を行うことで、真鍮フライス加工における品質向上と効率的な生産が実現できるのです。
まとめ
真鍮フライス加工では、材料の性質を考慮しながら適切な工具や切削条件を選択することが重要です。真鍮は柔らかい材料であり、切削時に振動や刃先の焼けを起こしやすいため、適切な冷却や刃先の交換を行うことがポイントです。また、適切な切削速度や切削深さを設定することで、品質の高い加工を実現することができます。