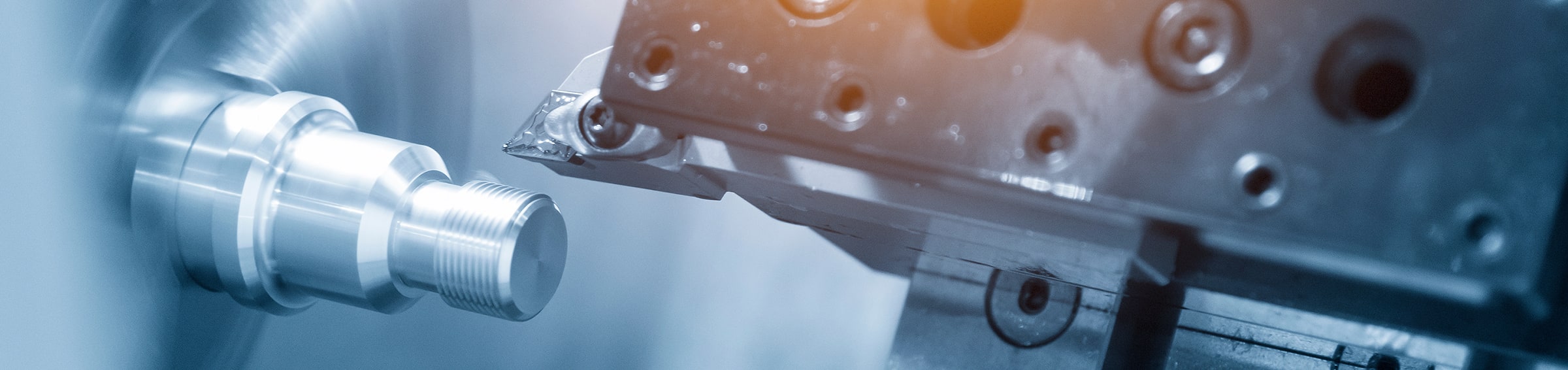
加工技術 column
黄銅のフライス加工における工具寿命を延ばすためのポイント
黄銅のフライス加工を行う際、工具寿命の延長は生産効率を高め、コストを削減するために非常に重要です。しかし、「どうすれば工具の寿命を延ばせるのか?」と悩む方も多いのではないでしょうか?そこで本記事では、黄銅のフライス加工における工具寿命の関係性を掘り下げ、実践的なポイントを詳しく解説します。
この文章は、次のような方におすすめです:
- 黄銅のフライス加工を行っているが、工具の摩耗が気になる
- より効率的に加工を行いたいが、どう進めればよいのかわからない
- 工具寿命を延ばすための具体的なテクニックや知識を得たい
黄銅の特性を理解し、適切な加工条件や工具の選定を実施することで、加工のクオリティとコストパフォーマンスが大きく向上します。この記事を通じて、あなたの加工技術を一段と高めるヒントを得ていただければ幸いです。
1. 黄銅のフライス加工と工具寿命の関係
1-1. 黄銅の切削加工における最適な切削速度と送りの設定方法
黄銅のフライス加工において、工具寿命を延ばすためにはいくつかのポイントがあります。まず、適切な切削速度と送りを設定することが重要です。これにより、工具の摩耗を減らし、長持ちさせることができます。例えば、切削速度が速すぎると、工具が熱を持ちすぎて壊れやすくなります。一方、遅すぎると加工効率が下がります。
さらに、冷却剤を使用することで、工具の温度を下げ、寿命を延ばすことができます。冷却剤は、切削中の摩擦を減らし、工具を保護します。例えば、黄銅を加工する際に適切な冷却剤を使うと、工具が長持ちします。
このように、適切な設定と冷却剤の使用が、黄銅のフライス加工における工具寿命を延ばす鍵となります。
1-2. 快削黄銅の特性と加工性の理解
黄銅のフライス加工において工具寿命を延ばすためには、いくつかのポイントがあります。まず、工具の材料や形状が重要です。例えば、硬い工具を使うことで、黄銅の加工中に工具が摩耗しにくくなります。次に、加工条件を見直すことも大切です。適切な回転速度や送り速度を設定することで、工具の負担を減らし、寿命を延ばすことができます。
具体的には、加工中に冷却剤を使うことも効果的です。冷却剤は工具を冷やし、摩耗を防ぐ助けになります。このように、工具の選び方や加工条件を工夫することで、黄銅のフライス加工における工具寿命を大きく延ばすことが可能です。これらのポイントを意識することで、より効率的な加工が実現できるでしょう。
1-3. 真鍮切削に適した工具の選定方法
真鍮のフライス加工を行う際、工具の寿命を延ばすことはとても大切です。まず、適切な工具を選ぶことが重要です。なぜなら、工具が合っていないと、すぐに摩耗してしまうからです。例えば、硬い真鍮を加工するには、刃先が鋭く、耐久性のある工具が必要です。
次に、加工条件を見直すことも効果的です。加工速度や送り速度を適切に設定することで、工具の負担を軽減し、寿命を延ばすことができます。例えば、あまり速く削りすぎると、工具が熱を持ち、早く壊れてしまいます。
工具を定期的に点検し、必要に応じてメンテナンスを行うことも大切です。これらのポイントを守ることで、真鍮のフライス加工における工具の寿命を大いに延ばすことができます。
1-4. 長寿命の工具を選ぶための基準とメンテナンス方法
黄銅のフライス加工において、工具の寿命を延ばすことはとても大切です。まず、良い工具を選ぶことが重要です。例えば、硬い素材でできた工具は長持ちします。また、加工の際には適切なスピードと圧力を保つことも必要です。これにより、工具が過度に摩耗するのを防げます。さらに、工具を定期的に点検し、必要に応じてメンテナンスを行うことも大切です。例えば、刃先が鈍くなったら研ぎ直すことで、工具を長く使うことができます。これらのポイントを守ることで、黄銅のフライス加工における工具の寿命を大いに延ばすことができます。これにより、効率的に作業を進めることができるのです。
1-5. 銅の切削加工における具体的なポイントと注意点
黄銅のフライス加工では、工具の寿命を延ばすことがとても大切です。まず、工具の寿命を延ばす理由は、長持ちすることでコストを抑えられるからです。例えば、工具を頻繁に交換すると、その分だけお金がかかります。次に、工具を長持ちさせるためには、適切な切削条件を設定することが重要です。具体的には、切削速度や送り速度を調整することで、工具の摩耗を減らすことができます。また、冷却剤を使うことで、工具の温度を下げ、寿命を延ばすことも可能です。工具の定期的な点検やメンテナンスも忘れずに行いましょう。これらのポイントを守ることで、黄銅のフライス加工における工具の寿命を効果的に延ばすことができます。
まとめ
黄銅のフライス加工で工具寿命を延ばすためには、適切な切削条件の設定が重要です。切削速度や送り速度を最適化し、冷却剤を効果的に使用することで熱の蓄積を抑えます。また、工具の材質選定や定期的なメンテナンスも寿命向上に寄与します。
真鍮加工のプロが教える!フライス加工での仕上げテクニックまとめ
「フライス加工で真鍮を美しく仕上げたいけど、どこから始めればいいのか分からない……」そんなお悩みを抱えているあなたに、お役立ちの情報をお届けします。
本記事では、真鍮加工におけるフライス加工のコツやテクニックについて、わかりやすく解説します。特に、美しい仕上がりを実現するための重要なポイントに焦点を当てますので、初心者の方から経験豊富な方まで、幅広くご参考にしていただける内容となっています。
真鍮はその美しい外観や加工のしやすさから、さまざまな製品に利用されていますが、仕上げが命と言えるほど、完成度が求められます。質の高い仕上げがなければ、いくら優れた材料でもその魅力を引き出すことはできません。
さあ、フライス加工の基本から、テクニック、注意点まで、あなたの真鍮加工スキルを一段と向上させるための情報を一緒に見ていきましょう!
1. フライス加工で真鍮を美しく仕上げるコツ
1-1. フライス加工の基本と真鍮の特性
フライス加工で真鍮を美しく仕上げるコツは、まず基本を理解することです。真鍮は金属の一種で、加工しやすく、見た目も美しいです。そのため、フライス加工を使うことで、細かい形やデザインを作ることができます。具体的には、刃物の角度や速度を調整することで、真鍮の表面を滑らかに仕上げることができます。例えば、ゆっくりとした速度で加工すると、傷が少なく、きれいな仕上がりになります。また、加工後には磨きをかけることで、さらに輝きを増すことができます。まとめると、フライス加工を使って真鍮を美しく仕上げるためには、基本をしっかり学び、丁寧に作業することが大切です。これにより、素晴らしい作品を作ることができるでしょう。
1-2. NCフライスを使った真鍮加工のメリット
真鍮加工において、NCフライスを使うことには多くのメリットがあります。まず、NCフライスは非常に精密な加工ができるため、真鍮の部品を美しく仕上げることができます。例えば、複雑な形状の部品でも、正確に削り出すことができるのです。この精度があるため、製品の品質が向上し、お客様からの信頼も得られます。
また、NCフライスは自動化された機械なので、作業の効率も良くなります。人手で行うよりも早く、同じ品質の部品を大量に作ることができます。これにより、コストを抑えながらも生産性を高めることが可能です。
NCフライスを使った真鍮加工は、高品質な製品を効率的に作るための優れた方法です。これからも多くの業界で活用されるでしょう。
1-3. 表面粗さを減少させるためのテクニック
フライス加工で真鍮を美しく仕上げるためには、いくつかのコツがあります。まず、仕上げを良くする理由は、見た目がきれいになるだけでなく、製品の耐久性も向上するからです。例えば、表面を滑らかにすることで、さびにくくなったり、触り心地が良くなったりします。
具体的なテクニックとしては、まず粗い刃物を使って大まかに削り、その後、細かい刃物に変えて仕上げる方法があります。また、仕上げの前に真鍮の表面をきれいに掃除することも大切です。仕上げを行った後は、専用のクリーナーを使って輝きを出すと、さらに美しい仕上がりになります。
これらのテクニックを使うことで、フライス加工での真鍮の仕上げがより素晴らしくなります。
1-4. 高精度な部品を作るためのマシニングセンタの活用法
フライス加工で真鍮を美しく仕上げるコツについてお話しします。まず、真鍮は金属の中でも加工しやすく、見た目が美しいため、人気があります。理由として、フライス加工を使うことで、細かい形やデザインを作れるからです。例えば、時計の部品や装飾品など、真鍮を使った商品は多くの人に愛されています。
具体的には、フライス加工では工具を使って金属を削り、滑らかな表面を作ります。その際、冷却液を使うことで、金属が熱で変形するのを防ぎます。また、仕上げの段階で磨きをかけると、さらに美しい光沢が出ます。
このように、フライス加工を使うことで真鍮を美しく仕上げることができます。これが、真鍮加工が多くの人に支持される理由です。
1-5. フライス加工での仕上がりを向上させるための具体的な方法
フライス加工で真鍮を美しく仕上げるためには、いくつかのコツがあります。まず、仕上げの段階で使う道具や刃物が大切です。鋭い刃物を使うと、滑らかな表面が得られます。次に、加工速度や送り速度を適切に設定することが重要です。速すぎると傷がつきやすく、遅すぎると効率が悪くなります。具体的な例として、真鍮のパーツを加工する際は、まず粗い加工を行い、その後に細かい加工を進めることで、より美しい仕上がりになります。仕上げの際には研磨剤を使うことで、さらに光沢を出すことができます。このように、フライス加工にはいくつかのポイントがあり、これを守ることで真鍮を美しく仕上げることができるのです。
まとめ
真鍮加工のプロが伝授するフライス加工の仕上げテクニックを紹介します。高精度な仕上げを実現するための工具選びや切削条件、仕上げ段階での注意点など、実践的なノウハウが満載。これらのテクニックを駆使することで、より美しい仕上がりを目指しましょう。
フライス盤による金属加工の基本:重要な要素を徹底解説
金属加工に興味があるけれど、「フライス盤についてよく知らない……」と感じている方はいませんか?そんなあなたのために、フライス盤による金属加工の基本を徹底解説します。
この記事は、以下のような方に特に役立ちます。
- フライス盤とは何かを知りたい
- フライス盤を使った金属加工のプロセスについて理解したい
- 成功する金属加工にはどんな重要な要素があるのかを学びたい
フライス盤は、金属加工業界で非常に重要な役割を果たしており、正しく使うことで高精度な部品を生み出すことができます。しかし、初心者の方にとっては、その操作やポイントが難しく感じられるかもしれません。このガイドでは、フライス盤の基本的な使い方から、効果的な加工のための重要な要素まで、わかりやすく解説します。
金属加工の世界をもっと深く理解し、スキルを磨くための第一歩を踏み出しましょう!
1. フライス盤による金属加工における重要要素の基本
1-1. フライス加工とは何か
フライス加工とは、金属を削って形を作る技術のことです。この技術は、特に機械や部品を作るときにとても重要です。なぜなら、フライス盤という機械を使うことで、金属を正確に削ることができるからです。例えば、車の部品や家電製品の部品など、私たちの身の回りにはフライス加工で作られたものがたくさんあります。
フライス盤は、金属を固定して回転する刃物で削る仕組みです。この方法を使うと、複雑な形や細かい部分も簡単に作ることができます。だから、フライス加工は工業の現場でとても重宝されています。
フライス加工は金属加工の基本であり、私たちの生活を支える大切な技術です。
1-2. フライス加工の歴史と発展
フライス盤による金属加工は、非常に重要な技術です。まず、この技術がなぜ大切かというと、金属の形を正確に作ることができるからです。例えば、自動車の部品や機械の部品は、フライス盤を使って作られます。次に、フライス盤の基本的な要素には、刃物の種類や加工する素材の特性があります。刃物の種類によって、切れるスピードや仕上がりが変わります。そして、素材によっても加工方法が異なります。フライス盤は、工業の進歩に大きく貢献しています。このように、フライス盤による金属加工は、私たちの生活を支える重要な技術であり、これからも必要とされるでしょう。
2. フライス盤による金属加工における重要要素の種類
2-1. フライス加工の種類
フライス盤による金属加工は、金属を形作るための重要な技術です。まず、フライス盤を使う理由は、さまざまな形状を正確に作ることができるからです。例えば、歯車や部品を作るときに便利です。次に、フライス盤にはいくつかの種類があります。一般的なものとしては、縦型フライス盤や横型フライス盤があります。それぞれの特徴を理解することが大切です。フライス盤を使った金属加工は、工業製品の製造に欠かせない技術です。このように、フライス盤は金属加工の基本であり、さまざまな製品を作るための重要な要素です。フライス盤を使うことで、私たちの生活に必要なものが生まれています。
2-2. 各種フライス加工の特徴
フライス盤による金属加工は、金属を形作るための重要な方法です。まず、フライス盤を使う理由は、金属を正確に切り取ることができるからです。たとえば、自動車や飛行機の部品を作るとき、正確さがとても大切です。次に、フライス盤にはいくつかの種類があり、それぞれに特長があります。例えば、垂直フライス盤は上下に動く刃を使い、横型フライス盤は横に動く刃を使います。これによって、さまざまな形状の金属を加工することができます。フライス盤による金属加工は、精密な製品を作るために欠かせない技術です。これにより、私たちの日常生活で使う多くのものが作られています。
3. フライス盤の構成と種類
3-1. フライス盤の基本構成
フライス盤は金属加工において非常に重要な機械です。フライス盤の基本構成を理解することは、金属を加工するための第一歩です。まず、フライス盤は主にモーター、テーブル、スピンドル、そして刃物から成り立っています。モーターは機械を動かし、テーブルは加工する金属を支えます。スピンドルは刃物を回転させる部分で、刃物が金属を削る役割を果たします。
例えば、フライス盤を使うことで、金属の部品を正確に切り出したり、形を整えたりすることができます。このような加工は、自動車や機械の部品作りに欠かせません。フライス盤の基本を知ることで、金属加工の世界がより身近に感じられるでしょう。フライス盤は、私たちの生活を支える大切な道具なのです。
3-2. フライス盤の種類とその用途
フライス盤は金属加工においてとても重要な機械です。まず、フライス盤を使うことで、金属の形を自由に変えることができます。なぜなら、フライス盤は回転する刃物で金属を削るからです。例えば、車の部品や機械の部品を作るときに、フライス盤を使うと正確な形に加工できます。
また、フライス盤にはいくつかの種類があります。立てフライス盤や横フライス盤などがあり、それぞれに特別な使い方があります。立てフライス盤は縦に刃を使って削るのに対し、横フライス盤は横に刃を使います。これにより、さまざまな形を作ることができます。
フライス盤は金属加工に欠かせない道具であり、正確な加工を可能にするための重要な要素です。
4. フライス盤による金属加工における重要要素を活用する方法
4-1. 効果的なフライス加工のテクニック
フライス盤による金属加工は、とても重要な技術です。まず、フライス盤を使うことで、金属をさまざまな形に加工できます。例えば、部品を作るときに、正確なサイズや形が必要です。この時、フライス盤はとても役立ちます。また、フライス盤は金属を削るスピードが速いため、大量生産にも向いています。さらに、フライス盤を使うと、複雑な形状も簡単に作ることができます。これにより、工場などで効率よく作業が進みます。フライス盤があることで、私たちの生活に必要な製品がたくさん作られ、便利な世界が実現します。フライス盤は金属加工の基本であり、これからも重要な役割を果たすでしょう。
4-2. フライス加工の際の注意点
フライス盤による金属加工は、非常に重要な技術です。まず、フライス盤を使うことで、金属を正確に切り出すことができます。なぜなら、フライス盤は回転する刃物で金属を削るため、細かい形状を作るのが得意だからです。例えば、機械の部品や工具など、さまざまなものを作ることができます。このように、フライス盤は精密な加工ができるため、工業の現場で広く使われています。
さらに、フライス盤を使う際には、安全に注意することが大切です。例えば、作業中は保護眼鏡をつけたり、手を刃物に近づけないようにしたりすることが必要です。このように、フライス盤による金属加工は、正確さと安全が求められる作業です。だからこそ、この技術を学ぶことはとても重要なのです。
5. 鉄の加工方法とフライス盤による金属加工における重要要素
5-1. 鉄の特性と加工方法
フライス盤による金属加工は、金属を形作るための重要な技術です。まず、フライス盤は金属を削るための機械で、特に精密な形状を作るのに適しています。なぜこれが重要かというと、正確な部品が必要な自動車や航空機の製造に欠かせないからです。例えば、自動車のエンジン部品は、フライス盤を使って細かく加工されます。これにより、部品同士がぴったり合い、安全に動くことができます。さらに、フライス盤は様々な形に加工できるため、デザインの自由度も高いです。フライス盤による金属加工は、精密さと効率を両立させるために不可欠であり、現代の製造業において非常に重要な役割を果たしています。
5-2. フライス盤を用いた鉄の加工事例
フライス盤を使った鉄の加工は、金属を形作るためのとても重要な方法です。まず、フライス盤は金属を削る機械で、精密な形を作ることができます。なぜこれが大切かというと、正確な部品が必要な機械や車の製造に欠かせないからです。例えば、自動車のエンジン部品は、フライス盤で加工されることで、強くて耐久性のあるものになります。このように、フライス盤を使うことで、私たちの生活に必要なものを作ることができるのです。フライス盤による金属加工は、私たちの生活を支えるために欠かせない技術であり、今後も重要な役割を果たすでしょう。
まとめ
フライス盤による金属加工は、精密な形状を作り出すための重要な技術です。主な要素には、切削工具の選定、加工条件の設定、素材の特性理解が含まれます。これらを適切に管理することで、高品質な仕上がりを実現し、効率的な生産が可能になります。
精密金属加工におけるフライス加工技術の重要性とは
「精密金属加工におけるフライス加工技術の重要性を知りたいけれど、具体的にどうやって学べばいいのか分からない…」そんな悩みを抱えている方はいませんか?この問題に応えるために、本記事では「フライス加工技術の全貌」をご紹介します。
もしあなたが以下のことに興味があるなら、ぜひお読みください。
- 精密金属加工とは何か?
- フライス加工技術がなぜ重要なのか?
- どのようにしてフライス加工を習得すればいいのか?
- 精密な加工を実現するためのポイントは何か?
精密金属加工は多くの産業において不可欠な技術であり、特にフライス加工は、その精度と多様性から非常に重要な役割を果たしています。さらなる成長を目指すためには、この技術を深く理解し、マスターすることが必要です。
本記事では、フライス加工技術の基本からその重要性、そして具体的な学び方や活用法まで幅広くお伝えします。あなたの技術力向上の手助けとなることを願っています。
1. 精密金属加工で求められるフライス技術の基本
1-1. フライス加工とは何か
フライス加工は、金属を切り削る技術で、とても重要です。まず、フライス加工は精密金属加工の一部で、金属の形を作るために使われます。この技術が必要な理由は、正確な形やサイズを作ることができるからです。例えば、自動車の部品や航空機のパーツなど、精密な部品が必要なものに使われています。
具体的には、フライス盤という機械を使って、金属の表面を削ったり、溝を作ったりします。これにより、部品がしっかりと機能するようになります。フライス加工がなければ、私たちの生活に欠かせない製品が作れなくなるかもしれません。
フライス加工技術は、精密金属加工において非常に重要であり、私たちの生活を支える大切な役割を果たしています。
1-2. フライス加工の歴史と進化
フライス加工技術は、精密金属加工において非常に重要です。なぜなら、この技術を使うことで、金属を正確な形に削り出すことができるからです。例えば、車の部品や機械のパーツを作るとき、フライス加工が必要です。この技術がなければ、部品の精度が低くなり、製品全体の品質が悪くなってしまいます。
フライス加工は、昔から使われてきた方法ですが、今ではコンピュータ制御の機械も登場し、さらに精度が高まっています。これにより、より複雑な形状の部品も簡単に作れるようになりました。
フライス加工技術は、精密金属加工に欠かせないものであり、これからもますます重要になるでしょう。
2. 精密金属加工で求められるフライス技術の種類
2-1. 一般的なフライス加工の種類
フライス加工技術は、精密金属加工においてとても重要です。なぜなら、フライス加工を使うことで、金属を正確に切り取ったり、形を整えたりできるからです。例えば、自動車や電子機器の部品を作る際に、フライス加工は欠かせません。これにより、部品がしっかりと機能し、製品全体の品質が向上します。
さらに、フライス加工はさまざまな形状に対応できるため、デザインの自由度も高まります。これにより、企業は独自の製品を作り出すことができ、競争力を持つことができます。
フライス加工技術は精密金属加工において、品質やデザインの向上に寄与するため、とても重要な技術なのです。
2-2. 特殊なフライス加工技術
フライス加工技術は、精密金属加工において非常に重要です。まず、この技術を使うことで、金属を正確に切り出したり、形を整えたりすることができます。理由は、精密な部品が必要な製品が多く、例えば自動車や航空機の部品などは、少しの誤差でも大きな問題を引き起こすからです。
具体的な例として、航空機のエンジン部品があります。これらは非常に高い精度が求められるため、フライス加工技術が不可欠です。この技術があることで、安全で信頼性の高い製品が作られ、私たちの生活が守られています。
フライス加工技術は精密金属加工において欠かせないものであり、私たちの生活を支える重要な役割を果たしています。
3. 精密金属加工で求められるフライス技術の注意事項
3-1. 高精度加工のためのポイント
フライス加工技術は、精密金属加工においてとても重要です。まず、フライス加工は金属を正確に削る技術で、部品の形を整えるのに役立ちます。これがなぜ大切かというと、精密な部品は機械や電子機器に欠かせないからです。例えば、自動車やスマートフォンの部品は、正確に作られていないと正常に動きません。
さらに、フライス加工は複雑な形状を作ることもできるため、デザインの自由度が高まります。これにより、さまざまな産業でのニーズに応えることができます。フライス加工技術が進化することで、より高品質な製品が生まれ、私たちの生活が便利になります。つまり、フライス加工技術は精密金属加工に欠かせない、非常に重要な技術なのです。
3-2. よくある失敗とその回避策
フライス加工技術は、精密金属加工においてとても重要です。なぜなら、フライス加工は金属を正確な形に削り出すことができるからです。例えば、機械の部品や工具など、細かい形が必要なものを作るときに使います。この技術がなければ、部品がうまく合わず、機械が動かなくなってしまうこともあります。
また、フライス加工は、さまざまな素材に対応できるため、多くの産業で利用されています。自動車や航空機、電子機器など、私たちの生活に欠かせないものを支える技術です。
フライス加工技術は精密金属加工において欠かせないものであり、私たちの生活を支える重要な役割を果たしています。この技術があるおかげで、私たちは安全で高性能な製品を手に入れることができるのです。
4. MC加工とフライス加工の違い
4-1. MC加工の基本概念
フライス加工技術は、精密金属加工において非常に重要です。なぜなら、フライス加工は金属の形を正確に整えるための方法だからです。例えば、機械の部品や工具を作るとき、フライス加工を使うことで、必要な形やサイズを正確に作ることができます。これにより、部品同士がうまく組み合わさり、機械がきちんと動くのです。
また、フライス加工はさまざまな材料に対応できるため、柔軟性があります。例えば、アルミニウムやステンレスなど、異なる金属でも加工が可能です。これらの理由から、フライス加工技術は精密金属加工に欠かせない技術と言えるでしょう。フライス加工は高品質な製品を作るために必要な技術であり、今後もその重要性は増していくでしょう。
4-2. フライス加工との比較
フライス加工技術は、精密金属加工においてとても重要です。なぜなら、この技術を使うことで、金属の形を正確に作ることができるからです。例えば、機械の部品や自動車のパーツなど、細かい形が必要なものに使われます。フライス加工では、金属を削ることで、必要な形を作り出します。この方法は、他の加工方法と比べて、より精密な仕上がりが可能です。
また、フライス加工は、複雑な形状を一度に作ることができるため、時間やコストを節約することにもつながります。これらの理由から、フライス加工技術は精密金属加工において欠かせない存在です。フライス加工は、ものづくりにおいて高い精度と効率を実現するために非常に重要な技術です。
4-3. それぞれの利点と適用例
フライス加工技術は、精密金属加工において非常に重要です。なぜなら、この技術を使うことで、金属を正確な形に削り出すことができるからです。例えば、自動車の部品や電子機器のパーツなど、精密さが求められる製品には欠かせません。このように、フライス加工は高い精度を必要とする製品を作るための基本的な技術となっています。
さらに、フライス加工技術を使うことで、複雑な形状や細かいデザインを持つ部品も作ることができます。これにより、さまざまな産業でのニーズに応えることができます。フライス加工技術は、精密金属加工において必要不可欠な技術であり、未来の製品開発に大きな影響を与えるでしょう。
5. 精密金属加工の定義と特徴
5-1. 精密金属加工とは
精密金属加工は、金属をとても細かく加工する技術です。この技術は、特に精度が求められる部品を作るために重要です。なぜなら、精密な部品が必要な機械や製品がたくさんあるからです。例えば、スマートフォンや自動車の部品には、非常に正確な加工が必要です。フライス加工という技術を使うことで、金属を削ったり、形を作ったりできます。この方法は、複雑な形でも高い精度で加工できるため、非常に役立ちます。精密金属加工におけるフライス加工技術は、現代の製品や機械を支える大切な技術です。この技術があるおかげで、私たちの生活がより便利で快適になっています。
5-2. 精密金属加工の重要性と応用分野
精密金属加工におけるフライス加工技術は非常に重要です。なぜなら、この技術は金属を正確に削り出して形を作ることができるからです。例えば、車の部品や機械の部品など、精密な形が必要なものに使われます。フライス加工では、回転する刃物を使って金属を削り、希望の形を作ります。この技術があることで、製品の品質が向上し、故障を減らすことができます。さらに、フライス加工はさまざまな素材に対応できるため、幅広い分野で活躍しています。フライス加工技術は精密金属加工において欠かせないものであり、私たちの生活を支える重要な役割を果たしています。
まとめ
精密金属加工におけるフライス加工技術は、高精度な部品製造に不可欠です。この技術は、複雑な形状や細かい寸法を実現し、製品の品質向上に寄与します。また、多様な材料に対応できる柔軟性があり、効率的な生産プロセスを可能にします。したがって、フライス加工は現代の製造業において重要な役割を果たしています。
これだけは知っておきたい!真鍮フライス加工の失敗しないためのガイド
真鍮のフライス加工に挑戦したいけれど、「どんなことに気を付ければいいのか分からない」と思っている方は多いのではないでしょうか?その悩みを解消するために、本ガイドでは真鍮のフライス加工における注意点を詳しく解説します。
もしあなたが、
- 真鍮を使った加工について基礎から学びたい
- フライス加工の際に避けるべき失敗を知りたい
- 効率的で高品質な仕上がりを目指している
このガイドはそんな方々のために作成されました。真鍮はその美しい外観と優れた加工性から多くの場面で利用される素材ですが、取り扱いには特有の注意点があります。加工時に気を付けるべきポイントを押さえることで、思わぬトラブルや失敗を未然に防ぐことができます。
この記事では、真鍮のフライス加工を行う際に知っておくべき重要な知識や実践的なテクニックを、具体的かつわかりやすくお伝えします。あなたの加工技術を一段と向上させるために、ぜひ最後までお付き合いください。
1. 真鍮のフライス加工で注意すべき点
1-1. 真鍮の特性とその影響
真鍮のフライス加工を行う際には、いくつかの注意点があります。まず、真鍮は柔らかい金属で、加工しやすいですが、切削時に熱を持ちやすいです。このため、冷却剤を使って金属が過熱しないようにすることが大切です。例えば、加工中に真鍮が焼けてしまうと、表面が傷んでしまい、製品の品質が悪くなります。また、刃物の選び方にも注意が必要です。適切な刃物を使わないと、切れ味が悪くなり、加工精度が落ちてしまいます。加工後の表面処理も重要です。きれいな仕上がりにするためには、磨きやコーティングを行うことが必要です。このように、真鍮のフライス加工では、いくつかのポイントに気を付けることで、良い結果を得ることができます。
1-2. 適切な切削条件の設定
真鍮のフライス加工を成功させるためには、適切な切削条件を設定することがとても大切です。まず、なぜこれが重要かというと、正しい条件で加工しないと、部品が壊れたり、仕上がりが悪くなったりするからです。例えば、切削速度や送り速度を間違えると、真鍮が熱を持ちすぎて変形することがあります。
具体的には、切削速度は材料の硬さや工具の種類に応じて調整する必要があります。もし切削速度が速すぎると、工具がすぐに摩耗してしまい、逆に遅すぎると加工時間が無駄に長くなります。これらを考慮して、最適な条件を見つけることが大切です。
真鍮のフライス加工では、適切な切削条件の設定が成功の鍵です。注意深く設定を行うことで、より良い結果を得ることができます。
1-3. 切削工具の選定と管理
真鍮のフライス加工を成功させるためには、いくつかの重要なポイントがあります。まず、適切な切削工具を選ぶことが大切です。理由は、工具が正しくないと、加工がうまくいかず、部品が壊れたり、仕上がりが悪くなったりするからです。例えば、真鍮用の専用工具を使うと、スムーズに加工でき、仕上がりもきれいになります。
次に、工具の管理も重要です。工具が鈍くなると、加工に時間がかかり、余計なコストがかかってしまいます。定期的に工具を点検し、必要に応じて交換することで、効率的に作業が進みます。
これらのポイントを守ることで、真鍮のフライス加工が成功し、良い結果を得られることを覚えておきましょう。
2. 真鍮のフライス加工におけるトラブル回避
2-1. 一般的なトラブルとその対策
真鍮のフライス加工を行う際には、いくつかの注意点があります。まず、加工がうまくいかないと、製品に傷や形の歪みができてしまいます。これは、正しい工具を使わなかったり、加工条件を間違えたりすることが原因です。例えば、回転速度や送り速度を適切に設定しないと、真鍮がうまく切れず、仕上がりが悪くなります。
次に、冷却剤を使うことが大切です。加工中に真鍮が熱を持つと、変形することがあります。冷却剤を使うことで、温度をコントロールし、良い仕上がりが得られます。
これらのポイントを守ることで、真鍮のフライス加工が成功しやすくなります。正しい方法を知って、安心して作業を進めましょう。
2-2. 加工中の注意点
真鍮のフライス加工を行う際には、いくつかの注意点があります。まず、加工中に部品が動かないようにしっかり固定することが大切です。これをしないと、部品がずれてしまい、正しい形に加工できなくなります。次に、適切な切削速度を選ぶことも重要です。速すぎると工具が壊れたり、真鍮が熱で変形したりすることがあります。例えば、特に細かい部分を加工する場合は、ゆっくりとした速度で行うと良いでしょう。
加工後には仕上げ作業を忘れずに行うことが大切です。これにより、表面が滑らかになり、見た目も良くなります。これらのポイントを守ることで、真鍮のフライス加工が成功しやすくなります。
2-3. 仕上げ加工の重要性
真鍮のフライス加工は、金属をきれいに削る作業ですが、注意が必要です。まず、加工を成功させるためには、正しい工具を使うことが大切です。例えば、真鍮専用の刃物を使うと、スムーズに削れます。次に、加工中の温度管理も重要です。真鍮は熱に弱いため、冷却液を使って温度を下げると良いでしょう。加工する時の速度も考えなければなりません。速すぎると、金属が傷んでしまいます。このように、真鍮のフライス加工では、工具、温度、速度の3つに気を付けることで、失敗を防げます。しっかりとした準備をして、安心して加工を進めましょう。
3. 真鍮の特性に基づいた加工方法
3-1. 真鍮の物理的特性
真鍮のフライス加工を行うときは、いくつかの注意点があります。まず、真鍮は柔らかい金属なので、加工中に傷がつきやすいです。そのため、適切な工具を使うことが大切です。例えば、刃先が鋭いフライスカッターを使うと、きれいに加工できます。
次に、真鍮は熱を持ちやすいので、加工中に温度が上がると変形することがあります。このため、冷却液を使って温度を下げることが必要です。さらに、加工後は表面が酸化しやすいので、すぐに手入れをすることが大切です。
以上のポイントを守ることで、真鍮のフライス加工が成功しやすくなります。しっかりと準備をして、良い結果を目指しましょう。
3-2. 加工方法の選択基準
真鍮のフライス加工を行うときには、いくつかの注意点があります。まず、加工の目的を明確にすることが大切です。なぜなら、目的によって必要な工具や加工方法が変わるからです。例えば、細かい部品を作りたい場合は、精密なフライス盤を使う必要があります。このように、目的に合った道具を選ぶことで、加工の精度が向上します。
次に、真鍮の特性を理解することも重要です。真鍮は柔らかく、加工しやすいですが、熱を加えると変形しやすくなります。したがって、加工中は冷却液を使って温度を管理することが必要です。これにより、品質の良い部品を作ることができます。
真鍮のフライス加工を成功させるためには、目的を明確にし、材料の特性を理解することが重要です。これらを守ることで、失敗を防ぎ、良い結果を得ることができるでしょう。
3-3. 加工精度を高めるための工夫
真鍮のフライス加工を行う際には、いくつかの注意点があります。まず、加工精度を高めるためには、工具の選び方が非常に重要です。例えば、切削工具が適切でないと、仕上がりが悪くなることがあります。また、加工する真鍮の種類によっても、必要な設定が変わります。具体的には、柔らかい真鍮の場合、切削速度を速めると良い結果が得られます。
次に、冷却剤の使用も大切です。冷却剤を使うことで、工具の摩耗を減らし、加工中の熱を抑えることができます。これにより、より高い精度で加工することが可能になります。
以上の理由から、真鍮のフライス加工では、工具の選定や冷却剤の使用が重要です。これらをしっかりと考慮することで、失敗を防ぎ、良い結果を得ることができます。
4. フライス加工における真鍮の加工事例
4-1. 成功事例の紹介
真鍮のフライス加工は、金属を切り出して形を作る方法ですが、失敗しないためにはいくつかのポイントがあります。まず、加工する際の工具の選び方が重要です。適切な工具を使うことで、きれいな仕上がりが得られます。例えば、真鍮専用の刃物を使うと、加工がスムーズになります。
次に、加工速度や送り速度も注意が必要です。速すぎると、金属が熱を持ち、変形してしまうことがあります。適切な速度を守ることで、精度の高い加工が実現できます。
加工後の仕上げも大切です。表面を磨くことで、見た目が美しくなり、製品の価値が上がります。これらのポイントを守ることで、真鍮のフライス加工は成功しやすくなります。
4-2. 失敗事例から学ぶ教訓
真鍮のフライス加工を行う際には、いくつかのポイントに注意が必要です。まず、加工の失敗を避けるためには、しっかりとした準備が大切です。例えば、工具の選び方や切削条件を正しく設定することが重要です。もし工具が適切でなかったり、切削速度が速すぎたりすると、材料が傷んでしまうことがあります。
具体的には、真鍮の硬さに合った工具を使うことや、冷却液を適切に使用することで、加工の精度を高めることができます。これにより、部品が正確に仕上がり、無駄な材料を減らすことができます。
真鍮のフライス加工では、事前の準備と適切な道具の使用が成功の鍵です。これを守ることで、失敗を減らし、より良い結果を得ることができるでしょう。
4-3. 実際の加工プロセスの解説
真鍮のフライス加工は、金属を切り出して形を作る方法です。この加工を成功させるためには、いくつかの注意点があります。まず、工具の選び方が大切です。真鍮は柔らかい金属なので、適切な刃物を使わないと、切り口がきれいになりません。例えば、刃物が鈍っていると、加工中に金属が溶けてしまうこともあります。
さらに、加工速度も重要です。速すぎると、金属が熱を持ちすぎて変形することがあります。逆に遅すぎると、効率が悪くなります。具体的には、適切な速度を保つことで、スムーズに加工が進みます。
これらのポイントを守ることで、真鍮のフライス加工が成功し、きれいな製品を作ることができます。正しい方法を知って、ぜひ挑戦してみてください。
5. 真鍮の切削加工におけるプロの技術
5-1. プロが使う切削技術
真鍮のフライス加工はとても便利ですが、失敗しないためにはいくつかのポイントを知っておく必要があります。まず、真鍮は柔らかい金属なので、切削工具の選び方が重要です。適切な工具を使うと、きれいに加工できます。例えば、刃先が鋭い工具を使うと、スムーズに削ることができます。
次に、加工速度や切削油の使い方にも注意が必要です。速すぎると、金属が熱を持ち、変形することがあります。また、切削油を使うことで、工具の摩耗を減らし、加工精度を高めることができます。
これらのポイントを守ることで、真鍮のフライス加工は成功しやすくなります。失敗を避けるために、ぜひこれらの注意点を参考にしてみてください。
5-2. 加工効率を上げるためのノウハウ
真鍮のフライス加工は、金属を加工する方法の一つで、注意が必要です。まず、加工の目的を明確にすることが大切です。なぜなら、目的がはっきりしていないと、仕上がりが期待外れになることがあるからです。例えば、部品を精密に作る場合、適切な工具や設定を選ばなければなりません。また、真鍮は柔らかい金属なので、切削速度や送り速度を間違えると、工具がすぐに摩耗してしまいます。加工後の仕上げも重要です。表面がきれいでないと、見た目が悪くなります。これらのポイントを押さえることで、真鍮のフライス加工を成功させることができます。しっかりと準備をして、注意深く作業を進めましょう。
5-3. 最新の加工技術とトレンド
真鍮のフライス加工は、金属を加工する際にとても重要です。この加工を成功させるためには、いくつかのポイントに注意が必要です。まず、適切な工具を選ぶことが大切です。例えば、真鍮専用の刃物を使うと、きれいに加工できます。次に、加工速度や送り速度を調整することも重要です。速すぎると、金属が熱を持ち、変形することがあります。具体的な例として、真鍮の部品を作るとき、刃物の角度を正しく設定することで、仕上がりが良くなります。このように、真鍮のフライス加工では、工具の選び方や加工条件をしっかり考えることが成功のカギです。最終的に、これらのポイントを守ることで、より良い製品を作ることができます。
まとめ
真鍮フライス加工の成功には、適切な工具選び、切削条件の設定、冷却液の使用が重要です。加工速度や送り速度を適切に調整し、切削時の振動を抑えることが失敗を防ぎます。また、試作品を作成し、加工プロセスを見直すことも効果的です。これらを実践することで、品質の高い仕上がりが期待できます。
砲金フライス加工の挑戦:難易度と効果的な対策について
砲金フライス加工に挑む際、多くの方が直面するのはその難易度です。「この加工は本当に上手くできるのだろうか?」と不安に思っている方も少なくないでしょう。しかし、適切な知識と対策を講じれば、難しいとされる砲金フライス加工も克服できるのです。
本記事では、砲金フライス加工の基本的な概念、加工時の具体的な難しさ、そしてそれに対する効果的な対策を詳しく解説します。「どうすればスムーズに加工できるのか?」と悩んでいる方や、「失敗を避けたい」と思っている方にとって、役立つ情報が満載です。
砲金はその特性上、加工が難しい材料とされていますが、正しい工程と技術を理解することで、質の高い仕上がりを実現することが可能です。これからのセクションでは、砲金フライス加工を成功に導くためのポイントを一緒に探っていきましょう。
1. 砲金フライス加工の難易度と対策
1-1. 砲金の特性とフライス加工における注意点
砲金フライス加工は、金属を削って形を作る技術ですが、難しさがあります。まず、砲金は硬くて加工が難しいため、特別な道具や技術が必要です。例えば、普通の金属よりも工具が早く磨り減ってしまうことがあります。このため、作業をする時は慎重に行う必要があります。
また、砲金は熱を持ちやすいので、加工中に温度管理が重要です。温度が高くなると、金属が変形したり、品質が悪くなったりすることがあります。具体的には、冷却液を使ったり、加工速度を調整したりする方法があります。
砲金フライス加工は難しいですが、正しい対策を取れば、良い結果が得られます。これにより、より高品質な製品を作ることができるのです。
1-2. 砲金フライス加工の難易度を理解する
砲金フライス加工は、金属を削って形を作る技術ですが、難しさがあります。まず、砲金は柔らかく加工しやすいですが、その分、削りすぎると形が崩れやすいのです。例えば、細かい部品を作るときには、少しのミスで使えなくなってしまうことがあります。これが難しさの理由です。
しかし、難しいからこそ、対策を講じることが重要です。例えば、加工する前にしっかりと設計を行い、適切な工具を使うことで、精度を上げることができます。また、経験を積むことで、より良い結果を得ることができるのです。
砲金フライス加工は難しいですが、しっかりとした準備と経験があれば、成功する可能性が高まります。
1-3. 砲金フライス加工の対策と推奨技術
砲金フライス加工は、金属を削って形を作る技術ですが、難しさがあります。まず、砲金は硬くて加工しにくい材料です。そのため、特別な道具や技術が必要です。例えば、切削速度や工具の種類を工夫することで、加工がスムーズになります。また、冷却液を使うことで、工具の寿命を延ばすことも大切です。これらの対策を行うことで、加工の精度が向上し、良い結果を得ることができます。砲金フライス加工は難しいですが、適切な技術や対策を使うことで、成功する可能性が高まります。このように、挑戦を乗り越えるためには、知識と工夫が重要です。
2. 真鍮の穴あけを正確に行うための方法
2-1. 真鍮の特性と穴あけの注意点
砲金フライス加工は、とても難しい作業ですが、適切な対策を取ることで成功することができます。まず、難しさの理由は、砲金が硬くて加工しにくいからです。しかし、正しい工具を使うことで、よりスムーズに加工が進みます。例えば、専用の刃物を使うと、切れ味が良くなり、加工時間が短縮されます。また、加工中の温度管理も重要です。温度が高くなると、材料が変形しやすくなるため、冷却液を使うと良いでしょう。加工の前に十分な準備をすることが大切です。これにより、失敗を減らし、効率的に作業を進めることができます。砲金フライス加工は難しいですが、工夫をすれば成功できるのです。
2-2. 穴あけのための具体的なテクニック
砲金フライス加工は、金属を削って形を作る技術ですが、難しさもあります。まず、砲金は硬い金属なので、加工するのが難しいです。例えば、精密な部品を作るためには、特別な道具や技術が必要です。このような理由から、加工の難易度が高くなります。しかし、効果的な対策を講じることで、この難しさを克服することができます。具体的には、最新の機械を使ったり、熟練した技術者による指導を受けたりすることが重要です。また、加工の前にしっかりと計画を立てることで、失敗を減らすことができます。砲金フライス加工は難しいですが、適切な対策を取ることで成功することが可能です。
2-3. 精度を高めるための工具選び
砲金フライス加工は、金属を削って形を作る技術ですが、難しさがあります。まず、難しい理由は、砲金という材料が硬くて加工しにくいからです。このため、特別な工具や技術が必要です。例えば、精密な工具を使わないと、思った通りの形にならないことがあります。
しかし、適切な対策を取ることで、成功することができます。例えば、高品質の切削工具を選ぶことや、加工条件をしっかりと設定することが大切です。また、経験豊富な技術者に相談することも効果的です。
砲金フライス加工は難しいですが、正しい道具と方法を使うことで、良い結果を得ることができます。これにより、より高い精度で製品を作ることが可能になります。
3. フライス加工の基本的な知識と技術
3-1. フライス加工の基本概念
フライス加工は、金属を削って形を作る方法です。この技術は、特に砲金のような特別な金属を加工するのが難しいとされています。その理由は、砲金が硬く、工具がすぐに摩耗してしまうからです。たとえば、精密な部品を作るためには、特別な工具や技術が必要です。しかし、適切な対策を取ることで、この難しさを克服することができます。例えば、冷却液を使うことで工具の温度を下げ、摩耗を減らすことができます。また、加工の速度を調整することも重要です。これらの対策を講じることで、より良い仕上がりの部品を作ることができ、効率的に作業を進めることができます。フライス加工は難しいですが、工夫次第で成功することが可能です。
3-2. フライス加工に必要な機器と工具
フライス加工は金属を削る作業で、特に砲金という材料は扱いが難しいです。しかし、適切な対策を講じることで、その難しさを克服できます。まず、フライス加工の難しさの理由は、砲金が硬くて加工しにくいからです。このため、専用の工具や機器を使う必要があります。例えば、高速回転するフライス盤や、特別な刃物を使うことで、よりスムーズに加工できます。また、加工中の温度管理も重要です。温度が上がると材料が変形することがあるからです。これらの対策をしっかり行うことで、砲金フライス加工の成功率が高まります。正しい道具と方法を使うことで、難しい砲金の加工も可能になります。
3-3. フライス加工のプロセスを視覚的に理解する
フライス加工は、金属やプラスチックを切り削る技術です。この技術は難しい部分がありますが、正しい対策を取ることで成功することができます。まず、フライス加工の難しさは、材料の硬さや形状によるものです。例えば、砲金という特殊な金属は、加工が難しいですが、耐久性が高いです。そこで、適切な工具や加工条件を選ぶことが重要です。具体的には、刃物の種類や回転速度を調整することで、加工の精度を上げることができます。これにより、品質の高い製品を作ることができるのです。フライス加工の難しさを克服するためには、適切な対策を講じることが大切であり、これが成功の鍵となります。
4. 銅加工の方法とポイント
4-1. 銅の特性と加工の難しさ
銅はとても特別な金属で、電気をよく通し、柔らかくて加工しやすいです。しかし、銅を加工するのは簡単ではありません。まず、銅は熱を持ちやすく、加工中に変形しやすいのです。これが難しさの一つです。たとえば、銅の部品を作るとき、温度管理が重要です。温度が高すぎると、形が崩れてしまいます。
また、銅は酸化しやすく、加工後に表面が黒くなってしまうこともあります。これを防ぐために、特別なコーティングを施すことが必要です。このように、銅の加工にはいくつかの難しさがありますが、適切な対策を講じることで、良い結果を得ることができます。銅の特性を理解し、効果的な加工方法を使うことで、私たちは高品質な製品を作ることができるのです。
4-2. 銅加工における効果的なアプローチ
砲金フライス加工は、金属を削って形を作る技術ですが、難しさもあります。まず、砲金は硬い材料で、加工が難しいためです。例えば、細かい部品を作るとき、正確に削らないと、部品がうまくはまらなくなってしまいます。このような問題を解決するためには、専用の道具を使ったり、加工の温度を調整したりすることが大切です。これにより、より良い品質の部品を作ることができます。砲金フライス加工は難しいけれど、適切な対策を取ることで、成功する可能性が高まります。技術を磨くことが、より良い製品を作るための鍵です。
4-3. 銅加工のための推奨技術
砲金フライス加工は、金属を切削する技術の一つで、特に難易度が高いとされています。その理由は、砲金という素材が硬く、加工するのが難しいからです。しかし、適切な対策を講じることで、加工を成功させることができます。例えば、専用の工具を使ったり、加工速度を調整することで、砲金の特性に合わせた加工が可能になります。
具体的には、工具の材質を選ぶことや、冷却液を使うことで、熱を抑えながら加工することが重要です。これにより、工具の寿命を延ばし、仕上がりも良くなります。
砲金フライス加工は難しいですが、正しい技術と対策を使うことで、うまく加工することができるのです。
5. フライス溝加工の精度を向上させるコツ
5-1. フライス溝加工の基本と重要性
フライス溝加工は、金属や他の材料に溝を作る大切な技術です。この加工は、機械部品の製造や設計に欠かせないものです。なぜなら、フライス溝があることで、部品がしっかりと組み合わさり、機械が正しく動くからです。例えば、自転車のギアや車のエンジン部品には、必ずこの加工が施されています。
しかし、フライス溝加工は簡単ではありません。材料の種類や厚さによって、加工の難しさが変わります。特に、硬い金属を加工する際は、特別な道具や技術が必要です。これに対処するためには、経験豊富な技術者が必要です。
フライス溝加工は重要でありながら、難しい技術です。適切な対策を講じることで、より良い製品を作ることができます。
5-2. 精度向上のための具体的な技術
砲金フライス加工は、金属を切り削って形を作る技術ですが、難しさがあります。まず、砲金は硬くて加工が難しいため、特別な道具や技術が必要です。例えば、精密な部品を作るためには、正確な角度や深さで削ることが求められます。このような難しさに対処するためには、経験豊富な技術者が必要ですし、最新の機械を使うことも重要です。
また、加工中に金属が熱を持つと、形が変わってしまうこともあります。これを防ぐために、冷却剤を使ったり、加工速度を調整したりする方法があります。こうした対策を講じることで、より高品質な製品を作ることができます。
砲金フライス加工は難しいですが、適切な技術や対策を使えば、成功することが可能です。
5-3. フライス溝加工における注意点と対策
フライス溝加工は、金属やその他の材料を正確に削る技術ですが、いくつかの難しさがあります。まず、加工の難易度が高いことが理由です。たとえば、材料の硬さや形状によって、道具がすぐに摩耗してしまうことがあります。また、精度を保つためには、高度な技術と経験が必要です。具体的には、金属の種類ごとに適切な切削条件を選ぶことが大切です。これにより、加工精度が向上し、無駄な材料を削減できます。さらに、適切な工具を使うことで、作業時間を短縮し、効率的に加工を進めることが可能です。これらの対策を講じることで、フライス溝加工の難しさを克服し、より良い結果を得ることができるでしょう。
まとめ
砲金フライス加工は、高精度な部品製作において挑戦的なプロセスです。主な難易度は、材料の特性や工具の摩耗にあります。効果的な対策としては、適切な切削条件の設定や工具の選定、冷却剤の使用が挙げられます。これにより、加工精度を向上させ、効率的な生産が可能になります。
砲金のフライス加工で直面する課題とその対策
砲金のフライス加工に興味はあるけれど、「どのような課題があるのかが分からない…」と悩んでいる方はいませんか?フライス加工は、金属加工の中でも特に精度が求められるプロセスです。特に砲金のような特性を持つ材料は、その特性ゆえに様々な難易度の高い課題に直面しがちです。
この記事では、砲金フライス加工の具体的な難易度と、それに対する有効な対策を詳しく解説します。もしあなたが、
- 砲金のフライス加工を始めたいが、どのような問題が出てくるのか心配だ。
- フライス加工に必要な技術やノウハウを知りたい。
- 効率的な加工方法や、トラブルシューティングのポイントを学びたい。
と考えているのであれば、このガイドはまさにあなたのためのものです。砲金の特性を理解し、加工の現場で直面する課題を乗り越えるための知識を身につけ、よりスムーズに作業を進める助けとなるでしょう。それでは、一緒に砲金フライス加工の世界を探っていきましょう!
1. 砲金フライス加工の難易度と対策
1-1. 砲金の特性とフライス加工における注意点
砲金のフライス加工は、金属を削って形を作る作業ですが、いくつかの課題があります。まず、砲金は硬くて加工が難しいため、特別な工具が必要です。例えば、普通の金属では使える刃物が、砲金にはすぐに摩耗してしまうことがあります。これが理由で、加工時間が長くなり、コストが上がることがあります。
さらに、砲金は熱を持ちやすいので、加工中に温度管理が大切です。温度が高くなると、金属が変形することがあります。これを防ぐためには、冷却液を使ったり、加工速度を調整することが効果的です。
このように、砲金のフライス加工には工夫が必要ですが、適切な対策を講じることで、効率的に作業を進めることができます。
1-2. 砲金フライス加工の難易度を理解する
砲金のフライス加工は、金属を削って形を作る技術ですが、いくつかの難しさがあります。まず、砲金は硬い素材なので、加工するのが大変です。例えば、金属を削るためには特別な道具や機械が必要です。これらの道具がないと、うまく加工できません。また、加工中に金属が熱を持つことがあり、これが精度に影響を与えることもあります。
しかし、これらの課題には対策があります。例えば、適切な道具を使うことや、加工の温度を管理することで、より良い結果が得られます。また、経験を積むことで、加工技術も向上します。
砲金のフライス加工は難しいですが、正しい方法を使えば、成功することができるのです。
1-3. 砲金フライス加工における一般的な問題とその対策
砲金のフライス加工は、金属を切削して形を作る作業ですが、いくつかの課題があります。まず、砲金は硬くて加工が難しいため、工具がすぐに摩耗してしまいます。これにより、加工精度が低下し、製品の品質に影響が出ることがあります。次に、加工中に発生する熱が問題です。熱がこもると、部品が変形することがあります。
これらの問題を解決するためには、適切な工具を選ぶことや、冷却剤を使って熱を抑えることが大切です。例えば、特別なコーティングが施された工具を使うことで、摩耗を減らすことができます。また、冷却剤を使うことで、加工中の温度を下げることができ、部品の変形を防げます。
このように、砲金のフライス加工には工夫が必要ですが、適切な対策を講じれば、高品質な製品を作ることができます。
2. 真鍮の穴あけ方法と技術
2-1. 真鍮の特性と穴あけの注意点
真鍮のフライス加工は、金属を削って形を作る大切な作業ですが、いくつかの課題があります。まず、真鍮は柔らかい金属なので、加工中に傷がつきやすいです。このため、特別な工具を使ったり、加工の速度を調整したりする必要があります。具体的には、刃物の角度を変えたり、冷却液を使って温度を下げたりします。これにより、加工がスムーズになり、品質も向上します。
真鍮のフライス加工には注意が必要ですが、適切な対策を講じることで、良い結果を得ることができます。加工の難しさを理解し、工夫をすることで、より良い製品を作ることができるのです。
2-2. 正確な穴あけのための具体的な技術
砲金のフライス加工は、金属を削って形を作る大切な技術ですが、いくつかの課題があります。まず、砲金は硬くて加工が難しいため、工具がすぐに摩耗してしまいます。これにより、加工精度が落ちたり、時間がかかったりします。例えば、精密な部品を作るためには、特別な工具や加工方法が必要です。
この問題に対処するためには、最新の工具を使ったり、加工条件を見直すことが重要です。例えば、冷却液を使って工具の温度を下げることで、摩耗を減らすことができます。
砲金のフライス加工には課題がありますが、適切な対策を講じることで、高品質な部品を効率よく作ることが可能です。
2-3. 真鍮の穴あけにおけるコツとトラブルシューティング
真鍮の穴あけは、特に難しい作業の一つです。まず、真鍮は柔らかい金属ですが、適切な道具や方法を使わないと、穴を開けるのが大変になります。例えば、ドリルの刃が鈍いと、金属が溶けてしまったり、穴が正確に開かないことがあります。このような問題を避けるためには、刃を定期的に研ぎ、適切な回転数で作業することが大切です。
また、穴を開ける際には、真鍮をしっかり固定することも重要です。固定が不十分だと、金属が動いてしまい、正しい位置に穴を開けることができません。これらのポイントに注意することで、真鍮の穴あけがスムーズに進むでしょう。正しい方法を知ることで、作業が楽になり、良い結果が得られます。
3. 真鍮(黄銅)の加工方法と効果的なポイント
3-1. 真鍮の加工特性とその影響
真鍮のフライス加工にはいくつかの課題がありますが、これらを理解し対策を講じることで、より良い結果を得ることができます。まず、真鍮は柔らかく加工しやすい材料ですが、熱がこもりやすく、加工中に変形することがあります。これが理由で、精度が求められる部品を作るのが難しくなります。例えば、精密機器の部品を作る際には、特に注意が必要です。
そのため、冷却液を使って熱を逃がしたり、適切な切削条件を設定することが大切です。また、工具の選び方も重要で、真鍮専用の工具を使うことで、加工精度を向上させることができます。これらの対策を講じることで、真鍮のフライス加工を成功させることができるのです。最終的には、これらの工夫が高品質な製品を生み出すことにつながります。
3-2. 効果的な加工方法と注意点
砲金のフライス加工は、金属を削って形を作る技術ですが、いくつかの課題があります。まず、砲金は硬くて加工が難しいため、特別な道具や技術が必要です。例えば、通常の金属加工では使える道具が使えないことがあります。これに対処するためには、専門の機械や経験豊富な技術者が必要です。
また、加工中に熱が発生しやすく、これが材料に悪影響を及ぼすこともあります。これを防ぐためには、冷却液を使ったり、加工速度を調整することが重要です。
砲金のフライス加工は難しいですが、適切な道具と技術を使うことで、成功する可能性が高まります。これにより、より良い製品を作ることができるのです。
3-3. 真鍮加工における成功のためのポイント
砲金のフライス加工は、金属を削って形を作る技術ですが、いくつかの課題があります。まず、砲金は硬い材料であるため、加工が難しいです。このため、特別な工具や技術が必要になります。例えば、刃物がすぐに摩耗してしまうことがあり、これが加工の効率を下げる原因となります。
次に、加工中に発生する熱が問題です。熱がこもると、材料が変形したり、精度が落ちたりします。このような課題に対しては、冷却剤を使ったり、加工速度を調整することで対策が可能です。
砲金のフライス加工は難しいですが、適切な対策を講じることで成功することができます。技術の進歩と工夫が、より良い加工を実現する鍵となります。
4. 切削加工の基礎と実践的なポイント
4-1. 切削加工の基本概念
砲金のフライス加工は、金属を削る技術ですが、いくつかの課題があります。まず、砲金は柔らかい金属で、加工中に変形しやすいです。これにより、正確な形を作るのが難しくなります。次に、砲金には特有の摩耗があり、工具がすぐに傷んでしまうことも問題です。例えば、砲金を使った部品は、機械の中で動く部分に多く使われますが、摩耗が早いと故障の原因になります。
これらの課題に対する対策としては、適切な加工条件を設定することや、耐摩耗性の高い工具を使用することが挙げられます。これにより、加工の精度を向上させ、部品の寿命を延ばすことができます。つまり、砲金のフライス加工には工夫が必要ですが、正しい方法を使えば良い結果が得られます。
4-2. 切削加工を始めるためのステップ
砲金のフライス加工は、金属を削り取って形を作る技術ですが、いくつかの課題があります。まず、砲金は硬くて加工が難しいため、特別な工具が必要です。例えば、通常の工具では刃がすぐに摩耗してしまいます。このため、適切な工具を選ぶことが重要です。また、加工中に熱が発生しやすく、これが材料の変形を引き起こすこともあります。これを防ぐために、冷却液を使うことが効果的です。砲金のフライス加工は難しいですが、適切な工具と冷却方法を使うことで、より良い結果を得ることができます。これにより、精度の高い部品を作ることができ、様々な産業で役立つのです。
4-3. 実践的な切削加工のポイント
砲金のフライス加工は、金属を削って形を作る作業ですが、いくつかの難しさがあります。まず、砲金は柔らかくて加工しやすい一方、熱を持ちやすく、変形しやすいです。このため、加工中に注意が必要です。例えば、加工速度を適切に調整することが重要です。これにより、熱の発生を抑え、材料の変形を防げます。
さらに、切削工具の選び方も大切です。適切な工具を使うことで、より精密な加工が可能になります。加工後の仕上げ作業も忘れずに行いましょう。これにより、製品の品質が向上します。
砲金のフライス加工には工夫が必要ですが、適切な対策を講じることで、良い結果を得ることができます。
5. 切削加工における表面粗さの問題と対策
5-1. 表面粗さの原因を理解する
砲金のフライス加工は、金属を削って形を作る大切な技術ですが、いくつかの難しさがあります。まず、砲金は硬くて加工しにくい素材です。このため、加工中に工具がすぐに摩耗してしまい、作業が遅くなります。例えば、精密な部品を作るとき、工具がすぐに壊れると、時間とお金が無駄になってしまいます。
そこで、対策としては、特別な工具を使ったり、加工の速度を調整することが考えられます。また、冷却液を使うことで工具の温度を下げ、摩耗を防ぐことも有効です。これらの方法を使うことで、フライス加工の効率を上げることができます。
砲金のフライス加工には挑戦があるものの、適切な対策を講じることで、より良い結果を得ることが可能です。
5-2. 表面粗さを改善するための対策
砲金のフライス加工は、金属を削って形を作る技術ですが、いくつかの課題があります。まず、砲金は硬くて加工しにくいため、工具がすぐに摩耗してしまいます。このため、加工の精度が下がることがあります。例えば、精密な部品を作る際には、工具の寿命を延ばすために、適切な切削条件を選ぶことが重要です。
さらに、加工中に発生する熱も問題です。熱がこもると、部品が変形することがあります。これを防ぐためには、冷却液を使って温度を下げることが有効です。
砲金のフライス加工には課題があるものの、適切な対策を講じることで、より良い結果を得ることができます。工具の選び方や冷却方法を工夫することで、加工精度を向上させることができるのです。
5-3. 切削加工における表面粗さの管理方法
切削加工における表面粗さの管理は、とても大切です。まず、表面粗さが良いと、製品の品質が向上し、顧客の満足度も高まります。理由としては、滑らかな表面は摩擦を減らし、部品の寿命を延ばすからです。具体的な例として、精密機器や自動車部品では、表面が粗いと動作不良を引き起こすことがあります。そこで、切削条件を適切に設定したり、工具の選び方を工夫したりすることが対策として有効です。表面粗さを管理することで、製品の信頼性が向上し、企業の競争力も強まります。このように、表面粗さの管理は製品づくりにおいて欠かせない要素です。
まとめ
砲金のフライス加工では、工具摩耗や熱膨張、切削条件の最適化が課題です。対策として、適切な切削速度や冷却液の使用、工具材質の選定が重要です。また、加工後の表面処理を行うことで、耐久性を向上させることも有効です。
黄銅フライス加工の切削条件を最適化するためのガイド
黄銅のフライス加工において、適切な切削条件を選定することは、品質の高い製品を生み出すために不可欠です。しかし、さまざまな要因が影響を及ぼすため、「どのように切削条件を最適化すれば良いのか?」と悩む方も多いのではないでしょうか?本ガイドでは、黄銅のフライス加工における切削条件の基礎から応用までを詳しく解説します。
このガイドは以下のような方々に向けています:
- 黄銅のフライス加工に興味があるが、どこから始めれば良いのかわからない方
- フライス加工の品質向上を目指している製造業の技術者
- 切削条件に関する最新の知識を身につけたいと考えている方
黄銅を効率よく加工するためには、切削速度、送り量、刃物の形状など、さまざまな要素を最適化する必要があります。本ガイドでは、これらの要素について詳しく掘り下げ、あなたのフライス加工を一段階引き上げるためのヒントを提供します。さあ、一緒に黄銅フライス加工の世界を探求していきましょう!
1. 黄銅のフライス加工における切削条件の重要性
1-1. フライス加工とは
フライス加工は、金属や木材を切り取って形を作る方法です。この技術は、特に精密な部品を作るのに役立ちます。フライス加工を行うためには、適切な切削条件を設定することがとても大切です。なぜなら、切削条件が悪いと、材料がうまく切れなかったり、工具がすぐに壊れてしまったりするからです。
例えば、黄銅という金属を加工する場合、切削速度や送り速度を正しく設定することで、スムーズに加工が進みます。良い切削条件を見つけることができれば、加工時間が短くなり、仕上がりも良くなります。最終的に、効率よく高品質な製品を作ることができるのです。したがって、フライス加工を成功させるためには、切削条件の最適化が不可欠です。
1-2. 黄銅の特性と加工の利点
黄銅は、金属の中でも特に加工しやすい材料です。まず、黄銅は柔らかく、切削しやすいので、さまざまな形に加工することができます。これにより、工業や家庭用品など多くの製品に利用されています。例えば、黄銅製の楽器や配管部品は、耐久性があり、長持ちします。
また、黄銅は耐腐食性が高く、湿気や酸に強いです。これにより、外で使う道具や装飾品にも適しています。さらに、黄銅は見た目が美しく、金色の光沢があるため、インテリアとしても人気があります。
このように、黄銅の特性と加工の利点から、多くの分野で重宝されています。これからも黄銅を使った製品は増えていくでしょう。
2. フライス加工における最適な切削速度や送りの設定方法
2-1. 切削速度の決定要因
黄銅のフライス加工を行う際、切削条件を最適化することがとても大切です。まず、適切な切削条件を選ぶことで、加工の効率が上がり、品質も良くなります。理由は、切削速度や送り速度、切削深さなどの条件が、加工の結果に大きく影響するからです。例えば、切削速度が速すぎると、工具がすぐに摩耗してしまい、逆に遅すぎると加工時間が長くなります。また、黄銅は柔らかい金属なので、適切な条件を見つけることで、スムーズに加工できます。切削条件をしっかりと調整することで、効率よく、高品質な製品を作ることができるのです。これが、切削条件を最適化する重要性です。
2-2. 送り速度の設定方法
送り速度の設定は、黄銅のフライス加工を成功させるためにとても重要です。まず、送り速度を適切に設定することで、加工の効率が上がります。例えば、早すぎる送り速度では工具がすぐに摩耗してしまい、遅すぎると作業が無駄に時間がかかります。具体的には、工具の種類や工作機械の性能に応じて、送り速度を調整することが求められます。例えば、硬い黄銅を加工する場合は、少し遅めの送り速度が良い結果を生むことがあります。このように、正しい送り速度を設定することで、加工品質が向上し、作業効率も良くなります。送り速度の設定は黄銅フライス加工の成功に欠かせない要素です。
2-3. 切削条件の実例
黄銅のフライス加工における切削条件を最適化することは、とても重要です。まず、最適な切削条件を設定する理由は、加工の効率を上げ、製品の品質を向上させるためです。例えば、切削速度や送り速度を調整することで、作業時間を短縮し、材料の無駄を減らすことができます。具体的な例として、切削速度を適切に設定することで、工具の摩耗を減らし、長持ちさせることができます。これにより、コストを抑えつつ、高品質な製品を生み出すことが可能になります。黄銅のフライス加工では、切削条件をしっかりと見直し、最適化することが成功の鍵となります。これにより、効率的で経済的な加工が実現できるのです。
3. 快削黄銅の加工における材質別ガイドライン
3-1. 快削黄銅の特性
快削黄銅は、金属加工において非常に重要な材料です。まず、快削黄銅は加工がしやすく、切削工具の摩耗が少ないため、効率的に作業ができます。この理由から、多くの工場で使用されています。具体例として、快削黄銅は自動車の部品や電子機器の部品など、さまざまな製品に使われています。これにより、製品の品質が向上し、コストを抑えることができます。快削黄銅はその特性から、金属加工において非常に有用であり、今後も多くの分野で活躍することでしょう。
3-2. 材質別の切削条件
黄銅のフライス加工における切削条件を最適化することは、とても重要です。まず、最適な切削条件を設定することで、加工の効率が上がり、時間を節約できます。例えば、黄銅を加工する際には、刃物の回転速度や進行速度を適切に調整する必要があります。これにより、材料の無駄を減らし、仕上がりがきれいになります。
また、切削油を使うことで、刃物の摩耗を防ぎ、長持ちさせることができます。具体的には、黄銅の加工では水溶性の切削油が効果的です。このように、切削条件を工夫することで、より良い結果が得られます。
黄銅のフライス加工では、切削条件を最適化することが成功の鍵です。これにより、効率的で高品質な加工が実現できます。
3-3. 加工時の注意点
黄銅のフライス加工を行う際には、いくつかの注意点があります。まず、適切な切削条件を選ぶことが重要です。なぜなら、切削条件が合っていないと、加工がうまくいかず、部品が壊れたり、仕上がりが悪くなったりするからです。例えば、切削速度や送り速度が適切でないと、黄銅が熱を持ち、変形することがあります。
具体的には、切削速度を速くしすぎると、工具が早く摩耗してしまいます。一方で、遅すぎると加工時間が長くなり、効率が悪くなります。適切な条件を見つけるためには、実際に加工を行いながら調整することが必要です。
黄銅のフライス加工では、正しい切削条件を見つけることが成功のカギです。これにより、高品質な部品を効率よく作ることができます。
4. 真鍮の切削加工に関する基本的な知識
4-1. 真鍮の種類と特性
真鍮は、銅と亜鉛を主成分とする金属で、特にその美しい金色が特徴です。真鍮の種類には、黄銅(銅が多い)や白銅(亜鉛が多い)などがあります。真鍮は加工がしやすく、さまざまな形に成形できるため、工業や装飾品に広く利用されています。また、耐腐食性も高いため、長持ちする特性があります。
具体的な例として、真鍮は楽器や金具、さらにはアクセサリーにも使われています。楽器では、音質を良くするために真鍮が選ばれることが多いです。このように、真鍮は多くの場面で役立つ素材です。
真鍮はその特性から、さまざまな用途に適した重要な金属であり、私たちの生活に欠かせない存在です。
4-2. 切削加工の基本技術
黄銅のフライス加工における切削条件を最適化することは、とても大切です。まず、最適な切削条件を設定することで、加工の効率が上がります。例えば、適切な切削速度や送り速度を選ぶことで、黄銅がスムーズに加工され、仕上がりが良くなります。また、工具の摩耗を減らすこともでき、長持ちさせることができます。さらに、冷却剤を使うことで、熱を抑え、加工中のトラブルを防ぐことができます。これらの理由から、切削条件をしっかりと考えることが重要です。最終的に、良い切削条件を見つけることで、より良い製品を作ることができ、時間やコストを節約することにつながります。
4-3. 注意すべきポイント
黄銅フライス加工の切削条件を最適化することは、とても大切です。まず、最適化をする理由は、効率よく加工を行い、良い品質の製品を作るためです。例えば、切削速度や送り速度を調整することで、素材の無駄を減らし、加工時間を短縮できます。具体的には、適切な刃物を選び、切削油を使うことで、摩耗を減らし、長持ちさせることができます。このように、切削条件を見直すことで、より良い結果が得られます。黄銅のフライス加工では、切削条件を最適化することが、効率と品質を向上させる鍵となります。
5. 切削条件の設定におけるプロの技術やヒント
5-1. 経験に基づく切削条件の調整
黄銅のフライス加工では、切削条件を最適化することがとても重要です。まず、最適な切削条件を見つけることで、加工の効率が上がり、良い品質の製品が作れます。例えば、切削速度や送り速度を適切に設定すると、工具の摩耗が減り、長持ちします。さらに、冷却剤を使うことで、加工中の熱を抑え、材料の変形を防ぐことができます。これらの工夫により、無駄なコストを減らし、より良い製品を作ることが可能になります。黄銅のフライス加工においては、経験に基づいた切削条件の調整が成功のカギとなります。正しい条件を選ぶことで、効率的かつ高品質な加工が実現できるのです。
5-2. ツール選定の重要性
黄銅のフライス加工における切削条件を最適化することは、とても大切です。なぜなら、正しい条件を選ぶことで、作業がスムーズに進み、良い品質の部品が作れるからです。たとえば、切削速度や送り速度を適切に設定することで、工具の寿命が延び、無駄なコストを減らすことができます。また、冷却液を使うことで、加工中の熱を抑え、材料の変形を防ぐこともできます。このように、最適な切削条件を見つけることは、効率的で経済的な加工を実現する鍵となります。黄銅のフライス加工では、切削条件の最適化が成功のポイントであり、それによって品質やコストを大きく改善できるのです。
5-3. 加工効率を上げるためのテクニック
黄銅のフライス加工において、切削条件を最適化することはとても大切です。まず、最適な切削条件を設定することで、加工効率が上がり、時間を節約できます。例えば、切削速度や送り速度を適切に調整することで、よりスムーズに加工が進みます。さらに、工具の種類や冷却方法を工夫することで、工具の寿命も延び、コストを抑えることができます。
具体的には、黄銅の加工では、適切な切削速度は約100メートル毎分とされています。この条件を守ることで、きれいな仕上がりが得られます。切削条件を見直すことで、加工の質や効率が向上し、より良い製品を作ることができるのです。これらのポイントを意識することが、成功につながります。
6. 正面フライス加工の計算方法や手順
6-1. 正面フライス加工の基本
黄銅のフライス加工において、切削条件を最適化することはとても大切です。まず、最適な切削条件を設定することで、加工の効率が上がり、材料の無駄を減らすことができます。例えば、適切な回転速度や送り速度を選ぶことで、黄銅をスムーズに削ることができ、仕上がりもきれいになります。
具体的には、黄銅のフライス加工では、回転数を高く設定すると切削が速くなりますが、刃物の摩耗も早くなることがあります。一方、送り速度を適切に調整することで、加工時間を短縮できることもあります。
このように、切削条件をしっかりと考えることで、より良い加工結果が得られます。最適化は成功の鍵ですので、ぜひ試してみてください。
6-2. 計算方法のステップ
黄銅のフライス加工における切削条件を最適化することは、とても重要です。まず、最適な切削条件を選ぶ理由は、加工効率を上げて、製品の品質を良くするためです。例えば、切削速度や送り速度、工具の種類を適切に設定することで、加工時間を短縮し、無駄を減らすことができます。
具体的には、黄銅を加工する際には、切削速度を速く設定することで、よりスムーズに加工できることがあります。また、刃物の材質や形状を選ぶことで、切り口がきれいになり、仕上がりが良くなります。このように、条件を工夫することで、効率的に作業が進められます。
黄銅のフライス加工では、切削条件を最適化することが、効率と品質を向上させる鍵となります。
6-3. 実践的な手順
黄銅のフライス加工における切削条件を最適化することは、とても重要です。まず、最適な切削条件を設定することで、加工の効率が上がり、時間を節約できます。例えば、適切な切削速度や送り速度を選ぶことで、加工時間を短縮し、より多くの部品を作ることができます。次に、切削条件を見直すことで、工具の寿命も延びます。例えば、切削油を使用することで、工具が熱くなりすぎず、長持ちします。最適化された切削条件は、製品の品質を向上させることにもつながります。きれいに仕上がった部品は、顧客の満足度を高め、リピート注文を得やすくなります。このように、切削条件を最適化することは、効率、コスト、品質のすべてに良い影響を与えます。
まとめ
黄銅フライス加工の切削条件を最適化するには、切削速度、送り速度、刃物の形状と材質を考慮することが重要です。適切な冷却剤の使用や工具の定期的なメンテナンスも、加工精度と工具寿命を向上させます。これにより、生産性を高め、コストを削減することが可能です。
真鍮をフライス加工するための最適な工具を徹底解説
真鍮のフライス加工に挑戦したいけれど、「どの工具を選べばいいのか分からない」と悩んでいる方はいませんか?そんなあなたのために、今回は「真鍮をフライス加工するための最適な工具」を徹底解説します。
この記事では、真鍮の特徴やフライス加工の基本的な方法に加え、工具選びのポイントを詳しく説明します。「どの工具が自分の作業に最適なのか?」、「加工精度を高めるためにはどうすればいいのか?」といった疑問にお答えし、初心者から経験者まで役立つ情報を提供します。
真鍮はその加工性や耐食性から、さまざまな製品に使用されています。しかし、適切な工具を選ばなければ、思うような結果を得られないこともあります。この記事を通じて、あなたのフライス加工技術を一段と向上させ、より良い作品を生み出す手助けをしましょう。
1. 真鍮のフライス加工に適した工具の選び方
1-1. フライス加工とは何か
フライス加工とは、金属や木材の表面を削って形を作る方法です。この加工は、特に真鍮のような金属でよく使われます。フライス加工が重要な理由は、精密な形を作ることができるからです。例えば、機械の部品や工具など、細かい部分が必要なものに最適です。
真鍮をフライス加工するためには、適切な工具を選ぶことが大切です。具体的には、硬い刃物や高精度のフライス盤が必要です。これにより、真鍮の表面が滑らかに仕上がり、正確な形が作れます。
真鍮のフライス加工には特別な工具が必要です。正しい道具を使うことで、より良い製品を作ることができるのです。
1-2. 真鍮の特性と加工の重要性
真鍮は金属の一種で、銅と亜鉛からできています。この金属は、見た目が美しく、耐腐食性も高いので、さまざまな製品に使われています。真鍮を加工することはとても重要です。なぜなら、正しい形やサイズにすることで、より使いやすく、魅力的な製品を作ることができるからです。例えば、真鍮の部品は楽器や装飾品などに使われ、良い加工が施されることで、その価値が高まります。加工には特別な工具が必要で、これを使うことで精密な作業が可能になります。真鍮の加工はその特性を活かし、素晴らしい製品を生み出すために欠かせない工程です。
1-3. 適切な工具の種類と特徴
真鍮をフライス加工するためには、適切な工具を選ぶことがとても大切です。まず、真鍮は柔らかい金属なので、切削がしやすいですが、工具の選び方を間違えると、加工がうまくいかないことがあります。例えば、刃物の素材としては、超硬合金やHSS(高速度鋼)が適しています。これらの素材は、真鍮をしっかりと切ることができ、長持ちします。
さらに、工具の形状も重要です。フライス加工には、平刃やボールエンドミルなど、さまざまな形状の工具があります。用途によって使い分けることで、より精密な加工が可能になります。
真鍮のフライス加工には、適切な素材と形状の工具を選ぶことが成功の鍵です。正しい工具を使えば、きれいで正確な仕上がりが得られます。
2. フライス加工の基本的な知識
2-1. フライス加工のプロセス
真鍮をフライス加工するための最適な工具についてお話しします。まず、適切な工具を選ぶことが重要です。なぜなら、正しい工具を使うことで、加工がスムーズになり、仕上がりも良くなるからです。
例えば、真鍮には「エンドミル」という工具が適しています。この工具は、金属を削るのに特化していて、細かい部分もきれいに仕上げることができます。また、刃の形状やサイズによって、加工する場所や仕上がりに影響を与えるため、自分の目的に合ったものを選ぶことが大切です。
真鍮のフライス加工には、適切な工具を選ぶことが成功のカギです。正しい工具を使うことで、より良い結果が得られます。
2-2. 切削工具の基本構造
真鍮をフライス加工するためには、適切な切削工具を選ぶことが大切です。まず、理由として真鍮は柔らかい金属であり、加工しやすいですが、工具の選び方を間違えると仕上がりが悪くなります。例えば、硬い工具を使うと真鍮が傷ついたり、切りくずがうまく出なかったりします。
具体的には、真鍮には高速度鋼(HSS)や超硬合金のエンドミルが適しています。HSSはコストが低く、初心者にも扱いやすいですが、超硬合金は耐久性が高く、長時間の作業に向いています。これらの工具を使うことで、スムーズな加工が可能になります。
真鍮をフライス加工する際は、適切な切削工具を選ぶことが成功の鍵です。正しい工具を使えば、より良い仕上がりが得られます。
2-3. 切削速度と送り速度の理解
真鍮をフライス加工するための最適な工具を選ぶことは、とても大切です。まず、良い工具を使うことで、加工がスムーズになり、仕上がりもきれいになります。例えば、真鍮に適した工具は、硬い刃物や特殊なコーティングが施されたものです。これにより、真鍮の柔らかさを活かしながら、正確に形を作ることができます。
また、工具の選び方には、切削速度や送り速度も関係しています。適切な速度で加工することで、工具が長持ちし、作業効率もアップします。たとえば、速すぎると刃が摩耗しやすくなります。
真鍮のフライス加工には、適切な工具の選択と加工速度の理解が重要です。これにより、より良い結果を得ることができるでしょう。
3. 真鍮加工時の切削条件や注意点
3-1. 切削条件の設定方法
真鍮をフライス加工するための最適な工具を選ぶことは、とても大切です。まず、理由として、適切な工具を使うことで、加工がスムーズに進み、仕上がりがきれいになるからです。例えば、真鍮専用のフライスカッターやエンドミルを使うと、金属が削りやすく、精度も高まります。
また、工具の選び方には、刃の形状や素材も重要です。真鍮は柔らかい金属なので、切れ味が良い工具を選ぶと良いでしょう。具体的には、チタンコーティングされた工具が耐久性があり、おすすめです。
正しい工具を使うことで、作業時間の短縮やコスト削減にもつながります。真鍮のフライス加工を行う際は、ぜひ適切な工具を選んで、効率よく作業を進めてください。
3-2. 加工中の注意点
真鍮をフライス加工する際には、適切な工具を選ぶことがとても大切です。まず、理由として真鍮は柔らかい金属で、加工しやすいですが、適切な工具を使わないと仕上がりが悪くなります。具体的には、真鍮専用のフライス刃やコーティングされた工具を使うと、切れ味が良くなり、加工中の摩擦も減ります。
例えば、タングステン carbide(カーバイド)製の刃物は、真鍮の加工に特に効果的です。また、切削油を使うことで、工具の寿命を延ばし、加工の精度も向上します。
真鍮のフライス加工には、適切な工具や方法を選ぶことが重要です。これにより、より良い仕上がりを得ることができ、作業もスムーズになります。
3-3. 切削液の役割と選び方
真鍮をフライス加工するためには、適切な工具を選ぶことがとても重要です。まず、真鍮は柔らかい金属なので、切削がしやすいです。しかし、工具が合っていないと、加工がうまくいかないことがあります。たとえば、刃先が鋭いエンドミルを使うと、きれいに切ることができます。また、切削液を使うことで、工具が長持ちし、加工がスムーズになります。切削液は、金属の熱を下げたり、切りくずを取り除いたりする役割があります。真鍮のフライス加工には、適切な工具と切削液を選ぶことが成功のカギです。これにより、効率的に加工ができ、良い結果が得られるでしょう。
4. フェイスミルの選び方や使用方法
4-1. フェイスミルの種類と特徴
真鍮のフライス加工に適した工具を選ぶことは、とても大切です。まず、適切な工具を選ぶ理由は、加工の精度や効率を高めるためです。例えば、真鍮は柔らかい金属なので、切削がしやすいですが、工具の選び方を間違えると、仕上がりが悪くなったり、工具がすぐに磨耗してしまったりします。
具体的には、真鍮には「フェイスミル」や「エンドミル」と呼ばれる工具が適しています。フェイスミルは平らな面を加工するのに便利で、エンドミルは細かい部分の加工に役立ちます。このように、工具の種類によって得意な加工が異なるため、目的に合ったものを選ぶことが重要です。
真鍮のフライス加工には適切な工具選びが不可欠です。これをしっかり理解することで、より良い加工ができるようになります。
4-2. フェイスミルの選定基準
真鍮をフライス加工するための最適な工具を選ぶことは、とても大切です。まず、良い工具を選ぶ理由は、加工の精度や効率が上がるからです。例えば、真鍮は柔らかい金属ですが、正しい工具を使わないと、部品が傷ついたり、加工がうまくいかなかったりします。そこで、フェイスミルやエンドミルなどの専用工具を使うと、スムーズに作業が進みます。さらに、工具の材質や刃の形状も重要です。高品質な工具を選ぶことで、長持ちし、コストパフォーマンスも良くなります。真鍮のフライス加工には、適切な工具を選ぶことが成功の鍵です。これにより、より良い結果を得ることができ、作業が楽しくなります。
4-3. フェイスミルの効果的な使用方法
真鍮のフライス加工には、適切な工具を選ぶことがとても重要です。まず、真鍮は柔らかい金属で、加工しやすいですが、工具が合わないと仕上がりが悪くなります。例えば、フェイスミルという工具は、平らな面を削るのにとても効果的です。これを使うことで、真鍮の表面を滑らかに仕上げることができます。また、切削油を使うと、工具の寿命を延ばし、加工中の熱を抑えることができます。これにより、よりきれいな仕上がりが得られます。適切な工具を選ぶことで、作業がスムーズになり、無駄な時間を省くことができます。真鍮をフライス加工する際は、工具選びをしっかり行うことが大切です。
5. 真鍮の切削加工における具体的な事例や技術
5-1. 実際の加工事例の紹介
真鍮をフライス加工するための最適な工具を選ぶことは、とても大切です。まず、真鍮は柔らかい金属なので、切削がしやすいです。このため、鋭い刃を持つ工具が必要です。例えば、エンドミルという工具は、真鍮をきれいに加工するのに適しています。次に、工具の材質も重要です。高速度鋼や超硬合金の工具は、長持ちし、加工がスムーズに進むのでおすすめです。工具のサイズも考えましょう。加工する部品の大きさに合ったサイズを選ぶことで、より精密な仕上がりが得られます。このように、真鍮のフライス加工には適切な工具選びが欠かせません。正しい工具を使うことで、作業が楽になり、良い結果が得られます。
5-2. 技術的な課題と解決策
真鍮のフライス加工に適した工具を選ぶことは、とても大切です。まず、良い工具を使うと、よりきれいで正確な仕上がりになります。たとえば、特別な刃を持つフライスカッターを使うと、真鍮の表面が滑らかになり、見た目も良くなります。また、工具の材質も重要で、硬い素材で作られたものを選ぶと、長持ちします。さらに、加工速度や切削油の使い方にも注意が必要です。これらをしっかり考えることで、作業がスムーズに進み、失敗も減ります。真鍮をフライス加工する際には、適切な工具を選ぶことが成功のカギです。正しい工具を使えば、仕上がりが美しく、作業も楽しくなります。
5-3. 今後の真鍮加工技術の展望
真鍮のフライス加工に適した工具を選ぶことは、とても大切です。理由は、正しい工具を使うことで、加工がスムーズになり、仕上がりも良くなるからです。例えば、真鍮専用のフライス刃を使うと、金属がきれいに切れ、形を整えやすくなります。また、切削油を使うことで、工具の寿命が延び、加工中の熱を抑えることができます。このように、適切な工具を選ぶことは、作業の効率を高めるだけでなく、結果にも大きく影響します。真鍮を加工する際は、専用の工具や適切な方法を選ぶことが、成功の鍵となります。正しい道具を使って、素晴らしい作品を作りましょう。
まとめ
真鍮のフライス加工には、切削工具の選定が重要です。高速度鋼(HSS)や超硬合金製のエンドミルが推奨され、特にコーティングされた工具は耐摩耗性が向上します。また、切削条件や冷却剤の使用も加工精度に影響を与えるため、適切な設定が求められます。これにより、高品質な仕上がりが実現できます。
フライス加工における砲金の特性と注意すべき技術
フライス加工は、精密な部品を製造するための重要な技術ですが、使用する材料によってその特性や加工難易度が大きく異なります。その中でも、砲金(青銅)はその優れた機械的特性と耐食性から、様々な産業で広く利用されています。しかし、砲金をフライス加工する際には、特有の注意点やコツがあります。
「砲金のフライス加工について詳しく知りたいけれど、何を気を付ければいいのか分からない」と悩んでいる方も多いのではないでしょうか?本記事では、砲金の特性を理解し、フライス加工での注意点や効果的なテクニックを詳しく解説します。これを通じて、あなたの加工技術を一段と向上させ、より高品質な製品を生み出す手助けをしたいと考えています。
砲金によるフライス加工を成功させるために、この記事を参考にしてみてください。必要な知識と技術を身につけ、自信を持って素材を扱えるようになることで、実務の現場でも大いに役立つはずです。さあ、砲金のフライス加工の世界に一歩踏み出してみましょう!
1. 砲金のフライス加工における注意点とコツ
砲金は優れた耐摩耗性と耐食性を持つ合金であり、フライス加工においても適切な手法を用いることで高精度な加工が可能となります。本章では、砲金の特性を理解し、フライス加工時の注意点やコツについて解説します。
1.1. 砲金の特性とフライス加工の重要性
砲金は銅と錫を主成分とする合金で、以下のような特性を持ちます。
- 耐摩耗性:摺動部品などに適している。
- 耐食性:水や薬品に強く、長期使用が可能。
- 加工性:適切な工具を選定すれば比較的容易に加工が可能。
フライス加工においては、これらの特性を考慮し、最適な工具と切削条件を設定することが重要です。
1.2. フライス加工における注意点
砲金のフライス加工では、以下の点に注意が必要です。
- 工具摩耗:砲金は硬度が高いため、超硬工具やコーティング工具の使用が推奨されます。
- 切削速度の調整:適切な切削速度を選ばないと、工具の寿命が短くなります。
- 切りくず処理:砲金は切りくずが細かくなりやすいため、適切なクーラントの使用や切りくず排出の工夫が必要です。
1.3. 砲金のフライス加工におけるコツ
砲金のフライス加工をスムーズに行うためのコツを紹介します。
- 工具の選定:耐摩耗性に優れた超硬エンドミルやCBN工具を使用。
- クーラントの適用:適切な冷却と潤滑により、加工精度を向上。
- 切削条件の最適化:低い送り速度と適度な切削速度を設定し、工具の寿命を延ばす。
2. 砲金の切削加工の基本
切削加工は、砲金を高精度に加工するための基本的な方法の一つです。本章では、砲金の切削加工のメリットとその方法について説明します。
2.1. 切削加工のメリット
砲金の切削加工には以下のような利点があります。
- 高い寸法精度:精密加工が可能であり、部品の品質が安定する。
- 加工の自由度:複雑な形状の加工が容易。
- 短時間加工:最適な工具と条件を選べば、効率的に加工が可能。
2.2. 切削加工の方法
砲金の切削加工には主に以下の方法があります。
- 旋盤加工:円筒形状の部品加工に適している。
- フライス加工:平面や溝加工など、複雑な形状の加工に適用可能。
- ボール盤加工:穴あけやリーマ加工に使用。
適切な工具と加工条件を選定することで、砲金の優れた特性を活かした高品質な部品を製作できます。
3. 砲金の切断方法
砲金の切断には、適切な工具と手法を選定することが重要です。本章では、砲金の切断に適した工具と、それぞれの切断手法について解説します。
3.1. 切断工具の選定
砲金を効率よく切断するためには、以下のような工具が適しています。
工具名 | 特徴 | 適用範囲 |
---|---|---|
バンドソー | 安定した切断が可能で、熱影響が少ない | 大型材料の切断 |
丸ノコ | 高速切断が可能だが、切断面の仕上がりには注意が必要 | 中小型材料の切断 |
レーザー切断機 | 高精度な切断が可能だが、設備投資が必要 | 精密加工が求められる部品 |
プラズマ切断機 | 厚板の切断に適しているが、熱影響が大きい | 大型部品の切断 |
ウォータージェット | 熱影響なしで高精度な切断が可能 | 複雑な形状の切断 |
3.2. 切断手法の比較
砲金の切断方法には、それぞれの特性があります。目的に応じた方法を選択することが重要です。
- 機械切断(バンドソー・丸ノコ)
- 長尺材料の切断に適している
- 熱影響が少なく、歪みが少ない
- 熱切断(プラズマ・レーザー)
- 精密な切断が可能だが、熱による影響が生じる
- 大量生産向き
- ウォータージェット切断
- 熱影響がないため、寸法精度が高い
- 設備投資が必要
4. 砲金の加工に適した工具やバイト
砲金の加工を効率的に行うためには、適切な工具の選定が必要です。本章では、フライス加工用の工具と、バイトの選び方について解説します。
4.1. フライス加工用の工具
砲金のフライス加工には、以下のような工具が推奨されます。
工具名 | 特徴 | 適用範囲 |
---|---|---|
超硬エンドミル | 耐摩耗性が高く、長寿命 | 高精度な加工 |
CBNエンドミル | 砲金の高硬度に対応可能 | 高速切削 |
コーティングエンドミル | TiN・TiAlNコーティングにより工具寿命が向上 | 高負荷加工 |
超硬ラジアスエンドミル | 切削抵抗を抑え、工具寿命を延ばす | 長時間加工 |
4.2. バイトの選び方と使用法
砲金の旋盤加工に適したバイトを選ぶ際は、以下の点を考慮します。
- 刃先材質
- 超硬チップバイト:耐摩耗性が高く、安定した切削が可能
- ダイヤモンドバイト:高精度な仕上げ加工向け
- 切削角度
- 大きめの逃げ角:砲金は切削抵抗が大きいため、逃げ角を大きめに設定すると仕上げ面が向上
- 適切なすくい角:切りくず排出をスムーズにし、加工効率を上げる
- 使用法のポイント
- 切削速度を適切に調整し、摩耗を抑える
- クーラントを適用し、熱影響を軽減
- 仕上げ加工では低速で精度を重視する
砲金の特性を理解し、適切な工具と加工条件を選定することで、高品質な加工を実現できます。
まとめ
フライス加工における砲金は、優れた耐摩耗性と加工性を持つため、精密部品に適しています。ただし、熱処理による変形や、切削条件の設定が重要です。工具の選定や冷却剤の使用にも注意が必要で、適切な管理が品質向上に寄与します。