快削黄銅をフライス加工する際のポイント!切削速度と送りの最適値とは?
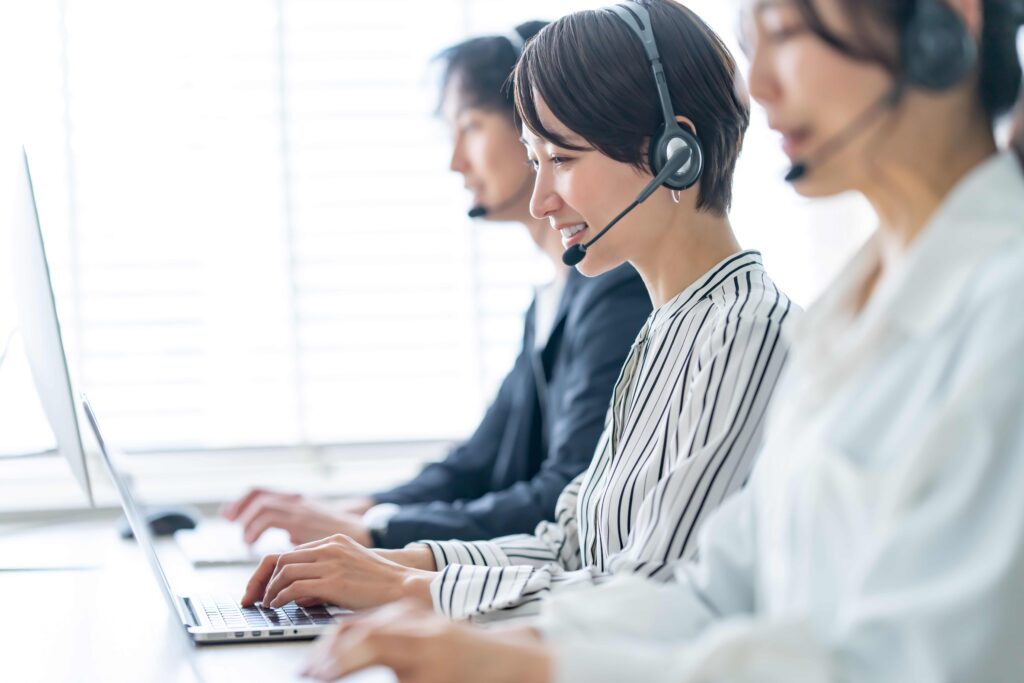
快削黄銅をフライス加工する際、切削速度と送りの最適値を知っていますか? これは、素材の特性や工具の種類によって異なる重要なポイントです。この記事では、快削黄銅の穴あけに焦点を当て、フライス加工の際の最適な切削速度と送りについて解説します。また、その他の注意すべきポイントやヒントについても紹介しますので、加工作業の効率化や品質向上に役立ててみてください。
快削黄銅 穴あけ・フライス加工の基礎知識
切削速度
快削黄銅の穴あけやフライス加工において、切削速度は100〜150m/minが理想的です。この範囲内で切削速度を設定することで、加工効率を最大化し、工具の摩耗を最小限に抑えることができます。切削速度が速すぎると、工具が過熱し、摩耗が早く進行する恐れがあります。一方、遅すぎると加工時間が無駄に長くなり、効率が悪くなるため、適切な速度を選定することが極めて重要です。特に快削黄銅は比較的加工しやすい材料であるため、この範囲内で安定した加工が可能です。
送り
送りは一般的に0.05〜0.20mm/revが適切とされていますが、工具の直径や刃数、仕上げ面の要求に応じて微調整が必要です。細かい送り設定は、加工物の材質や仕上げの要求精度によっても異なります。例えば、より精密な仕上げが求められる場合、送りを少し抑え気味に設定することがあります。また、大きな工具を使用する場合は、送りを少し高めに設定して加工効率を向上させることも可能です。正しい送り設定により、スムーズな加工が実現し、工具寿命の延長にも繋がります。
加工性
快削黄銅の加工性は非常に優れており、適切な切削速度と送りを守ることで、高精度な穴あけやフライス加工が可能となります。加工が安定すると、仕上げ面が美しく、寸法精度も高く保たれます。加工性が良いため、金型や機械部品など、精密な加工を要求される製品にも適しています。また、快削黄銅は他の金属材料に比べて切削中の発熱や摩耗が少ないため、安定した加工が可能です。これにより、製品の品質を高めることができ、製造工程全体の効率向上にも寄与します。
快削黄銅の特性と加工の利点
特性
加工作業の快適性:
快削黄銅の加工は低い切削熱と振動の抑制が特徴であり、作業者の作業環境が快適です。また、加工時の切粉が細かいため、機械に負担をかけず、作業がスムーズに進みます。
切削加工性:
快削黄銅は非常に優れた切削加工性を持ち、特にチップ排出性が良好です。これにより加工中に発生する熱を抑えることができ、工具の寿命が延びます。また、低い摩擦抵抗により、加工がスムーズに進行します。これにより安定した加工が可能となり、精度が高く効率的です。
機械的特性:
快削黄銅は良好な機械的特性を持ち、耐摩耗性や耐食性が高いため、長時間の加工でも安定した品質が確保されます。特に腐食環境での使用において、その耐食性が大きなメリットを発揮します。
切削工具への負担:
高いチップ排出性と低摩擦が切削工具の負担を軽減し、工具の寿命を延ばす要因となります。これにより、頻繁な工具交換が不要となり、全体の生産効率が向上します。
加工精度:
快削黄銅は高精度な加工が可能です。適切な切削条件を使用することで、微細な加工が得意であり、高精度な仕上がりを実現します。特に航空機部品や自動車部品など、精度が要求される製品で使用されることが多いです。
切削速度
快削黄銅のフライス加工において、切削速度は100〜150m/分が推奨されます。適切な切削速度を選定することで、工具の寿命を延ばし、加工面の仕上がりも向上します。過度に速い切削速度は、工具の摩耗を加速させる一方で、遅すぎると効率が悪くなり、コストが増大する可能性があります。そのため、推奨される切削速度を守ることが重要です。
送り速度
送り速度は0.05〜0.2mm/回が目安となります。正しい送り速度の設定により、高品質な加工面が得られます。送りが速すぎると加工の精度が低下し、遅すぎると加工時間が長くなり、効率が落ちてしまいます。最適な送り速度を選ぶことで、加工面が滑らかで美しい仕上がりとなり、部品の品質を保つことができます。
加工面の仕上がり
正しい切削条件下では、快削黄銅の加工面には美しい光沢が現れ、仕上がりが非常に良好になります。これにより、仕上げが必要な部品においても高い精度と美観を維持することができます。快削黄銅はその特性から、加工後の表面品質が重要な製品にも適しており、仕上がりの良さが製品の付加価値を高める要素となります。
快削黄銅 穴あけ時の切削条件設定
推奨切削条件
表面粗さが気になる場合は、微調整を行うことで、さらに精度の高い仕上がりが実現できます。
切削速度 (100〜150m/min)
切削速度は、使用する工具の直径や材料の特性に応じて調整する必要があります。一般的にこの範囲が推奨され、過度な速度での加工は工具の摩耗を早め、仕上がりに影響を及ぼす可能性があります。
高速で加工することで、効率よく作業が進みますが、過度に速すぎると表面粗さが増すため、適切な速度設定が重要です。
送り (0.05〜0.1mm/rev)
小径のエンドミルでは、下限の0.05mm/revで設定し、大径のエンドミルでは0.1mm/revが適切です。
送り速度が速すぎると、加工中に工具が過剰に摩耗したり、表面が荒れる原因となります。逆に、遅すぎると加工時間が増え、効率が低下するため、適切なバランスを取ることが大切です。
工具の摩耗
適切な切削条件を設定することで、工具の摩耗を抑制できます。摩耗を最小限に抑えつつ、高精度な仕上がりを得ることができます。
切削条件に無理があると、工具の寿命が短くなり、最終的には高いコストがかかることになります。工具の寿命を延ばすためには、常に最適な条件を見極めることが求められます。
試作と最適化
加工する黄銅の種類やフライスの仕様、工具の状態などに応じて、試作を繰り返し、最適な切削条件を見つけることが非常に重要です。
最適な切削条件を見つけることで、加工効率の向上だけでなく、工具寿命の延長や加工面の品質向上にも繋がります。
すべての加工条件は理論的な設定値に従うだけではなく、実際の加工状況に合わせて調整が必要です。
加熱と冷却
適切な冷却を行うことで、切削中の工具の温度をコントロールし、摩耗を減らすことができます。
加工中の温度が高すぎると、材料の変形や工具の早期摩耗を引き起こす可能性があるため、冷却液を活用して温度管理を行うことが重要です。
振動管理
加工時の振動は加工精度に悪影響を及ぼし、工具の摩耗を早める原因となります。振動を抑えるためには、適切な切削条件の選定に加えて、工具の取り付け状態や加工機の精度も重要です。
振動を管理することで、より安定した加工が可能となり、結果的に加工面の仕上がりが良くなります。
表面仕上げ
切削条件を正しく設定することで、表面仕上げの品質も向上します。快削黄銅の場合、適切な切削速度と送りを選ぶことで、美しい光沢を持つ加工面を得ることが可能です。
フライス加工における快削黄銅の切削速度と送りの決定
推奨切削条件
加工の途中で予想以上に摩耗が早い場合は、切削条件を再調整して、工具寿命を延ばすように工夫することが大切です。
切削速度 (100〜300m/分)
快削黄銅のフライス加工には、切削速度100〜300m/分の範囲内で設定するのが最適です。この範囲で設定することで、黄銅の優れた切削性能を活かし、加工がスムーズに進みます。
高すぎる切削速度は工具の摩耗を早める原因となり、逆に低すぎる切削速度では加工効率が悪くなるため、この範囲内で調整することが重要です。
送り (0.05〜0.35mm/歯)
送り速度は、加工内容に応じて調整が必要です。細かい加工には低い送りを設定し、大きな切削や粗加工には高い送りを使用します。
細かな加工:
精密な穴あけや仕上げ加工には、低い送り設定 (0.05〜0.1mm/歯) が適しています。低い送りで慎重に加工することで、より高精度な仕上がりが得られます。
精密加工では、工具の摩耗を抑え、きれいな表面仕上げを実現するため、送りを遅くし、加工面に余裕を持たせます。
大きな切削:
粗加工や大きな切削には、より高い送り設定 (0.2〜0.35mm/歯) が適しています。高い切削速度と送りで効率的に作業を行うことにより、加工時間を短縮し、コストを削減できます。
高送りでの加工は、特に高効率な加工を行いたい場合や、大きな部品の粗加工に適しています。
加工内容に応じた調整
加工の種類や黄銅の素材、工具の状態などに応じて、最適な切削速度と送りを設定することが求められます。例えば、穴あけや溝加工では、工具の摩耗を最小限に抑えるため、送りをやや低めに設定することが有効です。
非鉄金属部品の信頼性を高める切削技術
快削黄銅のフライス加工において、部品の信頼性を高めるためには、切削速度と送り率の適切な設定が非常に重要です。以下のポイントに注意することで、加工の精度や仕上がりを向上させることができます。
切削速度
まず、切削速度は、使用する材質や工具の耐久性に応じて調整する必要があります。快削黄銅の場合、一般的に100〜300m/分の範囲で設定することが推奨されています。この範囲で設定することにより、快削黄銅の優れた切削性能を活かしつつ、工具の寿命を延ばすことができます。また、適切な切削速度の選定は、加工面の仕上がりにも影響を与え、摩耗を抑えつつ安定した加工が可能となります。
送り率
次に、送り率ですが、これは加工内容や工具の種類に応じて最適な値を見つけることが求められます。送り率が遅すぎると加工時間が長くなり、経済的ではありません。逆に、送り率が早すぎると工具の摩耗が激しくなり、加工面の精度や仕上がりが悪化する可能性があります。そのため、送り速度を適切に調整することで、高い加工精度を維持しつつ、効率的な加工が可能になります。
穴あけ加工
さらに、穴あけ加工では、送りの調整が重要です。中心からの距離に応じて送りを調整し、均一な加工を実現することが求められます。特に精密加工の場合、慎重に送りを設定することで、より美しい仕上がりと高精度な加工が可能になります。
このように、快削黄銅のフライス加工においては、切削速度と送り率の適切な設定が部品の信頼性を高めるための重要な要素となります。適切な設定を行うことで、加工精度が向上し、部品の性能を最大限に引き出すことができ、高品質な加工結果を得ることができます。
快削黄銅の切削加工ポイントと実践的注意点
快削黄銅をフライス加工する際の切削速度と送り速度の設定は、加工品質と効率を向上させるために非常に重要です。以下に示すポイントと注意点を考慮することで、最適な加工条件を見つけることができます。
切削速度
高い切削速度を設定することは可能ですが、過度な速度設定は表面仕上がりに悪影響を与える可能性があります。特に加工初期には、メーカー推奨の設定値を参考にすることが重要です。これにより、加工中の工具の摩耗を最小限に抑えつつ、適切な加工面の仕上がりを確保することができます。
送り速度
快削黄銅は切削抵抗が小さいため、過度な送り速度を設定すると、表面仕上がりに問題が生じることがあります。適切な送り速度を設定することで、加工精度を保ちながら、効率的に作業を進めることができます。特に細かい加工が必要な場合は、送り速度を控えめに設定することが重要です。
微調整の重要性
実際の加工状況に合わせて微調整を行うことが必要です。例えば、小径のエンドミルを使用する場合、切削速度を高く設定し、送り速度を控えめに設定することが望ましいです。この微調整によって、工具の摩耗を抑え、仕上がり品質を向上させることができます。
テストカットの活用
加工条件を決定する際には、テストカットを行い、その結果を基に設定値を調整することが重要です。テストカットを通じて、実際の加工状況を確認し、品質と効率のバランスを保つための最適な設定を見つけることができます。
結論として、快削黄銅のフライス加工では、初期設定を参考にしつつ、テストカットを行ってその結果をもとに微調整を行うことが重要です。これにより、加工品質と効率の両方を向上させることができ、最適な加工条件を実現することができます。
快削黄銅の切削速度と切りくず生成現象の関係
快削黄銅をフライス加工する際には、切削速度と送りのバランスが非常に重要です。適切な切削速度と送り速度を選定することで、加工品質を向上させ、効率的に作業を進めることができます。以下に、切削速度と切りくず生成の関係について説明します。
切削速度の影響
快削黄銅は高い切削速度での加工が適しており、良好な加工性を発揮します。切削速度が遅くなると、材料が詰まりやすくなり、切削性が低下します。したがって、適切な切削速度を設定することが、加工効率と品質を確保するために不可欠です。
送りの影響
送り速度の設定も非常に重要です。速すぎる送り設定を行うと、工具の摩耗が激しくなり、加工精度に悪影響を及ぼすことがあります。一方で、遅すぎる送り設定は加工効率を低下させ、作業時間が無駄に長くなります。そのため、適切な送り速度の設定を行うことが必要です。
具体例
例えば、直径10mmのエンドミルを使用する場合、切削速度は60〜100m/minが一般的です。送り速度は0.05〜0.1mm/刃が推奨されます。この範囲内で切削速度と送り速度を設定することで、適切な切りくずの生成と高品質な加工面を実現することができます。
最適化の手順
最適な切削速度と送り速度を見つけるためには、まず小さな値から始めて徐々に切削速度と送りを上げていく方法が有効です。この方法により、理想的な切りくずの形成と加工面の仕上がりを実現し、最適な加工条件を導き出すことができます。
結論として、快削黄銅のフライス加工においては、切削速度と送りの最適値を見極めることが非常に重要です。これにより、加工面の仕上がりと切りくず生成を最適化し、加工の成功へとつながります。
快削黄銅 穴あけ・フライス加工のトラブルシューティング
快削黄銅をフライス加工する際には、いくつかのトラブルが発生することがあります。以下に、主なトラブルの原因とその対策を示します。
加工精度の低下
- 原因: 切削速度や送りが適切でない場合に発生することがあります。
- 対策: 切削速度を100〜300m/min、送りを0.05〜0.2mm/revに設定します。また、試作加工を行い、最適な切削条件を見つけることが重要です。
工具の摩耗が早い
- 原因: 切削速度や送り速度が高すぎることが原因で、工具に過度の負荷がかかるためです。
- 対策: 小径のエンドミル使用時には、高い切削速度と小さい送りを設定します。切削条件の見直しを行い、工具の摩耗を抑えるよう調整します。
バリの発生
- 原因: 不適切な切削条件が原因で、加工面にバリが発生します。
- 対策: 切削速度と送り速度を見直し、加工面の仕上がりを改善することが必要です。試作加工で条件を調整し、バリの発生を最小限に抑えます。
切りくずの排出不良
対策: 送り速度を適切に設定し、切削速度と合わせて調整します。これにより、切りくずがスムーズに排出されるようになります。
原因: 送り速度が適切でないか、切削速度が過剰または不足している場合、切りくずが適切に排出されないことがあります。快削黄銅の加工に関するテーブル
切削条件
条件 | 推奨値 | 説明 |
---|---|---|
切削速度 | 100〜150 m/min | 高速での加工が可能。切削速度が遅いと詰まりやすく、速すぎると摩耗が激しくなるため、バランスが重要です。 |
送り速度 | 0.05〜0.20 mm/rev | 工具の直径や刃数に応じて調整。速すぎると仕上がりが悪く、遅すぎると効率が悪化し、工具に負担がかかります。 |
穴あけ | 切削速度: 100〜150 m/min、送り: 0.05〜0.1 mm/rev | 小径エンドミル使用時に最適な設定。送り速度が遅すぎると加工効率が低下し、速すぎると仕上がりが粗くなる。 |
フライス加工 | 切削速度: 100〜300 m/min、送り: 0.05〜0.35 mm/歯 | 大きな切削や細かい加工に応じて最適化。加工面の仕上がりに合わせて、送りを適切に調整することが重要。 |
切削くず | 高速加工時は均等に排出されやすい | 高速加工時、切削速度と送りが適切であれば、良好な切りくずの形成が確保でき、排出もスムーズに行える。 |
加工技術と注意点
- 切削速度と送りの調整: 高い切削速度での加工は、快削黄銅の加工性を最大限に引き出すことができます。しかし、送り速度が適切でない場合、表面仕上がりが悪化し、工具の摩耗が早まる可能性があります。具体的には、切削速度は高めでも送りが速すぎると、表面に細かな傷がつき、精度が低下することがあります。逆に、送りが遅すぎると、加工効率が落ちるため、バランスの取れた調整が必要です。
- ツールの選定: 小径エンドミルを使用する際は、高い切削速度で送りを控えめにすることで、精度良く仕上げることができます。一方、大径ツールを使用する場合は、効率的な加工を行うために、より高い送り速度を選択することができます。エンドミルの選定や工具の材質によって、切削性能に大きな差が出るため、工具選びは重要な要素となります。
- 試作と調整: 最適な加工条件を見つけるためには、試作加工を行い、結果を基に微調整を行うことが不可欠です。試作を行うことで、実際の加工結果に基づいた最適な設定を見つけることができ、加工精度の向上や効率化が可能になります。特に、異なる工具や切削条件によって最適値が異なるため、いくつかの条件を試して調整することが重要です。
先進的加工技術の展望
環境に配慮した加工技術: 環境への配慮が重要な現代において、切削時のエネルギー消費や切削液の使用を抑えたエコ加工技術が注目されています。これらの技術を取り入れることで、エネルギーコストの削減や環境負荷の低減が可能になり、持続可能な生産活動が支援されています。
高精度と効率性: 現在の快削黄銅の加工技術では、高速切削と適切な送り速度のバランスが求められます。これにより、加工精度の向上と生産効率の向上を同時に実現できます。特に、CNC(コンピュータ数値制御)加工機などを活用することで、高精度な加工が可能となり、効率的な生産が実現します。最新の工具や刃物技術により、切削の精度と品質がさらに向上しています。
加工条件の最適化: 加工条件の最適化には、試行錯誤を繰り返しながら、最適な切削条件を見つけることが求められます。たとえば、冷却液の使用や工具の選定、切削面の仕上がりに対する要求を考慮することが必要です。さらに、精密加工が要求される場合、切削速度を抑えることが推奨されることもあります。これにより、精度を犠牲にせず、効率的な加工が可能となります。
デジタル技術の導入: 高度な加工技術では、デジタルモニタリングやAI(人工知能)による条件最適化が進んでおり、加工中のリアルタイムデータを基に自動的に条件を調整するシステムが登場しています。これにより、加工精度がさらに向上し、無駄を省いた効率的な生産が可能となります。
快削黄銅 穴あけ・フライス加工のまとめ
要素詳細
要素 | 詳細 |
---|---|
切削速度 | 快削黄銅の場合、100〜300m/minが推奨されます。熱伝導率が高く、加工時の熱を素早く逃がすことが可能です。 |
送り速度 | 0.05〜0.35mm/revが一般的な範囲です。適切な送り速度を保つことで、工具の摩耗を抑えつつ効率的に削り取ります。 |
加工条件の調整 | 旋盤などでの穴あけ加工では、直径に応じた切削速度と送りが設定表で提供されていることが多いです。材料や工具の状態に応じて微調整が必要です。 |
最適な加工 | 高い切削速度と適度な送り速度を保つことで、快削黄銅特有の絞りやねじれが少なく、美しい仕上がりが実現できます。 |
解説
快削黄銅を使用した穴あけやフライス加工においては、切削速度と送り速度の設定が加工品質に大きく影響します。まず、切削速度は100〜300m/minが理想的で、高い速度設定が推奨されます。快削黄銅は熱伝導率が高いため、加工時に発生する熱を迅速に逃がすことができ、これによって高い切削速度での加工が可能となります。
次に、送り速度については0.05〜0.35mm/revが一般的で、加工する穴のサイズや加工条件によって微調整が必要です。例えば、小径の穴を加工する場合は、送り速度を遅く設定し、大径の穴を加工する場合は、送り速度を速めるといった調整が求められます。旋盤やフライス盤の設定表を参考にしながら、材料や工具の状態に応じた最適な条件を見つけることが重要です。
最適な加工条件を守ることで、工具の寿命が延び、加工面が美しく仕上がるため、精度の高い仕上げが可能となります。また、加工中に発生する熱の管理がしっかり行われることで、工具の摩耗を抑えつつ効率的に削り取ることができるため、作業の効率が向上します。
高い切削速度と適度な送り速度を維持し、試作加工を通じて最適条件を見つけることが成功の鍵です。このような精緻な設定により、快削黄銅特有の絞りやねじれが少なく、美しい仕上がりを実現できます。